- お役立ち記事
- Improving Efficiency with CIP Molding
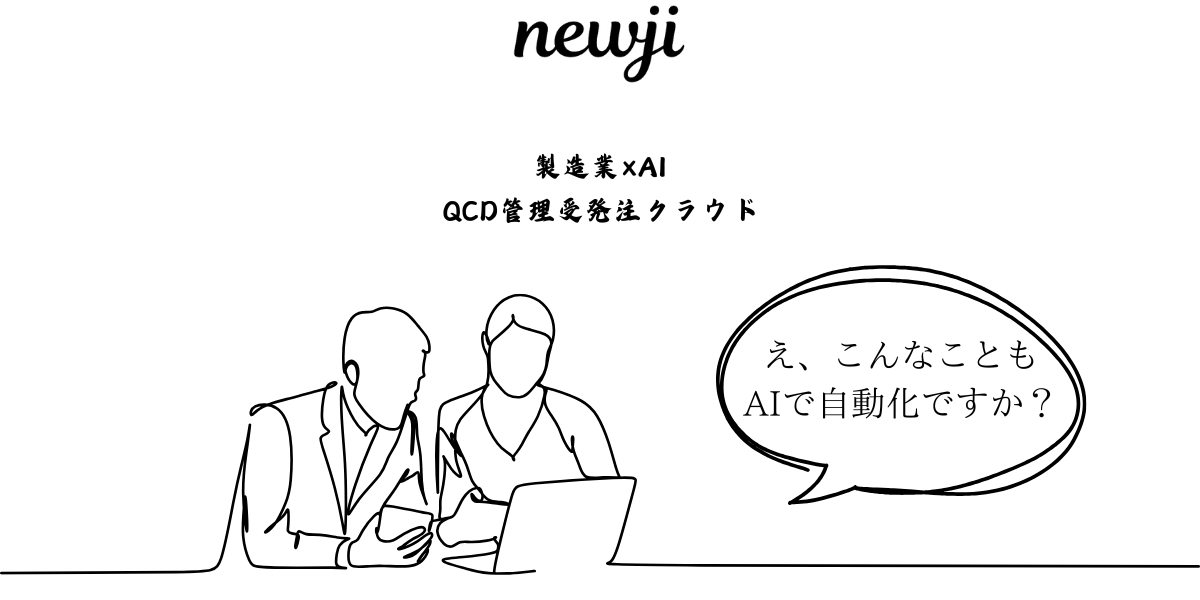
Improving Efficiency with CIP Molding
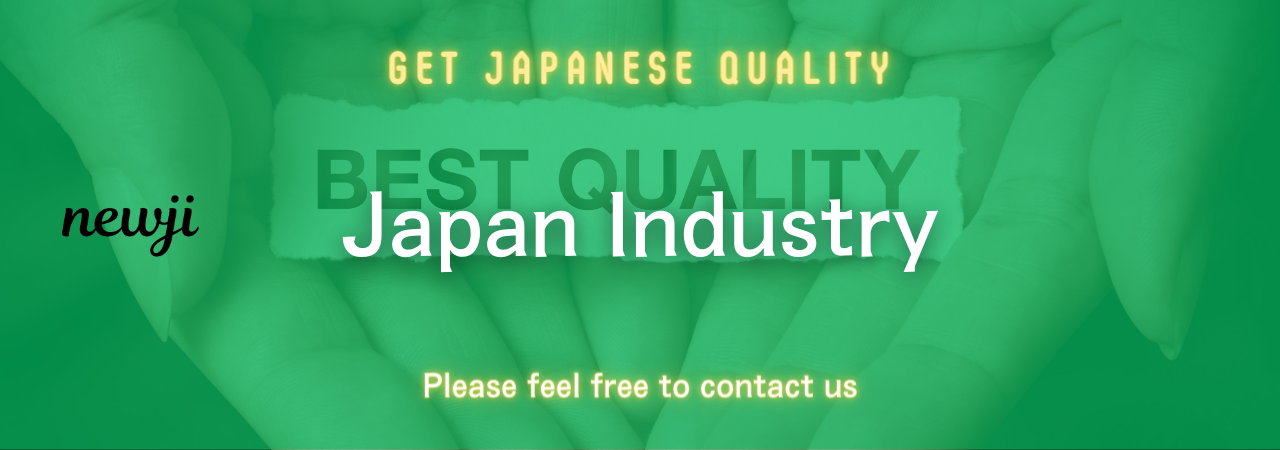
目次
Understanding CIP Molding
CIP molding, or Cold Isostatic Pressing, is a manufacturing process used to form complex shapes from powdered materials.
This technique is highly beneficial in industries where precision and performance are critical.
During the CIP process, powder is placed into a flexible mold, then it’s subjected to high pressure applied evenly from all directions, typically using a liquid medium like water or oil.
This pressure causes the powder particles to bond closely, resulting in a dense and uniform compact.
The magic of CIP molding lies in its ability to improve material properties while maintaining structural integrity.
The uniform pressure ensures that there’s no weak point in the component, which is crucial for parts that will experience stress or wear during use.
