- お役立ち記事
- Innovation in Product Development Through QFD: Challenges and Solutions in Manufacturing
月間76,176名の
製造業ご担当者様が閲覧しています*
*2025年3月31日現在のGoogle Analyticsのデータより
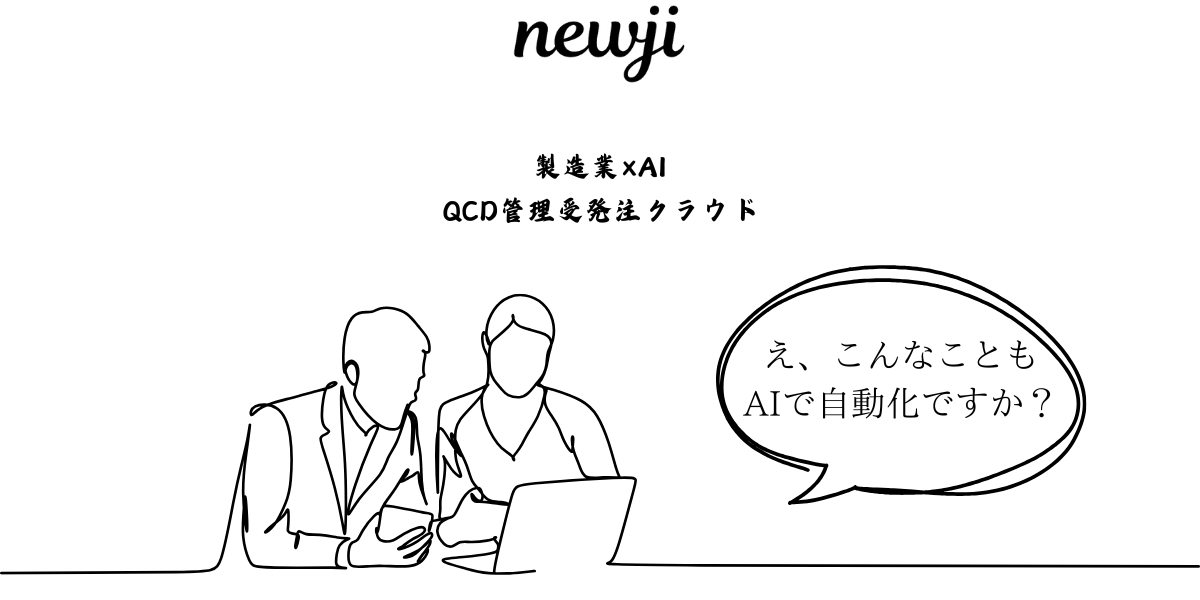
Innovation in Product Development Through QFD: Challenges and Solutions in Manufacturing
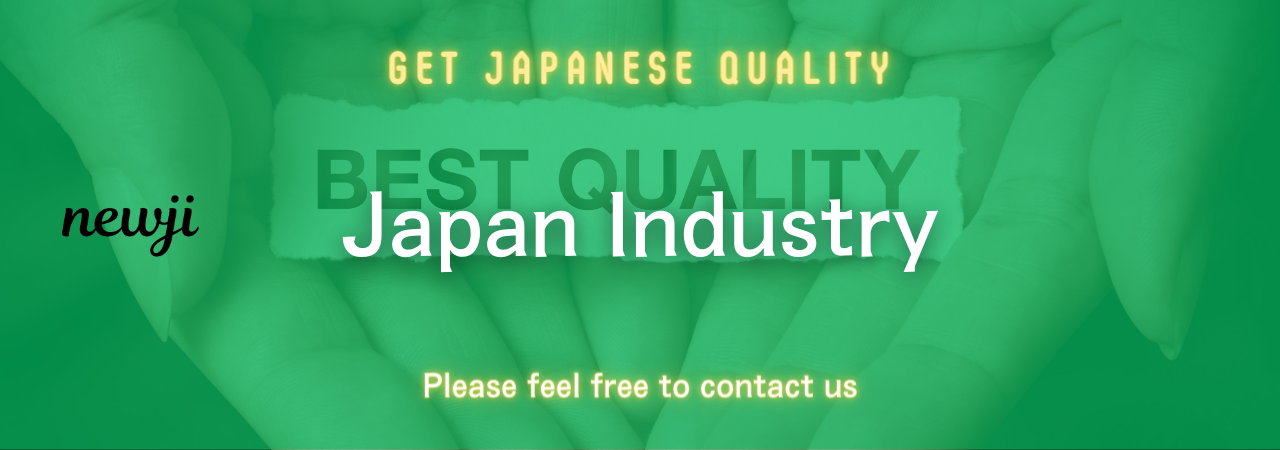
In today’s rapidly evolving market, innovation in product development is crucial for manufacturing companies to stay competitive.
One effective method for enhancing product development is Quality Function Deployment (QFD).
However, implementing QFD comes with its challenges.
In this article, we’ll explore what QFD is, its benefits, and the potential hurdles in its application, along with practical solutions to overcome them.
目次
Understanding Quality Function Deployment (QFD)
Quality Function Deployment, abbreviated as QFD, is a structured approach aimed at transforming customer needs into specific technical requirements.
