- お役立ち記事
- Innovations and Excellence: The Evolution of Japanese Manufacturing Industry
Innovations and Excellence: The Evolution of Japanese Manufacturing Industry
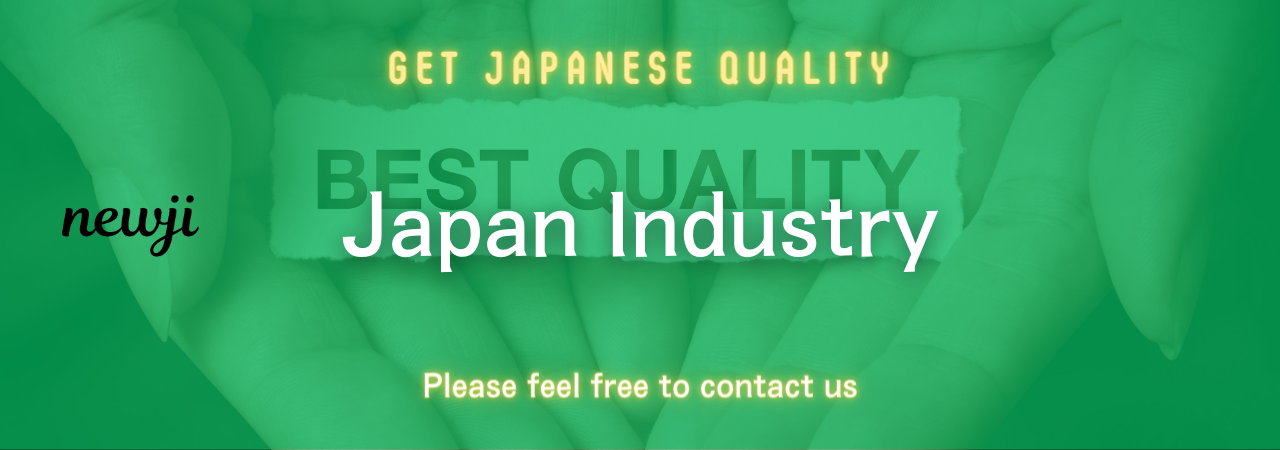
目次
Introduction to the Evolution of Japanese Manufacturing
The Japanese manufacturing industry has long been recognized as a global leader in quality, innovation, and efficiency.
Its evolution over the past several decades showcases a commitment to continuous improvement and technological advancement.
Japanese manufacturers have successfully navigated economic challenges, technological shifts, and changing global market dynamics.
This resilience and adaptability have solidified Japan’s position in the global manufacturing landscape.
Historical Context and Development
Post-World War II, Japan focused on rebuilding its economy, emphasizing manufacturing as a key driver of growth.
The adoption of lean manufacturing principles, notably the Toyota Production System, revolutionized production efficiency.
Japanese companies prioritized quality control, minimizing waste, and fostering a culture of continuous improvement, known as Kaizen.
These foundational strategies laid the groundwork for Japan’s manufacturing excellence.
Procurement and Purchasing in Japanese Manufacturing
Procurement and purchasing are critical components of the Japanese manufacturing process.
Japanese companies emphasize building strong relationships with suppliers to ensure quality and reliability.
This collaborative approach fosters mutual trust and long-term partnerships, essential for maintaining manufacturing standards.
Advantages of Japanese Procurement Practices
Japanese procurement practices offer several advantages:
They ensure high-quality materials and components, which are vital for superior product performance.
Long-term supplier relationships lead to better pricing and more reliable delivery schedules.
Collaborative problem-solving with suppliers enhances innovation and process improvements.
Disadvantages of Japanese Procurement Practices
However, there are also challenges:
The focus on long-term relationships may limit flexibility in sourcing from new or diverse suppliers.
Cultural differences can pose barriers in international procurement scenarios.
High expectations for quality and performance can increase pressure on suppliers and manufacturers alike.
Supplier Negotiation Techniques
Effective supplier negotiation is a cornerstone of Japanese manufacturing success.
Japanese negotiators employ a blend of respect, patience, and strategic planning to achieve favorable outcomes.
Building Trust and Long-Term Relationships
Trust is paramount in supplier negotiations.
Japanese companies invest time in understanding their suppliers’ capabilities and constraints.
This mutual understanding fosters a partnership mentality rather than a transactional relationship.
Emphasizing Mutual Benefits
Negotiations focus on creating win-win scenarios.
Both parties seek to benefit from the agreement, ensuring sustainability and long-term collaboration.
This approach minimizes conflicts and promotes continuous cooperation.
Attention to Detail and Clear Communication
Japanese negotiators pay meticulous attention to details, ensuring all aspects of the agreement are clearly understood.
Clear and precise communication helps prevent misunderstandings and ensures alignment of expectations.
Market Conditions and Their Impact
The global market conditions significantly influence Japanese manufacturing strategies.
Economic fluctuations, trade policies, and technological advancements shape how Japanese manufacturers operate.
Globalization and Supply Chain Management
Globalization has expanded the reach of Japanese manufacturers, allowing access to diverse markets and resources.
Effective supply chain management is crucial to handle the complexities of international operations.
Japanese companies leverage their strong supplier networks to maintain efficiency and responsiveness in global markets.
Technological Advancements
Advancements in technology have driven innovation in Japanese manufacturing.
Automation, robotics, and Industry 4.0 technologies enhance production capabilities and efficiency.
Japanese manufacturers continuously invest in new technologies to stay competitive and meet evolving market demands.
