- お役立ち記事
- Injection Molding Process Improvement: Success Stories from Small Factories
Injection Molding Process Improvement: Success Stories from Small Factories
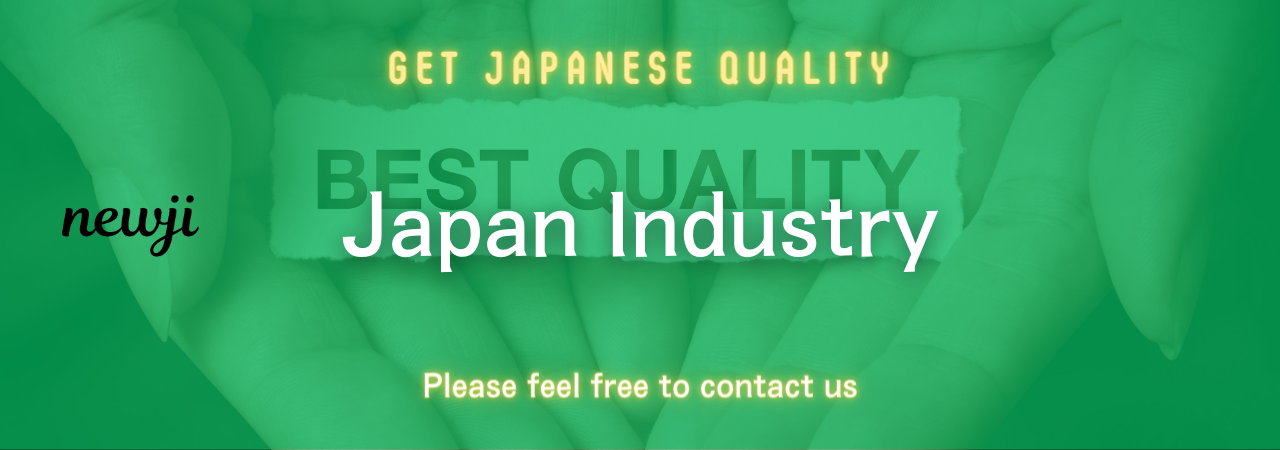
The world of manufacturing often seems like the domain of giant factories and massive production lines.
However, small factories play a crucial role in this space.
One of the manufacturing techniques that has been particularly beneficial to these smaller operations is injection molding.
This process has enabled small factories to optimize their production, offering compelling success stories.
In this article, we’ll delve into how small factories have improved their injection molding process and share their success stories.
目次
Understanding Injection Molding
Injection molding is a manufacturing process used to produce parts by injecting molten material into a mold.
The material may be plastic, metal, glass, or another substance, but plastic is the most commonly used.
It’s a versatile process that allows for high-volume production of complex shapes with tight tolerances.
Its applications range from automotive parts to household appliances, making it a critical technique in modern manufacturing.
The Basic Steps
The basic steps in injection molding are:
1. **Clamping:** The mold is clamped together to ensure it remains closed during the injection process.
2. **Injection:** Molten material is injected into the mold.
3. **Cooling:** The material cools and solidifies within the mold.
4. **Ejection:** The final product is ejected from the mold for inspection and further processing if needed.
Challenges in Small Factories
Small factories often face unique challenges when it comes to injection molding.
Limited budgets, smaller workforces, and fewer resources mean that optimizing every step of the process is crucial.
Equipment is another area of concern.
Small factories may not have access to the latest machinery, impacting efficiency.
Material Selection
Material selection is a critical aspect that can pose challenges.
Small factories must choose materials that balance cost and performance.
Selecting the wrong material can lead to increased costs and subpar products.
Quality Control
Maintaining quality is essential but can be challenging due to limited resources.
Small factories must implement stringent quality control measures to ensure each product meets standards.
Success Stories from Small Factories
Despite these challenges, many small factories have successfully improved their injection molding processes.
