- お役立ち記事
- Innovation Strategies for Differentiation in Forging Processing
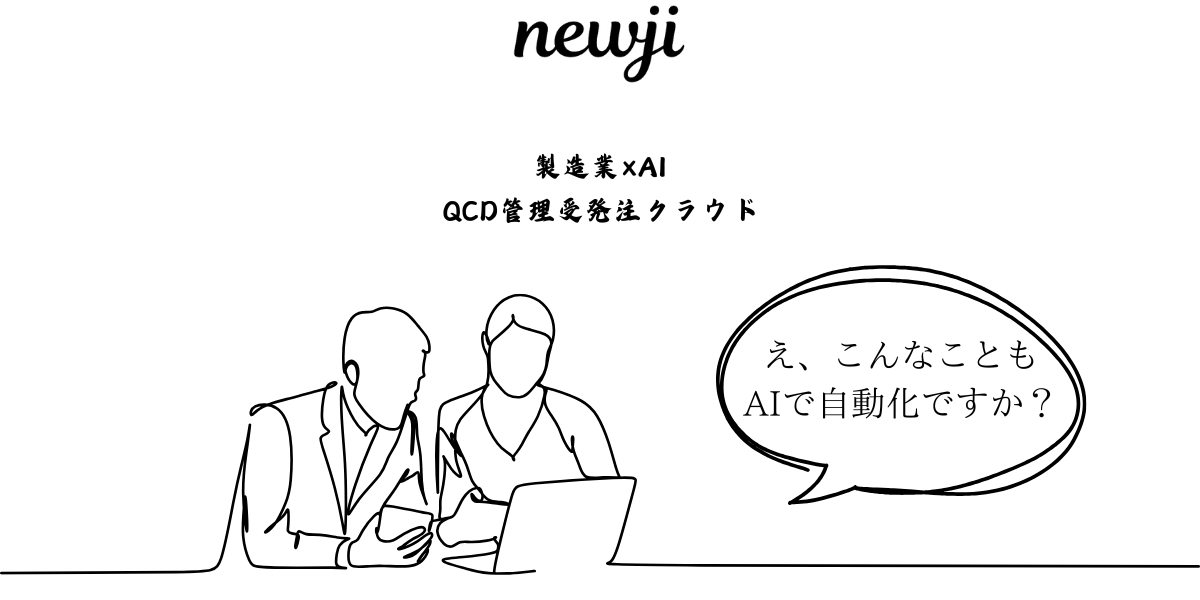
Innovation Strategies for Differentiation in Forging Processing
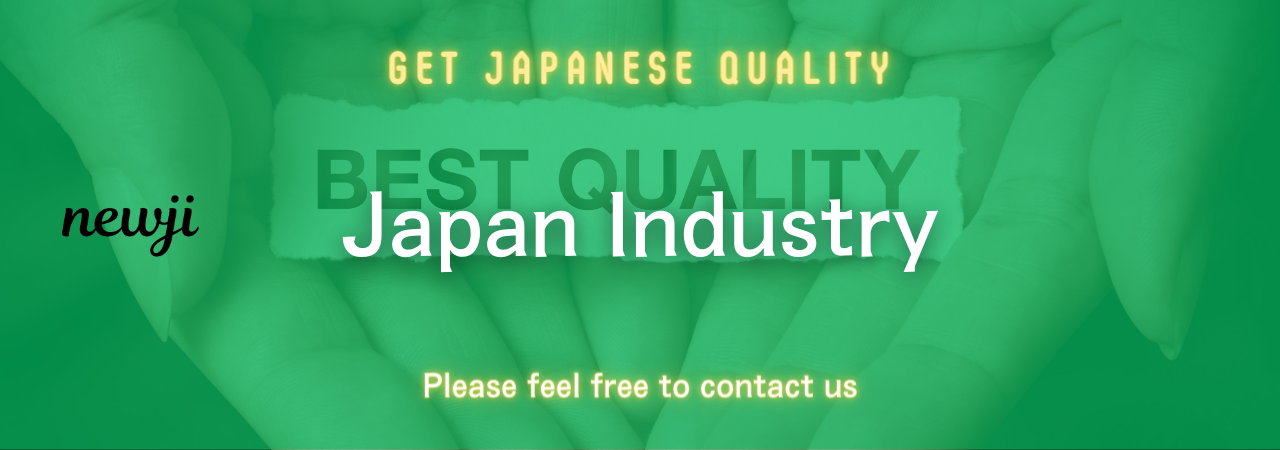
目次
Introduction to Forging Processing
Forging is a manufacturing process involving the shaping of metal using localized compressive forces.
It is one of the oldest known metalworking processes and is still widely used in various industries today, including automotive, aerospace, and construction.
Forging enhances the material properties and structural integrity of the metal, resulting in superior strength and reliability compared to other manufacturing processes.
The Need for Innovation in Forging
As industries evolve, the demand for higher quality, more complex, and customized metal components continues to rise.
Staying ahead of the curve requires constant innovation.
By implementing innovative strategies, companies can differentiate themselves from competitors and achieve operational excellence.
Innovation in forging is essential to meet these growing demands and improve overall efficiency.
Adopting Advanced Materials
High-Performance Alloys
One way to innovate in forging is by adopting high-performance alloys.
These materials offer enhanced mechanical properties, such as greater strength, corrosion resistance, and temperature stability.
By incorporating advanced alloy materials, companies can produce components that meet the stringent requirements of industries like aerospace and automotive.
