- お役立ち記事
- Improving Productivity by Reviewing Worker Movement Lines: Tips for On-Site Improvement
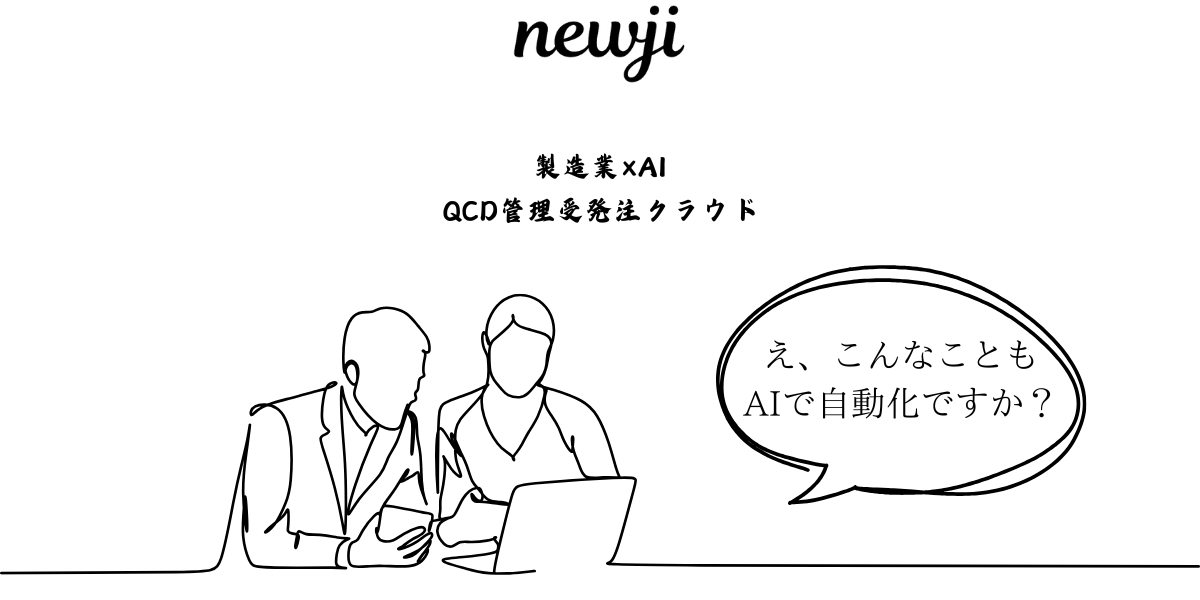
Improving Productivity by Reviewing Worker Movement Lines: Tips for On-Site Improvement
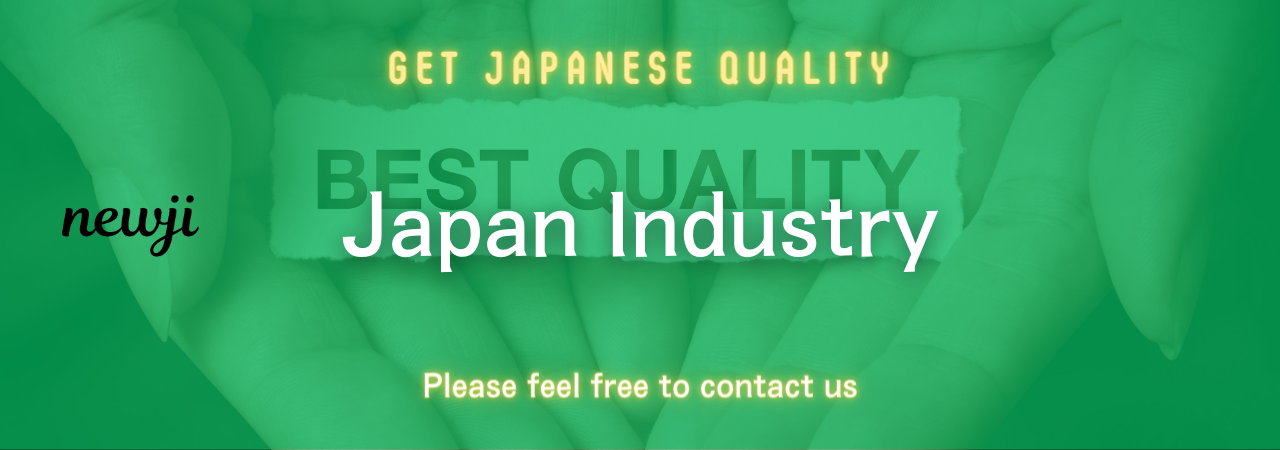
目次
Understanding Worker Movement Lines
Worker movement lines, also known as workflows, are the paths that employees follow as they carry out their tasks.
These paths often impact productivity and efficiency in significant ways.
Understanding them is the first step towards improving on-site operations.
Companies that meticulously analyze and adjust these lines can often see dramatic improvements in overall productivity.
The Importance of Efficient Worker Movement
When worker movement lines are optimized, employees can complete tasks faster and more accurately.
This is because they spend less time traveling between workstations and more time performing their duties.
Inefficient movement lines can lead to wasted time, increased fatigue, and lowered morale, all of which can significantly hamper productivity.
Boosted Efficiency
One of the most significant benefits of optimizing worker movement lines is increased efficiency.
When employees know exactly where they need to go and the most direct route to get there, it reduces unnecessary steps and time wasted.
