- お役立ち記事
- Improving Manufacturing Efficiency with the Kanban System
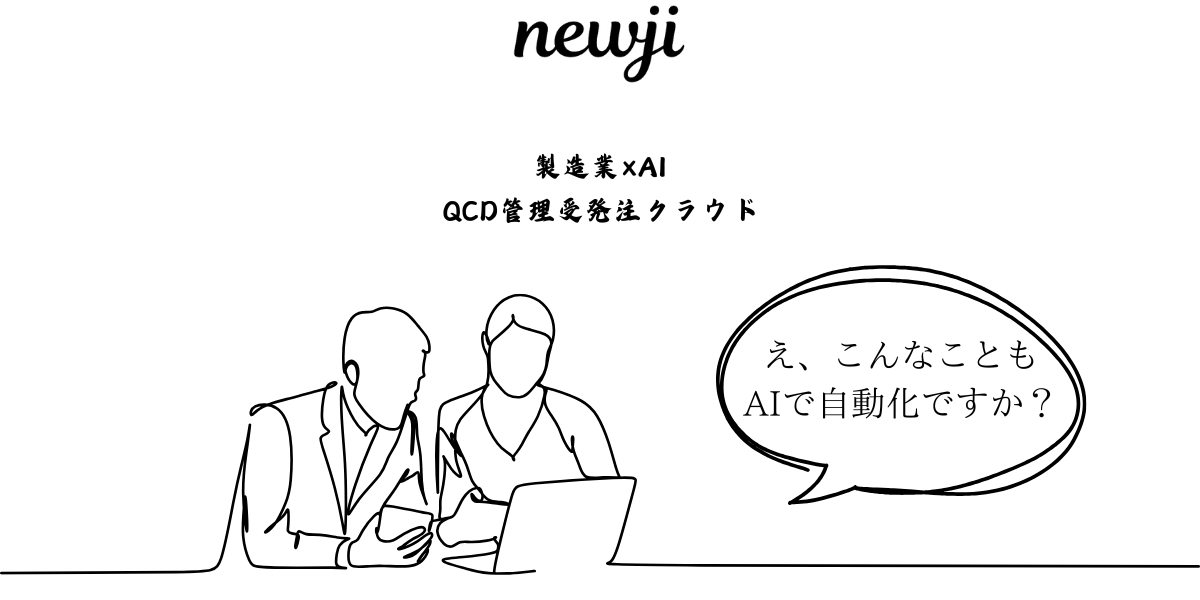
Improving Manufacturing Efficiency with the Kanban System
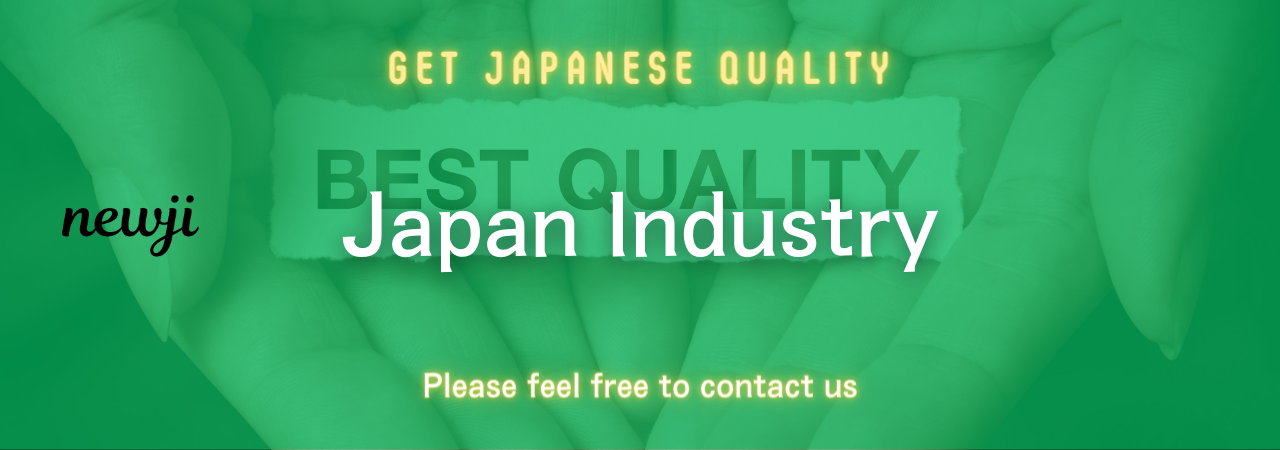
In today’s competitive market, manufacturers must find ways to improve efficiency and reduce waste.
One popular method for achieving these goals is the Kanban system.
This article explains how the Kanban system can help enhance manufacturing efficiency and why it’s particularly effective.
目次
What is the Kanban System?
The Kanban system is a visual workflow management method.
Originating from Japan, it was first developed by Toyota to boost production efficiency.
Kanban means “signboard” or “billboard” in Japanese.
Its primary purpose is to signal the need for more resources in the production process.
By utilizing visual signals, manufacturers can streamline operations and minimize waste.
