- お役立ち記事
- Injection molded product prototype development process and technical points
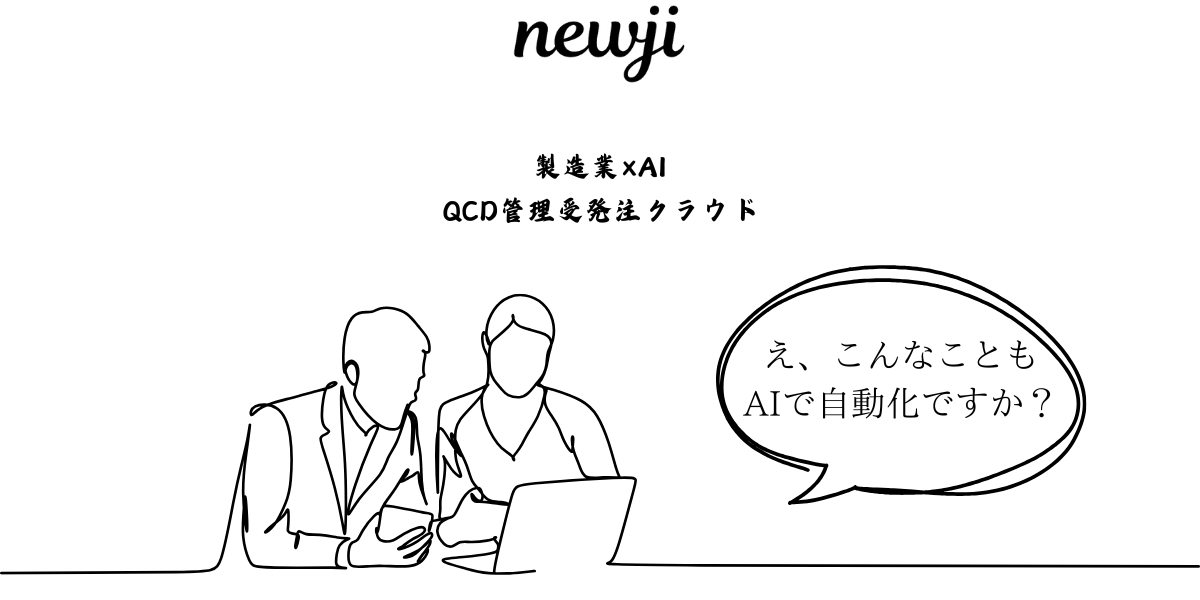
Injection molded product prototype development process and technical points
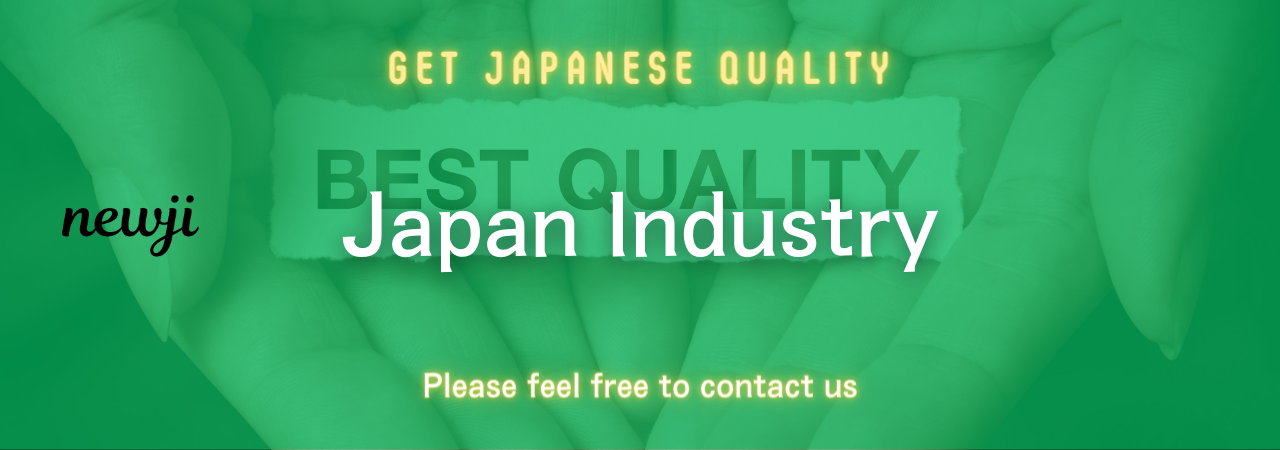
目次
Understanding Injection Molded Products
Injection molding is a widely used manufacturing process for creating items by injecting molten material into a mold.
The process is highly versatile and can produce a vast range of products, from simple household items to complex industrial components.
Understanding the intricacies of this procedure is essential for developing prototypes efficiently and effectively.
The Basics of Injection Molding
Before diving into the prototype development process, it’s crucial to grasp the fundamental aspects of injection molding.
This process involves using raw materials like plastics, metals, or glasses, melting them down, and injecting them into a mold where they eventually cool and solidify.
