- お役立ち記事
- Improving the flexibility of industrial robots and implementing them in the automotive parts market
月間76,176名の
製造業ご担当者様が閲覧しています*
*2025年3月31日現在のGoogle Analyticsのデータより
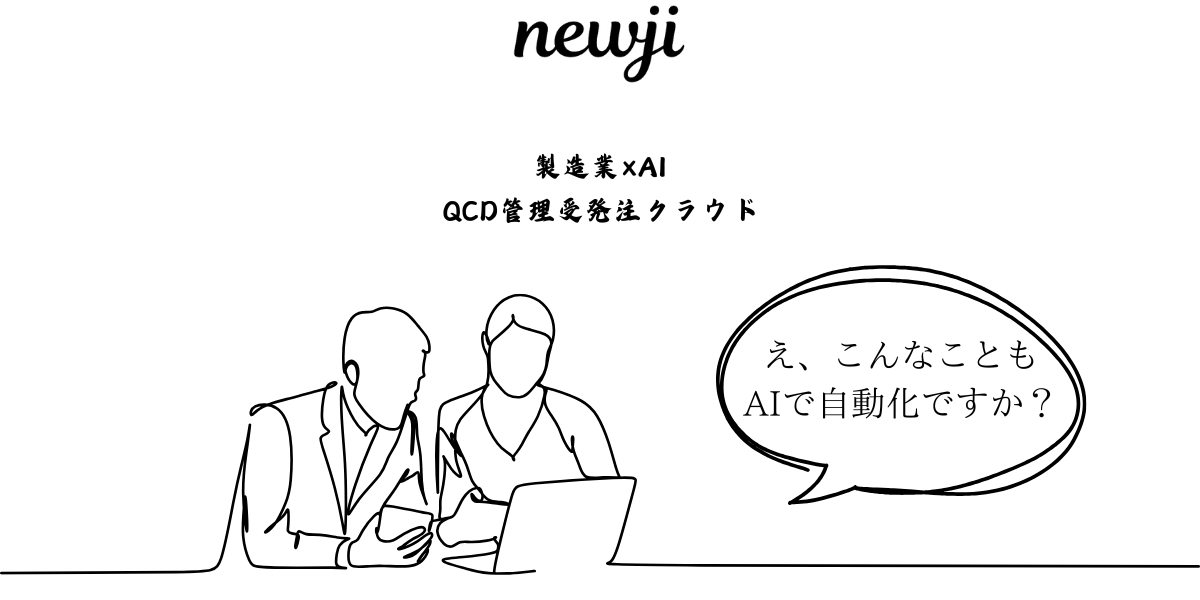
Improving the flexibility of industrial robots and implementing them in the automotive parts market
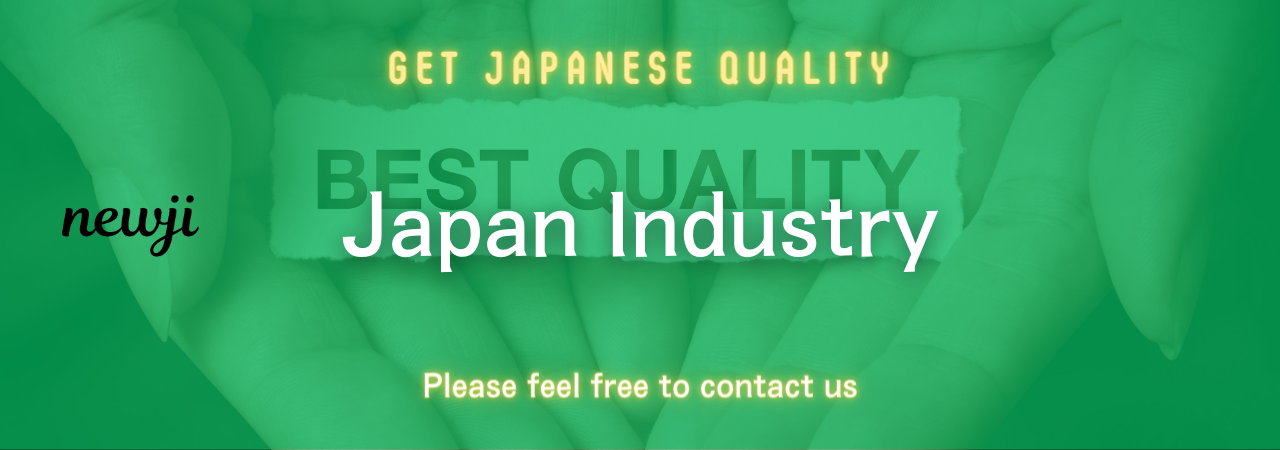
目次
Understanding the Role of Industrial Robots in the Automotive Industry
The automotive industry has seen a tremendous leap in technology, with industrial robots playing a pivotal role in manufacturing and assembly processes.
These robots are designed to perform repetitive tasks with precision and speed, significantly enhancing productivity and reducing human error.
In the automotive parts market, the role of industrial robots extends beyond assembling parts to include welding, painting, quality inspection, and other intricate operations.
The integration of robots into these processes has allowed manufacturers to meet the increasing demand for vehicles by streamlining production lines and ensuring consistency in quality.
