- お役立ち記事
- Initiatives Toward Realizing a Smart Factory
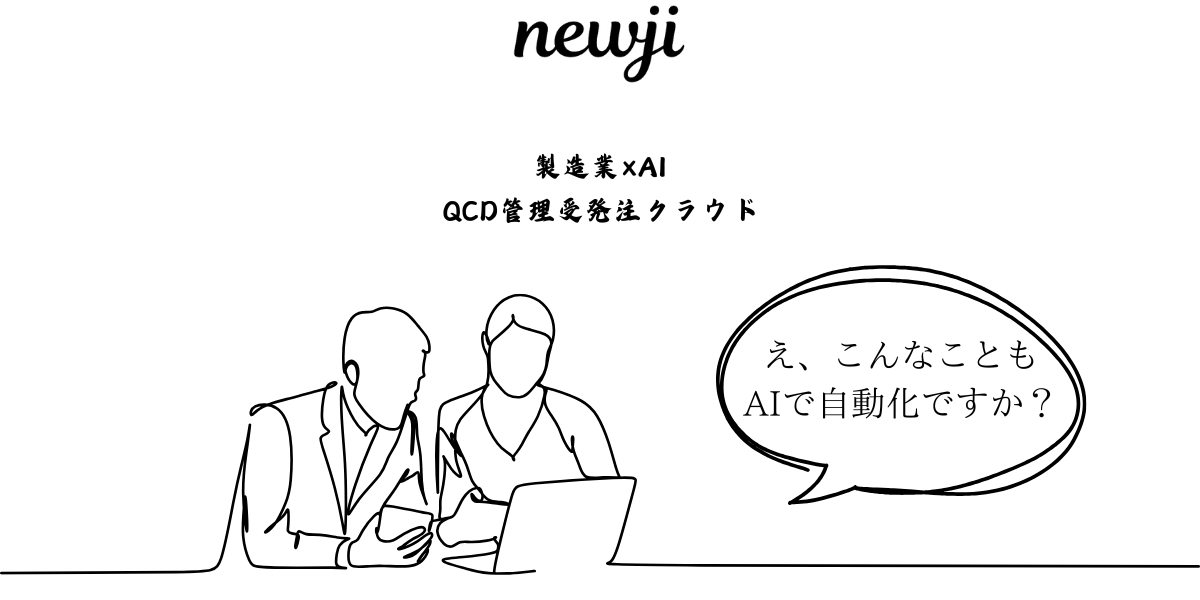
Initiatives Toward Realizing a Smart Factory
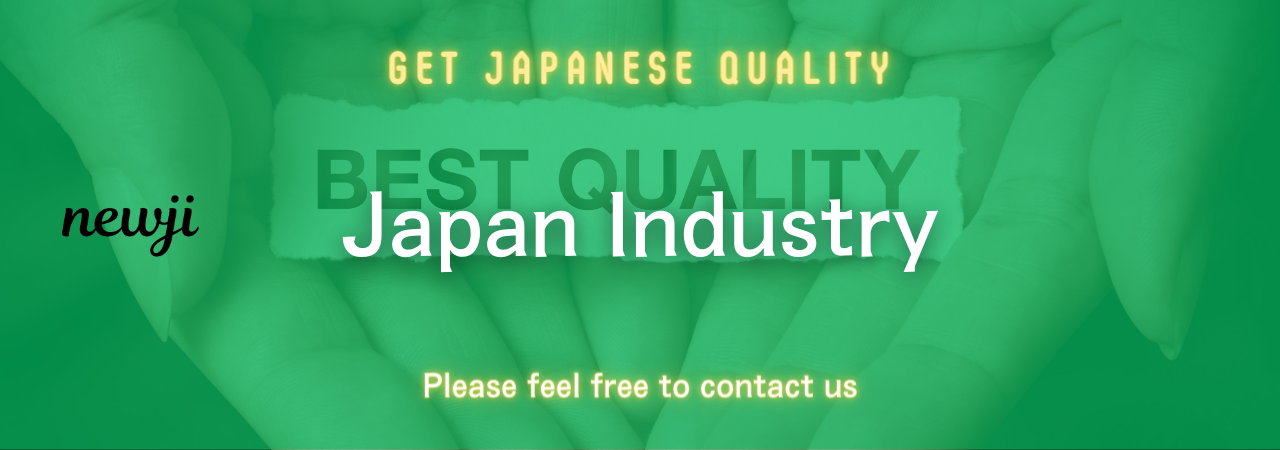
In today’s rapidly evolving technological landscape, businesses are striving to keep pace with advancements that can boost productivity and efficiency. One such advancement is the concept of a smart factory. A smart factory leverages cutting-edge technologies such as the Internet of Things (IoT), artificial intelligence (AI), big data, and automation to create an environment where manufacturing processes are interconnected and can be continuously optimized. This article delves into the initiatives that can help realize a smart factory.
目次
Understanding the Concept of a Smart Factory
A smart factory represents the pinnacle of next-generation manufacturing. Traditional factories rely heavily on manual labor and isolated systems, which often leads to inefficiencies and errors. In contrast, a smart factory integrates digital technologies to create a cohesive, automated production environment. Machines, systems, and human operators in smart factories communicate with each other seamlessly.
