- お役立ち記事
- Improving production efficiency by shortening parts lead time Benefits of coordination between purchasing and production
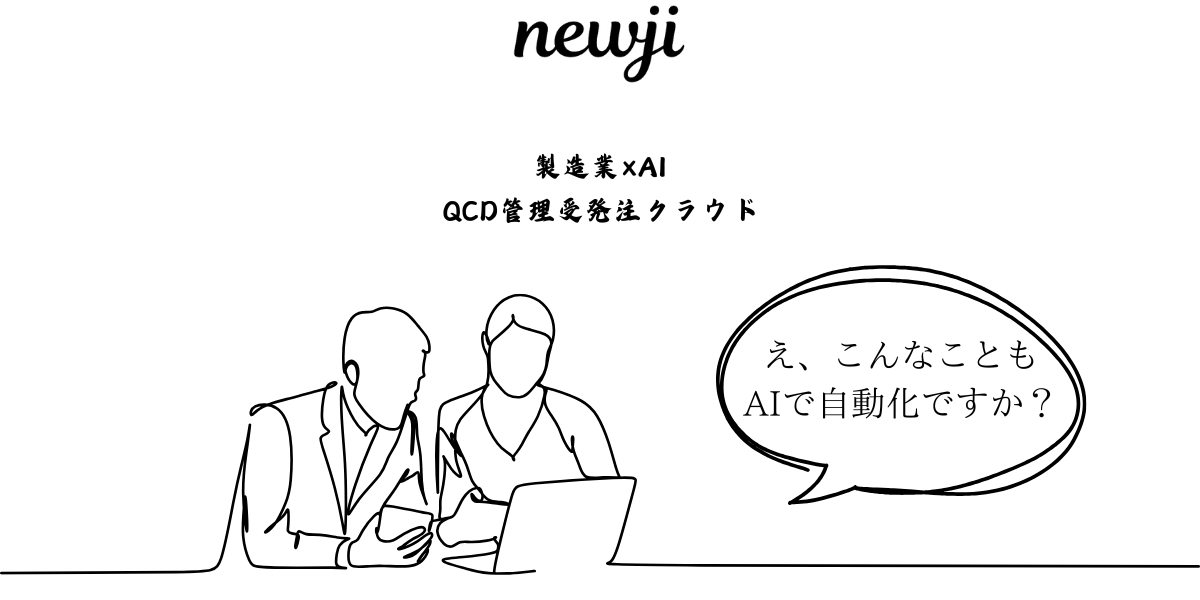
Improving production efficiency by shortening parts lead time Benefits of coordination between purchasing and production
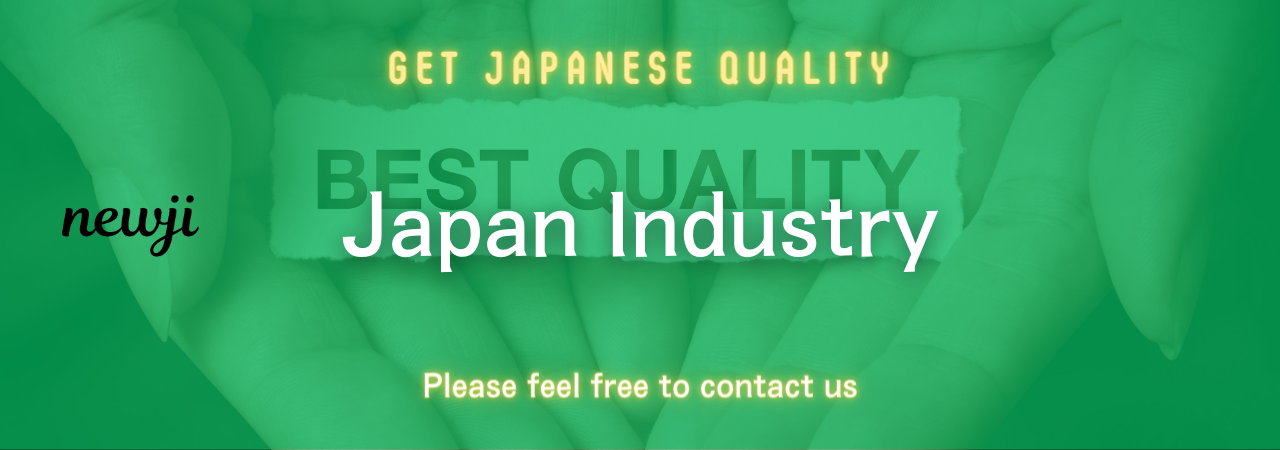
目次
Understanding Parts Lead Time and Its Impact on Production
In the manufacturing industry, efficiency is key to staying competitive and meeting customer demands.
One crucial factor that influences efficiency is the lead time associated with acquiring parts.
Lead time refers to the duration between placing an order for parts and receiving them for production.
Lengthy lead times can lead to bottlenecks in production, causing delays and potential revenue losses.
By reducing parts lead time, manufacturers can significantly improve production efficiency and overall company performance.
The Role of Purchasing and Production Coordination
Coordination between purchasing and production teams is essential in shortening parts lead time.
Purchasing teams are responsible for sourcing the necessary materials and components, while production teams need these parts to keep the manufacturing process running smoothly.
