- お役立ち記事
- Improving production efficiency by customizing manufacturing equipment
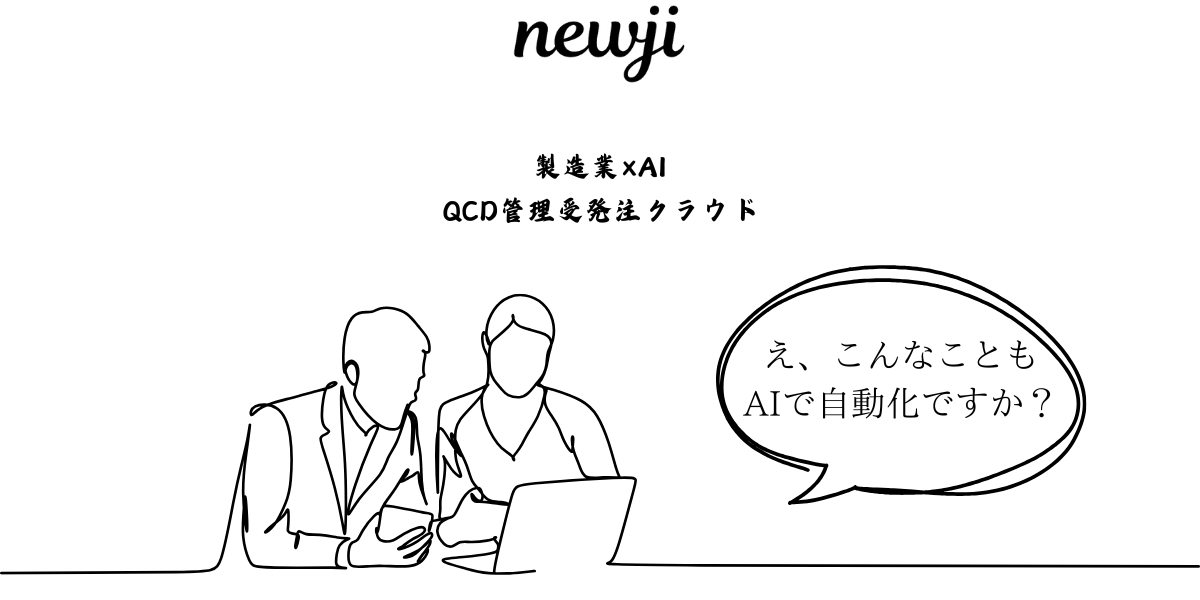
Improving production efficiency by customizing manufacturing equipment
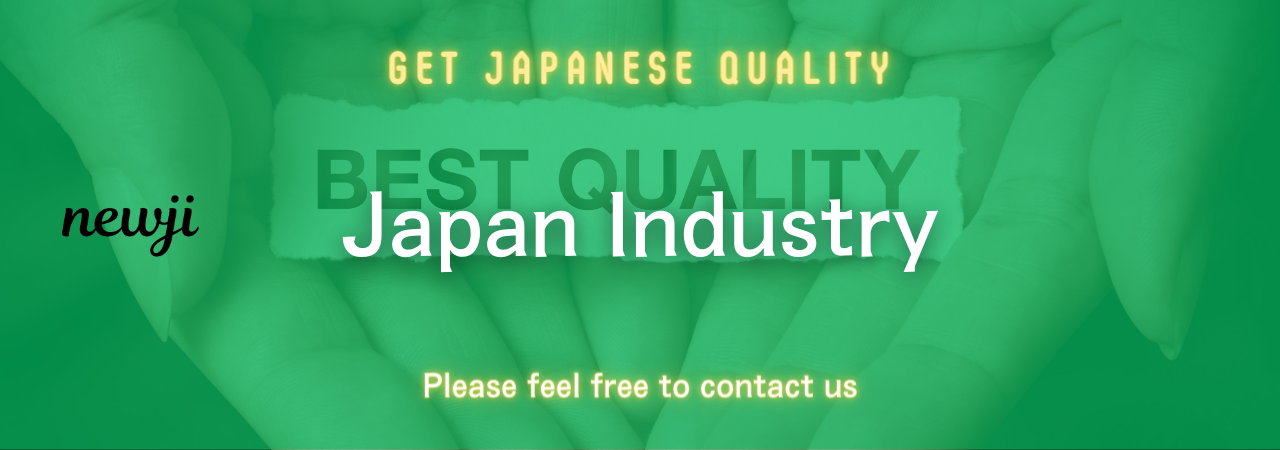
目次
Understanding Production Efficiency
Production efficiency is a measure of how well a manufacturing process converts inputs into outputs.
It is a critical factor that affects a company’s ability to compete in the market by improving cost-effectiveness and product quality.
To achieve optimal production efficiency, companies often need to assess their equipment, processes, and human resources.
In today’s competitive landscape, manufacturers are constantly seeking ways to improve their production efficiency.
One effective strategy is to customize manufacturing equipment to better meet the specific needs of production processes.
The Role of Customization in Manufacturing
Customization of manufacturing equipment involves modifying machinery or creating specialized tools to better align with the product requirements and workflow.
By tailoring equipment to their specific needs, manufacturers can significantly increase output, decrease waste, and reduce downtime.