The Role of IoT
The Internet of Things (IoT) is fundamental in smart factories. Through sensors and devices connected to the internet, a wealth of data is generated. This data encompasses every aspect of the manufacturing process—from raw material handling to product output. By analyzing this data, manufacturers can gain valuable insights into operations. This leads to improved decision-making, predictive maintenance, and reduced downtime.
Implementing Artificial Intelligence
Artificial Intelligence (AI) in smart factories enables systems to learn from data and make autonomous decisions. AI algorithms can analyze huge datasets to identify patterns and anomalies that would go unnoticed by human operators. Machine learning, a subset of AI, constantly improves process efficiency by anticipating potential issues and suggesting corrective actions.
Strategies to Transition to a Smart Factory
Transitioning to a smart factory involves a series of strategic steps. It is not an overnight transformation but a gradual process that requires careful planning and execution.
Assessment and Planning
Before implementing new technologies, manufacturers must assess their current capabilities and identify areas that need improvement. This involves a thorough analysis of existing processes, machinery, and systems. Based on this assessment, a detailed plan outlining the steps to be taken towards becoming a smart factory should be developed. This plan should include timelines, budget allocations, and milestones.
Investing in Technology
Investing in cutting-edge technology is vital for creating a smart factory. Manufacturers should prioritize acquiring IoT devices, sensors, cloud computing infrastructure, and AI algorithms that are tailored to their specific needs. Upgrading existing machinery with sensors and connectivity features can also yield significant benefits.
Training and Skill Development
Human operators in a smart factory must be equipped with the knowledge and skills to interact with new technologies. Comprehensive training programs are essential to ensure that employees are proficient in using IoT devices, interpreting data analytics, and operating AI-driven systems. Continuous skill development is crucial as technology evolves.
Benefits of a Smart Factory
The shift towards a smart factory yields numerous benefits, many of which significantly impact the bottom line and overall operational efficiency.
Enhanced Productivity
Smart factories streamline production processes, reducing bottlenecks and minimizing waste. Automation takes over repetitive tasks, allowing human operators to focus on more complex and strategic activities. This enhances overall productivity and reduces production cycles.
Improved Quality Control
With real-time data monitoring, smart factories can maintain high-quality standards consistently. IoT sensors detect deviations from expected parameters, triggering prompt corrective measures. AI algorithms predict potential quality issues and suggest preventive actions, reducing defects and rework.
Cost Efficiency
Though initial investments in smart technology can be significant, the long-term cost savings are substantial. Predictive maintenance reduces equipment downtime and repair costs. Optimized resource management minimizes energy consumption and material waste, translating to lower operational expenses.
Flexibility and Scalability
Smart factories can adapt to changing market demands quickly. Advanced analytics provide insights into consumer trends, enabling manufacturers to adjust their production schedules accordingly. Scalability is another advantage, as smart factories can accommodate increased production volumes without compromising efficiency.
Challenges in Realizing a Smart Factory
Despite the numerous benefits, transitioning to a smart factory comes with its own set of challenges.
High Initial Costs
Implementing IoT, AI, and automation technologies require substantial initial investment. While the long-term ROI is favorable, securing the required funds can be challenging for some manufacturers.
Data Security Concerns
With increased connectivity comes the risk of cyber threats. Protecting sensitive manufacturing data and ensuring the security of IoT devices is paramount. Manufacturers must invest in robust cybersecurity measures to mitigate these risks.
Change Management
Shifting to a smart factory demands a cultural shift within the organization. Employees might resist changes due to uncertainty or a lack of understanding of new technologies. Effective change management strategies, including transparent communication and involving employees in the transition process, are crucial.
Conclusion
The journey towards realizing a smart factory is a significant undertaking, but the rewards are well worth the effort. By embracing IoT, AI, and other advanced technologies, manufacturers can create a seamless, interconnected production environment that optimizes efficiency, enhances product quality, and boosts profitability.
With careful planning, investment in the right technologies, and a focus on training and development, any manufacturer can transform their operations and join the ranks of smart factories leading the future of manufacturing.
資料ダウンロード
QCD調達購買管理クラウド「newji」は、調達購買部門で必要なQCD管理全てを備えた、現場特化型兼クラウド型の今世紀最高の購買管理システムとなります。
ユーザー登録
調達購買業務の効率化だけでなく、システムを導入することで、コスト削減や製品・資材のステータス可視化のほか、属人化していた購買情報の共有化による内部不正防止や統制にも役立ちます。
NEWJI DX
製造業に特化したデジタルトランスフォーメーション(DX)の実現を目指す請負開発型のコンサルティングサービスです。AI、iPaaS、および先端の技術を駆使して、製造プロセスの効率化、業務効率化、チームワーク強化、コスト削減、品質向上を実現します。このサービスは、製造業の課題を深く理解し、それに対する最適なデジタルソリューションを提供することで、企業が持続的な成長とイノベーションを達成できるようサポートします。
オンライン講座
製造業、主に購買・調達部門にお勤めの方々に向けた情報を配信しております。
新任の方やベテランの方、管理職を対象とした幅広いコンテンツをご用意しております。
お問い合わせ
コストダウンが利益に直結する術だと理解していても、なかなか前に進めることができない状況。そんな時は、newjiのコストダウン自動化機能で大きく利益貢献しよう!
(Β版非公開)