- お役立ち記事
- Improving Manufacturing Processes with QC Circles
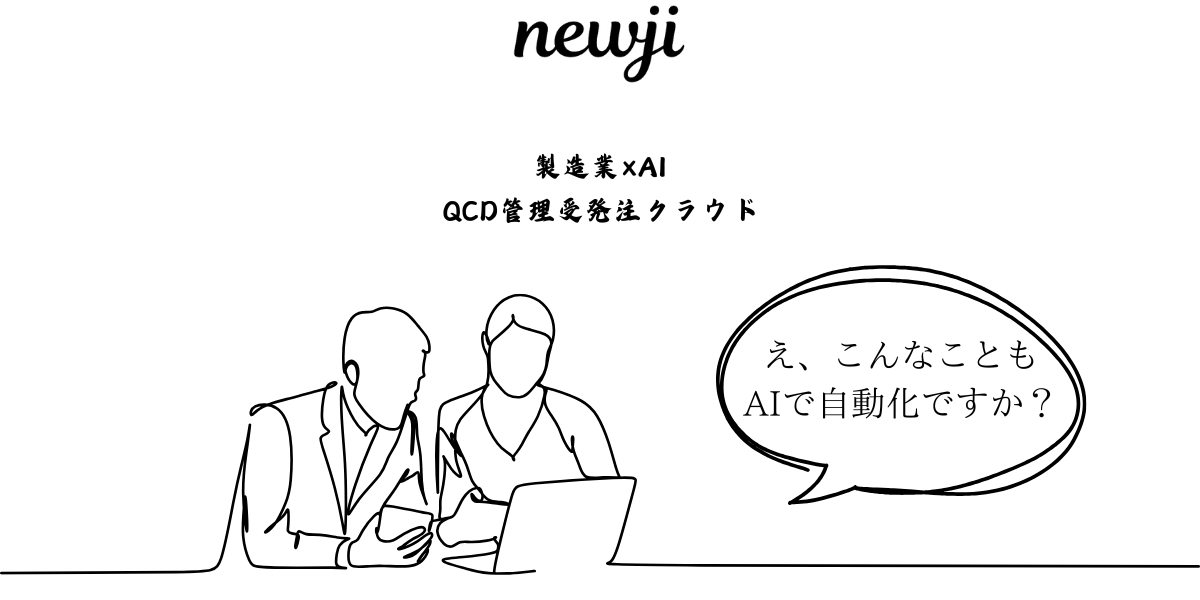
Improving Manufacturing Processes with QC Circles
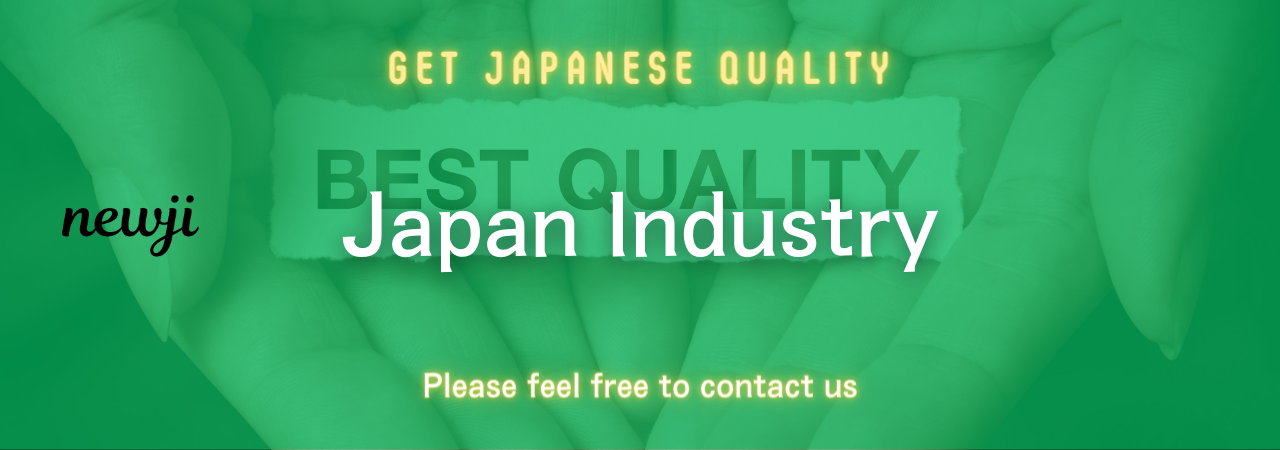
In the world of manufacturing, efficiency and quality are paramount.
It’s essential to continuously improve processes to maintain a competitive edge.
One effective method to achieve this is by implementing Quality Control (QC) circles.
These are small groups of workers who regularly meet to discuss and solve production-related problems.
This collaborative approach can lead to significant improvements in quality and productivity.
In this article, we’ll explore how QC circles can enhance manufacturing processes.
目次
Understanding QC Circles
QC circles originated in Japan during the 1960s and have since spread globally.
The concept is simple: involve frontline workers in identifying issues and brainstorming solutions.
