- お役立ち記事
- Innovations in Blow Molding: Implementation and Results in Small Factories
月間77,185名の
製造業ご担当者様が閲覧しています*
*2025年2月28日現在のGoogle Analyticsのデータより
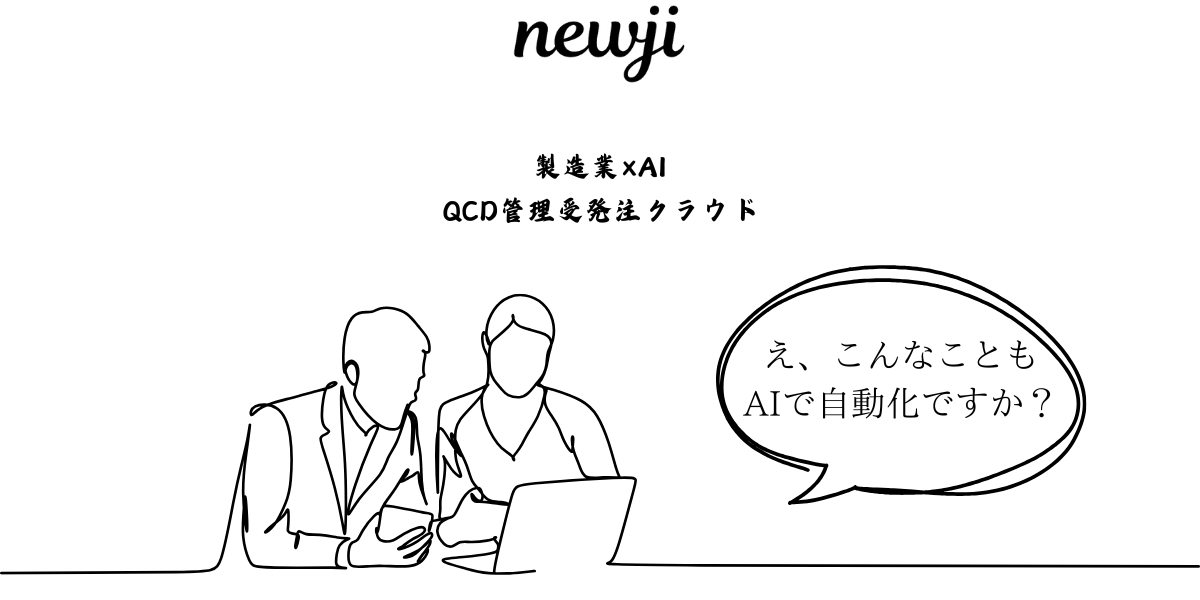
Innovations in Blow Molding: Implementation and Results in Small Factories
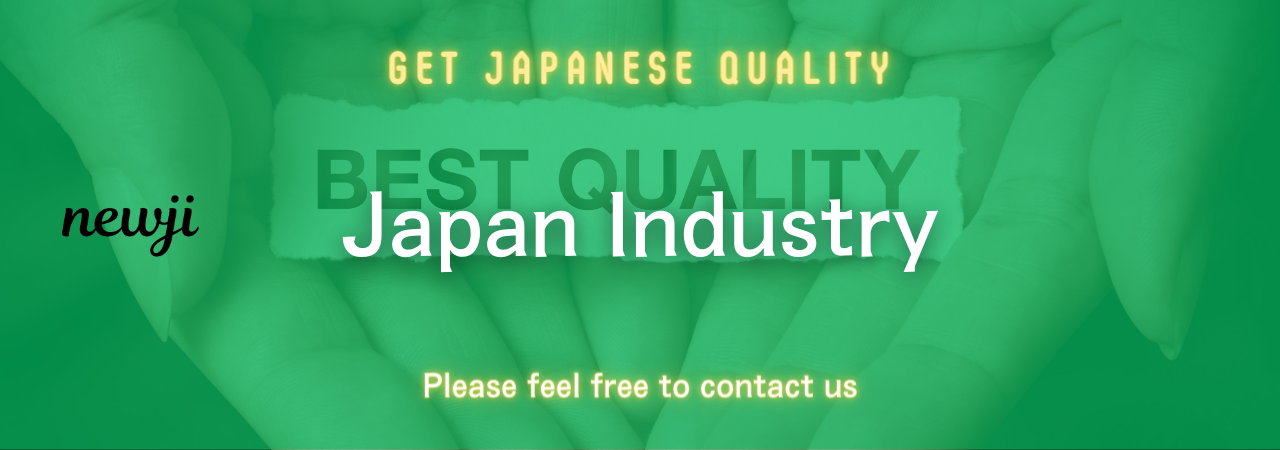
Blow molding has evolved significantly since its inception, offering numerous benefits for the manufacturing industry.
Small factories, in particular, are beginning to explore innovative techniques in blow molding to enhance production, reduce costs, and improve the quality of their products.
Understanding these advancements and their practical applications can be vital for small factories aiming to stay competitive in a constantly evolving market.
目次
Understanding Blow Molding
Blow molding is a manufacturing process used to create hollow plastic parts.
It involves heating plastic until it becomes molten, then inflating it into the desired shape using a mold.
This technique is widely used for producing containers such as bottles, jugs, and other hollow forms.
