- お役立ち記事
- Innovative Insights: Exploring the Evolution of Japanese Manufacturing Techniques
月間77,185名の
製造業ご担当者様が閲覧しています*
*2025年2月28日現在のGoogle Analyticsのデータより
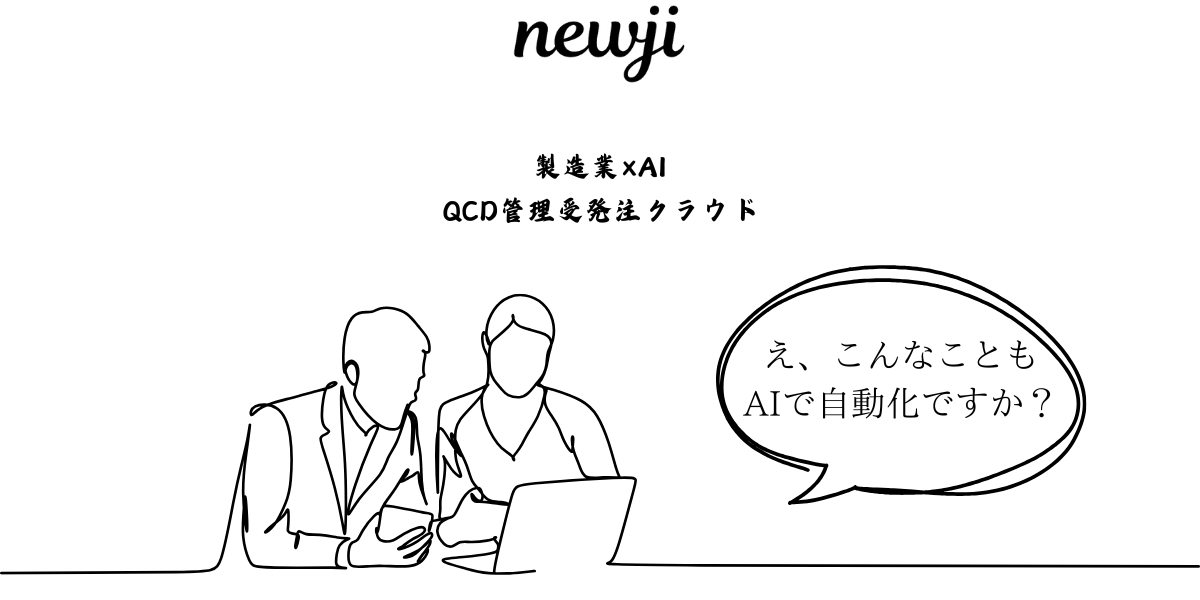
Innovative Insights: Exploring the Evolution of Japanese Manufacturing Techniques
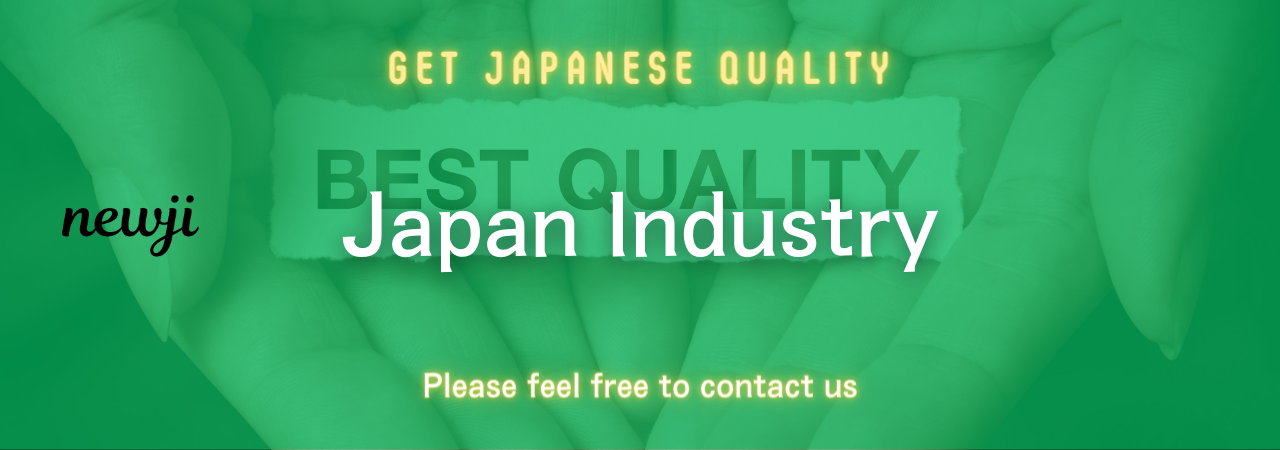
目次
Introduction
Japanese manufacturing has long been synonymous with quality, precision, and innovation.
The evolution of Japanese manufacturing techniques offers valuable lessons for global industries.
This article explores the development of these techniques and their impact on procurement and purchasing.
