- お役立ち記事
- Injection Molding Basics for Product Design and Defect Mitigation
月間76,176名の
製造業ご担当者様が閲覧しています*
*2025年3月31日現在のGoogle Analyticsのデータより
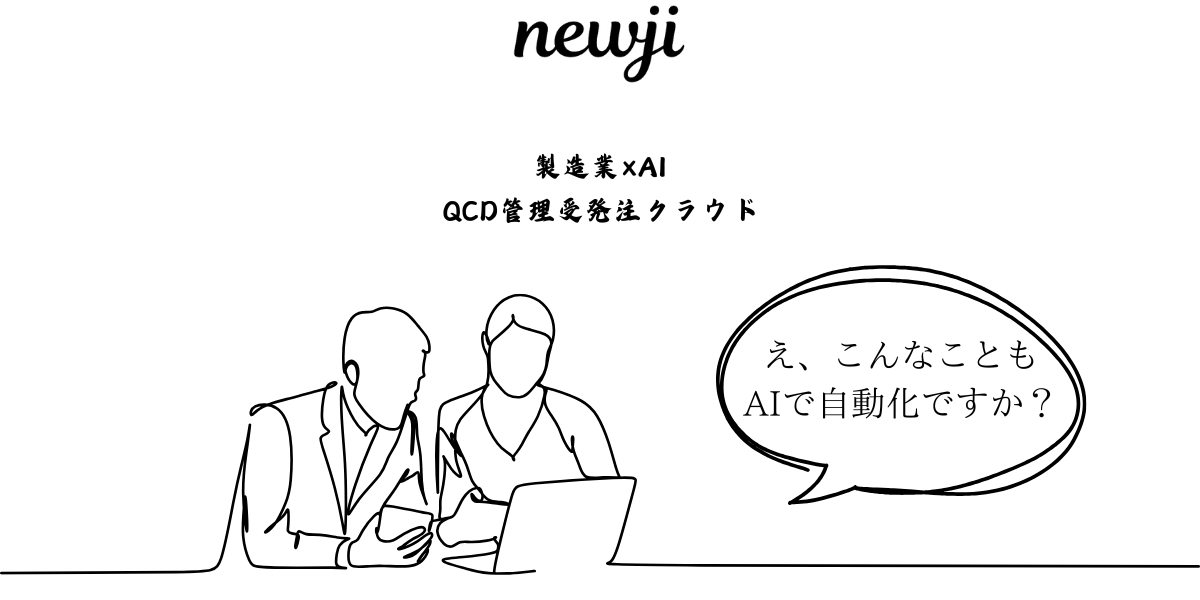
Injection Molding Basics for Product Design and Defect Mitigation
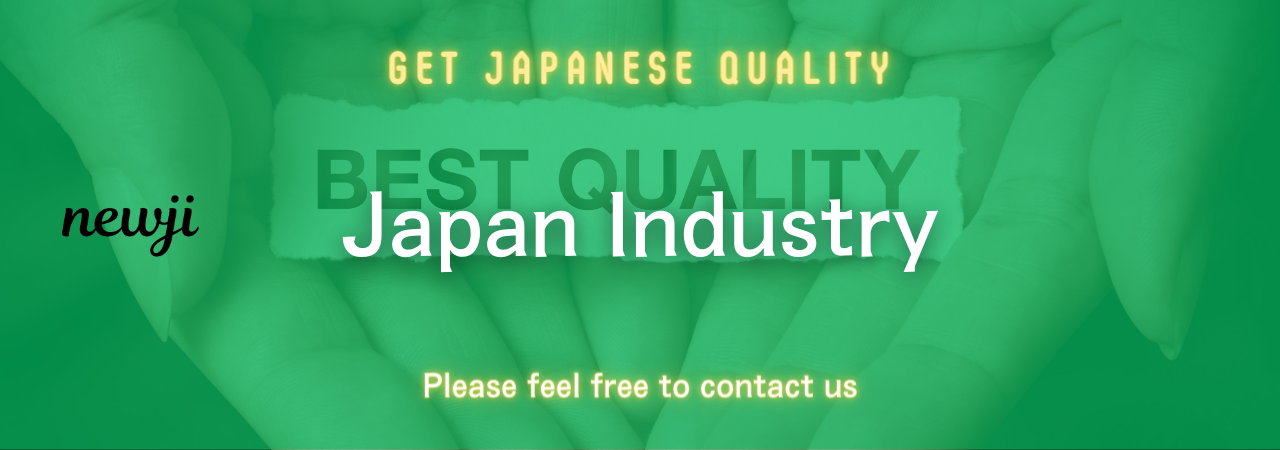
目次
Understanding Injection Molding
Injection molding is a popular manufacturing process used to create parts by injecting molten material into a mold.
The materials commonly used for injection molding are thermoplastic and thermosetting polymers.
This process is widely utilized for its efficiency and ability to produce high volumes of consistent parts.
