- お役立ち記事
- Improving skills by supporting acquisition of qualifications related to factory facilities
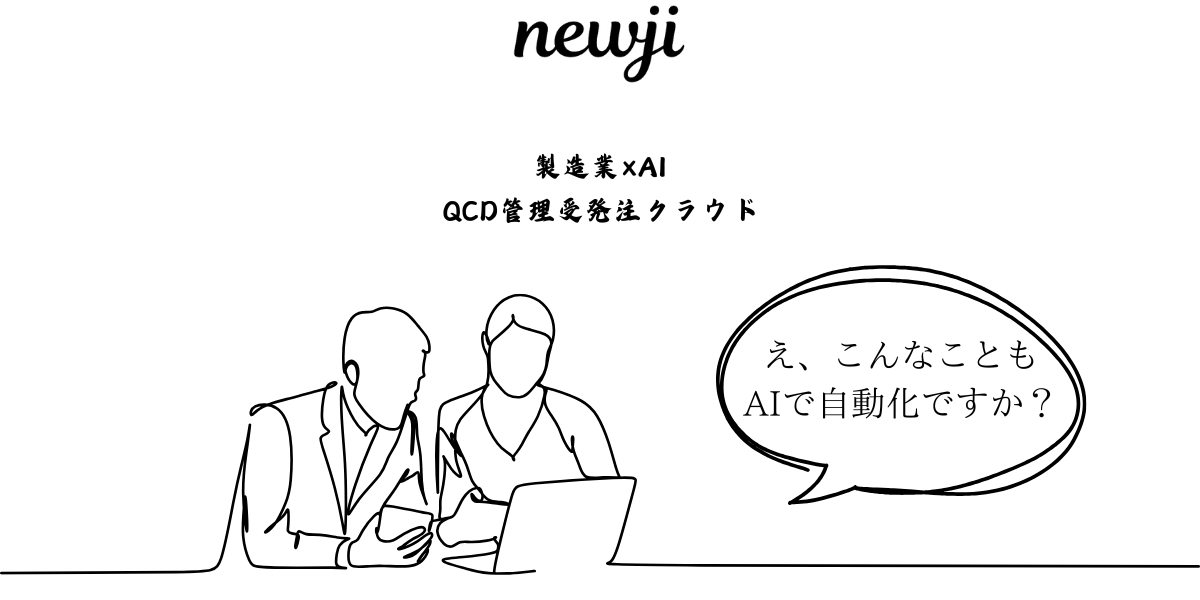
Improving skills by supporting acquisition of qualifications related to factory facilities
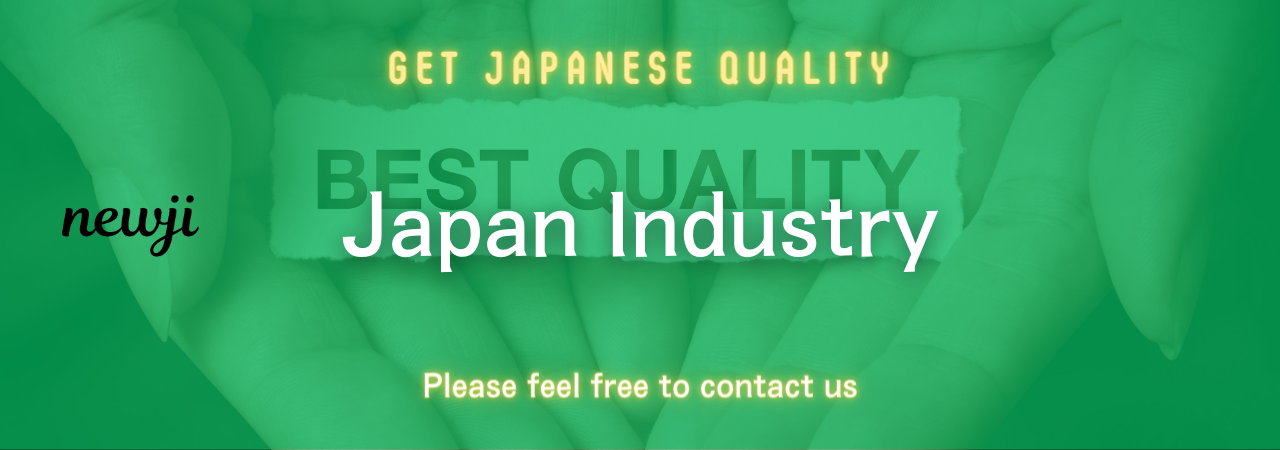
目次
Importance of Skill Improvement in Factory Facilities
In the fast-paced industrial world, continuous skill improvement is crucial.
Factories play a vital role in manufacturing and production, and ensuring that staff is equipped with the right skills is essential.
Acquiring qualifications related to factory facilities not only enhances personal growth but also boosts the overall efficiency of the facility.
Technological advancements are rapidly shaping factories.
Manufacturers are constantly updating their facilities with cutting-edge machinery and systems to remain competitive.
To effectively operate and maintain these advanced factory facilities, skilled personnel are indispensable.
