- お役立ち記事
- Improving development design efficiency and quality by utilizing quality engineering (Taguchi method)
月間76,176名の
製造業ご担当者様が閲覧しています*
*2025年3月31日現在のGoogle Analyticsのデータより
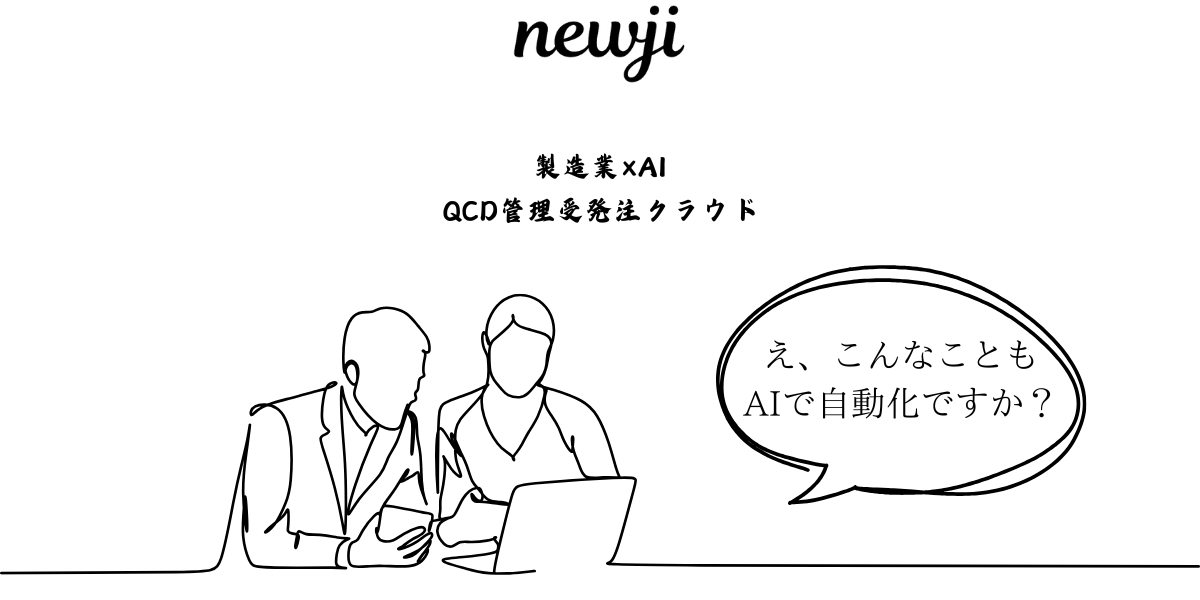
Improving development design efficiency and quality by utilizing quality engineering (Taguchi method)
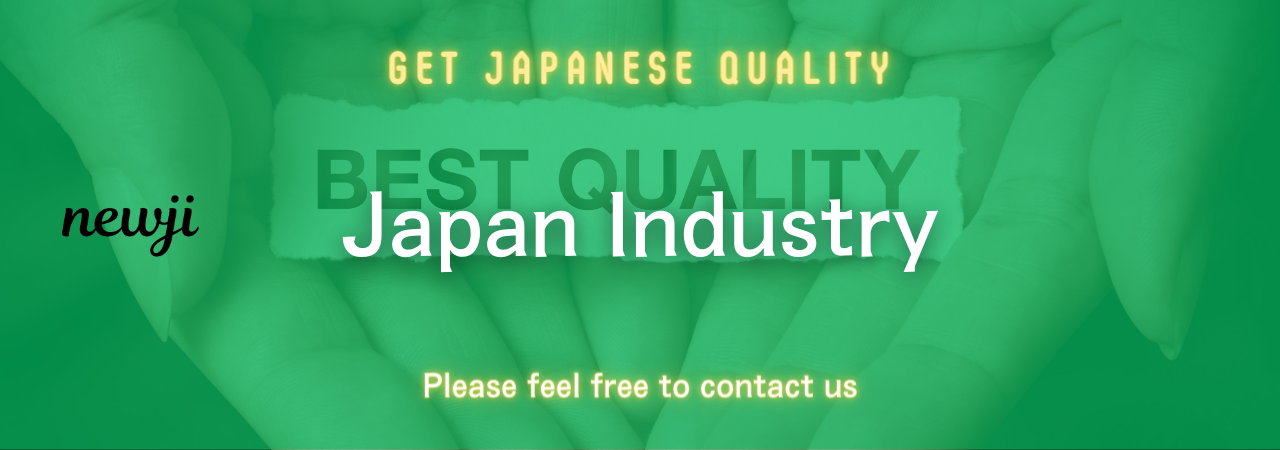
目次
Understanding Quality Engineering and the Taguchi Method
Quality engineering plays a vital role in the development and design of products across various industries.
One of the profound methodologies used within quality engineering is the Taguchi method.
Dr. Genichi Taguchi, a Japanese engineer and statistician, introduced this approach in the 1950s.
The Taguchi method emphasizes robust design and optimizing the process, aiming to improve the quality and performance of products while minimizing costs.
At the core of the Taguchi method is the concept of designing products that are insensitive to external variations, whether they involve noise factors, environmental changes, or manufacturing discrepancies.
This involves using statistical and optimization techniques to identify the most impactful factors affecting product quality and performance, and making adjustments in the manufacturing process accordingly.
