- お役立ち記事
- Improving Logistics Layout
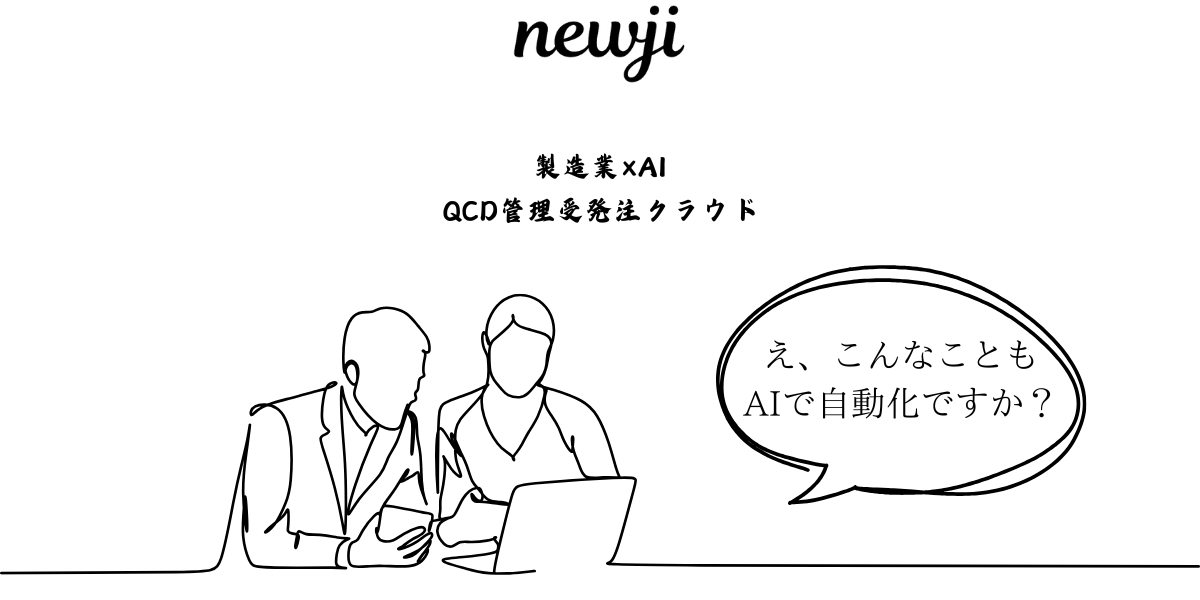
Improving Logistics Layout
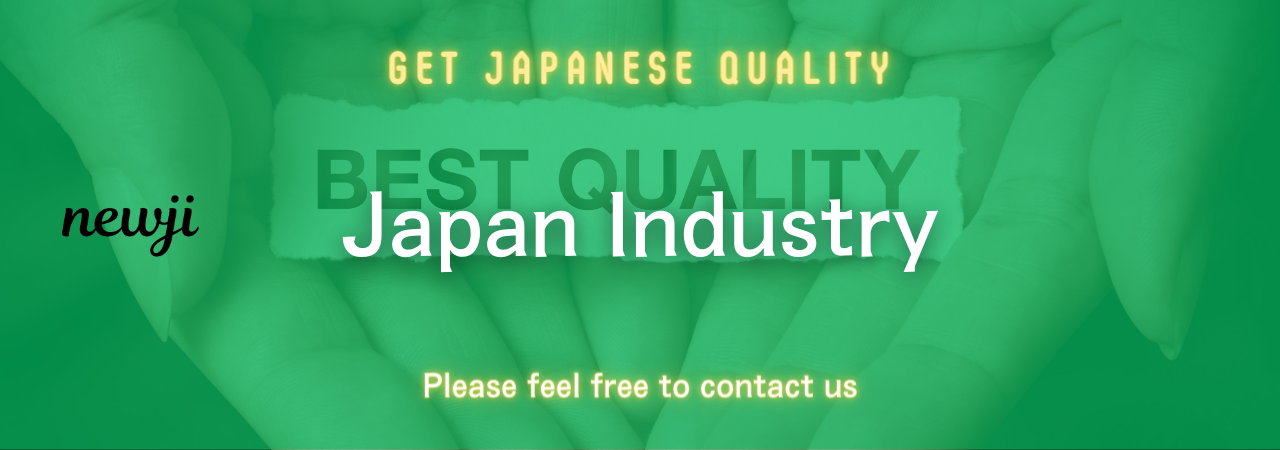
Improving logistics layout can lead to significant benefits for businesses, including reduced costs, increased efficiency, and higher customer satisfaction.
Focusing on optimizing the space, workflow, and storage solutions, businesses can create a streamlined operation that maximizes productivity.
目次
Understanding Logistics Layout
Before diving into improvements, it’s essential to understand what logistics layout entails.
Logistics layout refers to the arrangement of physical elements in a warehouse or distribution center.
This includes the placement of inventory, workstations, equipment, and pathways for transportation.
A well-designed logistics layout ensures smooth material flow and minimizes waste, delays, and errors.
