- お役立ち記事
- Improving the Quality of Polypropylene Products: Key Manufacturing Processes
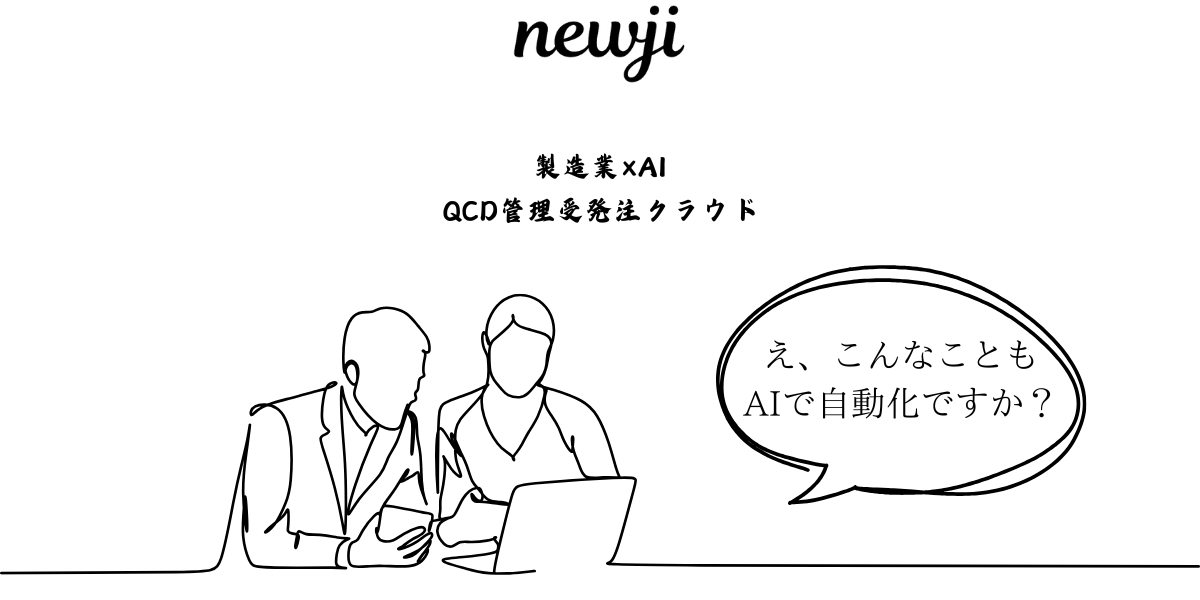
Improving the Quality of Polypropylene Products: Key Manufacturing Processes
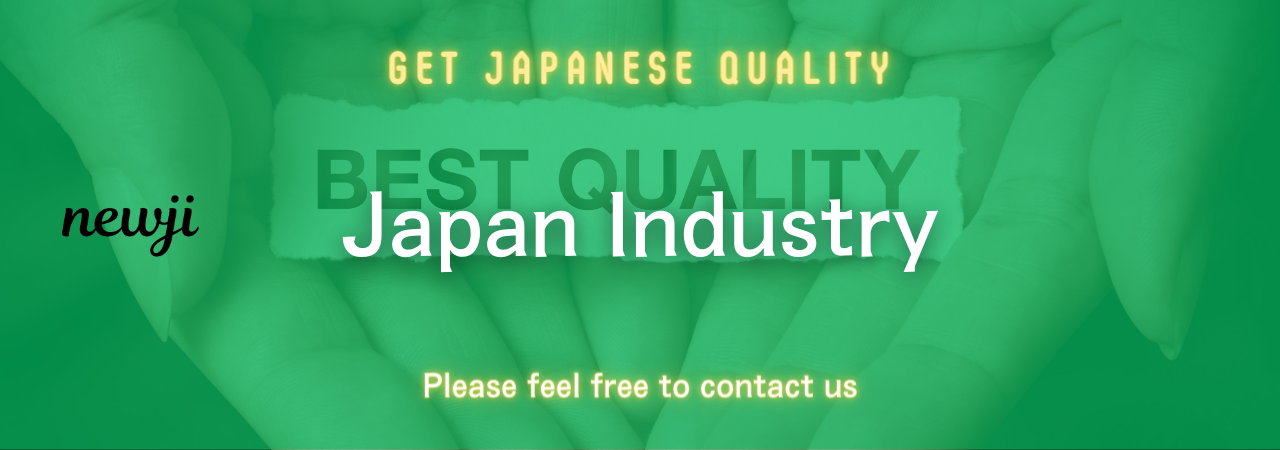
目次
Understanding Polypropylene
Polypropylene is a versatile plastic used in various industries, from packaging and textiles to automotive and construction applications.
It is a thermoplastic polymer known for its toughness, chemical resistance, and ability to withstand high temperatures.
Manufacturers favor polypropylene due to its lightweight nature, cost-effectiveness, and ease of production.
However, improving the quality of polypropylene products hinges on understanding and optimizing several key manufacturing processes.
Polymerization Process
The quality of polypropylene largely depends on the initial polymerization process.
Polypropylene is produced using a polymerization catalyst, typically a Ziegler-Natta or metallocene catalyst, along with propylene monomers.
The choice of catalyst can significantly affect the polymer’s isotacticity, which in turn influences mechanical properties like strength and rigidity.
Ensuring a controlled polymerization environment is crucial.
Factors such as temperature, pressure, and reaction time must be precisely managed to produce a high-quality polymer with desirable molecular weight and distribution.
