- お役立ち記事
- Improving Reliability in Manufacturing with ISO 9001 Certification
月間76,176名の
製造業ご担当者様が閲覧しています*
*2025年3月31日現在のGoogle Analyticsのデータより
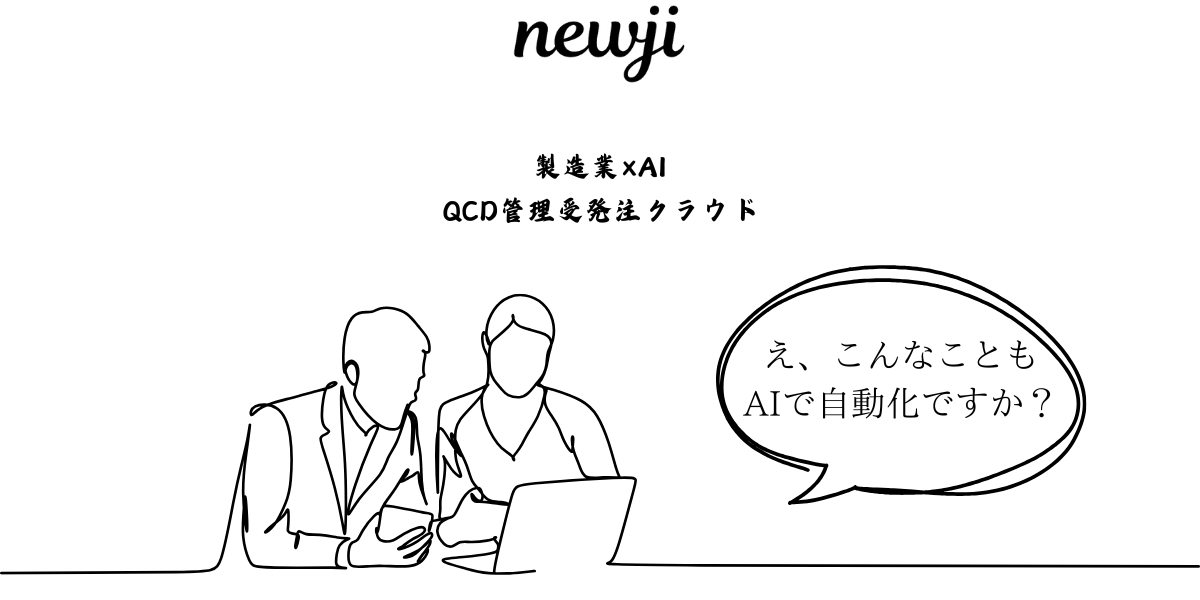
Improving Reliability in Manufacturing with ISO 9001 Certification
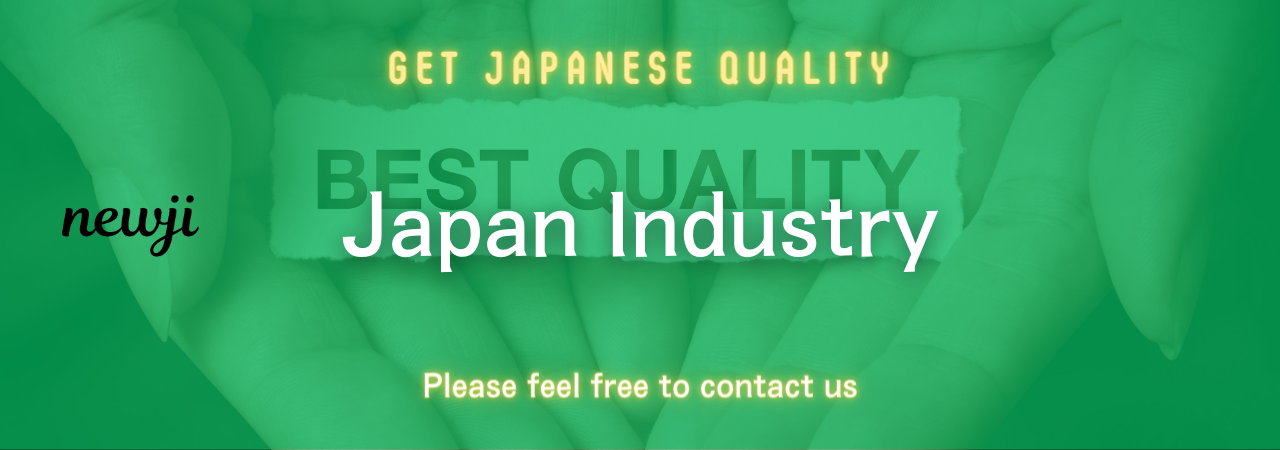
目次
Understanding ISO 9001 Certification and Its Importance
Manufacturing companies strive to deliver high-quality products to their customers.
One of the ways to demonstrate a commitment to quality is through obtaining ISO 9001 certification.
ISO 9001 is a globally recognized standard for a quality management system (QMS).
Being certified shows that a company has met specific requirements for ensuring quality and reliability in its processes.
ISO 9001 certification is not just a badge of honor.
It ensures that a manufacturing company has a well-structured approach to managing quality.
This includes having documented procedures, regular audits, and ongoing improvements.
Companies that achieve ISO 9001 certification are often viewed as more reliable and trustworthy by their customers.
Benefits of ISO 9001 Certification in Manufacturing
Enhanced Customer Satisfaction
One of the primary benefits of ISO 9001 certification is enhanced customer satisfaction.
