- お役立ち記事
- Improving productivity using electricity: Examples of energy efficiency in the manufacturing industry
月間77,185名の
製造業ご担当者様が閲覧しています*
*2025年2月28日現在のGoogle Analyticsのデータより
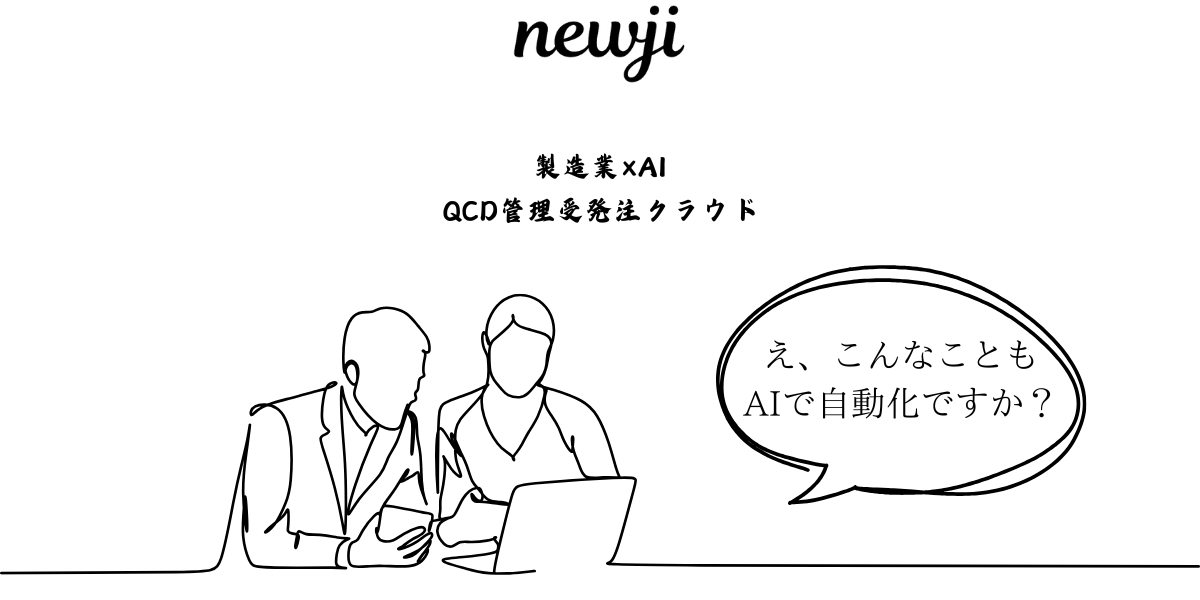
Improving productivity using electricity: Examples of energy efficiency in the manufacturing industry
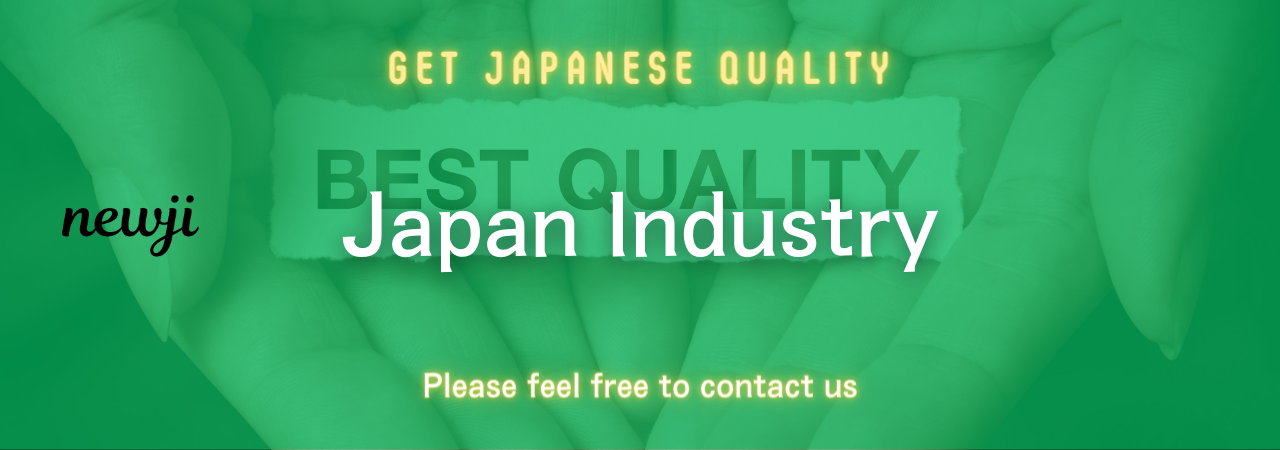
目次
The Importance of Energy Efficiency in Manufacturing
Energy efficiency is a critical aspect of modern manufacturing.
With the increasing demand for goods and the pressure to reduce carbon footprints, manufacturers are looking for ways to improve productivity while minimizing energy consumption.
Electricity is a significant part of the manufacturing process, powering machinery, lighting, heating, cooling, and other essential functions.
By focusing on energy efficiency, manufacturers can reduce costs, enhance sustainability, and improve overall operational efficiency.
Understanding Energy Efficiency
Energy efficiency in manufacturing means using less energy to produce the same amount of products or services.
It involves adopting technologies and practices that reduce energy waste and optimize the use of resources.
This not only cuts energy bills but also enhances competitiveness by lowering production costs.
Moreover, energy efficiency contributes to environmental conservation by reducing greenhouse gas emissions and reliance on non-renewable energy sources.
Benefits of Energy Efficiency
1. **Cost Savings**: Reducing energy consumption directly translates to lower energy bills, which can significantly impact the bottom line.
