- お役立ち記事
- In-Mold Decoration Technologies and Advantages in OEM Manufacturing
In-Mold Decoration Technologies and Advantages in OEM Manufacturing
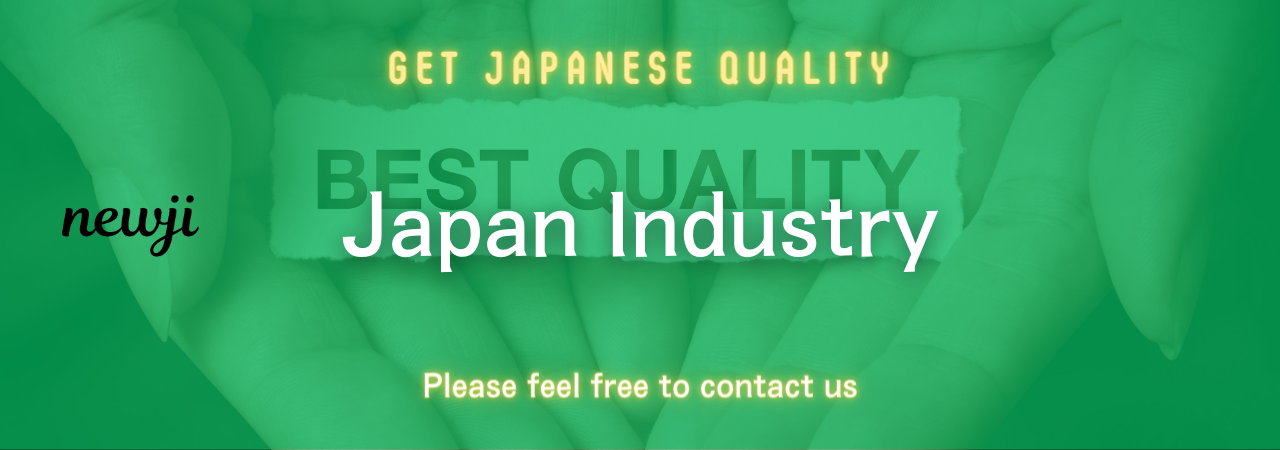
In the dynamic landscape of OEM manufacturing, In-Mold Decoration (IMD) stands out as a pivotal technology. By merging decoration and functionality into the molding process, IMD brings transformative benefits to products across various industries. Let’s dive into the intricacies of this technology and explore why it has become a game-changer.
目次
Understanding In-Mold Decoration
In-Mold Decoration (IMD) is a process that integrates decorative elements on plastic parts during the molding phase. Unlike traditional manual or post-production decoration methods, IMD embeds the decoration inside the mold, creating a seamless finish.
The IMD Process
The IMD process involves printing images or designs on a thin film. This film is then inserted into the mold cavity. During the molding process, the plastic material flows over the film, bonding it to the surface. Once the mold opens, the film becomes part of the final product, resulting in a durable and high-quality finish.
Types of In-Mold Decoration
IMD can be subdivided into two main categories:
– **In-Mold Labeling (IML)**: Utilized primarily for labeling and adding graphics. IML is common in the packaging industry, providing an efficient way to integrate labels onto plastic containers.
– **In-Mold Painting (IMP)**: Focuses on creating painted finishes and is often used in the automotive and consumer electronics sectors. IMP can replicate metallic finishes and other complex designs, offering a premium look without the cost of traditional painting methods.
Advantages of In-Mold Decoration
IMD offers a multitude of benefits that make it an attractive choice for OEM manufacturers.
Enhanced Durability
One of the key advantages of IMD is its durability. Since the decoration is embedded within the part itself, it is resistant to wear and tear. This makes IMD ideal for applications where the product will experience frequent handling or environmental stress.
Cost-Effectiveness
Integrating decoration into the molding process eliminates the need for post-production steps, reducing labor costs and production time. Additionally, because the process combines molding and decorating, it minimizes material waste.
Design Flexibility
IMD allows for a wide range of design possibilities. From intricate patterns to vibrant colors, manufacturers can achieve high levels of customization. This flexibility is particularly beneficial for brands that want to distinguish their products in the marketplace.
