- お役立ち記事
- Improving Injection Molding Processes: Success Stories from Small Factories
月間76,176名の
製造業ご担当者様が閲覧しています*
*2025年3月31日現在のGoogle Analyticsのデータより
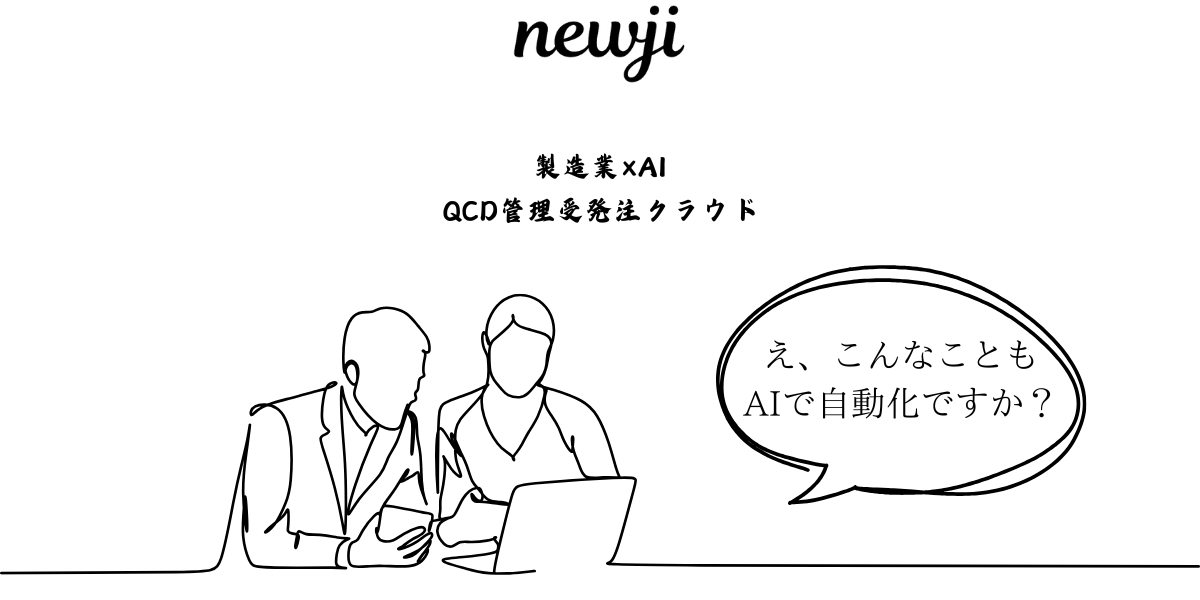
Improving Injection Molding Processes: Success Stories from Small Factories
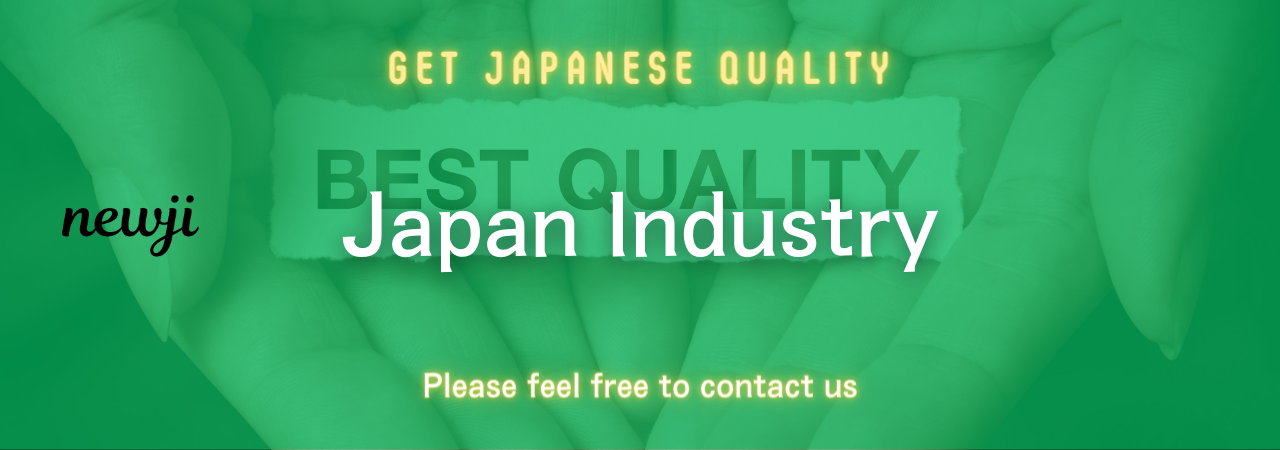
Injection molding is a popular process used in manufacturing to create plastic parts.
It is especially beneficial for small factories that need to produce intricate and detailed items efficiently.
In this article, we will explore the ways in which small factories have improved their injection molding processes.
We will share success stories that demonstrate how innovative strategies and new technologies can make significant differences.
目次
Understanding Injection Molding
Injection molding is a method where molten plastic is injected into a mold cavity to create a specific shape.
Once the plastic cools and solidifies, it is ejected from the mold, resulting in a finished product.
