- お役立ち記事
- Innovative Energy Technology Proposal: Strategies to Reduce Environmental Impact for Manufacturing Sales
Innovative Energy Technology Proposal: Strategies to Reduce Environmental Impact for Manufacturing Sales
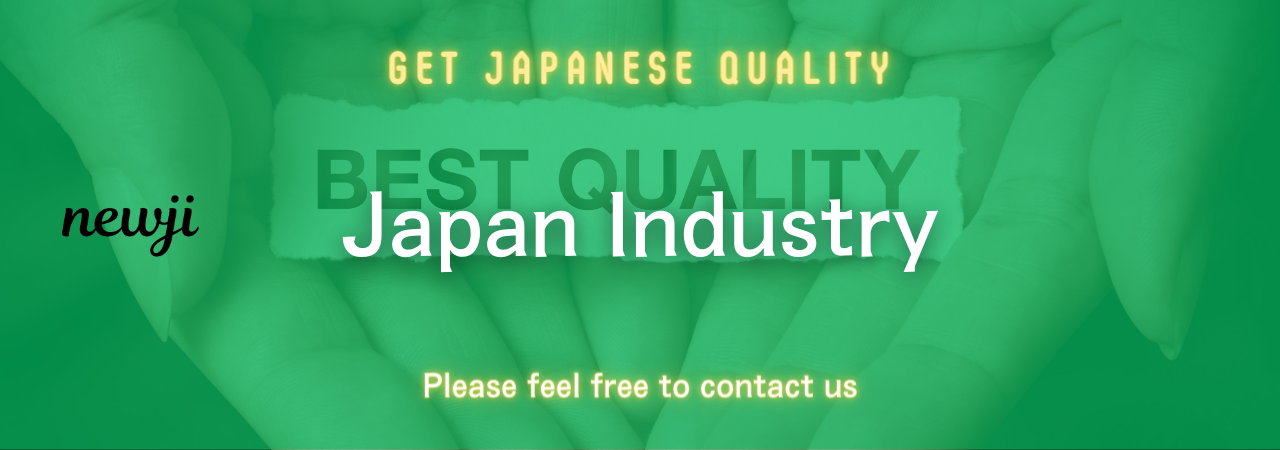
The manufacturing sector has always been a cornerstone of economic growth and technological development.
However, it also stands as one of the leading contributors to environmental degradation.
Given the increasing global focus on sustainability, there is an urgent need to explore innovative energy technologies that can significantly reduce the environmental impact of manufacturing operations.
This article will dive into various strategies that can be adopted by manufacturing and sales companies to mitigate their environmental footprint.
目次
Understanding the Environmental Impact of Manufacturing
Today’s world is characterized by an ever-growing demand for goods, placing immense pressure on manufacturing processes.
From raw material extraction to product disposal, every stage of manufacturing has its own set of environmental challenges.
Greenhouse gas emissions, water pollution, and resource depletion are some of the major issues.
Being energy-intensive, traditional manufacturing practices rely heavily on fossil fuels, contributing to carbon footprints and climate change.
Understanding these impacts is crucial for crafting effective solutions.
Shifting to Renewable Energy Sources
One of the most significant ways to reduce environmental impact is by transitioning to renewable energy sources.
Replacing fossil fuels with alternatives like solar, wind, and hydroelectric power can lead to substantial reductions in greenhouse gas emissions.
Solar Power
Solar energy is increasingly becoming a viable option for manufacturing units.
Photovoltaic panels can be installed on facility rooftops to harness sunlight and convert it into electricity.
Moreover, advancements in technology are making solar energy more efficient and cost-effective.
Wind Energy
Wind turbines can generate substantial amounts of electricity without emitting greenhouse gases.
Manufacturing plants located in windy areas can invest in wind farms to meet their energy requirements.
This not only reduces dependence on fossil fuels but also helps in achieving energy security.
Energy Efficiency Improvements
Improving energy efficiency within manufacturing processes is another critical strategy.
Older equipment often consumes more energy and operates less efficiently, leading to higher operational costs and a larger carbon footprint.
Upgrading Machinery
Investing in modern, energy-efficient machinery can result in considerable energy savings.
Many of the latest models come with energy management systems and automated controls that optimize energy usage.
Implementing Smart Manufacturing
The integration of Internet of Things (IoT) with manufacturing processes can lead to ‘smart manufacturing’.
By using sensors and data analytics, companies can monitor energy usage in real-time and make data-driven adjustments.
This helps in minimizing energy wastage and enhancing overall efficiency.
Adopting Green Building Practices
The facilities housing manufacturing units play a significant role in overall energy consumption.
