- お役立ち記事
- Innovation in stator molding using low-cost metal components
月間76,176名の
製造業ご担当者様が閲覧しています*
*2025年3月31日現在のGoogle Analyticsのデータより
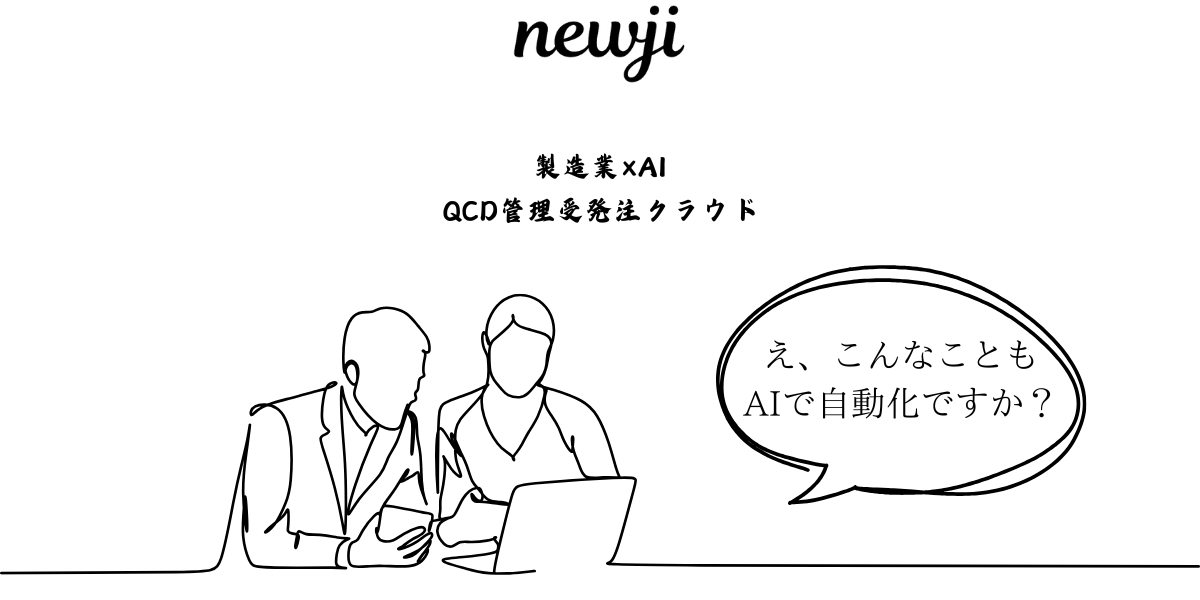
Innovation in stator molding using low-cost metal components
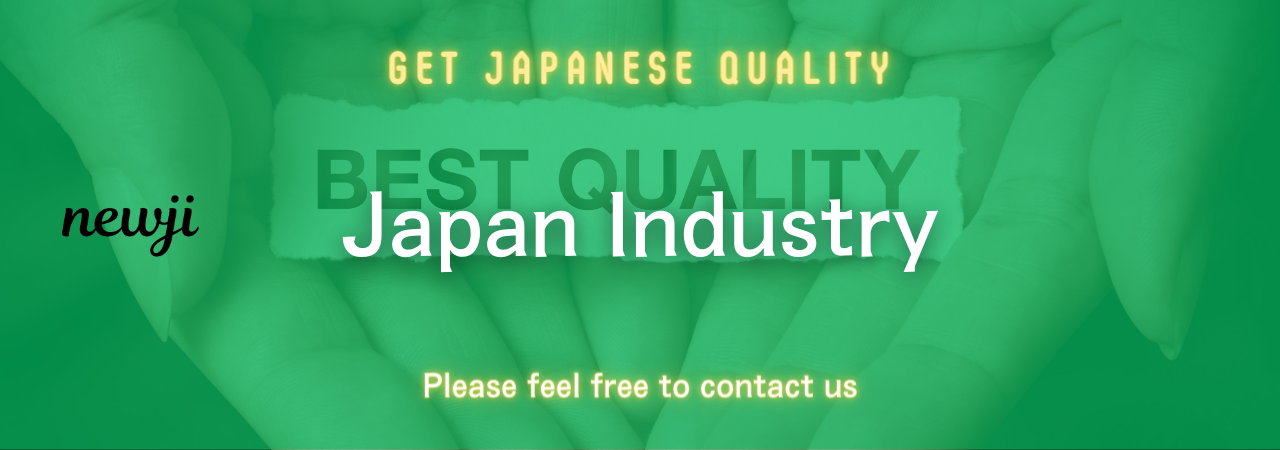
目次
Introduction to Stator Molding
Stator molding is an essential process in the production of electric motors and generators.
The stator acts as the stationary part of an electric machine and is crucial for its performance.
Over the years, innovations in this process have contributed significantly to improvements in efficiency and cost-effectiveness.
In recent times, an exciting development in stator molding has been the introduction of low-cost metal components.
This breakthrough is reshaping the industry by making high-quality motor production more affordable.
Why Metal Components Matter
Metal components are integral to stator molding for several reasons.
First, metals are naturally conductive, allowing electrical systems to operate efficiently.
By using metal, designers can create stators that minimize energy loss, which is crucial for effective motor function.
Second, metals provide strength and durability.
