- お役立ち記事
- Increasing efficiency through factory layout design and improvement, its key points, and effective use of IoT technology
月間77,185名の
製造業ご担当者様が閲覧しています*
*2025年2月28日現在のGoogle Analyticsのデータより
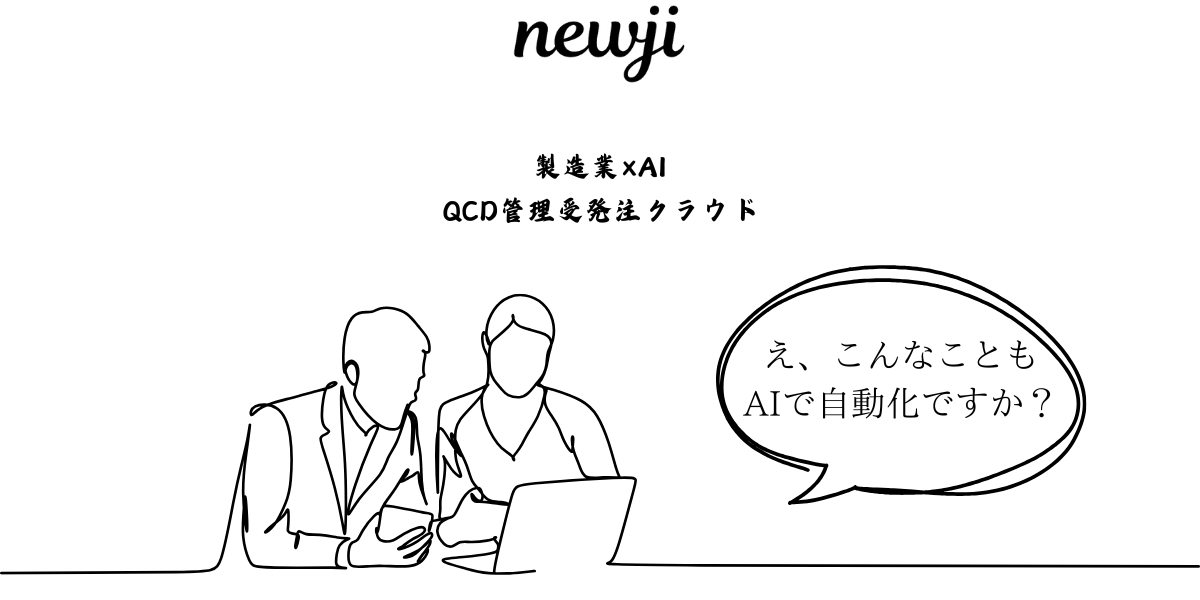
Increasing efficiency through factory layout design and improvement, its key points, and effective use of IoT technology
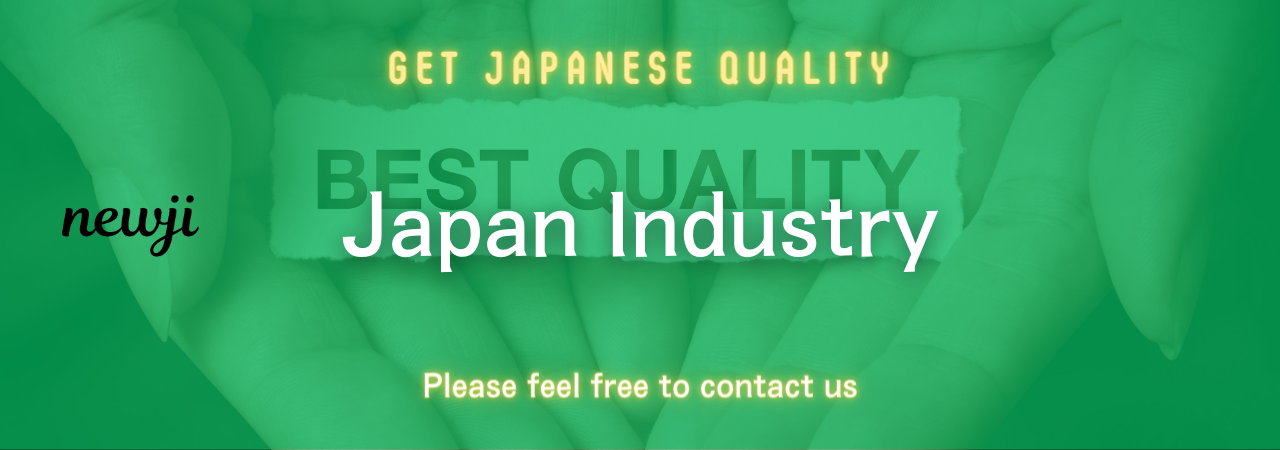
目次
Understanding the Basics of Factory Layout Design
Factory layout design is a critical component of manufacturing and production efficiency.
It involves the arrangement of physical elements within a production facility, such as machinery, equipment, workstations, and storage areas.
A well-planned layout aims to optimize workflows, minimize waste, and improve overall productivity.
When designing a factory layout, several factors need to be considered, including the type of production process, the space available, and the nature of the products being manufactured.
The goal is to create a seamless flow of materials and components, reducing the time and resources needed to move them between different stages of production.
Factory layout design can be divided into several types, including product layout, process layout, fixed-position layout, and cellular layout.
Each type has its own advantages and is suited to specific manufacturing situations.
Choosing the right layout involves evaluating the unique needs and constraints of the production environment.