Before diving into the nuances of product design and defect mitigation, it’s important to grasp the basics of how injection molding works.
The process starts with feeding plastic pellets into a heated barrel.
Once the plastic is melted, it is injected under pressure through a nozzle into a mold cavity.
The mold, which is shaped according to the desired design, is cooled to allow the plastic to solidify.
Finally, the molded part is ejected, and the cycle begins again.
The Importance of Product Design in Injection Molding
Good product design is integral to successful injection molding.
A well-designed product not only functions as intended but also minimizes production costs and mitigates potential defects.
Designers need to consider several factors to optimize the injection molding process.
Wall Thickness
Consistent wall thickness is crucial in injection molding.
Variations in thickness can lead to issues such as warping or sink marks.
Designers should aim for uniform wall distribution to ensure even cooling and material flow.
Draft Angles
Incorporating draft angles in the design helps in the ejection of the part from the mold.
Draft angles are slight angulations added to the vertical walls of a part.
This design feature minimizes friction during ejection, enhancing the longevity of the mold and improving production efficiency.
Rib and Boss Design
Ribs and bosses are used to add strength and facilitate assembly.
When integrating these features, it’s important to manage their thickness.
Ribs should be no more than half the wall thickness to avoid sink marks, and bosses should be optimized for structural integrity without adding unnecessary bulk.
Mitigating Defects in Injection Molding
Despite its efficiency, injection molding can be prone to defects.
Vigilant design strategies and production measures can help minimize these issues.
Common Defects
Some of the common defects in injection molding include sink marks, warping, and short shots.
Sink marks occur due to inadequate cooling or unequal wall thicknesses.
Warping happens when there’s uneven cooling, causing the part to distort.
Short shots result from insufficient material filling the mold, often due to inadequate pressure or improper venting.
Design Adjustments
To reduce the occurrence of defects, designers can make strategic adjustments.
For sink marks, ensure uniform wall thickness and consider using materials with higher shrinkage resistance.
To prevent warping, focus on symmetric designs and proper cooling time.
Increasing the injection pressure and ensuring proper venting can help avoid short shots.
Material Selection
Choosing the right material is vital to product quality and durability.
Material properties such as shrinkage, strength, and temperature resistance should align with the intended use of the finished product.
Consulting with material specialists can provide insights into the best options available for specific projects.
Collaboration and Communication
Effective collaboration between designers, engineers, and production teams is crucial to successful injection molding.
Open lines of communication can help identify potential design flaws or manufacturing challenges early in the process.
Prototyping
Creating prototypes is a valuable step in the injection molding process.
Prototypes allow designers to test and evaluate the product design before committing to full-scale production.
This stage can uncover areas for improvement and address functionality and aesthetics.
Regular Feedback
Involving teams in regular feedback sessions ensures that everyone is on the same page.
Feedback from production teams can offer practical insights and highlight issues not visible during the design phase.
Continuous Improvement
Injection molding processes can benefit from continuous evaluation and improvement efforts.
Investing in new technology, training, and process optimization can significantly enhance production quality and efficiency.
Technology Advancements
Staying updated with the latest advancements in injection molding technology is crucial.
Newer machines offer better precision, faster cycle times, and reduced energy consumption.
Automation solutions can further streamline processes and reduce human error.
Training and Development
Consistent training and skill development for team members can lead to more efficient production.
Understanding how to utilize tools and technologies effectively can prevent production issues and improve product quality.
In conclusion, mastering the basics of injection molding is essential for product design and defect mitigation.
The balance between thoughtful design and effective production techniques ensures high-quality, cost-effective manufacturing.
By continuously improving and adapting to technological advances, manufacturers can remain competitive and produce superior products.
資料ダウンロード
QCD管理受発注クラウド「newji」は、受発注部門で必要なQCD管理全てを備えた、現場特化型兼クラウド型の今世紀最高の受発注管理システムとなります。
ユーザー登録
受発注業務の効率化だけでなく、システムを導入することで、コスト削減や製品・資材のステータス可視化のほか、属人化していた受発注情報の共有化による内部不正防止や統制にも役立ちます。
NEWJI DX
製造業に特化したデジタルトランスフォーメーション(DX)の実現を目指す請負開発型のコンサルティングサービスです。AI、iPaaS、および先端の技術を駆使して、製造プロセスの効率化、業務効率化、チームワーク強化、コスト削減、品質向上を実現します。このサービスは、製造業の課題を深く理解し、それに対する最適なデジタルソリューションを提供することで、企業が持続的な成長とイノベーションを達成できるようサポートします。
製造業ニュース解説
製造業、主に購買・調達部門にお勤めの方々に向けた情報を配信しております。
新任の方やベテランの方、管理職を対象とした幅広いコンテンツをご用意しております。
お問い合わせ
コストダウンが利益に直結する術だと理解していても、なかなか前に進めることができない状況。そんな時は、newjiのコストダウン自動化機能で大きく利益貢献しよう!
(β版非公開)