This allows tasks and projects to be completed more quickly and accurately.
Reduction in Fatigue
Workers who follow optimized movement lines exert less physical effort, leading to reduced fatigue.
This can be particularly important in industries that involve significant physical labor.
Workers who are less tired are generally more productive and less prone to making errors, contributing to the overall efficiency of the operation.
Common Issues with Worker Movement Lines
Before you can improve worker movement lines, it’s crucial to identify common issues that can detract from productivity.
Some of these issues include:
Obstructions
Physical obstacles can disrupt the flow, forcing workers to take detours.
This can add unnecessary steps and time to every task, which adds up over the course of a day.
Poor Layout
A layout that is not conducive to the task at hand can significantly hamper productivity.
For example, placing commonly used tools or materials far from the work area means workers have to travel long distances frequently.
Frequent Interruptions
Interruptions can be a significant detriment to efficient movement.
This can include other workers crossing paths, machinery in the way, or even environmental factors like poor lighting or uneven flooring.
Steps to Improve Worker Movement Lines
Improving worker movement lines involves several steps.
Here are some actionable tips to help you get started.
Analyze Current Movement Patterns
The first step is to understand current movement patterns.
This can be done through direct observation, video recording, or even employee feedback.
Understanding where the bottlenecks and inefficiencies lie is crucial for making informed changes.
Use Technology
Employ tools such as workflow software or wearable devices to track and analyze movement patterns.
These technologies can provide valuable data that helps pinpoint exactly where changes need to be made.
Rearrange the Workspace
Based on your observations and data, rearrange the workspace to minimize travel distances.
Place commonly used tools and materials within easy reach of the workers who need them.
This simple change can drastically reduce wasted time.
Clear Obstructions
Ensure that pathways are free of obstacles.
This can involve rearranging equipment or even structural changes, like widening narrow corridors.
A clear path enables faster and more efficient movement.
Standardize Procedures
Create standardized procedures that all workers can follow.
This ensures everyone uses the most efficient routes and methods, reducing variability and increasing consistency.
Encouraging Employee Feedback
Perhaps one of the most important aspects of optimizing worker movement lines is encouraging employee feedback.
Your workers are the ones navigating these paths every day, so they often have valuable insights that can lead to meaningful improvements.
Create Open Communication Channels
Establish open lines of communication where workers feel comfortable sharing their observations and suggestions.
This can be through regular meetings, anonymous suggestion boxes, or digital platforms.
Implement Trial Runs
Before making permanent changes, conduct trial runs of new movement lines and procedures.
This allows you to assess their effectiveness and gather feedback from workers on what’s working and what’s not.
Case Studies on Improved Worker Movement
Many companies have successfully improved productivity by reviewing and optimizing worker movement lines.
Let’s take a look at a couple of case studies.
Case Study: Manufacturing Plant
A large manufacturing plant noticed a significant amount of time was being wasted as workers moved between different sections of the facility.
By using video analysis, they identified that tool and material placement was the main issue.
After rearranging the layout to place essential items closer to their point of use, the plant saw a 15% increase in overall productivity.
Case Study: Warehouse Facility
A warehouse facility suffering from frequent delays and errors implemented wearable tracking devices for their workers to study movement patterns.
This data revealed that poor pathway designs and obstructions were major productivity killers.
By redesigning the layout and ensuring clear paths, the warehouse reduced errors by 20% and improved efficiency by 30%.
The Long-Term Benefits of Optimized Worker Movement Lines
Investing time and resources into optimizing worker movement lines yields long-term benefits that go beyond immediate productivity gains.
Employee Morale and Job Satisfaction
Workers who operate in optimized environments are generally less stressed and more satisfied with their jobs.
This can lead to higher retention rates and a more motivated workforce.
Cost Savings
Increased efficiency and reduced errors translate directly into cost savings.
Less time and fewer resources are wasted, improving the bottom line.
Scalability
An optimized workflow can handle increased workloads more effectively, making it easier to scale operations as needed.
By paying close attention to worker movement lines and making the necessary improvements, companies can achieve remarkable gains in productivity, employee satisfaction, and cost efficiency.
資料ダウンロード
QCD調達購買管理クラウド「newji」は、調達購買部門で必要なQCD管理全てを備えた、現場特化型兼クラウド型の今世紀最高の購買管理システムとなります。
ユーザー登録
調達購買業務の効率化だけでなく、システムを導入することで、コスト削減や製品・資材のステータス可視化のほか、属人化していた購買情報の共有化による内部不正防止や統制にも役立ちます。
NEWJI DX
製造業に特化したデジタルトランスフォーメーション(DX)の実現を目指す請負開発型のコンサルティングサービスです。AI、iPaaS、および先端の技術を駆使して、製造プロセスの効率化、業務効率化、チームワーク強化、コスト削減、品質向上を実現します。このサービスは、製造業の課題を深く理解し、それに対する最適なデジタルソリューションを提供することで、企業が持続的な成長とイノベーションを達成できるようサポートします。
オンライン講座
製造業、主に購買・調達部門にお勤めの方々に向けた情報を配信しております。
新任の方やベテランの方、管理職を対象とした幅広いコンテンツをご用意しております。
お問い合わせ
コストダウンが利益に直結する術だと理解していても、なかなか前に進めることができない状況。そんな時は、newjiのコストダウン自動化機能で大きく利益貢献しよう!
(Β版非公開)