In fact, this process allows for the creation of components that might not be possible with other manufacturing techniques.
Advantages of CIP Molding
CIP molding offers numerous advantages over traditional manufacturing processes.
Firstly, it allows for near net-shape manufacturing, which minimizes waste.
Since the part is already close to its final shape post-pressing, there’s less material removal required in subsequent machining processes.
Secondly, it offers excellent reproducibility and consistency in terms of dimensions and mechanical properties.
Once a CIP mold is prepared, identical parts can be produced repeatedly with minimal variation.
This consistency is particularly important in industries such as aerospace or medical devices, where precision is critical.
Thirdly, CIP molding supports a wide range of materials, including ceramics, metals, and composite materials.
This versatility makes it a preferred process in various sectors.
In addition, components made through CIP typically exhibit superior material properties, such as increased strength and durability, due to the high density achieved in the process.
Applications of CIP Molding
CIP molding finds applications across several industries.
In the automotive industry, it is used to produce parts that need to withstand high pressure and extreme temperatures.
These include engine components and structural parts.
In the aerospace industry, the need for lightweight components without compromising on strength makes CIP molding a suitable choice.
Parts such as turbine blades and structural supports are commonly manufactured using this method.
The medical industry also benefits from CIP technology.
Components for implants and surgical tools, where precision and biocompatibility are paramount, rely on the high-quality finishes that CIP molding provides.
Furthermore, the electronics industry uses this process for making components like ceramic insulators, which require precise fabrication to function correctly in delicate electronic systems.
Improving Efficiency with CIP Molding
One of the key benefits of CIP molding is the potential for efficiency improvements.
The process itself is relatively quick compared to other methods that might require extensive machining or casting.
Since the parts are pressed to near their final size, minimal machining is needed, which reduces the overall production time and material waste.
Moreover, by using CIP molding, manufacturers can reduce costs associated with tooling and machining.
Traditional manufacturing processes often require custom tools and molds for each part variation.
CIP uses flexible molds, which can be reused for different designs, thus saving both time and money.
Additionally, the durability and precision of parts produced via CIP molding mean that these components often have a longer lifespan and better performance than those made with other techniques.
This reliability can lead to fewer replacements and repairs, offering long-term savings and efficiency improvements.
Challenges with CIP Molding
While CIP molding offers many advantages, there are also some challenges.
The initial cost for setting up CIP equipment can be high, although this is often offset by the savings in material and machining costs down the road.
Moreover, the development of the initial mold requires a high level of expertise and precision.
If there is an error in the mold design, it can lead to issues in the final product.
Thus, manufacturers need skilled personnel to handle the design and production processes.
Additionally, there might be limitations in terms of the size and complexity of parts that can be produced through CIP.
This means that for very large or highly intricate designs, alternative methods might be necessary.
The Future of CIP Molding
The future of CIP molding is bright, with ongoing technological advancements promising even greater efficiency and broader applications.
Research is continually being conducted into new materials and improved processes that could further enhance the capabilities and benefits of CIP molding.
There’s also significant interest in automating CIP processes to further improve efficiency and reduce costs.
Automation could lead to more precise control over the pressurization cycle and better repeatability in large-scale production.
Furthermore, the integration of CIP with other manufacturing technologies, like additive manufacturing, could open up new possibilities for creating complex, multi-material component parts.
This could be particularly revolutionary in sectors that depend heavily on innovation, such as electronics and medical devices.
In conclusion, CIP molding is a powerful process that brings efficiency, precision, and versatility to various industries.
While there are challenges to consider, the potential benefits and future advancements make it a promising choice for many manufacturers.
As industries continue to seek ways to enhance production efficiency and product quality, CIP molding stands out as a valuable tool in achieving these goals.
資料ダウンロード
QCD調達購買管理クラウド「newji」は、調達購買部門で必要なQCD管理全てを備えた、現場特化型兼クラウド型の今世紀最高の購買管理システムとなります。
ユーザー登録
調達購買業務の効率化だけでなく、システムを導入することで、コスト削減や製品・資材のステータス可視化のほか、属人化していた購買情報の共有化による内部不正防止や統制にも役立ちます。
NEWJI DX
製造業に特化したデジタルトランスフォーメーション(DX)の実現を目指す請負開発型のコンサルティングサービスです。AI、iPaaS、および先端の技術を駆使して、製造プロセスの効率化、業務効率化、チームワーク強化、コスト削減、品質向上を実現します。このサービスは、製造業の課題を深く理解し、それに対する最適なデジタルソリューションを提供することで、企業が持続的な成長とイノベーションを達成できるようサポートします。
オンライン講座
製造業、主に購買・調達部門にお勤めの方々に向けた情報を配信しております。
新任の方やベテランの方、管理職を対象とした幅広いコンテンツをご用意しております。
お問い合わせ
コストダウンが利益に直結する術だと理解していても、なかなか前に進めることができない状況。そんな時は、newjiのコストダウン自動化機能で大きく利益貢献しよう!
(Β版非公開)