- お役立ち記事
- Ink migration risk management for food packaging printing
月間76,176名の
製造業ご担当者様が閲覧しています*
*2025年3月31日現在のGoogle Analyticsのデータより
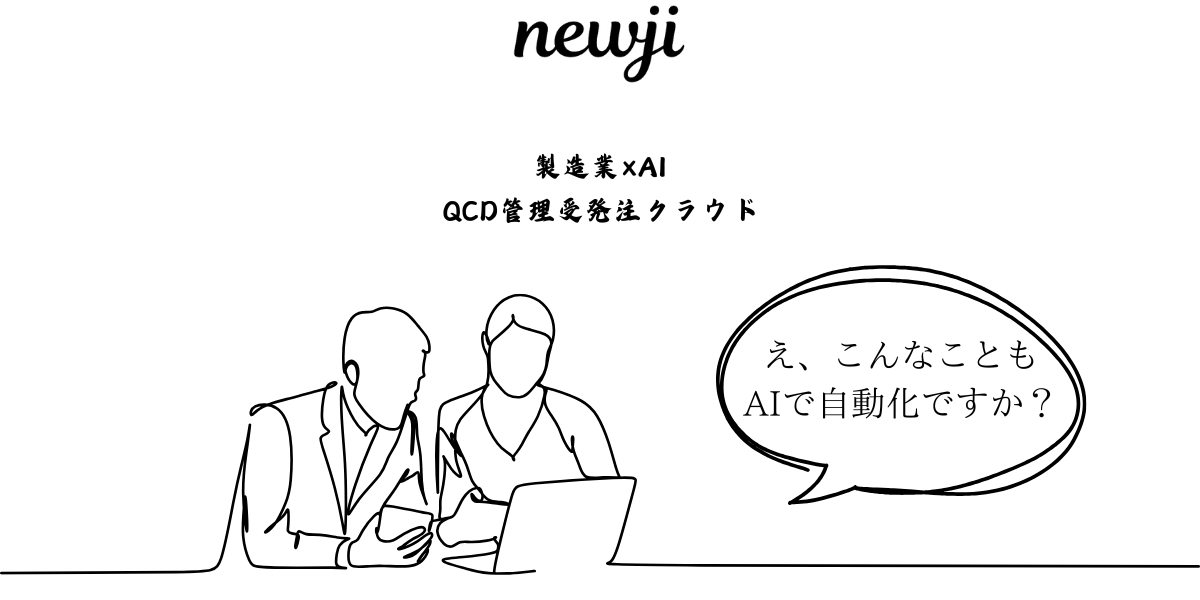
Ink migration risk management for food packaging printing
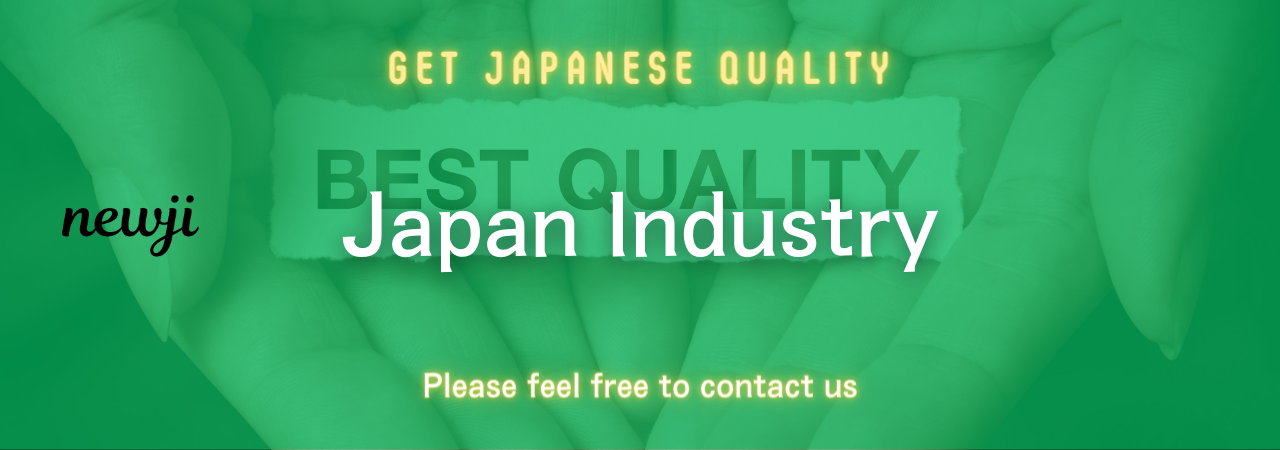
目次
Understanding Ink Migration in Food Packaging
Food packaging plays a critical role in preserving the quality and safety of food products.
However, one often overlooked aspect is the risk associated with ink migration.
Ink migration refers to the movement of ink components from the packaging materials to the food product itself.
This can potentially lead to contamination and pose health risks to consumers.
Understanding and managing ink migration risk is crucial for maintaining the integrity of food packaging.