When manufacturers employ standardized equipment, they may face limitations because such machines are designed to perform generic tasks.
These standard machines might not perform optimally for specialized or complex production processes, which can lead to inefficiencies.
Customization, therefore, becomes a crucial approach to bridging this gap.
Benefits of Customizing Manufacturing Equipment
Customizing manufacturing equipment offers multiple benefits that can lead to improved production efficiency.
1. **Enhanced Performance:**
Custom equipment can be designed to perform specific tasks more proficiently than generic machinery.
This enhancement can increase the speed and accuracy of production processes.
2. **Reduced Downtime:**
Custom equipment can be tailored to minimize the likelihood of breakdowns and maintenance issues, which subsequently reduces production downtime.
Reduced downtime ensures that production schedules remain on track, thereby enhancing efficiency.
3. **Increased Flexibility:**
Customization allows manufacturers to adapt their production lines more readily to changes in product design or variations in production volume.
This flexibility is essential in meeting market demands and staying ahead of competitors.
4. **Waste Reduction:**
By designing equipment that precisely meets production needs, manufacturers can minimize material waste during the production process.
Waste reduction not only leads to cost savings but also contributes to sustainability efforts.
5. **Quality Improvements:**
Custom equipment can improve product quality by ensuring consistent processing according to specific standards and tolerances.
Consistency in production translates to better-quality end products, which enhances customer satisfaction.
Steps to Implement Customization in Manufacturing
To successfully customize manufacturing equipment, companies should follow a structured approach.
Identify Specific Needs
The first step in customization is to understand the unique requirements of your production process.
Analyze aspects such as the type of materials you are working with, the desired product features, and any current limitations of your existing equipment.
This analysis will help identify what modifications or specialized machinery are needed.
Engage with Experts
Once you’ve identified your needs, it is crucial to engage with experts who specialize in manufacturing equipment customization.
Engineers and equipment suppliers with expertise in this field can provide valuable insights and propose solutions tailored to your requirements.
They can guide you in the design and development of custom machinery.
Design and Develop
Work with your chosen partners to design and develop the custom equipment.
This phase involves drafting detailed plans, selecting appropriate materials, and ensuring the design aligns with safety and operational standards.
Prototypes may be created to test and refine the equipment before full-scale production.
Test and Optimize
Once the equipment is developed, rigorous testing is essential to ensure it operates as expected within your production environment.
During testing, identify any areas for improvement, and make necessary adjustments to optimize performance.
Testing helps in ensuring that the equipment meets all production requirements and delivers the expected efficiency gains.
Train Staff
Training staff on using the new equipment is crucial for the successful implementation of custom machinery.
Employees should understand how to operate the machinery safely and efficiently, as well as troubleshoot common issues.
Well-trained staff can significantly contribute to maximizing the benefits of customized equipment.
Challenges and Considerations
While customizing manufacturing equipment can yield significant benefits, it is important to acknowledge potential challenges.
Initial Costs
One of the primary considerations is the cost of customization.
Developing and implementing custom equipment may require a substantial initial investment.
However, the long-term savings and efficiency improvements often justify the cost.
Time Investment
The customization process can be time-consuming, from the design and development phase to testing and implementation.
Companies need to plan carefully to minimize disruptions to their production schedules while integrating new equipment.
Technical Expertise
Customization requires specialized knowledge and technical expertise, which may not be readily available in-house.
Partnering with experienced engineers and suppliers is essential to overcome this challenge.
Conclusion
Customizing manufacturing equipment is a powerful strategy for improving production efficiency.
By tailoring machinery to meet specific production needs, manufacturers can achieve enhanced performance, reduced downtime, increased flexibility, waste reduction, and improved product quality.
Though the process involves initial investments in time and resources, the long-term benefits make it a worthy consideration.
By carefully planning and executing equipment customization, manufacturers can position themselves for greater success in the competitive marketplace.
資料ダウンロード
QCD調達購買管理クラウド「newji」は、調達購買部門で必要なQCD管理全てを備えた、現場特化型兼クラウド型の今世紀最高の購買管理システムとなります。
ユーザー登録
調達購買業務の効率化だけでなく、システムを導入することで、コスト削減や製品・資材のステータス可視化のほか、属人化していた購買情報の共有化による内部不正防止や統制にも役立ちます。
NEWJI DX
製造業に特化したデジタルトランスフォーメーション(DX)の実現を目指す請負開発型のコンサルティングサービスです。AI、iPaaS、および先端の技術を駆使して、製造プロセスの効率化、業務効率化、チームワーク強化、コスト削減、品質向上を実現します。このサービスは、製造業の課題を深く理解し、それに対する最適なデジタルソリューションを提供することで、企業が持続的な成長とイノベーションを達成できるようサポートします。
オンライン講座
製造業、主に購買・調達部門にお勤めの方々に向けた情報を配信しております。
新任の方やベテランの方、管理職を対象とした幅広いコンテンツをご用意しております。
お問い合わせ
コストダウンが利益に直結する術だと理解していても、なかなか前に進めることができない状況。そんな時は、newjiのコストダウン自動化機能で大きく利益貢献しよう!
(Β版非公開)