- お役立ち記事
- Improving Quality in Manufacturing Using QFD: Success Stories and Practical Guide
Improving Quality in Manufacturing Using QFD: Success Stories and Practical Guide
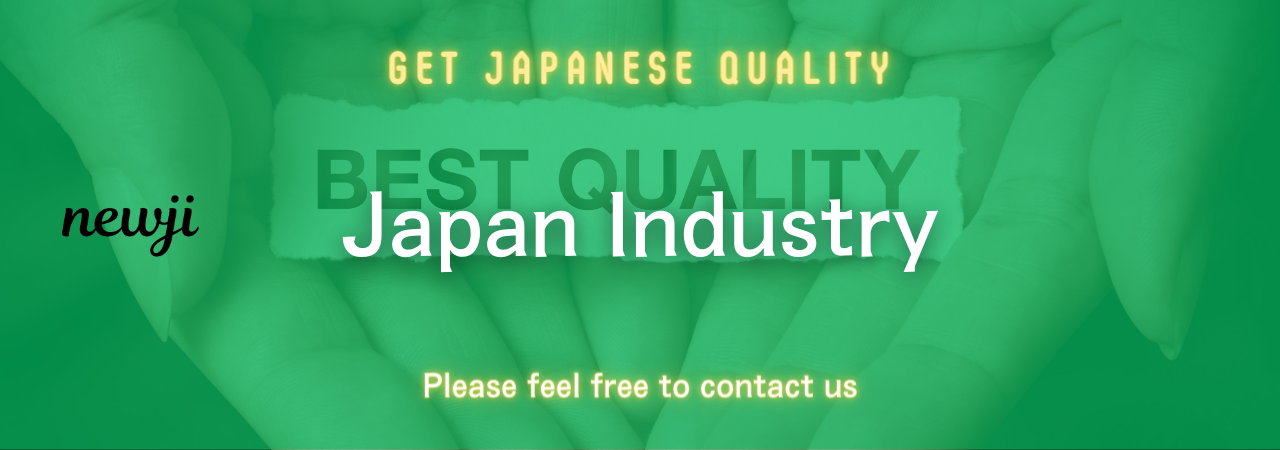
目次
Introduction
Quality Function Deployment (QFD) is a methodology that can significantly enhance the quality of manufacturing processes.
By incorporating customer needs and translating them into specific technical requirements, QFD helps in creating products that meet or exceed customer expectations.
In this article, we will explore some success stories and provide a practical guide to improving quality in manufacturing using QFD.
What is QFD?
The Basic Concept
Quality Function Deployment, commonly known as QFD, is a structured method used to identify and prioritize customer requirements.
It helps in translating these requirements into technical specifications that engineers and designers can use to develop products.
Originally developed in Japan during the 1960s, QFD has become an essential tool for quality improvement in various industries.
The House of Quality
One of the most popular tools in QFD is the House of Quality.
This is a matrix that helps in visualizing the relationship between customer requirements and technical features.
By using the House of Quality, teams can better understand what is most important to customers and how to achieve those needs through specific technical solutions.
Success Stories in QFD
Automotive Industry: Toyota’s Experience
Toyota is one of the early adopters of QFD, using it to great effect in their manufacturing processes.
By implementing QFD, Toyota was able to identify crucial customer requirements, such as safety, fuel efficiency, and reliability.
These insights helped the company design vehicles that are not only high in quality but also well-aligned with customer expectations.
As a result, Toyota gained a substantial competitive advantage in the automotive market.
Consumer Electronics: Panasonic
Panasonic used QFD to improve the quality of their products by focusing on customer feedback.
They collected detailed information about what customers liked and disliked about their products.
Through QFD, they were able to translate this feedback into actionable technical features.
This led to significant improvements in product quality and customer satisfaction.
Healthcare: Improving Medical Devices
In the healthcare industry, QFD has been used to enhance the quality of medical devices.
One notable example is the development of a specialized diagnostic machine.
By incorporating QFD, the manufacturing team was able to prioritize features that were most important to healthcare professionals, leading to a highly effective and reliable medical device.
This not only improved patient outcomes but also boosted the credibility and market reach of the product.
Practical Guide to Implementing QFD in Manufacturing
Step 1: Identify Customer Needs
The first step in implementing QFD is to identify the needs and preferences of your customers.