It delves into the advantages and disadvantages of Japanese manufacturing.
Additionally, it provides insights into supplier negotiation techniques, market conditions, and best practices.
Understanding these elements is crucial for businesses looking to benefit from Japanese manufacturing prowess.
The insights shared are based on extensive experience in international procurement and purchasing.
They aim to equip professionals with the knowledge to navigate the complexities of sourcing from Japan.
Ultimately, leveraging Japanese manufacturing techniques can lead to enhanced quality and efficiency.
However, it requires a nuanced approach to procurement and supplier relationship management.
The following sections provide a comprehensive analysis of these aspects.
The Evolution of Japanese Manufacturing Techniques
Historical Perspective
Japanese manufacturing techniques have their roots in traditional craftsmanship.
The concept of “monozukuri,” meaning the spirit of craftsmanship, has been integral to Japanese industries.
Post-World War II, Japan focused on rebuilding its manufacturing sector with a strong emphasis on quality and efficiency.
The introduction of Total Quality Management (TQM) revolutionized production processes.
Kaizen, or continuous improvement, became a cornerstone of Japanese manufacturing.
These principles fostered a culture of meticulous attention to detail and relentless pursuit of excellence.
Over the decades, Japanese companies like Toyota and Sony became global leaders.
Their success was driven by innovative manufacturing techniques and strategic procurement practices.
The historical commitment to quality laid the foundation for modern advancements in Japanese manufacturing.
Understanding this evolution is key to appreciating the sophistication of current manufacturing practices.
Modern Innovations
In recent years, Japanese manufacturing has embraced advanced technologies.
Automation and robotics have transformed production lines, enhancing precision and efficiency.
Industry 4.0 technologies, including the Internet of Things (IoT) and artificial intelligence (AI), are being integrated.
These innovations enable real-time monitoring and predictive maintenance.
Smart factories are becoming prevalent, where machines communicate and optimize operations autonomously.
Additive manufacturing, or 3D printing, is increasingly used for prototyping and small-scale production.
Sustainable practices are also gaining traction, with a focus on reducing waste and energy consumption.
Japanese manufacturers are leading the way in green manufacturing initiatives.
Moreover, the emphasis on digital transformation is paving the path for future advancements.
These modern innovations not only improve productivity but also enhance the flexibility of manufacturing systems.
Advantages of Japanese Manufacturing Techniques
One of the primary advantages is the unwavering focus on quality.
Japanese manufacturing emphasizes defect prevention rather than defect detection.
This approach ensures that products meet high standards consistently.
The implementation of Kaizen fosters a culture of continuous improvement.
This leads to incremental enhancements in processes and products over time.
Another advantage is the efficiency gained through lean manufacturing principles.
By eliminating waste and optimizing workflows, Japanese manufacturers achieve higher productivity.
Strong supplier relationships are also a significant benefit.
Collaborative partnerships with suppliers result in better material quality and reliable supply chains.
The integration of advanced technologies enhances precision and operational efficiency.
Moreover, the workforce is highly skilled and committed to excellence.
This combination of factors contributes to the overall competitiveness of Japanese manufacturing.
Businesses that adopt these techniques can expect improved product quality and operational performance.
Disadvantages of Japanese Manufacturing Techniques
Despite the numerous advantages, there are some drawbacks to consider.
One challenge is the high initial investment required for advanced technologies.
Implementing automation and Industry 4.0 solutions can be capital-intensive.
Additionally, the emphasis on continuous improvement may lead to incremental rather than radical innovations.
This can sometimes hinder breakthrough advancements.
Japanese manufacturing also tends to have longer lead times due to meticulous quality checks.
While this ensures product excellence, it may affect responsiveness to market changes.
Cultural differences can pose challenges in international procurement and supplier negotiations.
Language barriers and varying business practices may complicate collaborations.
Furthermore, the reliance on a highly skilled workforce may limit scalability.
Companies need to invest significantly in training and development to maintain expertise.
Understanding these disadvantages is essential for businesses to mitigate potential risks when engaging with Japanese manufacturers.
Procurement and Purchasing from Japanese Suppliers
Engaging with Japanese suppliers requires a strategic approach to procurement and purchasing.
Building strong relationships is fundamental to successful collaborations.
Cultural understanding plays a crucial role in fostering trust and mutual respect.
A thorough assessment of supplier capabilities ensures alignment with quality and production standards.
Negotiating contracts with Japanese suppliers often involves detailed discussions on quality control measures.
Transparent communication is vital to address expectations and responsibilities.
Flexible but clear terms regarding delivery schedules and payment conditions can facilitate smoother transactions.
Additionally, considering factors like supply chain resilience and sustainability is increasingly important.
Japanese suppliers often prioritize long-term partnerships, emphasizing reliability and consistency.
Implementing robust procurement processes can enhance the effectiveness of sourcing from Japan.
By adopting best practices, businesses can optimize their purchasing strategies and achieve better outcomes.
