- お役立ち記事
- Injection molding defect generation mechanism and its application to accuracy improvement technology using CAE analysis to prevent molding defects
月間76,176名の
製造業ご担当者様が閲覧しています*
*2025年3月31日現在のGoogle Analyticsのデータより
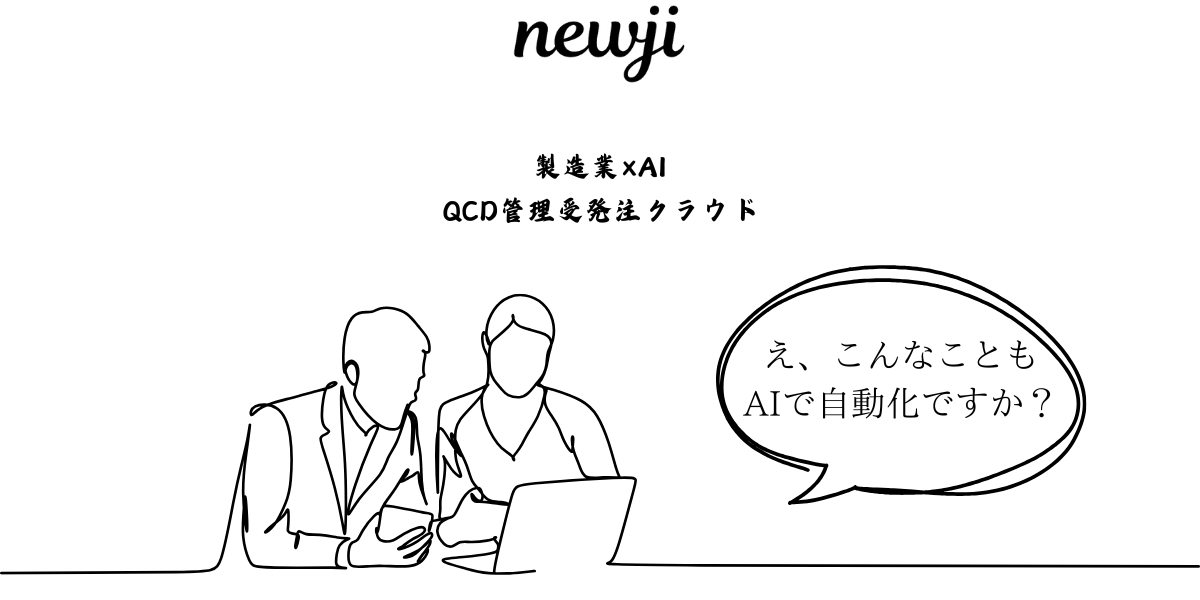
Injection molding defect generation mechanism and its application to accuracy improvement technology using CAE analysis to prevent molding defects
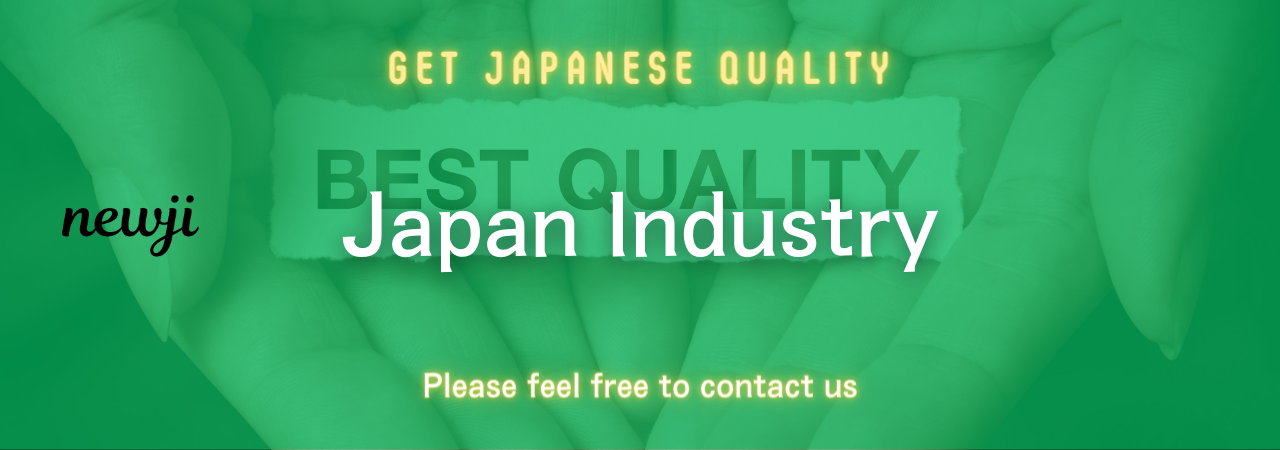
目次
Understanding Injection Molding Defects
Injection molding is a popular manufacturing process used for producing a wide range of plastic products.
However, like any manufacturing process, it is not without its challenges.
One of the major challenges faced in injection molding is the occurrence of defects.
These defects can affect the quality and performance of the molded products.
Understanding the generation mechanism of these defects is crucial for improving product quality and manufacturing efficiency.