This can be done through surveys, focus groups, and direct customer feedback.
Understanding what your customers want is crucial for the success of the QFD process.
Step 2: Develop a House of Quality
Once you have identified customer needs, the next step is to develop a House of Quality.
This involves creating a matrix that maps customer requirements to specific technical features.
The House of Quality helps in visualizing the relationship between what customers want and how you can deliver it through technical solutions.
Step 3: Prioritize Technical Requirements
After developing the House of Quality, the next step is to prioritize the technical requirements.
Not all features will be equally important, so it’s crucial to focus on those that will have the most significant impact on customer satisfaction.
Prioritization helps in making efficient use of resources and ensuring that the most critical features are implemented first.
Step 4: Develop an Action Plan
With prioritized technical requirements in hand, the next step is to develop an action plan.
This plan should outline the steps needed to implement the technical features, along with timelines and resource allocations.
An actionable plan ensures that the project stays on track and meets the set deadlines.
Step 5: Implement and Monitor
The final step is to implement the action plan and monitor the results.
This involves executing the plan, checking the quality of the output, and making necessary adjustments.
Continuous monitoring helps in identifying any issues early on and ensures that the final product meets the desired quality standards.
Benefits of Using QFD
Improved Customer Satisfaction
One of the most significant benefits of using QFD is improved customer satisfaction.
By focusing on what customers actually want, you can create products that are more likely to meet or exceed their expectations.
This leads to higher customer loyalty and better market performance.
Enhanced Product Quality
QFD helps in identifying and prioritizing the most critical technical features, leading to improved product quality.
By translating customer needs into actionable technical requirements, you can ensure that your products are built to high standards.
Efficient Use of Resources
By prioritizing technical requirements and focusing on what’s most important, QFD helps in making efficient use of resources.
This ensures that time, money, and manpower are used effectively, leading to better project outcomes.
Challenges in Implementing QFD
Resistance to Change
One of the main challenges in implementing QFD is resistance to change.
Teams may be hesitant to adopt a new methodology, especially if they are accustomed to traditional approaches.
Overcoming this resistance requires effective communication and training.
Complexity of the Process
QFD can be a complex process, requiring detailed analysis and planning.
This complexity can be daunting, especially for teams that are new to the methodology.
However, with proper training and practice, the process becomes more manageable.
Resource Allocation
Implementing QFD requires a significant investment of time and resources.
Allocating these resources effectively can be a challenge, especially for smaller companies.
Careful planning and prioritization can help in managing resource allocation more efficiently.
Conclusion
Quality Function Deployment (QFD) is a powerful tool for improving manufacturing quality.
By focusing on customer needs and translating them into technical requirements, QFD helps in creating products that meet or exceed customer expectations.
While implementing QFD can be challenging, the benefits far outweigh the difficulties.
With practical steps and successful examples from industries like automotive, consumer electronics, and healthcare, it’s evident that QFD can make a significant difference in product quality and customer satisfaction.
資料ダウンロード
QCD調達購買管理クラウド「newji」は、調達購買部門で必要なQCD管理全てを備えた、現場特化型兼クラウド型の今世紀最高の購買管理システムとなります。
ユーザー登録
調達購買業務の効率化だけでなく、システムを導入することで、コスト削減や製品・資材のステータス可視化のほか、属人化していた購買情報の共有化による内部不正防止や統制にも役立ちます。
NEWJI DX
製造業に特化したデジタルトランスフォーメーション(DX)の実現を目指す請負開発型のコンサルティングサービスです。AI、iPaaS、および先端の技術を駆使して、製造プロセスの効率化、業務効率化、チームワーク強化、コスト削減、品質向上を実現します。このサービスは、製造業の課題を深く理解し、それに対する最適なデジタルソリューションを提供することで、企業が持続的な成長とイノベーションを達成できるようサポートします。
オンライン講座
製造業、主に購買・調達部門にお勤めの方々に向けた情報を配信しております。
新任の方やベテランの方、管理職を対象とした幅広いコンテンツをご用意しております。
お問い合わせ
コストダウンが利益に直結する術だと理解していても、なかなか前に進めることができない状況。そんな時は、newjiのコストダウン自動化機能で大きく利益貢献しよう!
(Β版非公開)