When a manufacturing company follows ISO 9001 standards, it means they are committed to meeting customer requirements and enhancing satisfaction.
Customers will have more confidence in the products they receive, knowing that the company follows internationally recognized quality management principles.
Improved Operational Efficiency
ISO 9001 certification requires a company to thoroughly document its processes and procedures.
This leads to improved operational efficiency and reduced waste.
With well-documented processes, employees have clear guidelines to follow, which minimizes errors and rework.
Efficient operations translate to cost savings and faster turnaround times, making the company more competitive in the market.
Increased Market Opportunities
Many industries require suppliers to be ISO 9001 certified.
Having this certification opens up new market opportunities for manufacturing companies.
It allows them to participate in tenders and contracts that they might otherwise be excluded from.
Being ISO 9001 certified can be a significant advantage when trying to attract new customers or enter new markets.
Continuous Improvement
ISO 9001 emphasizes continuous improvement.
This means that certified companies must regularly review and improve their processes.
Continuous improvement leads to better products, services, and overall business performance.
By striving for ongoing enhancements, manufacturing companies can stay ahead of their competitors and adapt to changing market demands.
Steps to Achieve ISO 9001 Certification
Understand the Requirements
The first step towards achieving ISO 9001 certification is understanding the requirements of the standard.
The ISO 9001:2015 standard outlines the criteria for a quality management system.
Companies need to familiarize themselves with these requirements and assess how their current processes align with them.
Develop a Quality Management System (QMS)
Next, the company must develop a QMS that meets the ISO 9001 standards.
This involves documenting processes, procedures, and responsibilities.
The QMS should cover all aspects of the company’s operations, from product design and development to production and customer service.
Implement the QMS
Once the QMS is developed, it must be implemented across the organization.
This requires training employees on the new procedures and ensuring they understand their roles and responsibilities.
Implementing the QMS may involve changes to existing processes, so it’s essential to manage this transition effectively.
Conduct Internal Audits
Before seeking certification, the company should conduct internal audits to ensure that the QMS complies with ISO 9001 requirements.
Internal audits help identify any gaps or areas for improvement.
Addressing these issues before the external audit increases the chances of a successful certification process.
Choose a Certification Body
To become ISO 9001 certified, the company must choose an accredited certification body.
This is an independent organization that will conduct an external audit of the company’s QMS.
The certification body will assess whether the QMS meets ISO 9001 standards and, if successful, issue the certification.
Undergo the Certification Audit
The certification audit is a comprehensive review of the company’s QMS by the certification body.
The auditors will examine documentation, observe processes, and interview employees to ensure compliance with ISO 9001 standards.
If the company passes the audit, it will be awarded ISO 9001 certification.
Maintaining ISO 9001 Certification
Regular Surveillance Audits
ISO 9001 certification is not a one-time achievement.
Certified companies must undergo regular surveillance audits to maintain their certification.
These audits ensure that the QMS continues to meet ISO 9001 standards and that the company is committed to continuous improvement.
Ongoing Improvement
Maintaining ISO 9001 certification requires a commitment to ongoing improvement.
Companies should actively seek ways to enhance their processes, reduce waste, and improve customer satisfaction.
This proactive approach will help them remain competitive and ensure they continue to meet ISO 9001 standards.
Employee Training and Engagement
Employee training and engagement are crucial for maintaining ISO 9001 certification.
Companies should invest in regular training programs to keep employees updated on quality management practices and their specific roles within the QMS.
Engaged and well-trained employees are more likely to follow procedures and contribute to continuous improvement efforts.
Documentation and Record-Keeping
Accurate documentation and record-keeping are essential for demonstrating compliance with ISO 9001 standards.
Companies must maintain records of their processes, audits, and improvements.
These records should be readily available for review during both internal and external audits.
Conclusion
Achieving ISO 9001 certification is a significant step for manufacturing companies aiming to improve reliability and quality.
It offers numerous benefits, including enhanced customer satisfaction, improved operational efficiency, increased market opportunities, and continuous improvement.
By following the necessary steps to develop, implement, and maintain a QMS, companies can achieve and sustain ISO 9001 certification.
This demonstrates a commitment to quality and sets them apart as trusted and reliable providers in their industry.
資料ダウンロード
QCD管理受発注クラウド「newji」は、受発注部門で必要なQCD管理全てを備えた、現場特化型兼クラウド型の今世紀最高の受発注管理システムとなります。
ユーザー登録
受発注業務の効率化だけでなく、システムを導入することで、コスト削減や製品・資材のステータス可視化のほか、属人化していた受発注情報の共有化による内部不正防止や統制にも役立ちます。
NEWJI DX
製造業に特化したデジタルトランスフォーメーション(DX)の実現を目指す請負開発型のコンサルティングサービスです。AI、iPaaS、および先端の技術を駆使して、製造プロセスの効率化、業務効率化、チームワーク強化、コスト削減、品質向上を実現します。このサービスは、製造業の課題を深く理解し、それに対する最適なデジタルソリューションを提供することで、企業が持続的な成長とイノベーションを達成できるようサポートします。
製造業ニュース解説
製造業、主に購買・調達部門にお勤めの方々に向けた情報を配信しております。
新任の方やベテランの方、管理職を対象とした幅広いコンテンツをご用意しております。
お問い合わせ
コストダウンが利益に直結する術だと理解していても、なかなか前に進めることができない状況。そんな時は、newjiのコストダウン自動化機能で大きく利益貢献しよう!
(β版非公開)