- お役立ち記事
- Improving Efficiency Through Production Line Improvements: Significantly Reducing Work Time
Improving Efficiency Through Production Line Improvements: Significantly Reducing Work Time
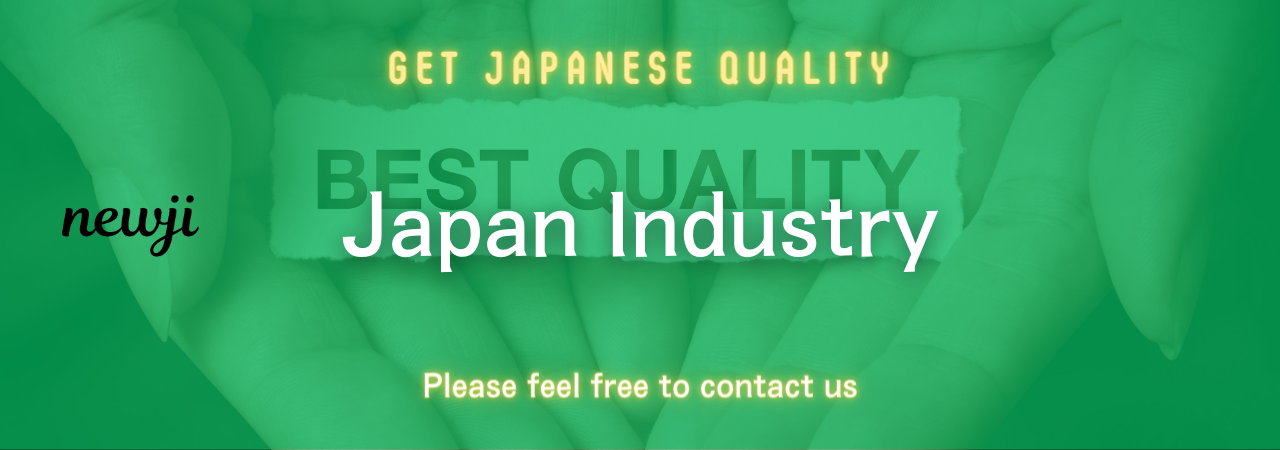
Improving the efficiency of production lines is crucial for any manufacturing business aiming to boost productivity and cut costs.
An effective production line does not just ensure quicker delivery of goods, but it also optimizes resource utilization and minimizes errors.
By analyzing and making strategic adjustments, companies can significantly reduce work time, leading to a more streamlined operation.
目次
Understanding Production Line Efficiency
Production line efficiency refers to how effectively a manufacturing line operates in terms of speed, cost, and quality.
It involves coordinating various processes and resources to produce goods in the least amount of time while maintaining high standards.
An efficient production line has several benefits including reduced labor costs, lower waste, and improved output quality.
Assessing the current state of your production line is the first step to making improvements.
Identifying Bottlenecks and Constraints
The foremost task is identifying bottlenecks and constraints.
A bottleneck in a production line is a stage that reduces the overall speed of the line.
This is where work accumulates and slows down the entire process.
By pinpointing these areas, you can implement targeted improvements.
Conducting a thorough analysis involving time studies and process flow mapping can help uncover these inefficiencies.
Time Studies
Time studies involve measuring how long each part of the production process takes.
By documenting these times, you can identify the stages that take longer than others.
Once these stages are identified, you can delve deeper to understand why they are slower and implement corrective measures.
Process Flow Mapping
Process flow mapping is another valuable tool.
It provides a visual representation of the entire production process, helping to quickly identify where delays and inefficiencies occur.
With a comprehensive map, you can see the sequence of operations and pinpoint exactly where improvements are needed.
Implementing Lean Manufacturing Principles
Lean manufacturing principles focus on minimizing waste and increasing efficiency.
Several methodologies under lean manufacturing can significantly reduce work time in production lines.
5S System
The 5S system is a workplace organization method that includes Sort, Set in order, Shine, Standardize, and Sustain.
Implementing this system ensures that the workspace is organized, which can significantly decrease the time workers spend looking for tools or materials.
Just-In-Time (JIT) Production
Just-In-Time production is a strategy where materials and products are produced only as needed.
This reduces storage time, minimizes inventory costs, and ensures that materials are always fresh and ready for use, thus reducing work time.
Automating Key Processes
Automation is another powerful way to enhance production line efficiency.
By incorporating modern technology, some of the more repetitive and time-consuming tasks can be handled by machines, freeing up human workers for more complex tasks.
Robotic Process Automation (RPA)
Robotic process automation involves using robots to perform repetitive tasks like transporting materials or handling simple assembly jobs.
Implementing RPA can speed up production times and reduce human error.
Advanced Software Solutions
Implementing advanced software solutions like manufacturing execution systems (MES) can streamline operations by coordinating and monitoring production processes in real-time.
This can lead to quicker decision-making and fewer delays in the production line.
Enhancing Worker Training and Engagement
Human resources are as vital to a production line as machinery and technology.
Ensuring that workers are well-trained and engaged can significantly reduce work time.
Regular Training Programs
Implementing regular training programs ensures that workers are always up-to-date with the latest techniques and technologies.
This reduces the time they spend figuring things out and allows them to work more efficiently.
Engagement and Incentives
Engaged workers are often more productive.
Offering incentives for meeting certain productivity targets can motivate employees to work more efficiently, thus reducing overall work time.
Continuous Improvement Through Feedback
The quest for a more efficient production line does not end after initial improvements are made.
Continuous evaluation and feedback are essential for maintaining efficiency and identifying further areas for improvement.
Feedback Loops
Establishing feedback loops where workers can report issues or suggest improvements can provide valuable insights.
Those who work on the production line daily may notice inefficiencies that management might overlook.
Regular Audits
Conducting regular audits can also help keep the production line running smoothly.
These audits can identify new bottlenecks or confirm that implemented improvements are functioning as expected.
In conclusion, improving production line efficiency is a multifaceted approach that involves identifying bottlenecks, implementing lean manufacturing principles, automating key processes, enhancing worker training, and continuously seeking feedback.
By making these targeted improvements, companies can significantly reduce work time, boost productivity, and maintain high-quality standards.
資料ダウンロード
QCD調達購買管理クラウド「newji」は、調達購買部門で必要なQCD管理全てを備えた、現場特化型兼クラウド型の今世紀最高の購買管理システムとなります。
ユーザー登録
調達購買業務の効率化だけでなく、システムを導入することで、コスト削減や製品・資材のステータス可視化のほか、属人化していた購買情報の共有化による内部不正防止や統制にも役立ちます。
NEWJI DX
製造業に特化したデジタルトランスフォーメーション(DX)の実現を目指す請負開発型のコンサルティングサービスです。AI、iPaaS、および先端の技術を駆使して、製造プロセスの効率化、業務効率化、チームワーク強化、コスト削減、品質向上を実現します。このサービスは、製造業の課題を深く理解し、それに対する最適なデジタルソリューションを提供することで、企業が持続的な成長とイノベーションを達成できるようサポートします。
オンライン講座
製造業、主に購買・調達部門にお勤めの方々に向けた情報を配信しております。
新任の方やベテランの方、管理職を対象とした幅広いコンテンツをご用意しております。
お問い合わせ
コストダウンが利益に直結する術だと理解していても、なかなか前に進めることができない状況。そんな時は、newjiのコストダウン自動化機能で大きく利益貢献しよう!
(Β版非公開)