Composite Materials
Another area of innovation involves the use of composite materials.
Composites combine metals with other materials, such as ceramics or polymers, to achieve properties not attainable with traditional alloys.
These materials can provide additional benefits, such as weight reduction, which is crucial for industries focused on fuel efficiency and performance.
Implementing Cutting-Edge Technologies
Automation and Robotics
Automation and robotics have revolutionized the manufacturing industry, including forging.
Implementing these technologies can significantly improve production speed, precision, and consistency.
Robotic systems can handle repetitive tasks, reducing human error and increasing safety.
Additionally, automation allows for continuous operation, maximizing production output.
Simulation and Modeling
Utilizing advanced simulation and modeling tools can optimize the forging process.
These tools allow engineers to simulate various forging scenarios and identify the most efficient production methods.
By leveraging these technologies, companies can reduce material waste, minimize production time, and produce higher-quality components.
Enhancing Process Efficiency
Lean Manufacturing
Implementing lean manufacturing principles is another effective innovation strategy.
Lean manufacturing focuses on minimizing waste and maximizing value.
By streamlining production processes, companies can reduce costs, improve efficiency, and increase customer satisfaction.
This approach ensures that resources are used more effectively and that production schedules are optimized.
Continuous Improvement
Continuous improvement initiatives, such as Six Sigma and Kaizen, promote a culture of ongoing innovation.
These methodologies emphasize the importance of identifying and addressing inefficiencies in the production process.
By encouraging employee involvement and regularly reviewing processes, companies can continuously enhance their forging operations.
Customization and Personalization
Customer-Specific Designs
Innovation in forging also involves offering customer-specific designs.
By collaborating closely with clients, companies can develop tailored solutions that meet unique requirements.
This customer-centric approach can lead to greater satisfaction and long-term partnerships.
Rapid Prototyping
Rapid prototyping technologies, such as 3D printing, enable quick and cost-effective production of prototypes.
These prototypes can be used to validate designs and make necessary adjustments before full-scale production.
Rapid prototyping accelerates the development process and ensures that final products meet exact specifications.
Investing in Workforce Development
Training and Education
A skilled workforce is essential for implementing and sustaining innovative forging processes.
Investing in employee training and education ensures that staff are knowledgeable about the latest technologies and methodologies.
Regular training programs can also enhance problem-solving skills and encourage creative thinking.
Fostering a Culture of Innovation
Creating a culture that values innovation is crucial for long-term success.
Encouraging employees to share ideas and take risks can lead to groundbreaking innovations.
By fostering an environment where creativity is rewarded, companies can maintain a competitive edge in the forging industry.
Collaborative Research and Development
Partnerships and Alliances
Forging companies can benefit from forming partnerships and alliances with research institutions, universities, and other industry players.
Collaborative research and development efforts can lead to the discovery of new materials, processes, and technologies.
Such collaborations can also provide access to specialized resources and expertise, accelerating innovation.
Industry Forums and Consortia
Participating in industry forums and consortia allows companies to stay informed about the latest trends and advancements in forging technology.
These platforms provide opportunities for networking, knowledge sharing, and collaborative problem-solving.
Engagement in such activities can inspire new ideas and foster innovation.
Sustainability and Environmental Responsibility
Eco-Friendly Materials
Sustainability is becoming increasingly important in manufacturing.
Using eco-friendly materials in forging processes can reduce environmental impact and appeal to environmentally-conscious customers.
Innovative materials, such as recycled metals or bio-based composites, can offer the necessary performance while minimizing carbon footprint.
Energy Efficiency
Improving energy efficiency in forging operations is another critical area of focus.
By optimizing energy usage, companies can reduce operational costs and greenhouse gas emissions.
Implementing energy-efficient technologies and practices, such as heat recovery systems and efficient heating methods, can significantly enhance sustainability.
Staying competitive in the forging industry requires a commitment to innovation.
By adopting advanced materials, implementing cutting-edge technologies, enhancing process efficiency, and fostering a culture of continuous improvement, companies can differentiate themselves.
Additionally, focusing on customization, investing in workforce development, promoting collaborative research, and prioritizing sustainability will position forging companies for long-term success.
資料ダウンロード
QCD調達購買管理クラウド「newji」は、調達購買部門で必要なQCD管理全てを備えた、現場特化型兼クラウド型の今世紀最高の購買管理システムとなります。
ユーザー登録
調達購買業務の効率化だけでなく、システムを導入することで、コスト削減や製品・資材のステータス可視化のほか、属人化していた購買情報の共有化による内部不正防止や統制にも役立ちます。
NEWJI DX
製造業に特化したデジタルトランスフォーメーション(DX)の実現を目指す請負開発型のコンサルティングサービスです。AI、iPaaS、および先端の技術を駆使して、製造プロセスの効率化、業務効率化、チームワーク強化、コスト削減、品質向上を実現します。このサービスは、製造業の課題を深く理解し、それに対する最適なデジタルソリューションを提供することで、企業が持続的な成長とイノベーションを達成できるようサポートします。
オンライン講座
製造業、主に購買・調達部門にお勤めの方々に向けた情報を配信しております。
新任の方やベテランの方、管理職を対象とした幅広いコンテンツをご用意しております。
お問い合わせ
コストダウンが利益に直結する術だと理解していても、なかなか前に進めることができない状況。そんな時は、newjiのコストダウン自動化機能で大きく利益貢献しよう!
(Β版非公開)