- お役立ち記事
- Improving Material Management in Manufacturing with MRP (Material Requirements Planning)
Improving Material Management in Manufacturing with MRP (Material Requirements Planning)
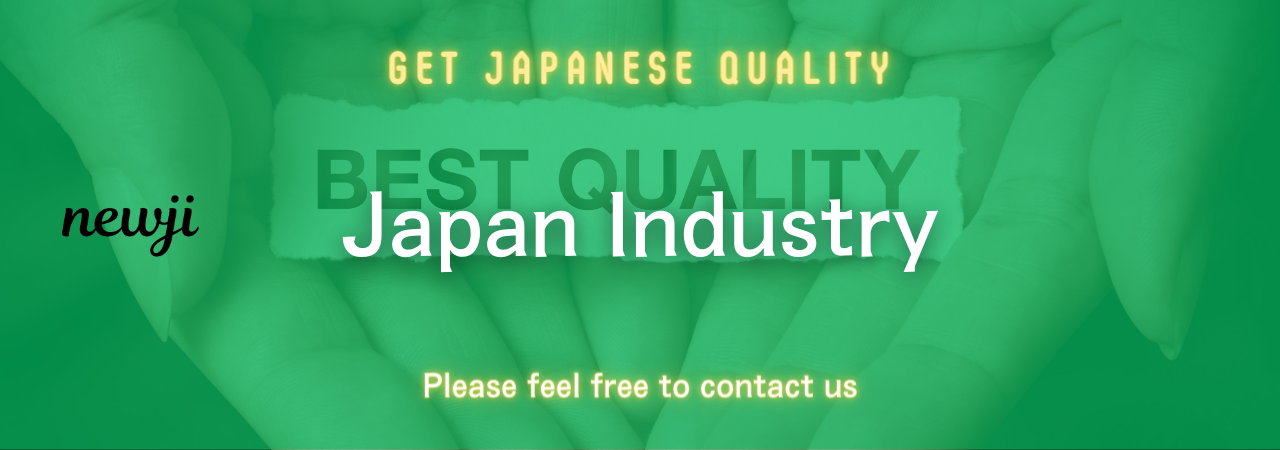
In today’s fast-paced and competitive manufacturing industry, proper management of materials is crucial. Without an efficient system in place, companies can face delays, increased costs, and decreased productivity. This is where Material Requirements Planning (MRP) comes into play.
MRP is a system that helps manufacturers manage their materials more effectively. It ensures that the right materials are available at the right time, reducing waste and improving production efficiency.
目次
What is MRP?
MRP, or Material Requirements Planning, is a computer-based inventory management system. It helps manufacturers plan the necessary raw materials and components needed for production. By utilizing MRP, companies can ensure that they have enough materials to meet customer demand without holding excessive inventory.
At its core, MRP works by analyzing the production schedule and determining the materials required. It takes into account factors such as lead time, order quantities, and production capacity. This helps manufacturers plan their material orders more accurately and efficiently.
Benefits of MRP
Implementing MRP can offer numerous benefits to manufacturers. Here are some of the key advantages:
1. Improved Inventory Control
With MRP, manufacturers can gain better control over their inventory. The system helps to minimize excess inventory, reducing the costs associated with storing and managing surplus materials. This leads to cost savings and more efficient use of storage space.
2. Enhanced Production Planning
MRP allows manufacturers to plan their production schedules more effectively. By knowing the exact materials needed for each production run, companies can avoid delays caused by material shortages. This leads to smoother production processes and improved on-time delivery to customers.
3. Reduced Waste
By accurately planning material requirements, MRP helps to reduce waste. Manufacturers can order the right amount of materials, minimizing the chances of overproduction or excess inventory. This not only saves costs but also contributes to a more sustainable manufacturing process.
4. Increased Efficiency
With MRP, manufacturers can streamline their production processes. The system automates many tasks, such as calculating material requirements and generating purchase orders. This reduces the reliance on manual processes, freeing up time for employees to focus on more strategic tasks.
5. Better Customer Service
Improved material management through MRP leads to better customer service. By ensuring that materials are available when needed, manufacturers can meet customer demands more consistently. This helps to build stronger relationships with customers and enhance overall satisfaction.