Maintaining an optimal balance allows manufacturers to tailor polypropylene properties to specific applications, enhancing product performance.
Enhancing Catalyst Efficiency
Innovations in catalyst technology have been instrumental in improving polypropylene quality.
Catalysts must be highly efficient and specific to achieve high yields with minimal by-products.
Recent advancements focus on developing catalysts that allow better control over stereoregularity and molecular architecture.
Improving catalyst productivity can lead to a higher degree of crystallinity in the polymer, resulting in enhanced mechanical properties and clarity.
Manufacturers continually invest in research and development to innovate catalysts that can offer consistent high-performance polypropylene grades.
Extrusion and Molding Techniques
Once the polymerization process is complete, polypropylene is typically processed through extrusion or molding techniques.
These methods shape the polymer into usable products, such as films, fibers, and plastic components.
Extrusion Process
Extrusion involves heating polypropylene and forcing it through a die to create continuous shapes like sheets, films, and pipes.
Achieving uniform thickness and structural integrity in extruded products requires precise control over processing conditions like temperature, screw speed, and cooling rate.
Advanced extrusion techniques, such as biaxial orientation, can significantly improve polypropylene’s strength and clarity.
This method involves stretching the material in two perpendicular directions, aligning the polymer chains and enhancing the film’s properties for applications like packaging and labeling.
Molding Process
Molding techniques, such as injection molding and blow molding, are vital for producing complex polypropylene components used in automotive, consumer goods, and construction industries.
Injection molding involves injecting molten polypropylene into a mold, where it cools and solidifies into the desired shape.
Achieving high-quality molded products requires optimizing parameters such as injection speed, pressure, and mold temperature.
Attention to detail during the molding process ensures that products exhibit excellent surface finish, dimensional accuracy, and mechanical strength.
Quality Control and Testing
Consistent quality control and testing are essential at every stage of polypropylene manufacturing.
Manufacturers employ rigorous testing procedures to ensure that the final products meet industry standards and customer specifications.
Mechanical and Physical Testing
Mechanical testing evaluates properties like tensile strength, impact resistance, and elasticity.
These tests help assess the material’s ability to withstand forces and environmental conditions encountered during use.
Physical testing involves analyzing properties such as density, melting point, and crystallinity.
These characteristics impact performance in specific applications and inform adjustments to manufacturing processes for improved quality.
Quality Assurance Systems
Implementing quality assurance systems ensures consistent monitoring and control of production processes.
Statistical process control (SPC) and other quality management tools help identify variations and prevent defects.
Companies often seek certifications such as ISO 9001 to standardize their quality management systems and demonstrate their commitment to maintaining superior product quality.
By integrating comprehensive quality assurance measures, manufacturers can reduce waste, increase efficiency, and enhance the reliability of polypropylene products.
Innovations and Sustainability
The polypropylene industry is continually innovating to meet evolving market demands and environmental concerns.
Sustainability has become a priority, driving initiatives to reduce waste and energy consumption in production processes.
Recycling and Reusability
Recycling polypropylene has gained prominence as manufacturers aim to minimize their environmental footprint.
Developing effective recycling systems allows for reprocessing of used polypropylene into new products, reducing landfill waste and conserving resources.
Enhancing the recyclability of polypropylene involves research into improving sorting technologies and developing additives that simplify reprocessing while maintaining material properties.
Bio-Based Polypropylene
Another sustainable advancement is the development of bio-based polypropylene, produced from renewable resources like plant oils.
Bio-based variants strive to reduce reliance on fossil fuels while maintaining similar performance characteristics to conventional polypropylene.
The integration of bio-based materials into production cycles represents a significant step towards achieving sustainability in the polypropylene industry.
By focusing on these innovations, manufacturers can offer eco-friendly solutions that align with environmental goals and meet consumer preferences.
In conclusion, improving the quality of polypropylene products relies on optimizing key manufacturing processes.
From refining polymerization techniques to advancing extrusion and molding technologies, each stage plays a crucial role in determining the final product’s performance and sustainability.
As manufacturers continue to innovate and prioritize quality assurance, the future of polypropylene is poised for enhanced functionality and eco-conscious solutions.
資料ダウンロード
QCD調達購買管理クラウド「newji」は、調達購買部門で必要なQCD管理全てを備えた、現場特化型兼クラウド型の今世紀最高の購買管理システムとなります。
ユーザー登録
調達購買業務の効率化だけでなく、システムを導入することで、コスト削減や製品・資材のステータス可視化のほか、属人化していた購買情報の共有化による内部不正防止や統制にも役立ちます。
NEWJI DX
製造業に特化したデジタルトランスフォーメーション(DX)の実現を目指す請負開発型のコンサルティングサービスです。AI、iPaaS、および先端の技術を駆使して、製造プロセスの効率化、業務効率化、チームワーク強化、コスト削減、品質向上を実現します。このサービスは、製造業の課題を深く理解し、それに対する最適なデジタルソリューションを提供することで、企業が持続的な成長とイノベーションを達成できるようサポートします。
オンライン講座
製造業、主に購買・調達部門にお勤めの方々に向けた情報を配信しております。
新任の方やベテランの方、管理職を対象とした幅広いコンテンツをご用意しております。
お問い合わせ
コストダウンが利益に直結する術だと理解していても、なかなか前に進めることができない状況。そんな時は、newjiのコストダウン自動化機能で大きく利益貢献しよう!
(Β版非公開)