When these two teams work cohesively, the overall lead time can be minimized, and the manufacturing process becomes more streamlined.
Effective communication and collaboration between these departments ensure that orders are placed in a timely manner, inventories are managed efficiently, and any discrepancies are quickly addressed.
By establishing a clear line of communication, potential issues can be anticipated and resolved before they impact the production schedule.
Benefits of Shortened Parts Lead Time
Reducing the lead time for parts offers several advantages for manufacturing companies.
These benefits not only enhance efficiency but also contribute positively to the company’s bottom line.
Improved Production Scheduling
With a shorter lead time, production schedules can be planned more accurately.
This allows manufacturing plants to operate at optimal capacity without the constant threat of delays.
When parts arrive on time, assembly lines can function without interruptions, leading to increased productivity and reduced idle time for workers and machinery.
Reduced Inventory Costs
Shorter lead times mean that companies do not need to maintain large inventories of parts and materials.
This reduction in inventory levels results in decreased holding costs, freeing up valuable financial resources for other operational needs.
Furthermore, reducing inventory minimizes the risk of obsolescence, ensuring that the materials used in production are up-to-date and relevant to current manufacturing processes.
Enhanced Flexibility and Responsiveness
A reduced lead time enhances a company’s ability to respond quickly to changing customer demands and market trends.
Manufacturers can adapt their production based on immediate demand rather than forecasting far into the future.
This flexibility allows companies to seize new opportunities faster and provide customers with timely product deliveries, enhancing customer satisfaction and loyalty.
Strategies for Shortening Parts Lead Time
Several strategies can be employed to reduce parts lead time effectively.
These strategies involve the collaboration of purchasing and production teams to streamline processes and improve overall efficiency.
Supplier Relationship Management
Forging strong relationships with suppliers is fundamental in ensuring timely delivery of parts.
Regular communication and a clear understanding of each other’s needs and capabilities help build trust and reliability.
Engaging in long-term contracts with suppliers can also secure priority status and better terms for the company, reducing uncertainty and delays.
Implementing Just-In-Time (JIT) Inventory
The Just-In-Time inventory approach involves receiving parts and materials just when they are needed in the production process.
This strategy minimizes storage costs and decreases lead times by aligning orders closely with production schedules.
Implementing JIT requires precise planning and strong coordination between suppliers and the internal teams to avoid any disruptions.
Automation and Digitalization
Leveraging technology to automate order processing and inventory management can drastically reduce lead times.
Digital platforms can provide real-time data on stock levels, supplier performance, and logistics, allowing for swift decision-making.
Automation eliminates manual errors and speeds up the entire supply chain process, providing manufacturers with additional time for production activities.
The Long-Term Impact of Efficient Purchasing and Production Coordination
The benefits of effective coordination between purchasing and production extend beyond immediate improvements in lead time and production efficiency.
In the long term, companies that optimize these processes can achieve sustained growth and a competitive edge in the marketplace.
Strengthening Market Position
By consistently delivering products on time and meeting customer expectations, companies enhance their reputation and differentiate themselves from competitors.
A strong market position is crucial for attracting new customers and retaining existing ones, thereby driving business growth.
Innovation and Continuous Improvement
With efficient operations, companies have the bandwidth to focus on innovation and continuous improvement initiatives.
Resources saved from reducing lead times and inventory costs can be reallocated to R&D and process improvements, fostering a culture of innovation that keeps the company ahead of the curve.
Sustainability and Resource Management
Optimized coordination reduces waste and promotes sustainable practices within manufacturing processes.
By managing resources more effectively, companies contribute to environmental preservation while benefiting from cost savings and improved operational efficiency.
In conclusion, by understanding the importance of parts lead time and fostering collaboration between purchasing and production teams, manufacturers can enjoy significant advances in efficiency and productivity.
Such improvements not only bolster immediate performance but also lay the foundation for sustained success and growth in the dynamic manufacturing landscape.
資料ダウンロード
QCD調達購買管理クラウド「newji」は、調達購買部門で必要なQCD管理全てを備えた、現場特化型兼クラウド型の今世紀最高の購買管理システムとなります。
ユーザー登録
調達購買業務の効率化だけでなく、システムを導入することで、コスト削減や製品・資材のステータス可視化のほか、属人化していた購買情報の共有化による内部不正防止や統制にも役立ちます。
NEWJI DX
製造業に特化したデジタルトランスフォーメーション(DX)の実現を目指す請負開発型のコンサルティングサービスです。AI、iPaaS、および先端の技術を駆使して、製造プロセスの効率化、業務効率化、チームワーク強化、コスト削減、品質向上を実現します。このサービスは、製造業の課題を深く理解し、それに対する最適なデジタルソリューションを提供することで、企業が持続的な成長とイノベーションを達成できるようサポートします。
オンライン講座
製造業、主に購買・調達部門にお勤めの方々に向けた情報を配信しております。
新任の方やベテランの方、管理職を対象とした幅広いコンテンツをご用意しております。
お問い合わせ
コストダウンが利益に直結する術だと理解していても、なかなか前に進めることができない状況。そんな時は、newjiのコストダウン自動化機能で大きく利益貢献しよう!
(Β版非公開)