How MRP Works
To understand how MRP works, let’s take a closer look at its key components and processes:
1. Master Production Schedule (MPS)
The MPS is a detailed plan that outlines the quantities and timing of production. It specifies what products need to be manufactured and when they should be completed. The MPS serves as the foundation for MRP calculations, as it determines the materials required for production.
2. Bill of Materials (BOM)
The BOM is a comprehensive list of all the materials and components needed to produce a finished product. It includes information such as part numbers, descriptions, and quantities. The BOM is used by the MRP system to determine the materials required for production.
3. Inventory Records
The MRP system maintains detailed records of the inventory on hand, including quantities and locations. This information is crucial for accurate material planning. By knowing the current inventory levels, the system can determine the additional materials needed to meet production requirements.
4. Material Requirements Plan
Using the data from the MPS, BOM, and inventory records, the MRP system generates a Material Requirements Plan. This plan outlines the specific materials needed for each production run, as well as the timing of when these materials are required. It helps to ensure that the right materials are available at the right time.
5. Purchase Orders and Production Orders
Based on the Material Requirements Plan, the MRP system generates purchase orders for the required materials. These purchase orders are sent to suppliers, ensuring that the materials are delivered in a timely manner. Additionally, production orders are created for internal manufacturing processes, specifying the quantities and timing of production.
Implementing MRP in Your Manufacturing Process
While MRP offers many benefits, successful implementation requires careful planning and consideration. Here are some key steps to help you implement MRP in your manufacturing process:
1. Assess Your Current Processes
Begin by evaluating your current material management processes. Identify any inefficiencies, bottlenecks, or areas for improvement. This will help you understand how MRP can address these issues and provide a clear roadmap for implementation.
2. Choose the Right MRP System
There are various MRP software solutions available in the market. Research and choose a system that aligns with your specific needs and requirements. Consider factors such as scalability, ease of use, and integration capabilities with your existing systems.
3. Train Your Team
Proper training is essential for successful MRP implementation. Ensure that your team understands how to use the MRP system effectively. Provide training sessions and resources to help them navigate the software and utilize its features to their fullest potential.
4. Data Accuracy
Accurate data is critical for MRP to function effectively. Ensure that your inventory records, BOM, and MPS are up to date and accurate. Regularly review and update this data to maintain the integrity of your MRP system.
5. Monitor and Adjust
Once MRP is implemented, continuously monitor its performance and make necessary adjustments. Regularly review the system’s outputs and address any discrepancies or issues that arise. This will help to optimize the benefits of MRP and ensure ongoing success.
In conclusion, MRP is a powerful tool for improving material management in manufacturing. By implementing MRP, manufacturers can achieve better inventory control, enhanced production planning, reduced waste, increased efficiency, and improved customer service. By following the steps outlined above, you can successfully integrate MRP into your manufacturing process and reap its many benefits.
資料ダウンロード
QCD調達購買管理クラウド「newji」は、調達購買部門で必要なQCD管理全てを備えた、現場特化型兼クラウド型の今世紀最高の購買管理システムとなります。
ユーザー登録
調達購買業務の効率化だけでなく、システムを導入することで、コスト削減や製品・資材のステータス可視化のほか、属人化していた購買情報の共有化による内部不正防止や統制にも役立ちます。
NEWJI DX
製造業に特化したデジタルトランスフォーメーション(DX)の実現を目指す請負開発型のコンサルティングサービスです。AI、iPaaS、および先端の技術を駆使して、製造プロセスの効率化、業務効率化、チームワーク強化、コスト削減、品質向上を実現します。このサービスは、製造業の課題を深く理解し、それに対する最適なデジタルソリューションを提供することで、企業が持続的な成長とイノベーションを達成できるようサポートします。
オンライン講座
製造業、主に購買・調達部門にお勤めの方々に向けた情報を配信しております。
新任の方やベテランの方、管理職を対象とした幅広いコンテンツをご用意しております。
お問い合わせ
コストダウンが利益に直結する術だと理解していても、なかなか前に進めることができない状況。そんな時は、newjiのコストダウン自動化機能で大きく利益貢献しよう!
(Β版非公開)