The Significance of Quality Engineering
Quality engineering ensures that a product meets or exceeds customer expectations by minimizing variations and defects in the design and manufacturing process.
It improves the development cycle by emphasizing continuous improvements based on data and systematic analysis.
By applying quality engineering principles, organizations can enhance their operational efficiency, achieve cost savings, and better comply with regulatory requirements.
Leveraging tools like the Taguchi method enables businesses to identify potential sources of defects and variability early in the design process, allowing for proactive corrections and optimizations.
Core Principles of the Taguchi Method
1. Robust Design
Robust design focuses on producing high-quality products that remain unaffected by external operational conditions.
This principle guides engineers to determine optimal parameters that enhance product reliability and performance, ensuring customer satisfaction and brand reputation.
2. Signal-to-Noise Ratio
The Taguchi method introduces the concept of the signal-to-noise (S/N) ratio.
This ratio is an analytical tool used to gauge the quality of a product by contrasting the desired result (signal) against disruptive factors (noise).
A higher S/N ratio implies a quieter, more stable process with less variability and higher reliability.
3. Orthogonal Arrays
Orthogonal arrays are a statistical tool that simplifies the experimental design process.
They allow engineers to systematically investigate the effects of multiple factors with a reduced number of experiments.
This technique ensures efficient resource usage while maintaining robustness and product quality.
4. Cost and Performance Balance
The Taguchi method helps achieve a balance between costs and performance by identifying the most significant factors influencing quality and making pertinent adjustments.
This approach prioritizes critical features and optimizations that yield the best overall improvements in quality without unnecessary expense.
Implementing the Taguchi Method in Development Design
To successfully implement the Taguchi method in development design, follow these practical steps:
Step 1: Define the Problem
Clearly identify and articulate the design problem that needs addressing.
This includes outlining customer needs, expected product performance, and potential sources of variation that might affect the quality.
Step 2: Determine Control and Noise Factors
Identify the control factors that can be altered to influence the product’s quality and performance.
Additionally, recognize the noise factors — variables that cannot be controlled but may impact the product’s stability under varying conditions.
Step 3: Design the Experiment
Utilize orthogonal arrays to design experiments that systematically manipulate the identified control factors.
This reduces the number of trials needed while ensuring a comprehensive investigation of possible outcomes.
Step 4: Conduct the Experiment
Execute the designed experiments to gather data on the performance and quality of the product under various conditions.
Empirical evidence drawn from these experiments will guide future design modifications.
Step 5: Analyze the Results
Analyze the collected data to compute signal-to-noise ratios for each set of conditions.
Determine the most favorable configuration of control factors that optimize product performance and minimize sensitivity to noise.
Step 6: Optimize the Design
Implement the improvements suggested by data analysis to refine the product design.
This may involve adjusting manufacturing processes, selecting alternative materials, or modifying design specifications to achieve greater quality and efficiency.
Case Example: Application of the Taguchi Method
A renowned automobile manufacturer faced challenges with engine durability due to variations in raw material properties and environmental conditions.
By applying the Taguchi method, the company identified critical material and process control factors influencing engine performance.
Through systematic experimentation and analysis, the Taguchi approach helped enhance engine robustness, leading to improved fuel efficiency and longer service life.
The manufacturer also experienced a reduction in warranty costs and an increase in customer satisfaction.
The Benefits of Utilizing Quality Engineering
The successful application of the Taguchi method within quality engineering offers several benefits:
– Improved product reliability and customer satisfaction
– Reduced production costs through better resource allocation
– Minimized waste and defects during manufacturing
– Greater innovation and competitive advantage
– Enhanced compliance with regulatory standards
Conclusion
In conclusion, incorporating quality engineering and the Taguchi method can significantly improve design efficiency and quality in product development.
By understanding and applying its principles, companies can achieve robust designs, balance cost and performance, and ultimately deliver high-quality products that exceed customer expectations.
This approach not only enhances operational efficiency but also contributes to long-term success and sustainability in an ever-evolving marketplace.
資料ダウンロード
QCD管理受発注クラウド「newji」は、受発注部門で必要なQCD管理全てを備えた、現場特化型兼クラウド型の今世紀最高の受発注管理システムとなります。
ユーザー登録
受発注業務の効率化だけでなく、システムを導入することで、コスト削減や製品・資材のステータス可視化のほか、属人化していた受発注情報の共有化による内部不正防止や統制にも役立ちます。
NEWJI DX
製造業に特化したデジタルトランスフォーメーション(DX)の実現を目指す請負開発型のコンサルティングサービスです。AI、iPaaS、および先端の技術を駆使して、製造プロセスの効率化、業務効率化、チームワーク強化、コスト削減、品質向上を実現します。このサービスは、製造業の課題を深く理解し、それに対する最適なデジタルソリューションを提供することで、企業が持続的な成長とイノベーションを達成できるようサポートします。
製造業ニュース解説
製造業、主に購買・調達部門にお勤めの方々に向けた情報を配信しております。
新任の方やベテランの方、管理職を対象とした幅広いコンテンツをご用意しております。
お問い合わせ
コストダウンが利益に直結する術だと理解していても、なかなか前に進めることができない状況。そんな時は、newjiのコストダウン自動化機能で大きく利益貢献しよう!
(β版非公開)