How Does the Kanban System Work?
The Kanban system operates with the help of Kanban cards.
Each card represents a work item or task that needs to be done.
These cards are moved through different stages of production as work progresses.
Typically, a Kanban board, divided into columns, is used to track tasks.
Each column represents a stage in the production process, such as “to-do,” “in progress,” and “done.”
Benefits of Using Kanban Cards and Boards
Kanban cards and boards bring several advantages to the manufacturing process:
1. **Improved Visibility:** Workers can see at a glance what tasks need to be done and what stage they are in.
2. **Better Communication:** Team members can easily understand their responsibilities and deadlines.
3. **Increased Flexibility:** The system allows for quick adjustments if there are changes in demand or resources.
4. **Waste Reduction:** By visualizing the workflow, it becomes easier to spot inefficiencies and areas of waste.
Steps to Implement the Kanban System
Implementing the Kanban system involves several key steps:
1. Analyze Your Current Workflow
Before introducing Kanban, examine your existing production process.
Identify stages where delays or bottlenecks occur.
Understanding your current workflow will help in designing an effective Kanban system.
2. Design the Kanban Board
Next, create a Kanban board that represents your production process.
Divide the board into columns, each representing a different stage of production.
Make sure to include an initial “to-do” column and a final “done” column.
3. Create Kanban Cards
Design the Kanban cards for each task in your workflow.
Include necessary details like task description, deadlines, and responsible persons.
Ensure that the cards are clear and easy to understand.
4. Establish Work-in-Progress (WIP) Limits
To avoid overburdening your team, set Work-in-Progress (WIP) limits for each column.
These limits restrict the number of tasks that can be in a particular stage at any given time.
WIP limits help maintain a steady workflow and prevent bottlenecks.
5. Monitor and Adjust
After implementing the Kanban system, regularly monitor its performance.
Gather feedback from team members and make adjustments as necessary.
Keep an eye out for new bottlenecks and areas for improvement.
Real-world Applications of the Kanban System
Many industries have successfully adopted the Kanban system to improve efficiency.
Automotive Industry
Toyota, the birthplace of Kanban, continues to use the system in its production lines.
By minimizing inventory levels and keeping production flexible, Toyota can quickly respond to market demands.
Healthcare
In hospitals, Kanban helps manage patient flow and resource allocation.
For example, it ensures that medical supplies are restocked promptly, preventing shortages and delays.
Software Development
Software companies use Kanban to manage tasks and improve project timelines.
With clear visibility of project stages, teams can prioritize tasks and meet deadlines more effectively.
The Impact of Kanban on Manufacturing Efficiency
Kanban’s visual approach has a significant impact on manufacturing efficiency.
It helps in minimizing waste, reducing production costs, and improving product quality.
Minimizing Waste
By highlighting bottlenecks and inefficiencies, Kanban helps identify waste in the production process.
Eliminating these bottlenecks can lead to a smoother workflow and better resource utilization.
Reducing Production Costs
With improved workflow and reduced waste, production costs can be significantly decreased.
Fewer idle times and optimal use of resources contribute to cost savings.
Improving Product Quality
Kanban encourages a focus on completing tasks correctly the first time.
This attention to detail results in higher quality products and fewer defects.
Conclusion
The Kanban system can greatly improve manufacturing efficiency through its visual workflow management strategy.
By using Kanban cards and boards, manufacturers can achieve better visibility, communication, and flexibility.
Implementing Kanban involves analyzing your current workflow, designing the Kanban board, creating Kanban cards, and setting WIP limits.
Real-world applications across various industries illustrate the system’s effectiveness.
Ultimately, adopting the Kanban system leads to minimized waste, reduced production costs, and improved product quality.
Make the switch to Kanban and see the positive impact on your manufacturing process.
資料ダウンロード
QCD調達購買管理クラウド「newji」は、調達購買部門で必要なQCD管理全てを備えた、現場特化型兼クラウド型の今世紀最高の購買管理システムとなります。
ユーザー登録
調達購買業務の効率化だけでなく、システムを導入することで、コスト削減や製品・資材のステータス可視化のほか、属人化していた購買情報の共有化による内部不正防止や統制にも役立ちます。
NEWJI DX
製造業に特化したデジタルトランスフォーメーション(DX)の実現を目指す請負開発型のコンサルティングサービスです。AI、iPaaS、および先端の技術を駆使して、製造プロセスの効率化、業務効率化、チームワーク強化、コスト削減、品質向上を実現します。このサービスは、製造業の課題を深く理解し、それに対する最適なデジタルソリューションを提供することで、企業が持続的な成長とイノベーションを達成できるようサポートします。
オンライン講座
製造業、主に購買・調達部門にお勤めの方々に向けた情報を配信しております。
新任の方やベテランの方、管理職を対象とした幅広いコンテンツをご用意しております。
お問い合わせ
コストダウンが利益に直結する術だと理解していても、なかなか前に進めることができない状況。そんな時は、newjiのコストダウン自動化機能で大きく利益貢献しよう!
(Β版非公開)