Recognizing the Benefits of Qualification Acquisition
Supporting the acquisition of qualifications brings numerous benefits.
When employees enhance their skills, it leads to improved productivity.
Qualified workers can handle machinery and equipment efficiently, leading to reduced downtime and increased output.
Moreover, when employees pursue further qualification, it fosters a culture of learning and development within the workplace.
This nurtures a positive work environment where collaboration and innovation can thrive.
Employee qualifications contribute significantly to workplace safety as well.
Well-trained employees are more adept at recognizing potential hazards and applying safety protocols.
This reduces the risk of accidents and ensures the well-being of everyone in the facility.
Finding the Right Qualifications
Identifying the right qualifications for employees is pivotal in skill improvement.
It begins with understanding the specific goals and requirements of the factory.
Are there particular machines or processes that present challenges?
What skills are currently lacking within the team?
Answering these questions helps in targeting qualifications that align with the factory’s objectives.
Researching industry trends and consulting with experts can also provide valuable insights into relevant qualifications.
Additionally, collaborating with educational institutions and training centers can be beneficial.
These institutions often offer tailored programs to suit industry needs.
Choosing Accredited Programs
Accreditation is an important consideration when selecting a qualification program.
Accredited programs assure quality education and training, validated by industry standards.
This ensures that employees receive up-to-date knowledge and skills that are applicable in real-world factory settings.
Accredited programs also have the advantage of being recognized by employers and industry stakeholders.
This recognition can be valuable for both personal career advancement and the factory’s reputation.
Online vs. In-Person Training
When it comes to acquiring qualifications, there are options for both online and in-person training.
Online programs offer flexibility, allowing employees to learn at their own pace and on their own schedule.
This is particularly advantageous for factories operating round-the-clock shifts.
In-person training, on the other hand, provides hands-on experience and face-to-face interactions with instructors.
This can be beneficial for practical skills that require direct application.
Balancing both methods can provide a comprehensive learning experience.
Employees can leverage the theoretical understanding gained online with the practical skills attained through in-person training.
Implementing Qualification Support Initiatives
For factories to support skill acquisition effectively, implementing qualification support initiatives is essential.
Here are some strategies to consider:
Providing Financial Assistance
Financial barriers can often hinder employees from pursuing further qualifications.
Offering financial assistance, such as scholarships or reimbursement programs, can encourage more employees to participate.
This investment in human capital eventually leads to improved operational efficiency and higher employee retention rates.
Allocating Time for Training
Schedule flexibility is another crucial factor in supporting qualification acquisition.
Factories can allocate dedicated time for training and learning within employees’ work schedules.
This ensures that employees can pursue their qualifications without compromising their work responsibilities.
Mentorship and Support Networks
Developing mentorship programs and support networks can provide invaluable guidance and motivation for employees.
Pairing experienced staff with those pursuing new qualifications helps in knowledge transfer and practical application of new skills.
Mentors can provide advice, share their experiences, and support mentees in navigating their qualification journey.
Measuring the Impact of Qualification Acquisition
Assessing the impact of qualification acquisition initiatives is important to ensure effectiveness.
Factories can measure this impact through key performance indicators (KPIs).
KPIs such as productivity levels, error rates, and employee engagement can provide insights into the benefits realized from qualification support programs.
Feedback from employees participating in qualification programs is also valuable.
Regularly collecting and analyzing this feedback helps in understanding the training’s effectiveness and identifying areas for improvement.
Looking Toward the Future
As the manufacturing industry continues to evolve, the need for skill improvement and qualification acquisition will persist.
Staying ahead of industry trends and adopting innovative training solutions will be crucial.
By prioritizing skill enhancement and qualification support, factories can ensure not only the success of their operations but also the growth and satisfaction of their workforce.
資料ダウンロード
QCD調達購買管理クラウド「newji」は、調達購買部門で必要なQCD管理全てを備えた、現場特化型兼クラウド型の今世紀最高の購買管理システムとなります。
ユーザー登録
調達購買業務の効率化だけでなく、システムを導入することで、コスト削減や製品・資材のステータス可視化のほか、属人化していた購買情報の共有化による内部不正防止や統制にも役立ちます。
NEWJI DX
製造業に特化したデジタルトランスフォーメーション(DX)の実現を目指す請負開発型のコンサルティングサービスです。AI、iPaaS、および先端の技術を駆使して、製造プロセスの効率化、業務効率化、チームワーク強化、コスト削減、品質向上を実現します。このサービスは、製造業の課題を深く理解し、それに対する最適なデジタルソリューションを提供することで、企業が持続的な成長とイノベーションを達成できるようサポートします。
オンライン講座
製造業、主に購買・調達部門にお勤めの方々に向けた情報を配信しております。
新任の方やベテランの方、管理職を対象とした幅広いコンテンツをご用意しております。
お問い合わせ
コストダウンが利益に直結する術だと理解していても、なかなか前に進めることができない状況。そんな時は、newjiのコストダウン自動化機能で大きく利益貢献しよう!
(Β版非公開)