- お役立ち記事
- Improving Injection Molding Quality Through Cold Slug Well Optimization
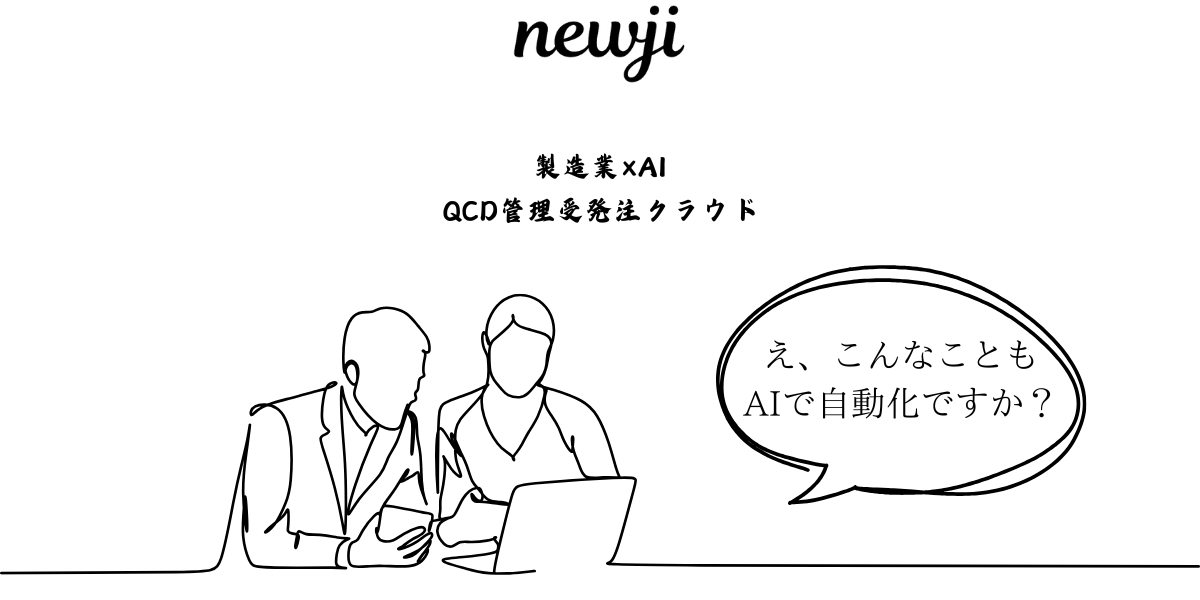
Improving Injection Molding Quality Through Cold Slug Well Optimization
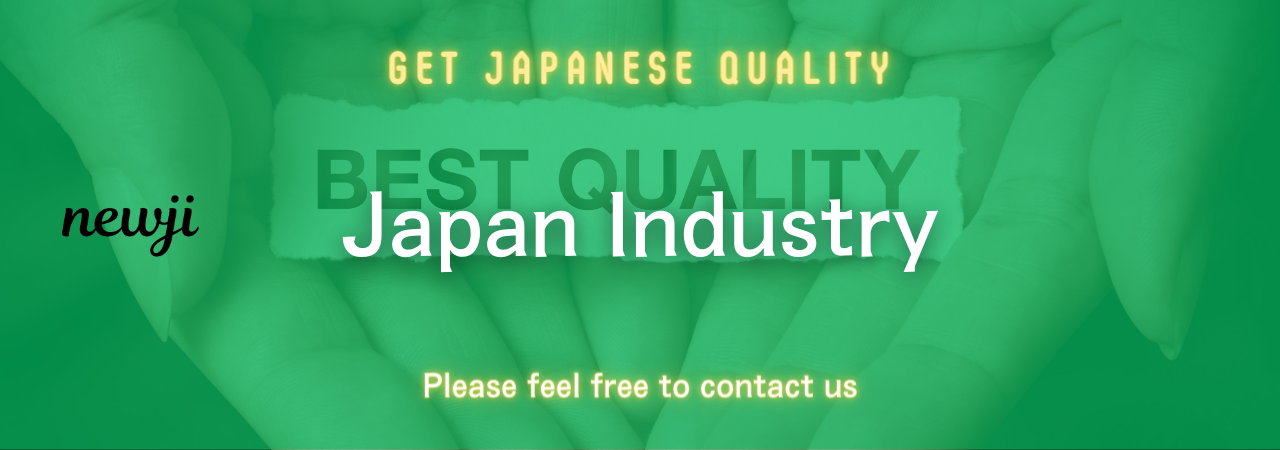
Injection molding is an essential manufacturing process used in various industries to create complex plastic components efficiently.
However, quality issues can arise if the process is not optimized correctly.
One crucial aspect of the injection molding process is the design and use of cold slug wells.
When optimized properly, cold slug wells can significantly improve the quality of the final product.
目次
What is Injection Molding?
Injection molding is a manufacturing process used to produce parts by injecting molten material into a mold.
The material, usually plastic, is heated until it becomes liquid and then injected into a mold cavity where it cools and hardens into the desired shape.
This process is widely used for producing high-volume parts with intricate designs and precise dimensions.
Despite its advantages, injection molding can face quality issues such as defects, inconsistencies, and inefficiencies.