By analyzing and addressing these mechanisms, manufacturers can prevent defects and enhance the accuracy of molded products.
Common Defects in Injection Molding
Before diving into the mechanisms, it is important to identify some common defects that occur in injection molding.
These include:
1. **Warping:** This occurs when different parts of a molded product cool and solidify at varying rates, leading to distortion in shape.
2. **Sink Marks:** These are depressions on the surface of a molded product caused by the cooling and shrinking of the internal material.
3. **Flow Lines:** Visible streaks or patterns on the surface of a molded product, typically resulting from variations in the flow of the molten material.
4. **Flash:** Excess material that escapes from the mold cavity and forms thin protrusions at the parting line.
5. **Short Shots:** Occurs when the molten plastic does not completely fill the mold cavity, resulting in incomplete products.
Mechanisms Leading to Injection Molding Defects
Understanding the root causes or mechanisms behind these defects is pivotal in both recognizing and preventing them.
Several factors contribute to the generation of defects during injection molding.
Material Characteristics
The properties of the plastic material used greatly influence the occurrence of defects.
Different plastics have different viscosities, shrinkage rates, and thermal conductivities.
Using a material unsuitable for the specific design or application can lead to defects like warping and sink marks.
Mold Design and Condition
The design and condition of the mold significantly affect product quality.
Poorly designed molds can cause defects such as short shots and flash.
Additionally, worn-out molds or those with inadequate venting may lead to defects.
Processing Parameters
Various parameters in the injection molding process, such as temperature, pressure, and injection speed, can impact defect formation.
Incorrect settings can lead to flow lines, warping, and other defects.
For example, too high an injection speed may cause turbulent flow, resulting in flow lines, while improper cooling times may cause warping.
Operator Skills
The skill level of the operator managing the injection molding process also plays a role.
An experienced operator can adjust process parameters effectively to minimize defects.
Conversely, lack of attention to detail can result in unnoticed defects during production.
Application of CAE Analysis in Preventing Defects
To improve the accuracy and quality of injection molded products, Computer-Aided Engineering (CAE) analysis has become an essential tool.
CAE analysis involves the use of simulation software to predict and address potential issues in the injection molding process.
Benefits of CAE Analysis
1. **Defect Prediction:** CAE analysis helps identify potential weak points in the mold design and process settings, predicting where defects might occur.
2. **Process Optimization:** By simulating different conditions, CAE allows for optimization of temperature, pressure, and cooling times to minimize defects.
3. **Cost Efficiency:** Early identification and correction of potential defects reduce the need for trial and error, saving both time and material costs.
4. **Improved Product Quality:** With more accurate predictions and settings adjustments, manufacturers can produce higher-quality products with fewer defects.
Implementing CAE Analysis
To effectively implement CAE analysis, manufacturers should follow several steps:
1. **Data Collection:** Gather detailed information about the materials, mold design, and processing parameters.
2. **Simulation Setup:** Use CAE software to set up a simulation based on the collected data.
3. **Analysis and Adjustment:** Analyze the simulation results to identify potential defects and adjust the process parameters accordingly.
4. **Verification:** Conduct physical trials to verify the simulation results and make further fine-tunings if necessary.
6. **Continuous Improvement:** Regularly update and refine CAE methods based on actual production outcomes to ensure ongoing improvements.
Conclusion
Injection molding defects can significantly impact the quality and functionality of plastic products.
Understanding the mechanisms that lead to these defects is crucial for their prevention.
By leveraging CAE analysis, manufacturers can predict, identify, and address potential issues before they manifest in production.
This approach not only improves product quality and accuracy but also enhances overall manufacturing efficiency.
As technology continues to advance, the integration of CAE analysis in the injection molding process will become increasingly vital in maintaining competitive advantage and ensuring customer satisfaction.
資料ダウンロード
QCD管理受発注クラウド「newji」は、受発注部門で必要なQCD管理全てを備えた、現場特化型兼クラウド型の今世紀最高の受発注管理システムとなります。
ユーザー登録
受発注業務の効率化だけでなく、システムを導入することで、コスト削減や製品・資材のステータス可視化のほか、属人化していた受発注情報の共有化による内部不正防止や統制にも役立ちます。
NEWJI DX
製造業に特化したデジタルトランスフォーメーション(DX)の実現を目指す請負開発型のコンサルティングサービスです。AI、iPaaS、および先端の技術を駆使して、製造プロセスの効率化、業務効率化、チームワーク強化、コスト削減、品質向上を実現します。このサービスは、製造業の課題を深く理解し、それに対する最適なデジタルソリューションを提供することで、企業が持続的な成長とイノベーションを達成できるようサポートします。
製造業ニュース解説
製造業、主に購買・調達部門にお勤めの方々に向けた情報を配信しております。
新任の方やベテランの方、管理職を対象とした幅広いコンテンツをご用意しております。
お問い合わせ
コストダウンが利益に直結する術だと理解していても、なかなか前に進めることができない状況。そんな時は、newjiのコストダウン自動化機能で大きく利益貢献しよう!
(β版非公開)