Improving Efficiency Through Layout Adjustments
Improving factory efficiency often starts with evaluating and adjusting the existing layout.
By identifying bottlenecks, redundant pathways, or underutilized spaces, manufacturers can make informed decisions on layout changes that enhance productivity.
One common approach is to implement lean manufacturing principles, which focus on eliminating waste and increasing value.
This might involve rearranging workstations for better ergonomic access or minimizing movement by streamlining the transportation of materials.
Another important aspect is ensuring flexibility in the layout design to accommodate future changes in production demands.
This might involve using modular equipment that can be easily reconfigured or creating open spaces that allow for quick adaptations.
A systematic review of current processes, often aided by simulations and modeling software, helps in visualizing the changes needed and predicting their impact on production.
Through continuous evaluation and improvement, factory layouts can remain responsive and efficient over time.
The Role of IoT Technology in Factory Layout Design
The Internet of Things (IoT) is revolutionizing industrial operations by bringing unprecedented levels of control and insight into manufacturing processes.
IoT devices collect and analyze data in real-time, offering manufacturers the ability to monitor operations continuously and make data-driven decisions.
In factory layout design, IoT technology can be leveraged in several key ways.
For instance, sensors placed on equipment can track usage, monitor performance, and forecast maintenance needs, thereby reducing downtime.
This data can inform layout changes that minimize disruptions and streamline operations.
IoT technology also enables enhanced communication between different facets of the production process.
This connectivity allows for coordinated adjustments and timely responses to workflow problems, further boosting efficiency.
Additionally, implementing IoT solutions can facilitate energy management in a factory.
Smart sensors can control lighting, heating, and machinery operation, optimizing energy usage and reducing costs.
Integration of IoT with Advanced Factory Systems
Combining IoT with advanced factory systems can lead to a smarter, more responsive production environment.
By integrating IoT technology with other digital solutions like artificial intelligence (AI) and machine learning, manufacturers can enjoy a higher degree of automation and predictive capabilities.
This integration allows for a more proactive approach to maintenance, as AI can predict equipment failures before they occur, enabling timely interventions and preventing costly downtime.
Moreover, machine learning algorithms can assist in refining production processes by identifying inefficiencies or opportunities for improvement.
Through dashboards and alerts, IoT-enabled systems provide factory managers with actionable insights, helping them to better manage resources, forecast demand, and adjust production as needed.
This real-time visibility is crucial for maintaining efficiency and meeting production goals consistently.
Effective Steps to Implement IoT in Factory Layout Design
Embracing IoT technology in factory layout design begins with a clear plan and understanding of objectives.
Manufacturers should first assess the specific needs of their production environment to determine where IoT can have the greatest impact.
Step one involves the strategic placement of IoT devices throughout the facility.
This includes installing sensors on machines and along production lines to collect data on performance and environmental conditions.
Once data collection is underway, the next step is to implement data analysis tools.
These tools help in translating the raw data into meaningful insights that can inform layout adjustments and operational changes.
It’s also important to ensure that IoT devices are integrated with existing factory systems.
This may require upgrading communication networks or infrastructure to support real-time data exchange and connectivity across the devices.
Finally, establishing a feedback loop where insights gained from IoT data influence continuous improvement strategies is crucial.
By refining actions based on data analysis, factories can maintain alignment with their efficiency goals over time.
The Future of Factory Layout Design
As technology continues to advance, the future of factory layout design looks promising, with IoT and other emerging technologies playing a central role.
Manufacturers who embrace these innovations can look forward to more efficient, resilient, and adaptive production environments.
Future layout designs are likely to incorporate an even greater level of automation, fueled by IoT and AI advancements.
Robots and autonomous systems will become more prevalent, capable of carrying out complex tasks with minimal human intervention, leading to improved safety and productivity.
Digital twins, a virtual representation of physical assets, will enable real-time simulation and testing of layout changes before implementation, thus reducing risks and improving outcomes.
Additionally, as sustainability becomes increasingly important, factory designs will emphasize energy-efficient processes, resource conservation, and waste reduction, leveraging IoT for monitoring and optimization.
By staying abreast of technological developments and continually refining their approaches, manufacturers can ensure their factory layouts remain innovative and aligned with evolving business needs.
資料ダウンロード
QCD管理受発注クラウド「newji」は、受発注部門で必要なQCD管理全てを備えた、現場特化型兼クラウド型の今世紀最高の受発注管理システムとなります。
ユーザー登録
受発注業務の効率化だけでなく、システムを導入することで、コスト削減や製品・資材のステータス可視化のほか、属人化していた受発注情報の共有化による内部不正防止や統制にも役立ちます。
NEWJI DX
製造業に特化したデジタルトランスフォーメーション(DX)の実現を目指す請負開発型のコンサルティングサービスです。AI、iPaaS、および先端の技術を駆使して、製造プロセスの効率化、業務効率化、チームワーク強化、コスト削減、品質向上を実現します。このサービスは、製造業の課題を深く理解し、それに対する最適なデジタルソリューションを提供することで、企業が持続的な成長とイノベーションを達成できるようサポートします。
製造業ニュース解説
製造業、主に購買・調達部門にお勤めの方々に向けた情報を配信しております。
新任の方やベテランの方、管理職を対象とした幅広いコンテンツをご用意しております。
お問い合わせ
コストダウンが利益に直結する術だと理解していても、なかなか前に進めることができない状況。そんな時は、newjiのコストダウン自動化機能で大きく利益貢献しよう!
(β版非公開)