Types of Blow Molding
There are three primary types of blow molding: extrusion blow molding, injection blow molding, and stretch blow molding.
Each type has unique advantages and specific applications.
**Extrusion Blow Molding**: In this method, melted plastic is extruded into a tube-like shape, known as a parison.
The parison is then clamped into a mold and inflated.
This method is commonly used for making larger containers such as fuel tanks and milk jugs.
**Injection Blow Molding**: With this technique, plastic is first injected into a pre-shaped mold to create a preform.
The preform is later placed into a blow mold and inflated.
This process is ideal for small bottles and containers requiring high precision.
**Stretch Blow Molding**: This type combines aspects of injection and blow molding.
A preform is created and then stretched and blown into the mold.
This method is highly effective for producing beverage bottles, offering excellent clarity and durability.
Innovations in Blow Molding
Recent advancements in blow molding technology are paving the way for high efficiency and better product quality.
Small factories can particularly benefit from these innovations by incorporating them into their manufacturing processes.
Automation and Robotics
Automation has become a game-changer in blow molding.
Integrating robots and automated systems greatly enhances precision and consistency while reducing human error.
Small factories that adopt automation can experience increased production rates and cost savings.
Additionally, automation helps in quality control, ensuring each product meets stringent standards.
Material Advancements
New materials compatible with blow molding are being developed, offering enhanced strength, flexibility, and environmental benefits.
Biodegradable plastics and composites are gaining popularity, addressing the growing demand for sustainable manufacturing practices.
Small factories can leverage these materials to produce eco-friendly products, catering to environmentally conscious consumers.
Improved Mold Design
Innovative mold designs significantly impact the quality and efficiency of blow molding.
Advanced mold materials improve heat distribution and durability, reducing cycle times and wear and tear.
Furthermore, 3D printing technology allows for rapid prototyping and creation of complex mold designs that were previously unattainable.
Small factories can take advantage of this technology to speed up product development and reduce costs.
Implementation in Small Factories
Incorporating these innovations requires strategic planning and investment.
Small factories need to assess their current capabilities and identify areas for improvement.
Assessing Production Needs
Before implementing new blow molding technologies, small factories should conduct a thorough analysis of their production needs.
This includes evaluating product specifications, production volumes, and existing equipment.
Understanding these factors helps in selecting the appropriate innovations that align with their business objectives.
Investing in Training
Training employees is crucial when adopting new technologies.
Small factories should invest in comprehensive training programs to ensure their workforce can efficiently use automated systems and new materials.
This not only improves production efficiency but also fosters a culture of continuous learning and innovation.
Collaborating with Experts
Seeking guidance from experts in blow molding technology can provide valuable insights.
Collaborating with suppliers, technology providers, and industry consultants can pave the way for successful implementation.
These experts can assist with selecting the right equipment, optimizing production processes, and ensuring a smooth transition.
Results and Benefits
Implementing innovative blow molding solutions offers numerous benefits for small factories.
These range from cost savings to improved product quality and environmental sustainability.
Cost Reduction
Automation and improved mold designs can significantly reduce production costs.
Enhanced efficiency leads to lower energy consumption and minimized waste.
Additionally, the ability to quickly prototype and test new designs saves time and resources in product development.
Quality Enhancement
Higher precision and consistency in blow molding result in superior product quality.
Automated systems ensure uniformity and reduce defects, leading to better customer satisfaction.
Moreover, advanced materials and mold designs contribute to the overall durability and aesthetics of the products.
Environmental Impact
Using biodegradable and sustainable materials in blow molding addresses environmental concerns.
Small factories can market their eco-friendly products, appealing to a broader audience of environmentally conscious consumers.
Furthermore, reducing waste through efficient production processes also contributes to a smaller carbon footprint.
Conclusion
Innovations in blow molding technology present significant opportunities for small factories.
From automation and advanced materials to improved mold designs, these advancements can drive efficiency, reduce costs, and enhance product quality.
By strategically implementing these technologies and investing in employee training, small factories can position themselves for long-term success in a competitive market.
資料ダウンロード
QCD管理受発注クラウド「newji」は、受発注部門で必要なQCD管理全てを備えた、現場特化型兼クラウド型の今世紀最高の受発注管理システムとなります。
ユーザー登録
受発注業務の効率化だけでなく、システムを導入することで、コスト削減や製品・資材のステータス可視化のほか、属人化していた受発注情報の共有化による内部不正防止や統制にも役立ちます。
NEWJI DX
製造業に特化したデジタルトランスフォーメーション(DX)の実現を目指す請負開発型のコンサルティングサービスです。AI、iPaaS、および先端の技術を駆使して、製造プロセスの効率化、業務効率化、チームワーク強化、コスト削減、品質向上を実現します。このサービスは、製造業の課題を深く理解し、それに対する最適なデジタルソリューションを提供することで、企業が持続的な成長とイノベーションを達成できるようサポートします。
製造業ニュース解説
製造業、主に購買・調達部門にお勤めの方々に向けた情報を配信しております。
新任の方やベテランの方、管理職を対象とした幅広いコンテンツをご用意しております。
お問い合わせ
コストダウンが利益に直結する術だと理解していても、なかなか前に進めることができない状況。そんな時は、newjiのコストダウン自動化機能で大きく利益貢献しよう!
(β版非公開)