- お役立ち記事
- Insert Molding Technologies and OEM Manufacturing Applications
月間77,185名の
製造業ご担当者様が閲覧しています*
*2025年2月28日現在のGoogle Analyticsのデータより
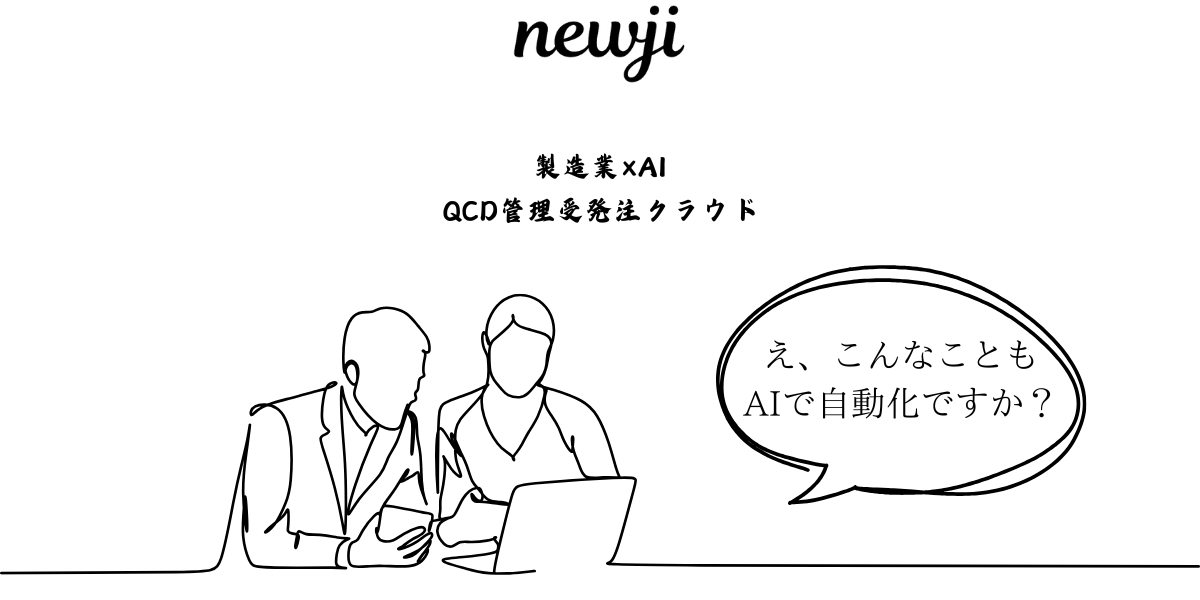
Insert Molding Technologies and OEM Manufacturing Applications
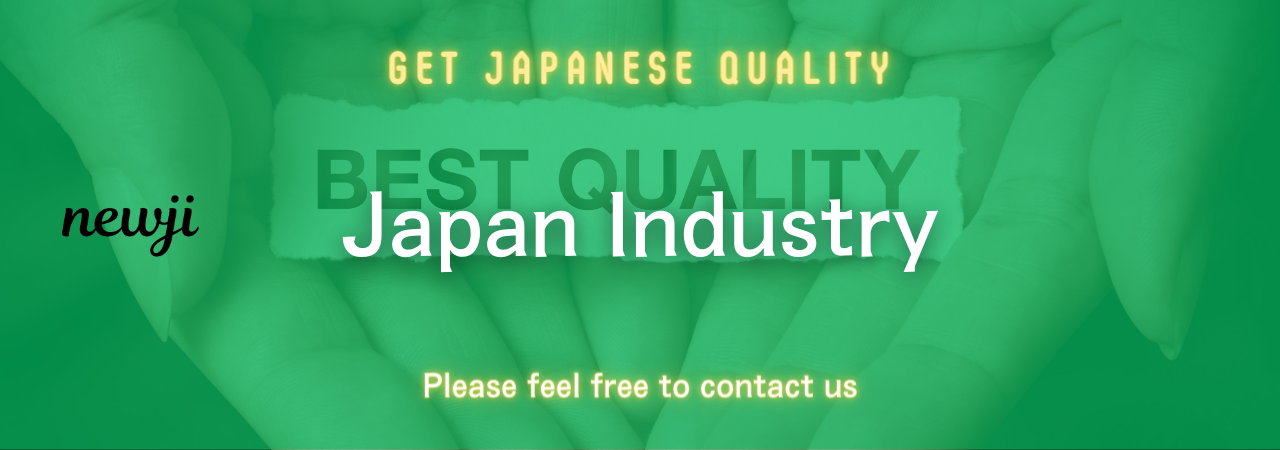
Insert molding is a versatile and innovative manufacturing process that is widely used in various industries today.