The Importance of a Good Layout
A well-structured logistics layout is critical for several reasons.
Firstly, it improves operational efficiency by enabling faster and more accurate order processing.
Workers can easily navigate the space, access inventory, and complete tasks without unnecessary movement or searching.
Secondly, it enhances safety by reducing the risk of accidents and injuries.
Clear pathways, organized storage, and proper signage help prevent mishaps and create a safer work environment.
Finally, a good logistics layout supports scalability.
As a business grows, the layout can be adjusted to accommodate increased demand without causing disruption.
Key Elements of an Effective Logistics Layout
To improve logistics layout, several key elements should be considered:
Space Utilization
Maximizing the use of available space is crucial.
This involves optimizing storage solutions, such as using vertical space through shelving and racks.
Implementing high-density storage systems can also increase capacity and improve access to items.
Workflow Optimization
Designing a layout that supports a logical workflow is essential for efficiency.
This includes arranging equipment and workstations in a manner that minimizes travel time and maximizes productivity.
Consider the sequence of operations and ensure that related tasks are grouped together.
Ergonomics
Taking ergonomics into account can reduce worker fatigue and prevent injuries.
This involves designing workstations at appropriate heights, providing anti-fatigue mats, and ensuring that tools and materials are within easy reach.
Technology Integration
Implementing technology, such as warehouse management systems (WMS) and automated guided vehicles (AGVs), can enhance the efficiency of a logistics layout.
These systems help streamline processes, track inventory, and automate repetitive tasks.
Steps to Improve Logistics Layout
Improving logistics layout involves several steps:
Analyze Current Layout
Start by analyzing the existing layout.
Identify bottlenecks, areas of waste, and inefficiencies.
This can be done through observing operations, collecting data, and seeking feedback from employees.
Set Clear Objectives
Define clear objectives for the improvements.
These could include reducing travel time, increasing storage capacity, or enhancing safety.
Having specific goals will guide the redesign process.
Design the New Layout
With clear objectives in mind, create a new layout design.
Consider factors such as space utilization, workflow optimization, and ergonomics.
Use layout planning tools or software to visualize the changes and make necessary adjustments.
Implement the Changes
Carefully implement the new layout design.
This may involve rearranging equipment, installing new storage solutions, and updating signage.
Ensure minimal disruption to operations during the transition.
Monitor and Adjust
Once the new layout is in place, monitor its performance.
Collect data and gather feedback to identify any remaining issues or areas for further improvement.
Make adjustments as needed to ensure optimal efficiency.
Case Study: Successful Logistics Layout Improvement
To understand the impact of improving logistics layout, consider the case of XYZ Company (a hypothetical example).
XYZ Company, a medium-sized e-commerce business, struggled with slow order processing and frequent stockouts.
To address these issues, they decided to revamp their logistics layout.
After analyzing their current setup, they identified several bottlenecks, including inefficient storage solutions and lengthy travel times for picking orders.
Their objectives were to reduce order processing time and increase storage capacity.
The new layout design involved implementing high-density shelving systems, reorganizing workstations to follow a logical workflow, and introducing a WMS to streamline inventory tracking.
These changes were implemented with minimal disruption to operations.
As a result, XYZ Company saw a 20% reduction in order processing time and a 15% increase in storage capacity.
Employee satisfaction improved due to the ergonomic workstations and clear pathways, leading to a decrease in workplace injuries.
Conclusion
Improving logistics layout is a critical step for businesses seeking to enhance efficiency, reduce costs, and increase customer satisfaction.
By focusing on key elements such as space utilization, workflow optimization, ergonomics, and technology integration, businesses can create a streamlined operation that maximizes productivity.
Through careful analysis, clear objectives, thoughtful design, and ongoing monitoring, companies can achieve significant improvements in their logistics layout, leading to long-term success.
資料ダウンロード
QCD調達購買管理クラウド「newji」は、調達購買部門で必要なQCD管理全てを備えた、現場特化型兼クラウド型の今世紀最高の購買管理システムとなります。
ユーザー登録
調達購買業務の効率化だけでなく、システムを導入することで、コスト削減や製品・資材のステータス可視化のほか、属人化していた購買情報の共有化による内部不正防止や統制にも役立ちます。
NEWJI DX
製造業に特化したデジタルトランスフォーメーション(DX)の実現を目指す請負開発型のコンサルティングサービスです。AI、iPaaS、および先端の技術を駆使して、製造プロセスの効率化、業務効率化、チームワーク強化、コスト削減、品質向上を実現します。このサービスは、製造業の課題を深く理解し、それに対する最適なデジタルソリューションを提供することで、企業が持続的な成長とイノベーションを達成できるようサポートします。
オンライン講座
製造業、主に購買・調達部門にお勤めの方々に向けた情報を配信しております。
新任の方やベテランの方、管理職を対象とした幅広いコンテンツをご用意しております。
お問い合わせ
コストダウンが利益に直結する術だと理解していても、なかなか前に進めることができない状況。そんな時は、newjiのコストダウン自動化機能で大きく利益貢献しよう!
(Β版非公開)