What Causes Ink Migration?
Several factors contribute to ink migration in food packaging.
Firstly, the composition of the ink itself is a major factor.
Inks can contain a variety of substances like pigments, binders, and solvents, some of which are volatile and can migrate into the food.
Additionally, the type of packaging material, the printing method used, and the conditions during processing and storage can all influence the extent of ink migration.
For instance, flexible packaging materials like films are more susceptible to ink transfer compared to rigid materials.
The process of laminate production, where multiple layers are combined under heat and pressure, can also facilitate the movement of ink components.
Furthermore, high temperatures or extended storage times can exacerbate this risk.
Risks and Regulations
The primary concern with ink migration is the potential health risk to consumers.
Certain chemical substances found in inks may be toxic, allergenic, or harmful if they contaminate food.
Beyond health implications, this can also impact the taste and quality of the food product, leading to potential consumer dissatisfaction and brand reputation damage.
Governments and regulatory bodies have established guidelines and regulations to mitigate these risks.
In the European Union, for example, the regulation (EC) No. 1935/2004 outlines safety requirements for materials that come into contact with food.
Similarly, the Code of Federal Regulations (CFR) Title 21 in the United States includes specific sections addressing food packaging safety and ink usage.
Strategies for Managing Ink Migration
To effectively manage ink migration risks, businesses involved in food packaging must adopt a proactive approach.
Choosing the Right Ink
Selecting the right type of ink is critical in reducing migration risks.
Low-migration inks are specifically formulated to minimize the movement of harmful substances from the coating to the food product.
These inks achieve this by utilizing safer solvents and binders.
Businesses should collaborate with ink manufacturers to ensure compliance with safety standards and to select suitable ink formulations.
Optimizing Packaging Materials
Packaging materials themselves play a crucial role in preventing ink migration.
Materials with a high barrier to permeability are ideal as they minimize the transfer of ink components.
Using multi-layer laminates or coatings that effectively block migration can also be beneficial.
It is important to test and validate the compatibility of packaging materials with the chosen inks to ensure optimal performance.
Proper Printing Processes
Implementing proper printing processes is another essential step in managing ink migration.
Printers should adhere to industry best practices and follow technical guidelines to control factors such as drying time and curing processes.
Ensuring that inks are fully cured or dried before packaging food is crucial to reducing migration risks.
Moreover, maintaining a clean and controlled printing environment can prevent contamination from external sources.
Regular Testing and Monitoring
Regular testing and monitoring of packaging materials and ink compositions are essential to ensure ongoing compliance with safety standards.
Conducting migration tests under conditions that mimic real-world scenarios, such as varying temperatures and humidity levels, can provide valuable insights.
These tests help identify potential issues and enable corrective actions before packaging reaches consumers.
The Role of Innovations and Technology
Technological advancements continue to offer new solutions for ink migration risk management.
For example, digital printing technologies have evolved significantly and offer precision, reducing the potential for over-application of ink and subsequent migration.
Moreover, advancements in barrier coatings and materials enhance the safety profile of food packaging.
Nanotechnology also shows promise in improving ink formulations by incorporating nanoparticles that serve as migration barriers.
Research and development in this field hold significant potential for creating safer and more effective packaging solutions.
Conclusion
Managing ink migration risk in food packaging is crucial to ensure the safety and quality of food products.
By understanding the causes and employing strategies such as using low-migration inks, optimizing packaging materials, and adhering to proper processes, manufacturers can significantly reduce the risk of ink contamination.
Innovation and ongoing testing further bolster these efforts, ultimately safeguarding consumer health and maintaining brand reputation.
As regulations continue to evolve, staying informed and proactive remains essential for success in the food packaging industry.
資料ダウンロード
QCD管理受発注クラウド「newji」は、受発注部門で必要なQCD管理全てを備えた、現場特化型兼クラウド型の今世紀最高の受発注管理システムとなります。
ユーザー登録
受発注業務の効率化だけでなく、システムを導入することで、コスト削減や製品・資材のステータス可視化のほか、属人化していた受発注情報の共有化による内部不正防止や統制にも役立ちます。
NEWJI DX
製造業に特化したデジタルトランスフォーメーション(DX)の実現を目指す請負開発型のコンサルティングサービスです。AI、iPaaS、および先端の技術を駆使して、製造プロセスの効率化、業務効率化、チームワーク強化、コスト削減、品質向上を実現します。このサービスは、製造業の課題を深く理解し、それに対する最適なデジタルソリューションを提供することで、企業が持続的な成長とイノベーションを達成できるようサポートします。
製造業ニュース解説
製造業、主に購買・調達部門にお勤めの方々に向けた情報を配信しております。
新任の方やベテランの方、管理職を対象とした幅広いコンテンツをご用意しております。
お問い合わせ
コストダウンが利益に直結する術だと理解していても、なかなか前に進めることができない状況。そんな時は、newjiのコストダウン自動化機能で大きく利益貢献しよう!
(β版非公開)