It serves as a bridge between customer desires and the design process, ensuring the final product meets or even exceeds expectations.
The concept was first developed in Japan in the 1960s and has since been adopted globally.
It involves various tools, with the most prominent one being the House of Quality matrix.
This matrix helps map out customer requirements, comparing them against the capabilities of the company to deliver on those demands.
Steps Involved in QFD
1. **Identifying Customer Needs:** Understanding what the customer values and expects from the product.
2. **Technical Requirements:** Translating those needs into measurable technical specifications.
3. **Prioritization:** Prioritizing requirements based on customer importance and technical challenges.
4. **Evaluation:** Continuous evaluation and adjustment based on feedback throughout the development process.
Benefits of Implementing QFD
Adopting QFD offers several advantages that can significantly enhance the product development process.
One of the core benefits is the alignment between customer requirements and the final product.
This alignment results in higher customer satisfaction and loyalty.
Enhanced Communication
QFD promotes better communication among different departments within the company.
Since everyone works from the same set of guidelines, there’s less room for misunderstandings and errors.
This cross-functional teamwork ensures that all aspects of the product are considered and that everyone is on the same page.
Reduction in Development Time and Costs
By systematically addressing customer requirements early on, QFD helps in identifying potential issues that could cause delays.
This proactive approach ensures that problems are tackled before they escalate, thereby reducing both development time and costs.
Improved Quality
The structured nature of QFD ensures that every aspect of the product is scrutinized against the highest standards.
This results in an overall improvement in product quality, which can lead to better market performance.
Challenges in Implementing QFD
Despite its numerous benefits, QFD is not without challenges.
These hurdles can sometimes deter companies from fully adopting this powerful methodology.
Complexity and Time-Consuming
One of the significant challenges is the complexity of the QFD process.
The intricate nature of translating customer needs into technical requirements can be time-consuming.
The initial stages require considerable effort in data collection, analysis, and mapping.
User Resistance
Another challenge is resistance from employees.
Introducing QFD often requires a cultural shift within the organization.
Employees may be resistant to change, especially if they are accustomed to traditional methods.
This resistance can hamper the smooth implementation of QFD.
Resource Intensive
Implementing QFD is resource-intensive, requiring skilled personnel and advanced tools.
Smaller companies may find it challenging to allocate the necessary resources for a full-scale QFD implementation.
Solutions to Overcome QFD Challenges
While the challenges are significant, they are not insurmountable.
With the right strategies, companies can successfully implement QFD and reap its numerous benefits.
Training and Education
Investing in training and education is crucial for overcoming complexity and user resistance.
Providing employees with a thorough understanding of the QFD process can help ease the transition.
Workshops, seminars, and hands-on training sessions can equip the team with the required skills.
Pilot Projects
Starting with smaller pilot projects can be an effective way to familiarize the team with QFD.
These projects can serve as learning experiences, helping the team to understand the nuances of QFD without overwhelming them.
Successful pilot projects can build confidence and pave the way for larger implementations.
Utilizing Software Tools
Several software tools are available to simplify the QFD process.
These tools can aid in data collection, analysis, and visualization, making the process more efficient.
Investing in the right tools can significantly reduce the time and effort required for QFD.
Cross-Functional Teams
Forming cross-functional teams can help in addressing resource constraints and promoting better communication.
These teams can bring different perspectives to the table and ensure that all aspects of the product are considered.
Conclusion
Quality Function Deployment is a powerful tool that can drive innovation in product development.
While its implementation comes with challenges, they can be effectively managed with the right strategies.
Investing in training, starting with pilot projects, utilizing appropriate tools, and fostering cross-functional teams are some of the ways to overcome these hurdles.
By embracing QFD, manufacturing companies can ensure that their products not only meet but exceed customer expectations, paving the way for long-term success.
In an ever-competitive market, the ability to systematically align product development with customer needs is invaluable, making QFD an essential practice in modern manufacturing.
資料ダウンロード
QCD管理受発注クラウド「newji」は、受発注部門で必要なQCD管理全てを備えた、現場特化型兼クラウド型の今世紀最高の受発注管理システムとなります。
ユーザー登録
受発注業務の効率化だけでなく、システムを導入することで、コスト削減や製品・資材のステータス可視化のほか、属人化していた受発注情報の共有化による内部不正防止や統制にも役立ちます。
NEWJI DX
製造業に特化したデジタルトランスフォーメーション(DX)の実現を目指す請負開発型のコンサルティングサービスです。AI、iPaaS、および先端の技術を駆使して、製造プロセスの効率化、業務効率化、チームワーク強化、コスト削減、品質向上を実現します。このサービスは、製造業の課題を深く理解し、それに対する最適なデジタルソリューションを提供することで、企業が持続的な成長とイノベーションを達成できるようサポートします。
製造業ニュース解説
製造業、主に購買・調達部門にお勤めの方々に向けた情報を配信しております。
新任の方やベテランの方、管理職を対象とした幅広いコンテンツをご用意しております。
お問い合わせ
コストダウンが利益に直結する術だと理解していても、なかなか前に進めることができない状況。そんな時は、newjiのコストダウン自動化機能で大きく利益貢献しよう!
(β版非公開)