Why Flexibility in Industrial Robots Matter
The flexibility of an industrial robot refers to its ability to perform a variety of tasks and adapt to different roles within the manufacturing process.
In the automotive parts market, this flexibility is crucial because it allows manufacturers to switch between different production tasks quickly, accommodating changes in design and order specifications without significant downtime.
This adaptability means that robots can be repurposed or reprogrammed to handle different components, facilitating a more efficient workflow.
Flexible robots can also work in smaller production environments, thus supporting industries that focus on customized or limited-edition automotive parts.
Technological Advancements Enhancing Flexibility
Several technological advancements have contributed to the enhanced flexibility of industrial robots.
One key development is the improvement in sensor technology.
Advanced sensors enable robots to better understand their surroundings, detect changes in the production line, and adjust their operations accordingly.
Additionally, artificial intelligence (AI) plays a significant role, as AI algorithms can learn from data and optimize robotic tasks, leading to smarter and more responsive robots.
Machine vision technology also allows robots to identify and handle different parts with greater accuracy, further boosting their versatility.
Modular Design and the Impact on Flexibility
Modular design is another innovation that impacts robot flexibility.
This approach involves designing robots with interchangeable parts or modules, allowing them to be easily customized or upgraded as needed.
For the automotive parts market, this means robots can be adapted to new tasks without requiring an entirely new system, saving both time and cost.
Manufacturers can implement module changes to accommodate new designs or processes with minimal disruption to ongoing operations.
Implementing Flexible Robots in the Automotive Parts Market
The implementation of flexible robots in the automotive parts market requires a strategic approach to ensure maximum efficiency and return on investment.
Manufacturers need to assess the specific requirements of their production processes and select robots whose capabilities align with those needs.
It’s also essential to invest in training for personnel who will interact with or oversee robotic systems to ensure a smooth integration.
Another crucial factor is collaboration with suppliers of robotic technology, as they can provide support and guidance in optimizing robotic operations.
Case Studies Highlighting Flexibility
Several case studies demonstrate how implementing flexible robots has transformed automotive production.
For instance, a leading automotive manufacturer introduced robots equipped with AI and vision systems to its assembly lines.
These robots could switch between different tasks within the same production shift, thus reducing the need for manual intervention and enabling the company to meet fluctuating demand more effectively.
Another example involves a supplier specializing in custom vehicle parts, which utilized modular robots to easily switch between different part designs without production delays.
Challenges in Achieving Flexibility
While the advantages of flexible industrial robots are clear, there are challenges involved in achieving this flexibility.
One significant hurdle is the cost associated with upgrading or replacing existing systems to accommodate new technologies.
Small and medium-sized enterprises (SMEs) may find it difficult to justify the initial investment despite the potential long-term benefits.
Another challenge is the complexity of programming and maintaining highly flexible robots, which requires specialized skills and knowledge.
Moreover, ensuring compatibility with existing production systems can be a complicated process, often necessitating custom solutions.
Overcoming These Challenges
To overcome these challenges, collaboration between manufacturers and technology providers is key.
By working together, they can develop cost-effective solutions tailored to the specific needs of different automotive segments.
Additionally, governments and industry bodies can play a role by offering incentives or subsidies to help offset the initial costs for SMEs.
Education and training programs can also equip the workforce with the skills needed to handle advanced robotic systems, further easing the transition to automation.
The Future of Flexible Robots in the Automotive Industry
The future of flexible robots in the automotive industry looks promising as ongoing innovations continue to push the boundaries of what these machines can do.
With increases in computational power and more sophisticated AI, the capabilities of industrial robots will only expand.
This means an even greater potential for automation within the automotive parts market, leading to improved efficiency, reduced waste, and heightened product quality.
As manufacturers continue to embrace flexibility, they will be better positioned to adapt to evolving consumer demands and market trends, ensuring their competitiveness in the global automotive landscape.
資料ダウンロード
QCD管理受発注クラウド「newji」は、受発注部門で必要なQCD管理全てを備えた、現場特化型兼クラウド型の今世紀最高の受発注管理システムとなります。
ユーザー登録
受発注業務の効率化だけでなく、システムを導入することで、コスト削減や製品・資材のステータス可視化のほか、属人化していた受発注情報の共有化による内部不正防止や統制にも役立ちます。
NEWJI DX
製造業に特化したデジタルトランスフォーメーション(DX)の実現を目指す請負開発型のコンサルティングサービスです。AI、iPaaS、および先端の技術を駆使して、製造プロセスの効率化、業務効率化、チームワーク強化、コスト削減、品質向上を実現します。このサービスは、製造業の課題を深く理解し、それに対する最適なデジタルソリューションを提供することで、企業が持続的な成長とイノベーションを達成できるようサポートします。
製造業ニュース解説
製造業、主に購買・調達部門にお勤めの方々に向けた情報を配信しております。
新任の方やベテランの方、管理職を対象とした幅広いコンテンツをご用意しております。
お問い合わせ
コストダウンが利益に直結する術だと理解していても、なかなか前に進めることができない状況。そんな時は、newjiのコストダウン自動化機能で大きく利益貢献しよう!
(β版非公開)