Best Practices in Japanese Manufacturing
Japanese manufacturing incorporates several best practices that contribute to its excellence and innovation.
Lean Manufacturing and Waste Reduction
Lean manufacturing principles focus on eliminating waste and optimizing processes.
By streamlining operations, Japanese manufacturers achieve higher efficiency and lower costs.
This approach also enhances product quality and customer satisfaction.
Continuous Improvement (Kaizen)
Kaizen, or continuous improvement, is ingrained in the Japanese manufacturing culture.
Employees at all levels are encouraged to identify and implement improvements in their work processes.
This collective effort leads to incremental gains that accumulate over time, driving overall excellence.
Quality Control and Assurance
Stringent quality control measures ensure that products meet high standards.
Japanese manufacturers employ comprehensive quality assurance systems to detect and address defects early in the production process.
This commitment to quality minimizes errors, reduces costs, and enhances customer trust.
Challenges and Adaptations
Despite its strengths, the Japanese manufacturing industry faces several challenges that require strategic adaptations.
Aging Workforce
Japan’s aging population poses a challenge to the manufacturing sector.
A shrinking workforce can impact productivity and innovation.
To address this, Japanese manufacturers are investing in automation and workforce training programs to maintain their competitive edge.
Global Competition
Increasing competition from other manufacturing hubs, such as China and Southeast Asia, pressures Japanese companies to innovate and reduce costs.
Maintaining quality while optimizing expenses is crucial for sustaining market leadership.
Environmental Sustainability
Environmental regulations and the demand for sustainable practices are shaping manufacturing strategies.
Japanese manufacturers are adopting green technologies and sustainable practices to minimize their environmental footprint and meet regulatory requirements.
Future Outlook
The future of Japanese manufacturing looks promising, driven by innovation and adaptability.
Embracing Industry 4.0
Japanese manufacturers are at the forefront of integrating Industry 4.0 technologies, such as the Internet of Things (IoT), artificial intelligence (AI), and big data analytics.
These technologies enhance operational efficiency, enable predictive maintenance, and improve decision-making processes.
Focus on Innovation
Continued investment in research and development ensures that Japanese manufacturers stay ahead in technology and product innovation.
Collaborations with startups and research institutions foster a culture of creativity and technological advancement.
Global Expansion and Diversification
Expanding into emerging markets and diversifying product portfolios help Japanese manufacturers mitigate risks and capitalize on new opportunities.
Strategic acquisitions and partnerships enable access to new technologies and markets, strengthening global presence.
Best Practices for International Procurement from Japan
Leveraging Japanese manufacturing excellence in international procurement requires adopting best practices tailored to cross-cultural and global contexts.
Understanding Cultural Nuances
Cultural understanding is essential for successful procurement from Japanese suppliers.
Respect for hierarchy, attention to detail, and indirect communication are key aspects to consider.
Building personal relationships and demonstrating commitment can enhance collaboration and trust.
Establishing Clear Contracts and Agreements
Clear and comprehensive contracts help prevent misunderstandings and ensure mutual expectations are met.
Contracts should outline quality standards, delivery schedules, pricing, and dispute resolution mechanisms.
Implementing Effective Communication Channels
Maintaining open and consistent communication channels facilitates smooth procurement processes.
Regular updates, feedback sessions, and collaborative problem-solving approaches enhance efficiency and responsiveness.
Investing in Supplier Development
Supporting supplier development initiatives can lead to improved quality and innovation.
Providing training, sharing best practices, and collaborating on process improvements strengthen the supplier relationship and enhance overall value.
Conclusion
The evolution of the Japanese manufacturing industry is a testament to its unwavering commitment to quality, innovation, and efficiency.
From its historical roots in post-war reconstruction to its current leadership in advanced manufacturing technologies, Japan continues to set global standards.
Effective procurement and purchasing strategies, characterized by strong supplier relationships, meticulous negotiation techniques, and a focus on continuous improvement, play a pivotal role in this success.
As the industry faces future challenges, including an aging workforce and increasing global competition, its ability to adapt and innovate will determine its ongoing prominence on the world stage.
Adopting Japanese best practices in international procurement can offer significant benefits, enhancing quality, efficiency, and competitiveness for manufacturing companies worldwide.
資料ダウンロード
QCD調達購買管理クラウド「newji」は、調達購買部門で必要なQCD管理全てを備えた、現場特化型兼クラウド型の今世紀最高の購買管理システムとなります。
ユーザー登録
調達購買業務の効率化だけでなく、システムを導入することで、コスト削減や製品・資材のステータス可視化のほか、属人化していた購買情報の共有化による内部不正防止や統制にも役立ちます。
NEWJI DX
製造業に特化したデジタルトランスフォーメーション(DX)の実現を目指す請負開発型のコンサルティングサービスです。AI、iPaaS、および先端の技術を駆使して、製造プロセスの効率化、業務効率化、チームワーク強化、コスト削減、品質向上を実現します。このサービスは、製造業の課題を深く理解し、それに対する最適なデジタルソリューションを提供することで、企業が持続的な成長とイノベーションを達成できるようサポートします。
オンライン講座
製造業、主に購買・調達部門にお勤めの方々に向けた情報を配信しております。
新任の方やベテランの方、管理職を対象とした幅広いコンテンツをご用意しております。
お問い合わせ
コストダウンが利益に直結する術だと理解していても、なかなか前に進めることができない状況。そんな時は、newjiのコストダウン自動化機能で大きく利益貢献しよう!
(Β版非公開)