- お役立ち記事
- Innovation in adhesive technology between plastic and steel and optimization of manufacturing process
月間77,185名の
製造業ご担当者様が閲覧しています*
*2025年2月28日現在のGoogle Analyticsのデータより
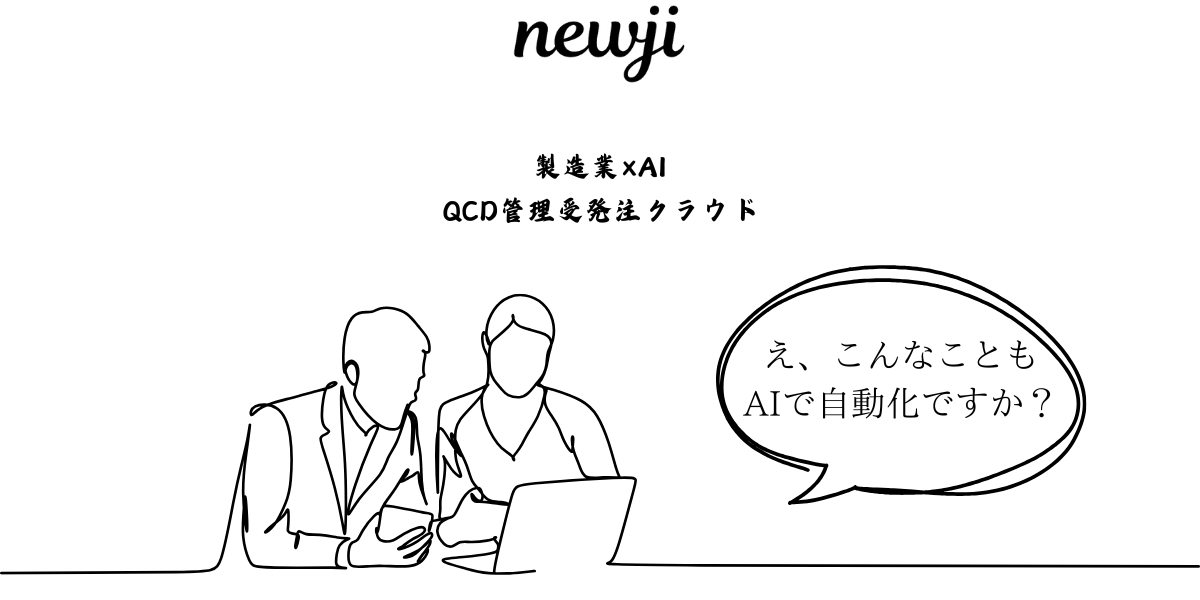
Innovation in adhesive technology between plastic and steel and optimization of manufacturing process
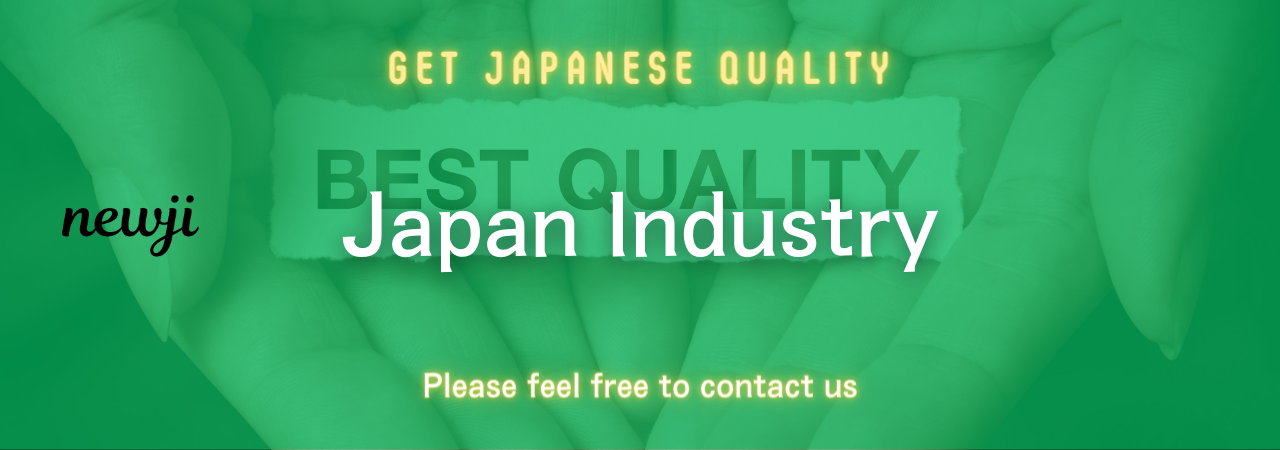
Innovations in adhesive technology have revolutionized the way industries bond materials like plastic and steel.
These advancements not only improve the quality and durability of products but also streamline the manufacturing process, leading to significant cost savings and enhanced efficiency.
This article explores the latest innovations in adhesive technology, emphasizing their impact on bonding plastic to steel and the resulting optimization of manufacturing processes.
目次
The Importance of Adhesive Technology in Manufacturing
Adhesive technology plays a crucial role in modern manufacturing, allowing different materials to be joined seamlessly.
Traditionally, mechanical fastening methods like bolts and welding were the go-to solutions for bonding materials such as plastic and steel.
