- お役立ち記事
- Improving Productivity by Selecting the Right Measuring Equipment
月間76,176名の
製造業ご担当者様が閲覧しています*
*2025年3月31日現在のGoogle Analyticsのデータより
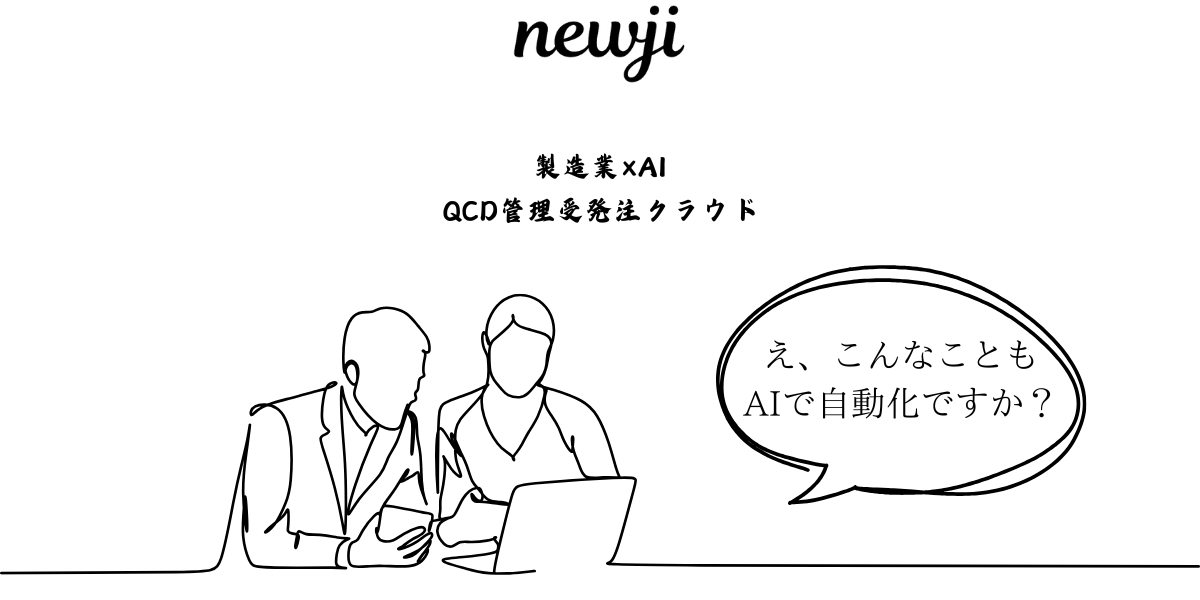
Improving Productivity by Selecting the Right Measuring Equipment
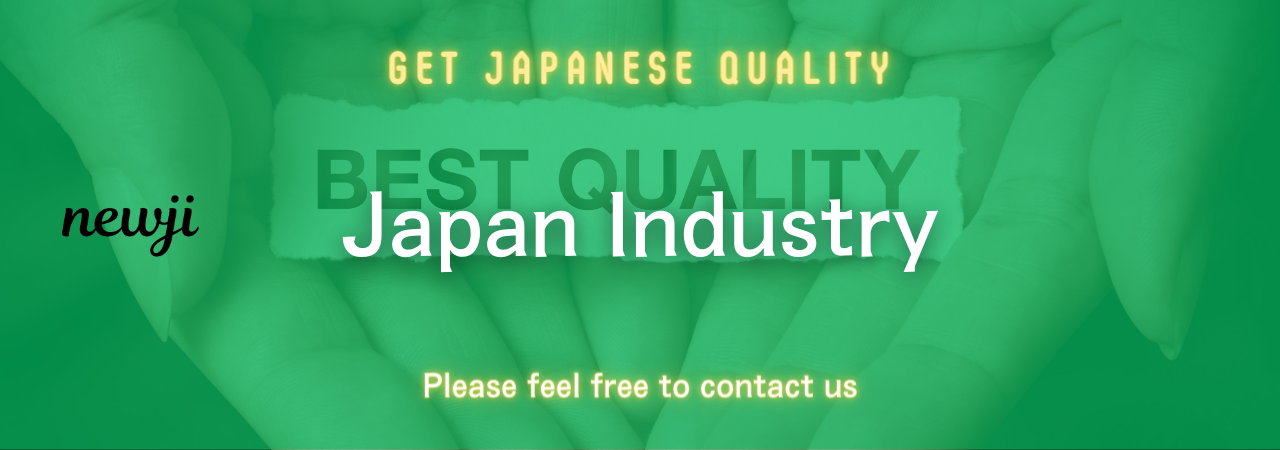
Choosing the right measuring equipment can dramatically improve workplace productivity.
Whether you’re in manufacturing, construction, or any other industry, having the right tools can save time, reduce errors, and enhance the quality of work.
This article will guide you through the process of selecting the best measuring equipment for your needs.
目次
Understanding the Importance of Measuring Equipment
Measuring equipment plays a crucial role in various industries.
