- お役立ち記事
- Injection Molding Innovations and OEM Benefits
月間77,185名の
製造業ご担当者様が閲覧しています*
*2025年2月28日現在のGoogle Analyticsのデータより
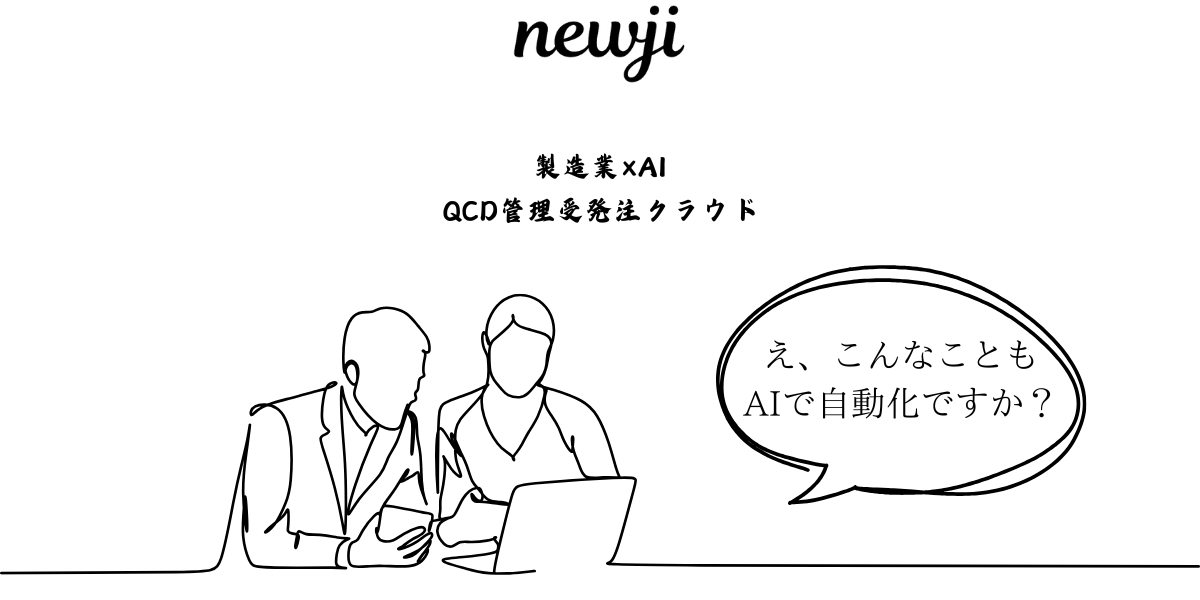
Injection Molding Innovations and OEM Benefits
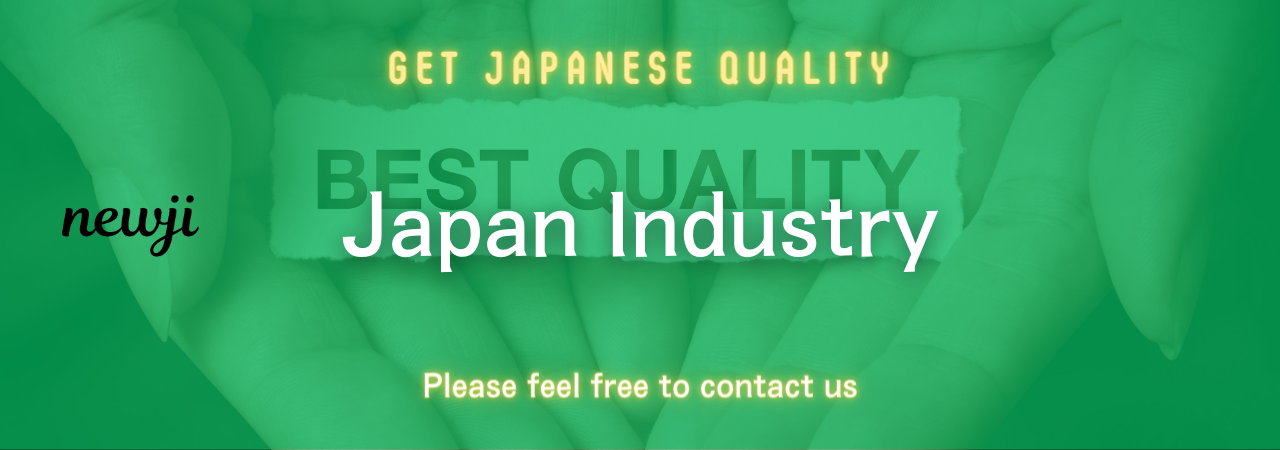
目次
Introduction to Injection Molding
Injection molding is a manufacturing process widely used for producing parts by injecting molten material into a mold.
It’s a versatile method, enabling the creation of a variety of products from small components to large items.
This process is essential in various industries including automotive, consumer goods, medical devices, and more.
With technological advancements, injection molding has evolved, providing numerous benefits, especially for Original Equipment Manufacturers (OEMs).