However, these methods often present challenges, including increased weight, susceptibility to corrosion, and limited flexibility in design.
In contrast, adhesives provide a way to join materials without these drawbacks.
They offer greater flexibility, distribute stress more evenly across bonded surfaces, and can bond materials that differ significantly in their physical properties.
These characteristics are particularly vital in industries such as automotive, aerospace, and consumer electronics, where the demand for lightweight and durable products is high.
Challenges in Bonding Plastic and Steel
Bonding plastic and steel presents unique challenges due to their different physical and chemical properties.
Steel is a rigid, high-strength material, while plastic can vary widely in terms of flexibility, chemical composition, and surface energy.
Additionally, plastics are often non-porous, which can hinder adhesion.
Thermal expansion rates differ significantly between plastics and steel, potentially causing delamination when exposed to temperature changes.
Moreover, certain types of plastic may interact with adhesives differently, leading to inconsistent results across various applications.
Overcoming these challenges requires an in-depth understanding of both materials and the development of adhesives designed specifically for such applications.
Recent Innovations in Adhesive Technology
Advanced Epoxy Adhesives
Epoxy adhesives have long been used in industrial applications due to their strong bonding capabilities.
Recent advancements have led to the development of specialized formulations that enhance their compatibility with both plastic and steel.
These advanced epoxy adhesives can withstand extreme temperatures and resist chemical and environmental degradation.
They also provide superior adhesion without the need for harsh surface preparation, making them ideal for high-stress applications like automotive and aerospace components.
Acrylic Adhesives
Acrylic adhesives are another category benefiting from recent technological advancements.
These adhesives cure quickly at room temperature, reducing production times and energy consumption.
New formulations have focused on improving their flexibility and impact resistance, making them suitable for dynamically loaded applications.
Moreover, low VOC (Volatile Organic Compounds) acrylic adhesives align with the growing emphasis on environmentally conscious manufacturing practices.
Their fast curing times and adaptability make acrylic adhesives a popular choice for manufacturers looking to optimize their processes.
Hybrid Adhesives
Hybrid adhesives combine the best properties of different adhesive types, offering a versatile solution for bonding plastic to steel.
These adhesives often blend urethane, epoxy, and acrylic components, providing a customized balance of strength, flexibility, and durability.
Hybrid adhesives are particularly valuable in applications requiring rapid curing times and strong, lasting bonds.
Their adaptability makes them ideal for complex manufacturing environments where multiple material types are used.
Optimizing the Manufacturing Process
The integration of advanced adhesive technologies into manufacturing processes presents numerous advantages.
Improved Production Efficiency
By replacing mechanical fasteners with adhesives, manufacturers can streamline production lines.
The reduction in weight and the simplification of assembly processes contribute to faster production times.
Adhesives also require less secondary finishing, such as grinding or polishing, further enhancing production efficiency.
Cost Reduction
While high-performance adhesives may initially seem more expensive than traditional fastening methods, they often lead to significant cost savings over time.
The savings come from reduced labor costs, fewer components needed, and decreased material waste.
Additionally, the enhanced durability and reduced maintenance of adhesive-bonded products contribute to lower lifecycle costs.
Enhanced Product Design
Adhesive technology allows for greater freedom in product design by enabling the joining of complex shapes and materials that are incompatible with traditional methods.
This flexibility leads to innovative product designs that can differentiate manufacturers in competitive markets.
Lighter products with fewer assembly parts can result in more efficient and eco-friendly products, aligning with consumer preferences and regulatory standards.
Conclusion
The innovations in adhesive technology, specifically in bonding plastic and steel, have transformed modern manufacturing processes.
By providing stronger and more efficient solutions, these advancements have allowed industries to overcome traditional challenges associated with material bonding.
The result is optimized manufacturing processes that reduce costs, enhance productivity, and enable innovative design possibilities.
As industries continue to evolve, ongoing research and development in adhesive technologies promise further improvements.
Manufacturers that embrace these innovations are well-positioned to meet the demands of the future, delivering high-quality products in increasingly sustainable and resource-efficient ways.
資料ダウンロード
QCD管理受発注クラウド「newji」は、受発注部門で必要なQCD管理全てを備えた、現場特化型兼クラウド型の今世紀最高の受発注管理システムとなります。
ユーザー登録
受発注業務の効率化だけでなく、システムを導入することで、コスト削減や製品・資材のステータス可視化のほか、属人化していた受発注情報の共有化による内部不正防止や統制にも役立ちます。
NEWJI DX
製造業に特化したデジタルトランスフォーメーション(DX)の実現を目指す請負開発型のコンサルティングサービスです。AI、iPaaS、および先端の技術を駆使して、製造プロセスの効率化、業務効率化、チームワーク強化、コスト削減、品質向上を実現します。このサービスは、製造業の課題を深く理解し、それに対する最適なデジタルソリューションを提供することで、企業が持続的な成長とイノベーションを達成できるようサポートします。
製造業ニュース解説
製造業、主に購買・調達部門にお勤めの方々に向けた情報を配信しております。
新任の方やベテランの方、管理職を対象とした幅広いコンテンツをご用意しております。
お問い合わせ
コストダウンが利益に直結する術だと理解していても、なかなか前に進めることができない状況。そんな時は、newjiのコストダウン自動化機能で大きく利益貢献しよう!
(β版非公開)