The Importance of Cold Slug Wells
A cold slug well is a small chamber located at the end of the injection unit, just before the mold cavity.
Its primary function is to capture the “cold slug,” a small amount of cooled material that forms at the nozzle tip after each injection cycle.
If the cold slug enters the mold cavity, it can cause defects in the final product such as flow marks, voids, or weak spots.
By capturing the cold slug, the well ensures that only molten material enters the mold cavity, leading to a higher quality finish.
Benefits of Cold Slug Wells
Utilizing cold slug wells provides several advantages:
1. **Reduced Defects**: Capturing the cold slug prevents it from entering the mold cavity, reducing defects like voids and flow marks.
2. **Consistent Quality**: By ensuring that only molten material is injected, cold slug wells contribute to consistent product quality.
3. **Improved Surface Finish**: Preventing cold material from entering the mold cavity ensures a smooth and uniform surface finish.
4. **Enhanced Structural Integrity**: Reducing defects and ensuring consistent material flow enhances the overall structural integrity of the final product.
Optimizing Cold Slug Wells
For optimal performance, cold slug wells must be designed and implemented thoughtfully.
The following considerations can help achieve this:
1. Proper Placement
The placement of the cold slug well plays a critical role in its effectiveness.
It should be positioned close to the nozzle tip, just before the mold cavity.
This ensures that it captures the cold slug efficiently before it can enter the mold.
2. Appropriate Size and Shape
The size and shape of the cold slug well must be carefully designed to accommodate the expected volume of the cold slug.
It should be large enough to capture the entire cold slug but not so large that it affects the injection pressure or material flow.
3. Material Compatibility
The material used for the cold slug well should be compatible with the molten material being injected.
It should have good thermal conductivity to prevent excessive cooling of the molten material and ensure that it remains at the desired temperature throughout the injection process.
4. Regular Maintenance
Regular maintenance of the cold slug well is essential to ensure its continued performance.
Any build-up of material or debris should be removed promptly to prevent blockages and ensure smooth operation.
Challenges in Cold Slug Well Optimization
While cold slug wells offer significant benefits, optimizing them can be challenging.
Common challenges include:
Design Complexity
Designing an effective cold slug well requires careful consideration of various factors, such as the expected volume of the cold slug, the material properties, and the injection parameters.
This complexity can make it challenging to achieve the perfect design.
Cost Implications
Implementing and maintaining cold slug wells can incur additional costs.
However, these costs are often outweighed by the benefits of improved product quality and reduced defects.
Material Compatibility
Ensuring that the cold slug well material is compatible with the injected material can be challenging.
Different materials have different properties, and finding the right match requires careful selection and testing.
Overcoming Challenges
Despite these challenges, several strategies can help overcome them and achieve optimal cold slug well performance.
Simulation and Testing
Using simulation software can help predict the behavior of the cold slug well and optimize its design.
Testing different designs and materials can also help identify the most effective solution.
Expert Consultation
Consulting with experts in injection molding can provide valuable insights and recommendations for optimizing cold slug wells.
Their experience and knowledge can help navigate the complexities and achieve the best results.
Continuous Improvement
The injection molding process should be continuously monitored and improved.
Regularly reviewing and updating the cold slug well design and maintenance procedures can help maintain optimal performance and quality.
Conclusion
Cold slug wells play a crucial role in the injection molding process, helping to improve product quality and reduce defects.
By capturing the cold slug and ensuring that only molten material enters the mold cavity, they contribute to consistent product quality and enhanced structural integrity.
Optimizing cold slug wells involves careful consideration of factors such as placement, size, shape, and material compatibility.
Despite the challenges, strategies such as simulation, testing, expert consultation, and continuous improvement can help achieve optimal performance.
By focusing on cold slug well optimization, manufacturers can significantly enhance the quality of their injection molded products and achieve greater efficiency and cost-effectiveness in their processes.
資料ダウンロード
QCD調達購買管理クラウド「newji」は、調達購買部門で必要なQCD管理全てを備えた、現場特化型兼クラウド型の今世紀最高の購買管理システムとなります。
ユーザー登録
調達購買業務の効率化だけでなく、システムを導入することで、コスト削減や製品・資材のステータス可視化のほか、属人化していた購買情報の共有化による内部不正防止や統制にも役立ちます。
NEWJI DX
製造業に特化したデジタルトランスフォーメーション(DX)の実現を目指す請負開発型のコンサルティングサービスです。AI、iPaaS、および先端の技術を駆使して、製造プロセスの効率化、業務効率化、チームワーク強化、コスト削減、品質向上を実現します。このサービスは、製造業の課題を深く理解し、それに対する最適なデジタルソリューションを提供することで、企業が持続的な成長とイノベーションを達成できるようサポートします。
オンライン講座
製造業、主に購買・調達部門にお勤めの方々に向けた情報を配信しております。
新任の方やベテランの方、管理職を対象とした幅広いコンテンツをご用意しております。
お問い合わせ
コストダウンが利益に直結する術だと理解していても、なかなか前に進めることができない状況。そんな時は、newjiのコストダウン自動化機能で大きく利益貢献しよう!
(Β版非公開)