- お役立ち記事
- Improvement methods to achieve the goal of “zero complaints”—measures that should be promoted by the quality assurance department
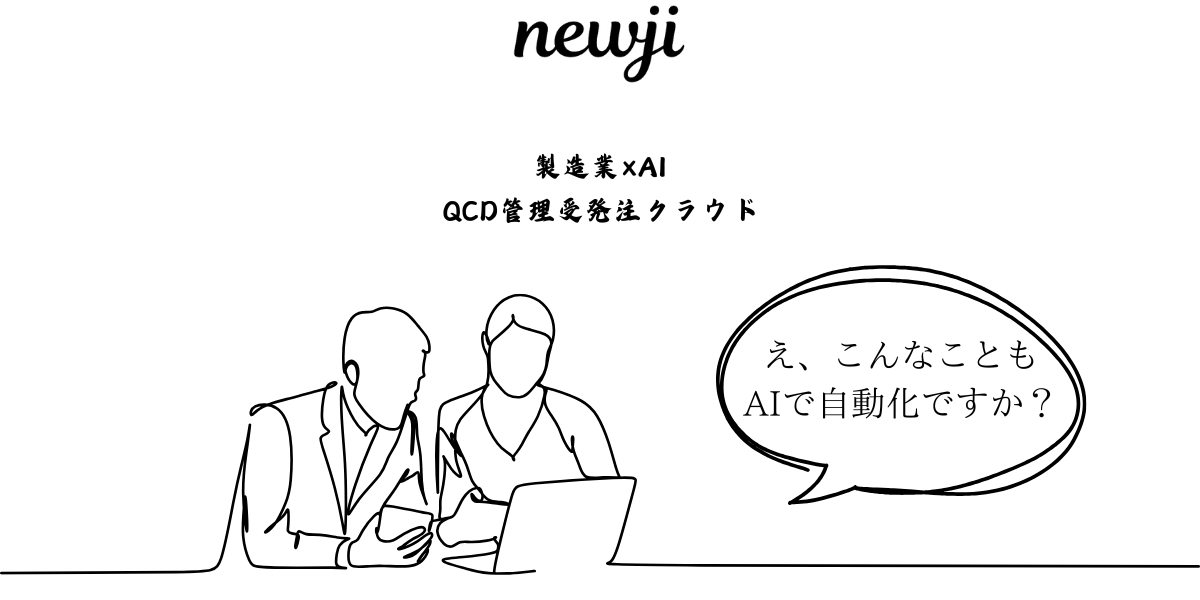
Improvement methods to achieve the goal of “zero complaints”—measures that should be promoted by the quality assurance department
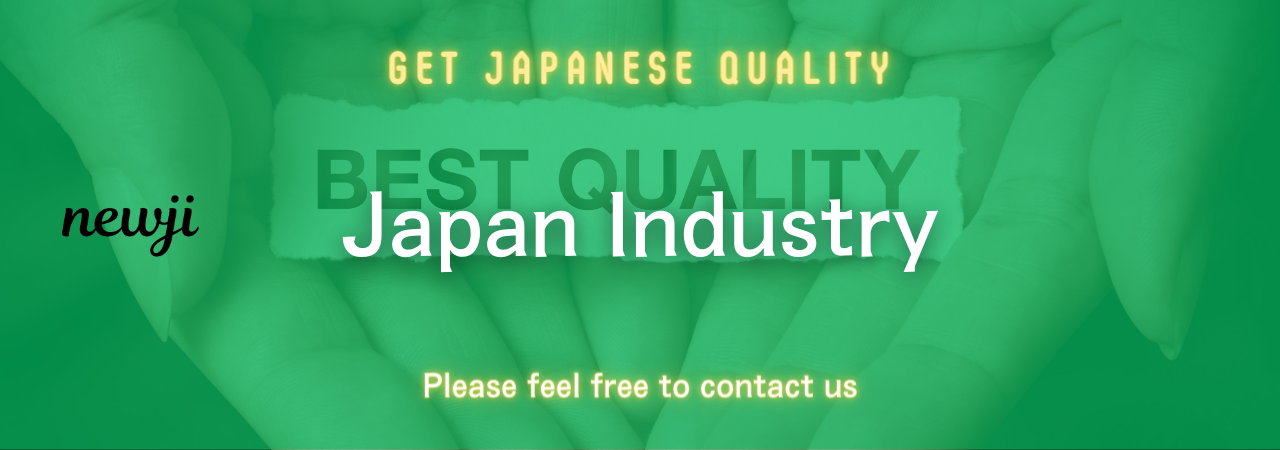
目次
Understanding the Importance of Zero Complaints
Achieving the goal of zero complaints is crucial for any company aiming for excellence in customer satisfaction and product quality.
When customers have no complaints, it reflects a high level of trust and confidence in a brand.
This fosters loyalty, promotes positive word-of-mouth, and ultimately leads to an increase in sales and company growth.
For any organization, especially the quality assurance department, understanding how to consistently ensure zero complaints is essential.
The Role of the Quality Assurance Department
The quality assurance (QA) department is pivotal in shaping a company’s product quality and ensuring customer satisfaction.
