- お役立ち記事
- Innovation in Japanese Manufacturing and Its Adoption Cases
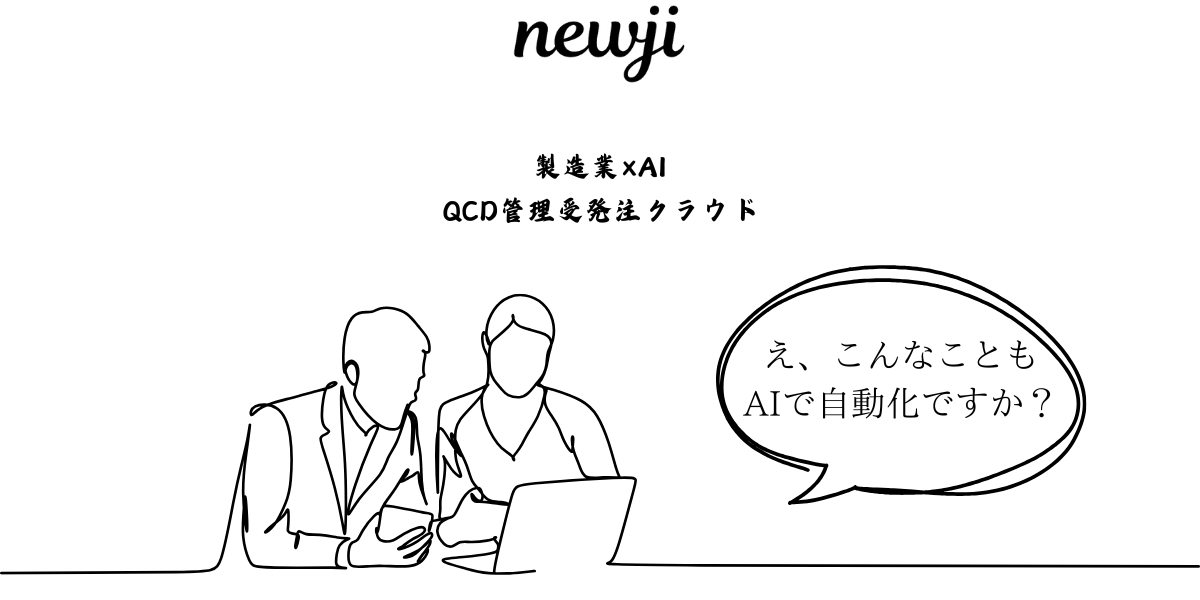
Innovation in Japanese Manufacturing and Its Adoption Cases
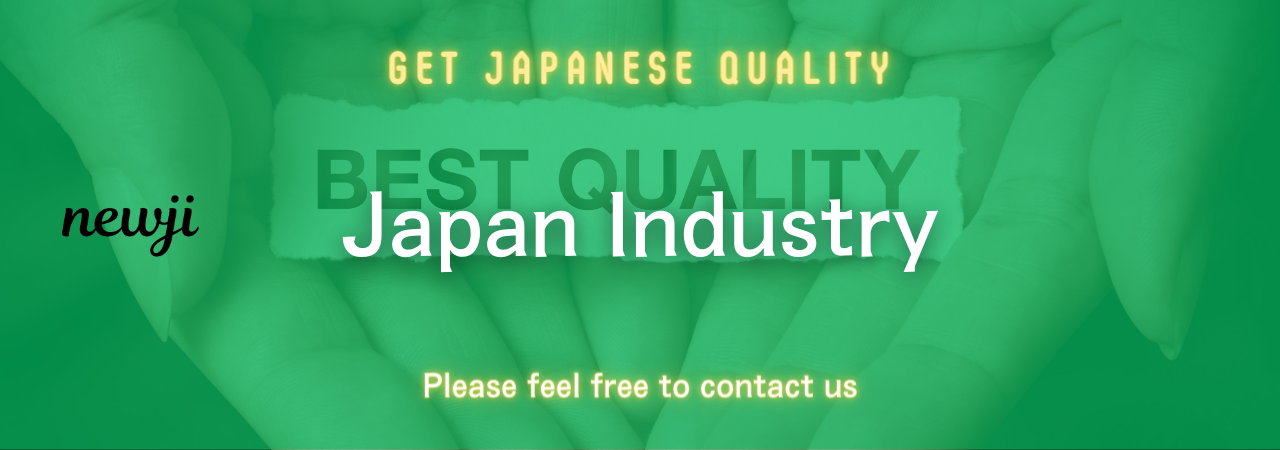
Japanese manufacturing has long been renowned for its commitment to quality, precision, and innovation.
This standard has made Japan a global leader in various industrial sectors, setting benchmarks for efficiency and reliability.
Recently, Japanese manufacturers have been focusing even more on innovative practices to stay ahead in a competitive market.
This article explores the evolution of Japanese manufacturing and showcases some adoption cases that provide insights into how these practices are implemented.
目次
The Foundations of Japanese Manufacturing
Japanese manufacturing has been heavily influenced by traditional philosophies and practices.
Kaizen, meaning “continuous improvement,” is one example.
This concept is centered on the idea of making incremental changes to enhance efficiency and effectiveness.
Another significant principle is Just-in-Time (JIT) manufacturing.
This approach aims to reduce waste by producing only what is needed, when it’s needed, and in the required quantities.
Toyota, one of Japan’s most prominent automakers, pioneered this technique, revolutionizing global manufacturing processes.
Technological Innovations
Japan has been at the forefront of integrating cutting-edge technologies into manufacturing processes.
