- お役立ち記事
- Improving the efficiency of lot management How to shorten the working time of the purchasing department
Improving the efficiency of lot management How to shorten the working time of the purchasing department
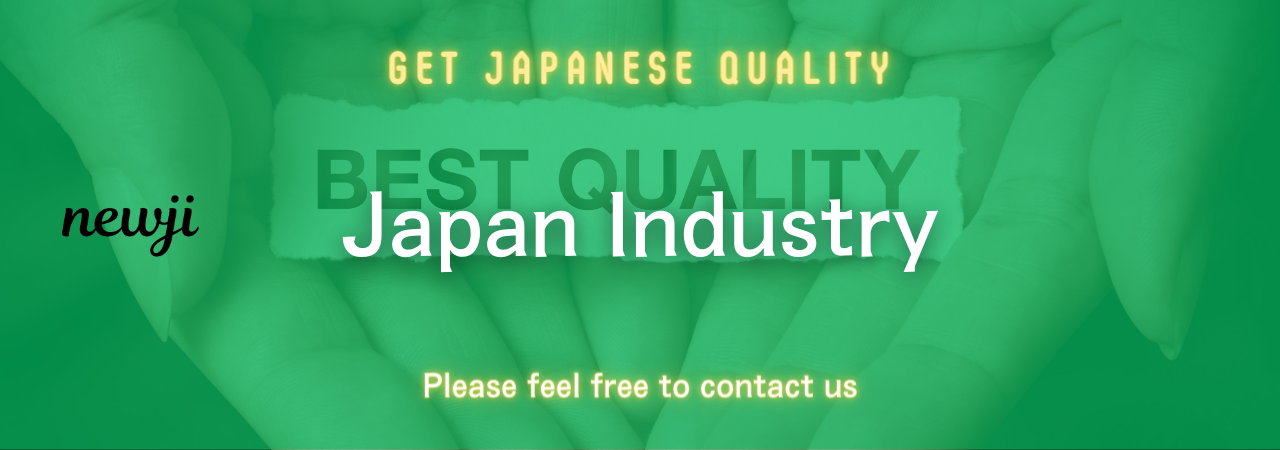
目次
Understanding Lot Management
Lot management is a crucial process in the purchasing department of any organization.
It involves tracking, recording, and managing product lots, which are batches of goods or materials that are received, stored, and eventually used or sold.
Efficient lot management ensures the timely acquisition and availability of materials while minimizing waste and reducing costs.
It’s an aspect that directly impacts an organization’s ability to perform and meet customer demands promptly.
However, without an efficient system in place, the purchasing department may face challenges in maintaining accurate inventory records, leading to delays and inefficiencies.
Importance of Improving Lot Management Efficiency
Improving the efficiency of lot management can have a significant effect on the overall productivity of the purchasing department.
A streamlined lot management process means accurate order tracking, better inventory control, and minimal errors.
It allows for effective monitoring of stock levels and provides proactive insights into potential shortages or oversupply.
By efficiently managing lots, companies can also ensure compliance with regulations, leading to improved quality assurance.
Moreover, a faster purchasing process means that customer orders are fulfilled on time, fostering better relationships with clients.
Steps to Reduce Working Time in the Purchasing Department
1. Implement Advanced Inventory Management Software
One of the essential steps to improve lot management efficiency is to adopt advanced inventory management software.
These systems can automate many aspects of the purchasing process, providing real-time data on stock levels, purchase orders, and supplier information.
Automation helps reduce manual entry errors and ensures accurate records, saving precious time for purchasing staff.
Additionally, many software solutions can predict demand patterns, thus helping to optimize order quantities and reduce lead times.
2. Standardize Procedures and Training
Creating standardized procedures and providing adequate training for employees can work wonders for efficiency.
Clear, concise procedures help ensure everyone knows their role and the exact steps in the lot management process.
Training programs should focus on best practices, use of technology, and the importance of accuracy in maintaining records.
When employees understand the process and their part in it, they’re more likely to perform their tasks efficiently.
3. Foster Supplier Relationships and Communication
Good supplier relationships can play a pivotal role in improving the purchasing department’s efficiency.
By maintaining open, regular communication with suppliers, companies can negotiate better terms, improve lead times, and build trust.
Having reliable suppliers means fewer delays in receiving lots and more consistent quality of materials.
Furthermore, good relationships can pave the way for collaboration on forecasting needs and addressing any potential bottlenecks proactively.
4. Optimize Lot Sizes
Optimizing lot sizes can significantly reduce inventory holding costs and streamline the purchasing process.
Calculating the optimal lot size requires understanding demand patterns, storage costs, and ordering lead times.
By determining the correct lot size, the purchasing department can reduce excess stock and the risk of obsolescence.
This optimization not only lowers costs but also makes it easier to manage inventory levels efficiently.
5. Utilize Barcoding and RFID Technology
Adopting barcoding or Radio Frequency Identification (RFID) technology helps in faster and more accurate tracking of lots.
These technologies allow for quick scanning and updating of inventory records and reduce the room for human errors.
RFID, in particular, provides precise, real-time tracking information and can be used to automate various processes, from goods receipt to dispatch.
Implementing such technologies can significantly cut down the time required for manual checks and audits.
6. Regularly Review and Analyze Processes
Continuous improvement should be a part of the purchasing department’s culture.
Regularly reviewing and analyzing lot management processes can help identify inefficiencies and areas for improvement.
The use of Key Performance Indicators (KPIs) and performance metrics can provide valuable insight into how well the lot management system is working.
Based on these analyses, processes can be adjusted, and best practices updated to continually enhance performance and efficiency.
7. Foster a Collaborative Environment
Encouraging collaboration among departments can further enhance lot management efficiency.
The purchasing team can work closely with sales, production, and other departments to align objectives and share information.
Such alignment ensures that all departments are working towards the same goals and helps eliminate redundancy and miscommunication.
Conclusion
Improving the efficiency of lot management is an ongoing process that requires a proactive approach and the willingness to adapt new technologies and practices.
By implementing these steps, companies can reduce the working time of their purchasing department and enhance overall productivity.
A department that operates efficiently can support the broader organizational goals, ensuring customer satisfaction and a competitive market edge.
Ultimately, it becomes a vital cog in the wheel that drives business success.
資料ダウンロード
QCD調達購買管理クラウド「newji」は、調達購買部門で必要なQCD管理全てを備えた、現場特化型兼クラウド型の今世紀最高の購買管理システムとなります。
ユーザー登録
調達購買業務の効率化だけでなく、システムを導入することで、コスト削減や製品・資材のステータス可視化のほか、属人化していた購買情報の共有化による内部不正防止や統制にも役立ちます。
NEWJI DX
製造業に特化したデジタルトランスフォーメーション(DX)の実現を目指す請負開発型のコンサルティングサービスです。AI、iPaaS、および先端の技術を駆使して、製造プロセスの効率化、業務効率化、チームワーク強化、コスト削減、品質向上を実現します。このサービスは、製造業の課題を深く理解し、それに対する最適なデジタルソリューションを提供することで、企業が持続的な成長とイノベーションを達成できるようサポートします。
オンライン講座
製造業、主に購買・調達部門にお勤めの方々に向けた情報を配信しております。
新任の方やベテランの方、管理職を対象とした幅広いコンテンツをご用意しております。
お問い合わせ
コストダウンが利益に直結する術だと理解していても、なかなか前に進めることができない状況。そんな時は、newjiのコストダウン自動化機能で大きく利益貢献しよう!
(Β版非公開)