The result is a product that’s typically cheaper and faster to produce compared to other manufacturing methods.
The major steps in injection molding include clamping the mold, injecting the molten material, cooling the mold, and finally, ejecting the finished part.
Prototype Development Process
Developing prototypes for injection molded products involves several key steps.
These steps ensure that the finished component meets all necessary requirements and works as intended.
1. Conceptual Design
The first step in developing a prototype is creating a conceptual design.
At this stage, the focus is on defining the product’s purpose, functionality, and overall appearance.
Designers typically use computer-aided design (CAD) software to create digital models of the intended product.
This step is crucial, as it forms the foundation for the entire development process.
2. Material Selection
Choosing the right material is fundamental to the success of any injection molded product.
The material selection impacts various factors, including the product’s durability, flexibility, and cost.
Common materials used in injection molding include polypropylene, polyethylene, and polycarbonate.
The choice of material depends on the intended application and the specific properties required from the final product.
3. Detailed Design and Analysis
Once the conceptual design is finalized, a more detailed design is created.
This step typically involves refining the shape, size, and other specifications of the product.
Simulation and analysis tools are often used at this stage to test the performance and reliability of the design.
Finite Element Analysis (FEA) can help identify potential weak spots or areas of improvement before the physical prototype is made.
4. Mold Design
Designing the mold itself is a critical part of the prototype development process.
The mold needs to be designed with precision, taking into account factors such as shrinkage rates and cooling paths.
Mold design requires expertise, as even a small miscalculation can lead to flaws in the final product.
Typically, experienced engineers are involved in the mold design to ensure it meets the required standards and specifications.
5. Prototype Creation
With the mold design completed, the physical creation of the prototype can begin.
This step involves manufacturing the prototype to test the design in a real-world setting.
Prototyping helps in identifying any practical issues that might not have been evident in the digital design phase.
Rapid prototyping technologies, such as 3D printing, can be useful for creating early-stage prototypes quickly and cost-effectively.
6. Testing and Refinement
Once the prototype is created, it must undergo thorough testing.
Testing checks the product’s functionality, durability, and compliance with design specifications.
Any deficiencies or issues identified during testing need to be addressed through refinements in the design or material selection.
This iterative process continues until the prototype performs as expected and meets all design criteria.
Technical Points in Injection Molding
Understanding the technical aspects of injection molding is vital for successful prototype development.
1. Mold Accuracy
The accuracy of the mold significantly affects the quality of the final product.
Precise mold design ensures that the product dimensions and features are consistent with expectations.
Advanced machining technologies and engineering software are often employed to enhance mold accuracy and reliability.
2. Injection Pressure
Proper management of injection pressure is crucial to achieve desired results.
Too much pressure can lead to defects in the part, while too little may result in incomplete filling of the mold.
Careful calibration of injection machines can help maintain optimal pressure levels throughout production.
3. Cooling Time
The amount of time allotted for cooling can significantly affect both production efficiency and product quality.
Adequate cooling ensures the product solidifies properly without warping or distorting.
Effective cooling system designs can also reduce cycle times, thus increasing production speed.
4. Ejection Process
The ejection phase is a sensitive part of the injection molding process.
Proper ejection techniques reduce the risk of damaging the product as it is removed from the mold.
Positioning ejection pins and using specialized coatings can help minimize damage and maintain surface quality.
Impact of Prototype Development Process
The proper development of injection molded product prototypes can have a significant impact on the final production process.
A well-executed prototype development process leads to fewer production errors, reduced costs, and faster time-to-market for new products.
It also allows designers and engineers to test innovative ideas and make necessary adjustments before committing to full-scale production.
Ultimately, understanding both the prototype development process and the technical points of injection molding contributes to producing high-quality, reliable products tailored to meet specific market demands.
資料ダウンロード
QCD調達購買管理クラウド「newji」は、調達購買部門で必要なQCD管理全てを備えた、現場特化型兼クラウド型の今世紀最高の購買管理システムとなります。
ユーザー登録
調達購買業務の効率化だけでなく、システムを導入することで、コスト削減や製品・資材のステータス可視化のほか、属人化していた購買情報の共有化による内部不正防止や統制にも役立ちます。
NEWJI DX
製造業に特化したデジタルトランスフォーメーション(DX)の実現を目指す請負開発型のコンサルティングサービスです。AI、iPaaS、および先端の技術を駆使して、製造プロセスの効率化、業務効率化、チームワーク強化、コスト削減、品質向上を実現します。このサービスは、製造業の課題を深く理解し、それに対する最適なデジタルソリューションを提供することで、企業が持続的な成長とイノベーションを達成できるようサポートします。
オンライン講座
製造業、主に購買・調達部門にお勤めの方々に向けた情報を配信しております。
新任の方やベテランの方、管理職を対象とした幅広いコンテンツをご用意しております。
お問い合わせ
コストダウンが利益に直結する術だと理解していても、なかなか前に進めることができない状況。そんな時は、newjiのコストダウン自動化機能で大きく利益貢献しよう!
(Β版非公開)