They are tasked with setting quality standards, developing procedures, conducting audits, and training staff to meet these standards.
Their work is integral to identifying and addressing potential issues in production, thus minimizing or eliminating customer complaints.
Setting Quality Standards
QA teams must establish clear, achievable quality benchmarks that align with customer expectations and industry regulations.
This includes developing comprehensive guidelines that govern the entire product lifecycle, from design to delivery.
Having precise standards helps in minimizing errors and ensuring that every product meets or exceeds customer expectations.
Implementing Robust Procedures
Robust procedures are vital for maintaining consistency in product quality.
The QA department should develop detailed processes for every stage of production, ensuring consistency in quality control measures.
This not only reduces the likelihood of defects but also streamlines operations, enhancing overall productivity.
Regular Audits and Inspections
Conducting regular audits and inspections is key to identifying areas for improvement.
It helps in discovering any potential issues before they result in customer complaints.
By actively monitoring processes and systems, QA teams can take early corrective actions, thereby maintaining product integrity and quality.
Training and Development
Ensuring that all employees are adequately trained is essential for achieving zero complaints.
The QA department should facilitate ongoing training sessions that emphasize quality assurance principles, problem-solving, and customer service skills.
Empowered employees are more likely to take initiative in resolving issues before they escalate into complaints.
Key Measures to Minimize Customer Complaints
There are several proactive measures that QA departments can adopt to minimize customer complaints effectively.
Enhancing Communication Channels
Effective communication channels are essential for understanding customer needs and concerns.
QA teams should work alongside customer service to ensure that there is a seamless process for customers to express their issues.
This allows for immediate feedback and quicker resolution of any problems.
Utilizing Customer Feedback
Listening to customer feedback is crucial for continuous improvement.
QA departments should regularly analyze feedback to identify recurring issues and potential areas for product enhancement.
This information should then be used to make informed decisions and modifications, ensuring future products meet customer expectations.
Leveraging Data and Analytics
Data analytics can provide deep insights into emerging trends and potential problem areas.
QA teams should leverage analytical tools to track quality control metrics, identify patterns, and predict potential failure points.
This proactive approach aids in preventing issues before they arise and helps maintain high standards.
Implementing Continuous Improvement Practices
Continuous improvement is the cornerstone of achieving zero complaints.
Implementing frameworks such as Six Sigma or Total Quality Management (TQM) can guide systematic quality improvements.
These methodologies promote a culture of excellence where every team member is focused on enhancing processes and eliminating waste.
Cultivating a Quality-Centric Culture
A culture that prioritizes quality involves everyone in the organization, from top management to entry-level employees.
Creating this culture is essential for achieving zero complaints.
Leadership Commitment
Leadership must demonstrate a strong commitment to quality assurance initiatives.
By actively participating in QA meetings and emphasizing quality as a core value, leaders can set a positive example for the entire organization.
Their support and involvement are vital for driving meaningful quality improvements.
Fostering Open Communication
Encouraging open communication across all levels of the organization helps in identifying and resolving quality issues swiftly.
A transparent communication model ensures that every team member feels comfortable raising concerns and sharing ideas.
This openness contributes to rapid identification of potential problems and fosters teamwork in resolving them.
Recognition and Rewards
Recognizing and rewarding employees for quality-driven performance boosts morale and encourages commitment to excellence.
Whether through monetary bonuses, public acknowledgments, or other incentives, acknowledging employees’ dedication to maintaining high standards nurtures a quality-centric atmosphere.
The Path to Zero Complaints
Achieving the goal of zero complaints demands a concerted effort by the entire organization.
It requires a robust strategy that includes setting clear quality standards, deploying effective procedures, leveraging customer insights, and cultivating a culture truly centered around quality.
By focusing on these strategies, the quality assurance department can actively guide their companies towards achieving and maintaining zero complaints.
Maintaining this standard not only ensures customer satisfaction but also significantly contributes to long-term success and competitiveness in the marketplace.
資料ダウンロード
QCD調達購買管理クラウド「newji」は、調達購買部門で必要なQCD管理全てを備えた、現場特化型兼クラウド型の今世紀最高の購買管理システムとなります。
ユーザー登録
調達購買業務の効率化だけでなく、システムを導入することで、コスト削減や製品・資材のステータス可視化のほか、属人化していた購買情報の共有化による内部不正防止や統制にも役立ちます。
NEWJI DX
製造業に特化したデジタルトランスフォーメーション(DX)の実現を目指す請負開発型のコンサルティングサービスです。AI、iPaaS、および先端の技術を駆使して、製造プロセスの効率化、業務効率化、チームワーク強化、コスト削減、品質向上を実現します。このサービスは、製造業の課題を深く理解し、それに対する最適なデジタルソリューションを提供することで、企業が持続的な成長とイノベーションを達成できるようサポートします。
オンライン講座
製造業、主に購買・調達部門にお勤めの方々に向けた情報を配信しております。
新任の方やベテランの方、管理職を対象とした幅広いコンテンツをご用意しております。
お問い合わせ
コストダウンが利益に直結する術だと理解していても、なかなか前に進めることができない状況。そんな時は、newjiのコストダウン自動化機能で大きく利益貢献しよう!
(Β版非公開)