2. **Environmental Impact**: By using energy more efficiently, manufacturers can reduce their carbon footprint and contribute to mitigating climate change.
3. **Enhanced Competitiveness**: Companies that manage energy resources effectively can offer products at lower prices or improved quality, giving them a competitive edge.
4. **Regulatory Compliance**: Energy efficiency initiatives help companies comply with environmental regulations and standards, avoiding potential fines and sanctions.
5. **Sustainability Goals**: Demonstrating a commitment to energy efficiency aligns with broader corporate sustainability goals, appealing to environmentally conscious consumers and investors.
Examples of Energy Efficiency in the Manufacturing Industry
Many manufacturers are already employing innovative strategies to enhance energy efficiency.
Here are a few examples that showcase how the manufacturing industry can improve productivity using electricity:
Retrofit Projects
Retrofitting existing equipment is one way manufacturers improve energy efficiency.
By upgrading older machines with more energy-efficient components, manufacturers can significantly reduce electricity consumption.
For example, replacing traditional lighting with LED bulbs or installing variable speed drives in motors can save significant amounts of electricity.
Energy Management Systems (EMS)
An Energy Management System (EMS) helps manufacturers monitor and control energy use throughout their facilities.
These systems provide real-time data on energy consumption, allowing companies to identify and address inefficiencies promptly.
The insights gained from an EMS can inform strategic decisions that optimize energy use and reduce waste.
Process Optimization
Manufacturers can improve energy efficiency by optimizing production processes.
This can involve rearranging production lines to reduce wasted motion or minimizing idle times of machines.
For example, adopting just-in-time (JIT) production models can help synchronize operations, thereby reducing unnecessary energy expenditure.
Heat Recovery Systems
Manufacturing processes often generate excess heat, which can be repurposed using heat recovery systems.
These systems capture waste heat and reuse it in other processes, such as heating water or spaces, thereby reducing the need for additional energy input.
This not only lowers energy consumption but also improves overall process efficiency.
Adopting Renewable Energy Sources
Incorporating renewable energy sources, such as solar or wind power, into manufacturing operations can significantly reduce reliance on conventional electricity from the grid.
While the initial investment may be substantial, the long-term savings and environmental benefits make it a worthwhile option for many manufacturers.
Technological Advancements Aiding Energy Efficiency
Advancements in technology continually open new opportunities for energy efficiency in manufacturing.
The integration of artificial intelligence (AI) and the Internet of Things (IoT) in manufacturing can dramatically improve energy utilization.
Smart Manufacturing
Smart manufacturing leverages connected devices and sensors to monitor and manage energy use across production facilities.
These technologies enable real-time adjustments and predictive maintenance, ensuring that equipment operates at its peak efficiency.
Automation
Though automation involves energy use, it optimizes overall efficiency when implemented correctly.
By automating repetitive, energy-intensive tasks, manufacturers can reduce energy waste and improve productivity.
Advanced Materials
Innovations in advanced materials can contribute to energy savings.
For example, lightweight materials require less energy to transport, and thermally resistant materials can improve insulation and reduce heating or cooling demands.
Steps to Implement Energy Efficiency Measures
For manufacturers looking to improve energy efficiency, a strategic approach is essential.
Here are steps to facilitate this transition:
1. **Conduct an Energy Audit**: Understanding where and how energy is used within a facility is crucial. An energy audit identifies opportunities for improvement and sets a baseline for measuring progress.
2. **Set Clear Goals**: Establish measurable and achievable energy efficiency targets. These goals provide direction and motivation for the entire organization.
3. **Engage Employees**: Foster a culture of energy efficiency by involving staff in the process. Training and awareness campaigns can motivate employees to adopt energy-saving practices.
4. **Invest in Technology**: Adopt energy-efficient technologies and upgrade existing systems where feasible. The right technologies can yield substantial energy savings over time.
5. **Monitor and Adjust**: Continuously monitor energy consumption and process efficiency. Use insights to refine strategies and make informed adjustments.
In conclusion, energy efficiency is a crucial element of sustainable manufacturing.
By implementing these strategies and focusing on continuous improvement, manufacturers can enhance productivity, reduce costs, and contribute positively to environmental sustainability.
These efforts not only lead to economic advantages but also demonstrate a commitment to responsible industry practices that benefit society as a whole.
資料ダウンロード
QCD管理受発注クラウド「newji」は、受発注部門で必要なQCD管理全てを備えた、現場特化型兼クラウド型の今世紀最高の受発注管理システムとなります。
ユーザー登録
受発注業務の効率化だけでなく、システムを導入することで、コスト削減や製品・資材のステータス可視化のほか、属人化していた受発注情報の共有化による内部不正防止や統制にも役立ちます。
NEWJI DX
製造業に特化したデジタルトランスフォーメーション(DX)の実現を目指す請負開発型のコンサルティングサービスです。AI、iPaaS、および先端の技術を駆使して、製造プロセスの効率化、業務効率化、チームワーク強化、コスト削減、品質向上を実現します。このサービスは、製造業の課題を深く理解し、それに対する最適なデジタルソリューションを提供することで、企業が持続的な成長とイノベーションを達成できるようサポートします。
製造業ニュース解説
製造業、主に購買・調達部門にお勤めの方々に向けた情報を配信しております。
新任の方やベテランの方、管理職を対象とした幅広いコンテンツをご用意しております。
お問い合わせ
コストダウンが利益に直結する術だと理解していても、なかなか前に進めることができない状況。そんな時は、newjiのコストダウン自動化機能で大きく利益貢献しよう!
(β版非公開)