From robotics to artificial intelligence (AI), the technological landscape in Japan is ever-evolving.
Robotic Automation
Robots have long been a staple in Japanese manufacturing.
Advanced robotic systems are used to carry out repetitive tasks with high precision.
Companies like FANUC and Yaskawa Electric are leading the way in industrial robotics, providing solutions that enhance productivity and safety.
Artificial Intelligence and IoT
AI and the Internet of Things (IoT) are playing an increasingly important role in modern manufacturing.
Smart factories use AI to predict machine failures, thereby reducing downtime.
IoT devices collect data in real-time, offering insights into production processes and allowing for rapid adjustments.
Fujitsu and Hitachi are among the companies spearheading these innovations, making factories smarter and more efficient.
Sustainability in Manufacturing
Environmental concerns are prompting Japanese manufacturers to adopt more sustainable practices.
Eco-friendly manufacturing processes not only help in reducing the carbon footprint but also offer long-term cost benefits.
Clean Energy and Resource Management
Japanese companies are increasingly turning to renewable energy sources.
Solar panels and wind turbines are becoming common sights in industrial areas.
Toyota’s Environmental Challenge 2050 aims to eliminate CO2 emissions entirely from its production activities.
Additionally, companies like Panasonic are investing in energy-efficient technologies to minimize waste and optimize resources.
Zero-Waste Manufacturing
The zero-waste initiative is gaining traction in Japan.
Companies are developing methods to recycle materials and reduce landfill waste.
For example, Canon has implemented recycling programs to reuse resources, while Nissan has set ambitious goals to recycle 100% of its end-of-life vehicles.
Case Studies of Innovation
Understanding the theoretical aspects of innovation is beneficial, but real-world examples offer practical insights.
Here are some adoption cases that highlight how these innovative practices are implemented.
Toyota’s Production System
Toyota’s commitment to innovation is evident in its production system, commonly known as TPS (Toyota Production System).
This world-renowned system incorporates JIT manufacturing and Kaizen principles.
Through continuous improvement, the company has been able to reduce waste and increase efficiency.
The implementation of kanban systems helps in managing inventories more effectively, ensuring that parts are available just in time for production.
Fujitsu’s Smart Factory
Fujitsu is another pioneer in adopting innovative practices.
The company’s smart factory initiative integrates AI and IoT to optimize manufacturing processes.
Real-time data collection allows for instant adjustments, ensuring high-quality outputs and minimizing downtimes.
By utilizing predictive maintenance, Fujitsu ensures that machines are always in optimal condition, preventing costly breakdowns.
Sony’s Sustainable Practices
Sony has made significant strides in incorporating sustainability into its manufacturing processes.
The company has set long-term goals to reduce its environmental impact through renewable energy and resource conservation.
Sony’s “Road to Zero” initiative aims for a zero environmental footprint by 2050.
By adopting energy-efficient technologies and recycling practices, Sony is setting a standard for sustainable manufacturing.
Challenges and Future Prospects
Despite the various innovations, Japanese manufacturing faces several challenges.
Global competition, aging populations, and fluctuating economic conditions are some of the hurdles that need to be overcome.
Maintaining Competitive Edge
To maintain its competitive edge, Japanese manufacturers must continue to innovate and adapt.
Investment in research and development is crucial.
Companies must also focus on upskilling their workforce to handle advanced technologies effectively.
Adapting to Demographic Changes
Japan’s aging population poses a significant challenge to the manufacturing sector.
With fewer young people entering the workforce, companies need to find ways to maintain productivity.
Automation and robotic solutions can help mitigate this issue, but they are not a complete substitute for human expertise and ingenuity.
Economic Fluctuations
Economic instability can impact the manufacturing sector significantly.
Companies must develop robust strategies to weather economic downturns.
Diversifying supply chains and adopting flexible manufacturing practices can provide some level of protection against market volatility.
The future of Japanese manufacturing looks promising, driven by a culture of innovation and a commitment to quality.
With the continued adoption of advanced technologies and sustainable practices, Japan is well-positioned to remain a global leader in manufacturing.
Through real-world examples and case studies, it becomes evident that Japanese manufacturers are not just participants in the industry but are often setting the standards for others to follow.
As the landscape continues to evolve, staying ahead of these trends will be crucial for ongoing success.
資料ダウンロード
QCD調達購買管理クラウド「newji」は、調達購買部門で必要なQCD管理全てを備えた、現場特化型兼クラウド型の今世紀最高の購買管理システムとなります。
ユーザー登録
調達購買業務の効率化だけでなく、システムを導入することで、コスト削減や製品・資材のステータス可視化のほか、属人化していた購買情報の共有化による内部不正防止や統制にも役立ちます。
NEWJI DX
製造業に特化したデジタルトランスフォーメーション(DX)の実現を目指す請負開発型のコンサルティングサービスです。AI、iPaaS、および先端の技術を駆使して、製造プロセスの効率化、業務効率化、チームワーク強化、コスト削減、品質向上を実現します。このサービスは、製造業の課題を深く理解し、それに対する最適なデジタルソリューションを提供することで、企業が持続的な成長とイノベーションを達成できるようサポートします。
オンライン講座
製造業、主に購買・調達部門にお勤めの方々に向けた情報を配信しております。
新任の方やベテランの方、管理職を対象とした幅広いコンテンツをご用意しております。
お問い合わせ
コストダウンが利益に直結する術だと理解していても、なかなか前に進めることができない状況。そんな時は、newjiのコストダウン自動化機能で大きく利益貢献しよう!
(Β版非公開)