Improved Aesthetics
The seamless nature of IMD ensures a high-quality finish that enhances the overall appearance of the product. The technology enables manufacturers to create sleek, modern designs that are not possible with other methods.
Applications of In-Mold Decoration
IMD’s versatility makes it suitable for various industries. Below, we explore some of the key sectors that benefit from this technology.
Automotive Industry
In the automotive industry, IMD is used for interior and exterior components. From dashboard panels to trims and control buttons, IMD provides a high-quality finish that enhances the vehicle’s aesthetic appeal. Additionally, IMD can replicate metal and wood textures, offering a luxurious feel without the added weight or expense.
Consumer Electronics
IMD is widely used in the production of consumer electronics, such as smartphones, tablets, and home appliances. The technology allows for sleek designs with vibrant colors and intricate patterns, contributing to a product’s premium look and feel.
Medical Devices
In the medical field, aesthetics and durability are crucial. IMD provides a reliable way to ensure that medical devices are both visually appealing and able to withstand rigorous sterilization processes. It is used for decorating items like surgical instruments and medical containers.
Packaging
IML, a subset of IMD, is extensively used in the packaging industry. It allows for the seamless integration of labels, eliminating the need for adhesive labels that can peel off over time. This ensures that packaging remains intact and attractive throughout its lifecycle.
Challenges in In-Mold Decoration
While IMD offers many benefits, it is not without its challenges. Understanding these can help manufacturers make informed decisions.
Initial Investment
The upfront cost of IMD equipment and tooling can be significant. However, the long-term savings in labor and material costs often justify the initial investment.
Technical Expertise
IMD requires a high level of technical expertise to ensure optimal results. Manufacturers must invest in training and skilled labor to leverage this technology effectively.
Material Compatibility
Not all plastic materials are compatible with IMD. Manufacturers must carefully select materials that can bond effectively with the decorative films. This requires thorough testing and material science knowledge.
Future Trends in In-Mold Decoration
The future of IMD looks promising, with ongoing advancements that will further enhance its capabilities.
Smart Textures and Surfaces
Emerging technologies are enabling the creation of smart surfaces with integrated functionality. For example, touch-sensitive controls and haptic feedback are being incorporated into IMD processes, creating user interfaces that are both functional and aesthetic.
Sustainability
Sustainability is becoming a significant focus in manufacturing. IMD processes are being optimized to minimize waste and utilize eco-friendly materials. This aligns with the growing demand for sustainable products in the consumer market.
Integration with Additive Manufacturing
There is a growing trend towards integrating IMD with additive manufacturing techniques. This hybrid approach allows for even greater design flexibility and customization, opening up new possibilities for product innovation.
In conclusion, In-Mold Decoration is a revolutionary technology that brings numerous advantages to OEM manufacturing. Its ability to enhance durability, reduce costs, and provide design flexibility makes it a valuable asset for various industries. As technology continues to advance, IMD will undoubtedly play an increasingly important role in shaping the future of product design and manufacturing.
資料ダウンロード
QCD調達購買管理クラウド「newji」は、調達購買部門で必要なQCD管理全てを備えた、現場特化型兼クラウド型の今世紀最高の購買管理システムとなります。
ユーザー登録
調達購買業務の効率化だけでなく、システムを導入することで、コスト削減や製品・資材のステータス可視化のほか、属人化していた購買情報の共有化による内部不正防止や統制にも役立ちます。
NEWJI DX
製造業に特化したデジタルトランスフォーメーション(DX)の実現を目指す請負開発型のコンサルティングサービスです。AI、iPaaS、および先端の技術を駆使して、製造プロセスの効率化、業務効率化、チームワーク強化、コスト削減、品質向上を実現します。このサービスは、製造業の課題を深く理解し、それに対する最適なデジタルソリューションを提供することで、企業が持続的な成長とイノベーションを達成できるようサポートします。
オンライン講座
製造業、主に購買・調達部門にお勤めの方々に向けた情報を配信しております。
新任の方やベテランの方、管理職を対象とした幅広いコンテンツをご用意しております。
お問い合わせ
コストダウンが利益に直結する術だと理解していても、なかなか前に進めることができない状況。そんな時は、newjiのコストダウン自動化機能で大きく利益貢献しよう!
(Β版非公開)