Accurate measurements ensure that products meet quality standards and specifications.
They also play a key role in maintaining safety and compliance with regulations.
By using the correct measuring equipment, businesses can avoid costly mistakes, reduce waste, and enhance overall efficiency.
Common Types of Measuring Equipment
There are several types of measuring equipment, each designed for specific tasks.
Some common categories include:
– **Dimensional Measuring Tools:** These tools, such as calipers and micrometers, measure the dimensions of objects.
– **Weight Measuring Devices:** Scales and balances fall into this category and provide weight measurements.
– **Temperature Gauges:** Instruments like thermometers and infrared cameras measure temperature.
– **Pressure Measuring Devices:** Pressure gauges and manometers measure the pressure of gases or liquids.
Understanding the purpose and function of each type of measuring equipment is the first step in choosing the right tools for your needs.
Factors to Consider When Selecting Measuring Equipment
When choosing measuring equipment, several factors should be considered to ensure you make the best choice for your specific application.
Accuracy and Precision
Accuracy refers to how close a measurement is to the true value, while precision indicates how repeatable the measurement is.
Both factors are crucial for maintaining high-quality standards.
Select equipment that offers the required level of accuracy and precision for your tasks.
Range and Resolution
The range is the span within which the tool can take measurements, and the resolution is the smallest increment the device can detect.
Choose equipment with a range and resolution that cater to your specific needs.
For instance, if you are measuring small objects, a tool with high resolution and a smaller range would be more appropriate.
Durability and Reliability
Work environments can vary significantly, and some may be harsh on equipment.
Choose measuring tools that are durable and reliable under your working conditions.
Consider factors such as build quality, material, and resistance to environmental factors like dust and moisture.
Ease of Use
Equipment that is easy to use can speed up processes and reduce the likelihood of measurement errors.
Consider whether the device has a user-friendly interface, clear display, and ergonomic design.
Training staff to use the equipment effectively is also essential.
Calibration and Maintenance
Regular calibration is vital for maintaining the accuracy of measuring equipment.
Choose tools that are easy to calibrate and maintain.
Verify if the manufacturer provides calibration services or if you need to perform it in-house.
Cost and Return on Investment (ROI)
While cost is a significant factor, it shouldn’t be the only consideration.
Investing in high-quality measuring equipment can lead to long-term savings by reducing errors and rework.
Evaluate the potential return on investment when selecting equipment.
Steps for Choosing the Right Measuring Equipment
Follow these steps to ensure you select the best measuring tools for your needs.
Identify Your Requirements
Start by clearly defining what you need to measure.
Consider the specifications, tolerances, and standards needed for your application.
Knowing your requirements will narrow down your options.
Research Equipment Options
Conduct thorough research to compare different types of measuring equipment.
Look into industry recommendations, reviews, and case studies.
Consult with manufacturers and suppliers to understand the features and benefits of various tools.
Test the Equipment
Whenever possible, test the equipment before purchasing.
Many suppliers offer demo units or trial periods.
Testing helps you ensure that the tool meets your accuracy, usability, and durability requirements.
Consider User Feedback
Gather feedback from potential users within your organization.
Their insights can be invaluable in evaluating the ease of use, functionality, and practicality of the equipment.
Evaluate Support Services
Consider the level of support provided by the manufacturer or supplier.
This includes warranty, customer service, and availability of spare parts.
Reliable support can significantly affect the lifespan and performance of your measuring equipment.
Conclusion
Selecting the right measuring equipment is a critical decision that can greatly enhance productivity and efficiency in the workplace.
By considering factors such as accuracy, precision, durability, and ease of use, you can choose tools that meet your specific needs.
Investing in high-quality measuring equipment can lead to long-term savings and improved product quality, making it a worthwhile investment for any industry.
資料ダウンロード
QCD管理受発注クラウド「newji」は、受発注部門で必要なQCD管理全てを備えた、現場特化型兼クラウド型の今世紀最高の受発注管理システムとなります。
ユーザー登録
受発注業務の効率化だけでなく、システムを導入することで、コスト削減や製品・資材のステータス可視化のほか、属人化していた受発注情報の共有化による内部不正防止や統制にも役立ちます。
NEWJI DX
製造業に特化したデジタルトランスフォーメーション(DX)の実現を目指す請負開発型のコンサルティングサービスです。AI、iPaaS、および先端の技術を駆使して、製造プロセスの効率化、業務効率化、チームワーク強化、コスト削減、品質向上を実現します。このサービスは、製造業の課題を深く理解し、それに対する最適なデジタルソリューションを提供することで、企業が持続的な成長とイノベーションを達成できるようサポートします。
製造業ニュース解説
製造業、主に購買・調達部門にお勤めの方々に向けた情報を配信しております。
新任の方やベテランの方、管理職を対象とした幅広いコンテンツをご用意しております。
お問い合わせ
コストダウンが利益に直結する術だと理解していても、なかなか前に進めることができない状況。そんな時は、newjiのコストダウン自動化機能で大きく利益貢献しよう!
(β版非公開)