These employees, who are directly involved in the production process, often have valuable insights that managers or engineers might overlook.
QC circles are usually composed of 6 to 10 members who meet regularly.
The goal is to foster a sense of ownership and accountability among workers.
The Purpose of QC Circles
The primary objective of QC circles is to improve product quality and operational efficiency.
By encouraging employees to participate in problem-solving, manufacturers can tap into a wealth of on-the-ground knowledge.
Other purposes include:
– Enhancing team spirit and motivation.
– Developing employees’ problem-solving skills.
– Promoting a culture of continuous improvement.
The Operational Framework of QC Circles
For QC circles to be effective, they must operate within a structured framework.
This usually involves several steps:
Identifying Problems
Employees observe and document issues in their daily work.
These can range from minor nuisances to significant bottlenecks slowing down production.
Each member’s input is valuable, and no problem is too small to warrant attention.
Analyzing Root Causes
Once a problem is identified, the next step is to investigate its root cause.
This involves analyzing data, conducting discussions, and sometimes performing experiments.
The aim is to understand the underlying issues rather than just treating symptoms.
Brainstorming Solutions
Members of the circle then brainstorm possible solutions to the identified problem.
Creativity is encouraged, and all ideas are considered.
The collaborative nature of this process often leads to innovative solutions that might not emerge in a top-down approach.
Implementing Solutions
After a feasible solution is agreed upon, it is implemented in the production process.
This phase might involve modifying machinery, adjusting workflows, or introducing new tools.
Employees are usually responsible for carrying out these changes.
Reviewing Results
It’s crucial to monitor the outcomes of any implemented solution.
The team reviews data and feedback to determine if the problem has been resolved.
If not, the circle revises their approach, learning from any mistakes.
Benefits of QC Circles
Implementing QC circles can lead to numerous benefits for both the company and its employees.
Improved Quality and Efficiency
By addressing problems at the grassroots level, QC circles can significantly improve the quality of products.
They help identify inefficiencies, reduce waste, and streamline processes.
Over time, this leads to higher productivity and better use of resources.
Employee Empowerment
Involving workers in decision-making processes empowers them.
When employees feel that their opinions matter, they are more engaged and motivated.
This can lead to a more motivated and satisfied workforce.
Cost Reduction
By solving quality issues and streamlining processes, companies can save considerable amounts of money.
Reduced waste, fewer defects, and more efficient operations all contribute to cost savings.
Enhanced Communication
QC circles foster open communication among employees.
Team members discuss problems and potential solutions, improving overall communication within the company.
This can lead to a more cohesive and collaborative working environment.
Implementing QC Circles: Best Practices
For companies looking to implement QC circles, several best practices can maximize their effectiveness.
Management Support
Management must support QC circles for them to succeed.
This includes providing time for meetings, resources for implementing solutions, and recognition for achievements.
Management should also be open to feedback and willing to make necessary changes based on QC circle recommendations.
Training
Employees need training to effectively participate in QC circles.
This can include training on problem-solving techniques, data analysis, and effective communication.
Ongoing training ensures that team members continue to develop their skills.
Clear Objectives
Each QC circle should have clear objectives and goals.
These goals should be specific, measurable, and achievable.
Clear objectives help keep the group focused and ensure that efforts are aligned with overall company goals.
Regular Meetings
QC circles should meet regularly to maintain momentum and address issues promptly.
Regular meetings also help build team cohesion and keep everyone engaged in the process.
Conclusion
QC circles offer a powerful way to improve manufacturing processes.
By involving frontline workers in problem-solving, companies can tap into valuable insights and foster a culture of continuous improvement.
When implemented correctly, QC circles can lead to improved quality, efficiency, and employee satisfaction.
With management support and proper training, any manufacturing company can harness the benefits of QC circles to stay competitive in today’s fast-paced market.
資料ダウンロード
QCD調達購買管理クラウド「newji」は、調達購買部門で必要なQCD管理全てを備えた、現場特化型兼クラウド型の今世紀最高の購買管理システムとなります。
ユーザー登録
調達購買業務の効率化だけでなく、システムを導入することで、コスト削減や製品・資材のステータス可視化のほか、属人化していた購買情報の共有化による内部不正防止や統制にも役立ちます。
NEWJI DX
製造業に特化したデジタルトランスフォーメーション(DX)の実現を目指す請負開発型のコンサルティングサービスです。AI、iPaaS、および先端の技術を駆使して、製造プロセスの効率化、業務効率化、チームワーク強化、コスト削減、品質向上を実現します。このサービスは、製造業の課題を深く理解し、それに対する最適なデジタルソリューションを提供することで、企業が持続的な成長とイノベーションを達成できるようサポートします。
オンライン講座
製造業、主に購買・調達部門にお勤めの方々に向けた情報を配信しております。
新任の方やベテランの方、管理職を対象とした幅広いコンテンツをご用意しております。
お問い合わせ
コストダウンが利益に直結する術だと理解していても、なかなか前に進めることができない状況。そんな時は、newjiのコストダウン自動化機能で大きく利益貢献しよう!
(Β版非公開)