In an electric motor, the materials need to withstand mechanical stress and heat over time.
High-quality metal components ensure the longevity and reliability of the motor.
Lastly, metals allow for precise engineering.
In the world of electronics, small variations can lead to significant performance differences.
Metal components can be manufactured with high precision, ensuring a high level of performance in every unit produced.
Low-Cost Metal Components Impact
The innovation of using low-cost metal components in stator molding has broad implications.
One of the primary benefits is cost reduction.
Previously, the high cost of metals like copper made large-scale production expensive.
These new, affordable alternatives make it easier for manufacturers to maintain quality while reducing expenses.
In addition, access to low-cost metals democratizes technology.
Smaller companies and startups can enter the market without the high initial investment that traditional production methods required.
This fosters competition, leading to more innovation and better products for consumers.
Furthermore, low-cost components contribute to sustainability efforts.
As demand rises, there’s a need for eco-friendly solutions.
Less expensive metals often require less energy-intensive processes during production.
Thus, they reduce overall carbon emissions for each unit produced.
The Process of Stator Molding with Low-Cost Metals
The process of integrating low-cost metal components into stator molding begins with material selection.
Engineers need to find metals that maintain conductivity and strength but are available at a reduced cost.
Aluminum is a common candidate due to its affordability and favorable properties.
Once the material is chosen, it moves to the phase of design and prototyping.
In this stage, engineers use computer-aided design (CAD) software to create blueprints of the desired stator structure.
This step is crucial, as the design must take full advantage of the metal’s properties while meeting the specific performance requirements of the electric machine.
After design approval, the manufacturing process begins.
The metal is shaped using various molding techniques, such as die casting or stamping, depending on the required specifications.
This stage benefits from the metal’s inherent malleability, which allows for precision shaping and adherence to intricate designs.
Quality control is the next critical step.
Manufacturing errors can result in efficiency losses or even complete motor failure.
Therefore, rigorous testing is conducted to ensure each component meets the necessary standards.
Advanced technologies such as X-ray inspections and ultrasonic testing are employed to detect any sub-surface defects.
Finally, the stator is assembled into the electric motor.
Here, it aligns with other components to form a complete, functional machine.
This integration is carefully monitored to ensure compatibility and overall system performance.
Challenges and Considerations
Despite the advantages, there are challenges associated with adopting low-cost metal components in stator molding.
One primary concern is the potential compromise in quality.
While these materials are less expensive, they must not detract from the motor’s overall efficiency or durability.
Engineers need to conduct thorough research and testing to find metals that offer the best balance between cost savings and performance.
Another challenge is adapting existing manufacturing processes.
Shifting to new materials might require retooling and updating production lines.
This can be costly and time-consuming, but is necessary to maximize the benefits of low-cost metals.
Additionally, availability and consistency of supply for these metals can pose an issue.
Reliable suppliers are crucial for maintaining continuous production line capabilities and ensuring all products meet quality requirements.
The Future of Stator Molding
The future of stator molding looks promising with the integration of low-cost metal components.
As technology advances, we can expect further innovations that could improve metal properties, making them even more suitable for electric motor applications.
The ongoing research into alloys and composites is likely to yield new materials that blend affordability and performance seamlessly.
Moreover, enhanced recycling programs and resource management strategies can support the production of these metals sustainably.
Another area ripe for exploration is automation in the stator molding process.
Automated systems can increase precision and reduce human error.
Incorporating robotics and AI into production lines could optimize the manufacturing process for even greater efficiency.
Conclusion
Innovation in stator molding using low-cost metal components is transforming the electric motor industry.
By embracing affordable materials, manufacturers can produce reliable, efficient products while saving costs.
These developments promise a more sustainable and competitive future, encouraging advancements that benefit businesses and consumers alike.
As we continue to explore and refine these technologies, the potential to revolutionize the way electric motors are made becomes clearer.
Low-cost metals symbolize a significant step forward in making advanced technology accessible to all and ensuring it meets the needs of modern society.
資料ダウンロード
QCD管理受発注クラウド「newji」は、受発注部門で必要なQCD管理全てを備えた、現場特化型兼クラウド型の今世紀最高の受発注管理システムとなります。
ユーザー登録
受発注業務の効率化だけでなく、システムを導入することで、コスト削減や製品・資材のステータス可視化のほか、属人化していた受発注情報の共有化による内部不正防止や統制にも役立ちます。
NEWJI DX
製造業に特化したデジタルトランスフォーメーション(DX)の実現を目指す請負開発型のコンサルティングサービスです。AI、iPaaS、および先端の技術を駆使して、製造プロセスの効率化、業務効率化、チームワーク強化、コスト削減、品質向上を実現します。このサービスは、製造業の課題を深く理解し、それに対する最適なデジタルソリューションを提供することで、企業が持続的な成長とイノベーションを達成できるようサポートします。
製造業ニュース解説
製造業、主に購買・調達部門にお勤めの方々に向けた情報を配信しております。
新任の方やベテランの方、管理職を対象とした幅広いコンテンツをご用意しております。
お問い合わせ
コストダウンが利益に直結する術だと理解していても、なかなか前に進めることができない状況。そんな時は、newjiのコストダウン自動化機能で大きく利益貢献しよう!
(β版非公開)