Supplier Negotiation Techniques
Effective negotiation with Japanese suppliers requires cultural sensitivity and strategic planning.
Understanding the importance of relationship-building is paramount.
Building rapport through respect and patience lays the groundwork for successful negotiations.
Approaching negotiations with a collaborative mindset rather than a confrontational stance is beneficial.
Focusing on mutual gains fosters a win-win scenario for both parties.
Being well-prepared with detailed information and clear objectives enhances credibility.
Flexibility in negotiations allows for accommodating the supplier’s perspectives and constraints.
Emphasizing long-term partnership over short-term gains can lead to more favorable terms.
Respecting hierarchy and decision-making processes within Japanese companies is also important.
Maintaining open and honest communication throughout the negotiation process helps in resolving conflicts amicably.
These techniques can significantly improve the outcomes of negotiations with Japanese suppliers.
Best Practices
Adopting best practices in procurement and purchasing from Japan enhances efficiency and effectiveness.
Establishing clear and detailed specifications for products and services ensures alignment with expectations.
Implementing regular quality audits and inspections helps maintain high standards.
Leveraging technology for data-driven decision-making can optimize procurement processes.
Building a diverse and multi-functional team with expertise in Japanese business practices is advantageous.
Investing in cultural training for procurement personnel can bridge communication gaps.
Developing contingency plans for supply chain disruptions enhances resilience.
Fostering innovation through collaborative projects with suppliers can drive mutual growth.
Maintaining transparency and ethical standards in all transactions builds trust and integrity.
Continuous evaluation and improvement of procurement strategies ensure sustained success.
By integrating these best practices, businesses can maximize the benefits of sourcing from Japanese suppliers.
Market Conditions and Trends
The global manufacturing landscape is continually evolving, influencing procurement strategies.
There is an increasing demand for high-quality and customized products, driving the adoption of advanced Japanese manufacturing techniques.
Sustainability is becoming a critical factor, with businesses seeking eco-friendly and responsible manufacturing solutions.
Technological advancements, such as automation and AI, are shaping the future of manufacturing, making Japanese techniques more relevant.
Global supply chain disruptions have highlighted the importance of resilient and adaptable procurement strategies.
Japan’s aging population poses challenges in maintaining a skilled workforce, prompting investments in automation and training.
The rise of digital platforms facilitates easier access to Japanese suppliers and streamlined procurement processes.
Economic factors, including currency fluctuations and trade policies, can impact the cost and feasibility of sourcing from Japan.
Consumer preferences are shifting towards products that emphasize quality and durability, aligning with Japanese manufacturing strengths.
Staying abreast of these market conditions and trends is essential for businesses to effectively leverage Japanese manufacturing techniques.
Conclusion
The evolution of Japanese manufacturing techniques offers invaluable insights for global industries.
From traditional craftsmanship to modern technological advancements, Japanese manufacturing has consistently emphasized quality and efficiency.
The advantages of these techniques, including superior quality, continuous improvement, and strong supplier relationships, make them highly sought after.
However, businesses must navigate challenges such as high initial investments and cultural differences.
Effective procurement and purchasing strategies, grounded in best practices and cultural understanding, are key to successful collaborations with Japanese suppliers.
Staying informed about market conditions and trends further enhances the ability to leverage Japanese manufacturing innovations.
By embracing these strategies, businesses can enjoy the benefits of sourcing from Japan, leading to enhanced product quality and competitive advantage.
The lessons learned from Japanese manufacturing evolution are not only applicable to procurement but also to broader aspects of production and management.
Continuous learning and adaptation are essential to fully harness the potential of Japanese manufacturing techniques.
Ultimately, integrating these innovative insights can drive sustainable growth and excellence in the global manufacturing landscape.
資料ダウンロード
QCD管理受発注クラウド「newji」は、受発注部門で必要なQCD管理全てを備えた、現場特化型兼クラウド型の今世紀最高の受発注管理システムとなります。
ユーザー登録
受発注業務の効率化だけでなく、システムを導入することで、コスト削減や製品・資材のステータス可視化のほか、属人化していた受発注情報の共有化による内部不正防止や統制にも役立ちます。
NEWJI DX
製造業に特化したデジタルトランスフォーメーション(DX)の実現を目指す請負開発型のコンサルティングサービスです。AI、iPaaS、および先端の技術を駆使して、製造プロセスの効率化、業務効率化、チームワーク強化、コスト削減、品質向上を実現します。このサービスは、製造業の課題を深く理解し、それに対する最適なデジタルソリューションを提供することで、企業が持続的な成長とイノベーションを達成できるようサポートします。
製造業ニュース解説
製造業、主に購買・調達部門にお勤めの方々に向けた情報を配信しております。
新任の方やベテランの方、管理職を対象とした幅広いコンテンツをご用意しております。
お問い合わせ
コストダウンが利益に直結する術だと理解していても、なかなか前に進めることができない状況。そんな時は、newjiのコストダウン自動化機能で大きく利益貢献しよう!
(β版非公開)