This method is widely used because it is cost-effective, repeatable, and capable of producing high-quality products.
Success Story: Implementing Advanced Machinery
One small factory in the Midwest struggled with their outdated injection molding machines.
These older machines were not only slow but also produced a fair number of defective parts.
The factory decided to invest in advanced injection molding machinery featuring modern control systems and higher precision.
The new machines made a remarkable difference.
The rate of defective parts dropped by 30%, and production speed increased by 25%.
Improving the machinery also reduced the need for quality checks, saving both time and resources.
Cost Efficiency and ROI
While the initial investment for advanced machinery can be substantial, the long-term benefits often outweigh the costs.
In the case of the Midwest factory, the investment paid for itself within two years through reduction in waste and increased production speed.
This provided them with a strong return on investment (ROI), allowing them to reinvest in other areas of the business.
Success Story: Optimizing the Mold Design
Another small factory found success by focusing on mold design optimization.
Initially, they faced frequent mold failures, causing downtime and increasing production costs.
By working closely with an experienced mold design engineer, they were able to identify and correct the flaws in their original molds.
The re-engineered molds had improved cooling systems and better material flow channels.
These changes resulted in a more consistent product and reduced cycle times by 20%.
Benefits of Mold Design Optimization
Optimizing mold design not only improves the quality of the final product but also enhances production efficiency.
Smaller molds that are well-designed can run faster and require less maintenance.
This directly affects the bottom line by reducing costs and increasing output.
Success Story: Utilizing Automation
A small family-owned factory decided to introduce automation into their injection molding processes.
Previously, their operations were heavily reliant on manual labor, which was not only slow but also prone to human error.
They implemented robotic arms for part extraction and assembly, along with automated quality control systems.
The introduction of automation led to a 50% reduction in labor costs and a 40% increase in production speed.
The factory also saw an improvement in the consistency and quality of the products.
Streamlined Workflow
Automation can significantly streamline workflows by minimizing human intervention.
This ensures that production runs smoothly, with fewer interruptions.
In addition to increasing speed and efficiency, automated systems are excellent for maintaining a high standard of quality.
Success Story: Enhancing Material Use
Material selection and management is crucial for the success of injection molding.
One small factory faced issues with material waste and inconsistent product quality.
They decided to switch to higher-quality raw materials that, while more expensive, reduced defects and wasted material.
After consulting with material specialists, they also began to recycle scrap plastic back into their production process.
These adjustments led to a reduction in raw material costs by 15% and improved product quality.
Recycling in Injection Molding
Recycling scrap plastic reduces waste and lowers material costs.
It also contributes to environmental sustainability by minimizing the amount of plastic waste that ends up in landfills.
For small factories, recycling can make the production process more efficient and cost-effective.
Success Story: Employee Training Programs
A small factory in the Northeast decided to invest in extensive training programs for their employees.
Initially, they faced high turnover rates and frequent production errors.
By providing comprehensive training in both technical skills and soft skills, the factory empowered its workforce.
The outcome was a significant drop in turnover rates and a marked increase in employee satisfaction and productivity.
The trained workforce was better equipped to handle complex machinery and troubleshoot issues, reducing downtime and enhancing overall efficiency.
The Value of Skilled Labor
Investing in employee training yields long-term advantages.
A skilled workforce can adapt to new technologies and workflows more quickly.
Additionally, trained employees are often more engaged and committed, leading to a more resilient and efficient production environment.
Conclusion
Improving injection molding processes can have a profound impact on small factories.
By investing in advanced machinery, optimizing mold design, embracing automation, enhancing material use, and implementing robust training programs, factories can achieve significant productivity gains and cost savings.
Success stories from various small factories illustrate that these improvements are achievable and beneficial.
Whether through cutting-edge technology or better workforce training, the possibilities for enhancing injection molding processes are abundant.
By focusing on these strategies, small factories can not only survive but thrive in a competitive marketplace.
資料ダウンロード
QCD管理受発注クラウド「newji」は、受発注部門で必要なQCD管理全てを備えた、現場特化型兼クラウド型の今世紀最高の受発注管理システムとなります。
ユーザー登録
受発注業務の効率化だけでなく、システムを導入することで、コスト削減や製品・資材のステータス可視化のほか、属人化していた受発注情報の共有化による内部不正防止や統制にも役立ちます。
NEWJI DX
製造業に特化したデジタルトランスフォーメーション(DX)の実現を目指す請負開発型のコンサルティングサービスです。AI、iPaaS、および先端の技術を駆使して、製造プロセスの効率化、業務効率化、チームワーク強化、コスト削減、品質向上を実現します。このサービスは、製造業の課題を深く理解し、それに対する最適なデジタルソリューションを提供することで、企業が持続的な成長とイノベーションを達成できるようサポートします。
製造業ニュース解説
製造業、主に購買・調達部門にお勤めの方々に向けた情報を配信しております。
新任の方やベテランの方、管理職を対象とした幅広いコンテンツをご用意しております。
お問い合わせ
コストダウンが利益に直結する術だと理解していても、なかなか前に進めることができない状況。そんな時は、newjiのコストダウン自動化機能で大きく利益貢献しよう!
(β版非公開)