Implementing green building practices can lead to substantial environmental benefits.
LEED Certification
Pursuing Leadership in Energy and Environmental Design (LEED) certification can be an excellent step.
LEED-certified buildings adhere to stringent guidelines for energy efficiency, water conservation, and indoor environmental quality.
This not only helps in reducing operational costs but also boosts brand image as an environmentally responsible entity.
Energy-Efficient Lighting and HVAC Systems
Replacing traditional lighting with energy-efficient LED lights can result in drastic electricity savings.
Similarly, upgrading HVAC systems to more efficient models ensures better energy management, leading to reductions in overall energy consumption.
Efficient Waste Management Systems
Manufacturing operations generate significant amounts of waste.
Efficient waste management systems can drastically reduce the environmental impact.
Recycling and Reusing Materials
Implementing a robust recycling program can divert substantial waste from landfills.
Materials like metals, plastics, and paper can be recycled and reused in the manufacturing process.
This not only helps in reducing raw material costs but also minimizes environmental degradation.
Implementing Zero-Waste Policies
Zero-waste policies focus on designing and managing products and processes to systematically avoid and eliminate the volume and toxicity of waste and materials.
These policies can lead to considerable reductions in waste, thereby reducing the environmental footprint of manufacturing activities.
Water Conservation Techniques
Water is an essential resource in many manufacturing processes.
With increasing global water scarcity, adopting water conservation techniques is imperative.
Water Recycling Systems
Implementing water recycling systems can significantly reduce water consumption.
These systems treat and reuse wastewater, making the process more sustainable.
Rainwater Harvesting
Rainwater harvesting can provide a sustainable water source for various non-potable needs within a manufacturing unit.
This reduces dependence on municipal water supplies and helps in conserving valuable water resources.
Employee Training and Engagement
Employees play a crucial role in implementing and sustaining energy-efficient practices.
Training and engaging staff in energy conservation measures can yield substantial benefits.
Energy Awareness Programs
Conducting regular workshops and training sessions can keep employees informed about the latest energy-saving techniques and technologies.
An informed workforce is more likely to adopt and support sustainable practices.
Incentivizing Green Practices
Offering incentives for employees who actively participate in energy conservation initiatives can foster a culture of sustainability.
This can range from financial rewards to public recognition and certifications.
Collaboration and Partnerships
Collaborating with other businesses, government bodies, and non-governmental organizations can amplify efforts in reducing environmental impact.
Partnerships can lead to the sharing of best practices, resources, and technologies.
Industry Alliances
Forming alliances within the industry can foster a collective effort towards sustainability.
This can include sharing research, co-developing new technologies, and jointly investing in renewable energy projects.
Government Programs
Participating in government programs that promote energy efficiency and sustainability can provide financial benefits.
Grants, tax incentives, and subsidies can make the adoption of innovative technologies more economically feasible.
In conclusion, reducing the environmental impact of manufacturing and sales requires a multi-faceted approach.
From adopting renewable energy sources to implementing efficient waste management systems, every step counts.
By leveraging innovative energy technologies and fostering a culture of sustainability, the manufacturing sector can significantly mitigate its environmental footprint.
Ultimately, these strategies not only contribute towards a healthier planet but also enhance operational efficiencies, leading to long-term economic benefits.
資料ダウンロード
QCD調達購買管理クラウド「newji」は、調達購買部門で必要なQCD管理全てを備えた、現場特化型兼クラウド型の今世紀最高の購買管理システムとなります。
ユーザー登録
調達購買業務の効率化だけでなく、システムを導入することで、コスト削減や製品・資材のステータス可視化のほか、属人化していた購買情報の共有化による内部不正防止や統制にも役立ちます。
NEWJI DX
製造業に特化したデジタルトランスフォーメーション(DX)の実現を目指す請負開発型のコンサルティングサービスです。AI、iPaaS、および先端の技術を駆使して、製造プロセスの効率化、業務効率化、チームワーク強化、コスト削減、品質向上を実現します。このサービスは、製造業の課題を深く理解し、それに対する最適なデジタルソリューションを提供することで、企業が持続的な成長とイノベーションを達成できるようサポートします。
オンライン講座
製造業、主に購買・調達部門にお勤めの方々に向けた情報を配信しております。
新任の方やベテランの方、管理職を対象とした幅広いコンテンツをご用意しております。
お問い合わせ
コストダウンが利益に直結する術だと理解していても、なかなか前に進めることができない状況。そんな時は、newjiのコストダウン自動化機能で大きく利益貢献しよう!
(Β版非公開)