Technological Innovations in Injection Molding
The field of injection molding has witnessed numerous innovations that enhance efficiency, precision, and product quality.
Automation and robotics play a crucial role in modern injection molding facilities, improving cycle times and reducing labor costs.
These technologies allow for the automation of repetitive tasks, enabling human workers to focus on more complex operations.
Another significant innovation is the development of advanced materials.
Engineers now have access to high-performance polymers that offer superior strength, flexibility, and thermal resistance.
These materials expand the possibilities of what can be achieved through injection molding, allowing OEMs to meet stringent industry standards.
Furthermore, 3D printing and rapid prototyping have become invaluable in the injection molding process.
These technologies enable designers to create and test prototypes quickly and cost-effectively.
This flexibility allows for more iterations during the design phase, resulting in better final products.
Improved Mold Design and Simulation
Advancements in mold design have made it easier to create complex and intricate components with high levels of accuracy.
Computer-aided design (CAD) software allows for precise mold creation, ensuring that every detail of the product is up to specification.
Simulation software can predict potential issues before the actual molding process, saving time and reducing material waste.
Energy Efficiency and Sustainability
Sustainability is a growing concern in manufacturing, and injection molding is no exception.
Innovations in equipment, such as all-electric injection molding machines, have led to reduced energy consumption compared to traditional hydraulic machines.
These machines ensure consistent performance with minimal energy waste.
Additionally, advancements in recycling techniques allow manufacturers to repurpose scrap material, minimizing environmental impact.
OEMs adopting these practices not only reduce costs but also enhance their brand reputation by committing to sustainable manufacturing practices.
Benefits of Injection Molding for OEMs
Injection molding offers numerous benefits for OEMs, making it an attractive choice for mass production.
Cost-Effectiveness
One of the primary advantages is cost-effectiveness.
Once the initial investment in molds is made, the cost per unit decreases significantly as production volumes increase.
This is particularly beneficial for OEMs producing large volumes of parts.
Consistency and Quality
Injection molding provides consistent quality, crucial for OEMs that require parts with precise specifications and tight tolerances.
The process produces identical outputs, ensuring that each piece meets the required standards.
Design Flexibility
OEMs benefit from the design flexibility offered by injection molding.
The process supports complex geometries and allows for the integration of multiple features into a single part.
This flexibility can lead to innovative product designs that stand out in competitive markets.
Speedy Production
Speed is another significant advantage.
Once a mold is finalized, the production process is quick, enabling OEMs to respond swiftly to market demands.
This rapid turnaround is especially beneficial in industries where time-to-market is critical.
Challenges and Considerations in Injection Molding
While injection molding offers numerous advantages, there are challenges that OEMs must consider.
Initial Investment
The initial cost of designing and producing molds can be high, which may be a barrier for smaller businesses.
However, for large-scale production, the long-term cost benefits often outweigh the initial expenditure.
Material Selection
Choosing the right material is crucial and can impact cost, performance, and product success.
OEMs must consider factors such as strength, flexibility, and environmental resistance when selecting materials for their products.
Design Limitations
Despite its versatility, injection molding has some design limitations.
For instance, complex parts may require multiple molds, increasing time and costs.
OEMs must collaborate with experienced mold designers to navigate these challenges effectively.
Conclusion
Injection molding continues to revolutionize the manufacturing landscape with its innovations and numerous benefits.
For OEMs, it offers a powerful solution for producing high-quality, cost-effective parts at scale.
By embracing the latest innovations in injection molding, OEMs can enhance their production processes, meet market demands, and maintain a competitive edge.
As technology advances, the future of injection molding promises even more opportunities for growth and efficiency in manufacturing.
資料ダウンロード
QCD管理受発注クラウド「newji」は、受発注部門で必要なQCD管理全てを備えた、現場特化型兼クラウド型の今世紀最高の受発注管理システムとなります。
ユーザー登録
受発注業務の効率化だけでなく、システムを導入することで、コスト削減や製品・資材のステータス可視化のほか、属人化していた受発注情報の共有化による内部不正防止や統制にも役立ちます。
NEWJI DX
製造業に特化したデジタルトランスフォーメーション(DX)の実現を目指す請負開発型のコンサルティングサービスです。AI、iPaaS、および先端の技術を駆使して、製造プロセスの効率化、業務効率化、チームワーク強化、コスト削減、品質向上を実現します。このサービスは、製造業の課題を深く理解し、それに対する最適なデジタルソリューションを提供することで、企業が持続的な成長とイノベーションを達成できるようサポートします。
製造業ニュース解説
製造業、主に購買・調達部門にお勤めの方々に向けた情報を配信しております。
新任の方やベテランの方、管理職を対象とした幅広いコンテンツをご用意しております。
お問い合わせ
コストダウンが利益に直結する術だと理解していても、なかなか前に進めることができない状況。そんな時は、newjiのコストダウン自動化機能で大きく利益貢献しよう!
(β版非公開)