Here are some inspiring stories:
Case Study 1: ABC Plastics
ABC Plastics, a small factory in the Midwest, faced issues with their cooling times.
By investing in advanced cooling systems and optimizing their cycle times, they managed to reduce the cooling period by 20%.
This change led to a 15% increase in production efficiency.
Furthermore, they implemented a training program for their staff, focusing on latest techniques and technologies.
The result was a more skilled workforce and an increase in overall product quality.
Case Study 2: Precision Components Ltd
Precision Components Ltd, located in the Southeast, struggled with material waste.
They switched to a more efficient material with better flow properties.
This decision cut their material waste by 30%.
Additionally, they adopted a meticulous maintenance schedule for their machinery, reducing downtime and improving efficiency.
The combined effect was a 25% increase in productivity and significant cost savings.
Case Study 3: Vertex Manufacturing
Vertex Manufacturing in the West faced issues with inconsistent product quality.
They decided to invest in an advanced Quality Management System (QMS).
This system allowed for real-time monitoring and quality checks, ensuring each part met the required standards.
The introduction of the QMS led to a 40% reduction in defect rates.
Moreover, by analyzing data from the QMS, they optimized their processes further, boosting their overall efficiency.
Strategies for Improvement
The success stories demonstrate that even small changes can lead to significant improvements.
Here are some strategies that can be employed:
Invest in Training
Knowledge is power.
Investing in the training of employees can yield substantial benefits.
Understanding the latest techniques and technologies can improve efficiency and product quality.
Optimize Material Selection
Choosing the right material is critical.
Work with suppliers to find materials that offer the best balance of cost and performance.
Efficient material use can lead to significant cost savings and better quality products.
Upgrade Equipment
While budget constraints may limit the ability to invest in new equipment, small upgrades can make a big difference.
For instance, modern cooling systems and advanced QMS can dramatically improve efficiency and product quality.
Implement Quality Control Systems
Real-time monitoring and quality checks can nip issues in the bud.
Advanced quality control systems ensure that each product meets the required standards, reducing waste and increasing customer satisfaction.
Conclusion
Injection molding is a versatile and crucial manufacturing process.
Small factories, despite their unique challenges, can significantly improve their injection molding process.
As shown by the success stories of ABC Plastics, Precision Components Ltd, and Vertex Manufacturing, optimization is possible.
By investing in training, selecting the right materials, upgrading equipment, and implementing stringent quality control systems, small factories can achieve remarkable results.
These strategies not only improve efficiency and reduce costs but also enhance product quality, leading to increased customer satisfaction and business growth.
Small factories have proven that size is no barrier to success in the world of injection molding.
With the right approach and a willingness to innovate, they can achieve outstanding results.
資料ダウンロード
QCD調達購買管理クラウド「newji」は、調達購買部門で必要なQCD管理全てを備えた、現場特化型兼クラウド型の今世紀最高の購買管理システムとなります。
ユーザー登録
調達購買業務の効率化だけでなく、システムを導入することで、コスト削減や製品・資材のステータス可視化のほか、属人化していた購買情報の共有化による内部不正防止や統制にも役立ちます。
NEWJI DX
製造業に特化したデジタルトランスフォーメーション(DX)の実現を目指す請負開発型のコンサルティングサービスです。AI、iPaaS、および先端の技術を駆使して、製造プロセスの効率化、業務効率化、チームワーク強化、コスト削減、品質向上を実現します。このサービスは、製造業の課題を深く理解し、それに対する最適なデジタルソリューションを提供することで、企業が持続的な成長とイノベーションを達成できるようサポートします。
オンライン講座
製造業、主に購買・調達部門にお勤めの方々に向けた情報を配信しております。
新任の方やベテランの方、管理職を対象とした幅広いコンテンツをご用意しております。
お問い合わせ
コストダウンが利益に直結する術だと理解していても、なかなか前に進めることができない状況。そんな時は、newjiのコストダウン自動化機能で大きく利益貢献しよう!
(Β版非公開)