This technique involves placing a pre-formed part, known as an insert, into a mold before injecting it with a thermoplastic or thermoset resin.
The result is a single, integrated component that combines the characteristics of both the insert and the molded material.
目次
Understanding Insert Molding Technologies
Insert molding can significantly enhance the functionality and durability of products.
The core idea is to insert metal, ceramic, or other types of pre-formed components into a mold.
Once secured in place, the mold is filled with plastic, encapsulating the insert.
This approach is distinct from other molding techniques because it strategically incorporates distinct materials to form a single, cohesive part.
Types of Inserts Used in Insert Molding
Various materials can serve as inserts in the insert molding process.
Common choices include:
1. **Metal Inserts:** Often used for added strength and durability.
These typically include threaded brass or stainless steel inserts.
2. **Ceramic Inserts:** Used when electrical insulative properties or heat resistance is crucial.
3. **Plastic Inserts:** Although less common, plastic inserts can provide solutions for specific design requirements.
4. **Magnetic and Electronic Inserts:** Employed in cases where the final product needs magnetic properties or integrated electronics.
Advantages of Insert Molding
Insert molding offers several benefits over traditional manufacturing methods.
**Enhanced Durability:** The bonding of different materials in one process can produce highly durable components ideal for demanding applications.
**Reduced Assembly Costs:** By eliminating the need for separate manual assembly, insert molding significantly cuts down on labor and assembly costs.
**Improved Product Integrity:** The overall strength and integrity of the product increase, thus reducing the likelihood of failure under stress.
**Versatility in Applications:** This technology can be applied across various sectors, from medical devices to aerospace and automotive industries.
OEM Manufacturing Applications
Insert molding has a wide range of applications in Original Equipment Manufacturing (OEM).
OEMs are businesses that manufacture products or components that are purchased by another company and retailed under that purchasing company’s brand name.
Insert molding is often used to create specialized components that meet the specific needs of OEMs.
Automotive Industry
The automotive sector is one of the largest users of insert molding technologies.
Insert molding produces components like dashboards, control panels, and airbag systems.
The main benefit is integrating metal inserts into plastic molded components, enhancing durability and performance.
This technique helps in producing parts that are lighter yet equally strong, contributing to vehicle efficiency and safety.
Medical Devices
In the medical field, the integrity and reliability of devices are paramount.
Insert molding is widely used to manufacture medical devices incorporating metal or ceramic inserts for enhanced strength and durability.
Examples include syringes, surgical instruments, and various monitoring devices.
The seamless integration of materials ensures a contamination-free product, crucial for medical applications.
Electronics and Electrical Industry
Insert molding has found extensive applications in the electronics and electrical industry.
This technique is used to encase delicate electronic components in durable plastic housing, providing excellent insulation and protection.
Connectors, switches, and various handheld devices are commonly produced using insert molding.
The encapsulation of electronic components helps in protecting them from environmental factors and mechanical stress.
Aerospace Industry
The aerospace industry requires components that can withstand extreme conditions.
Insert molding is used to manufacture parts for aircraft, such as structural components and various mechanisms that need metal inserts for added strength.
This process ensures the components are lightweight yet able to endure the high stresses and temperatures experienced during flight.
Innovation and Future Trends
Insert molding continues to evolve with advancements in materials and technology.
Researchers are exploring new insert materials that offer superior properties, such as enhanced thermal stability or electrical conductivity.
Future trends in insert molding may include the integration of smart materials and technologies like sensors directly into the molded components.
Sustainable Materials
There is a growing interest in using sustainable materials in the insert molding process.
For example, bio-based plastics and recyclable inserts can reduce the environmental impact of manufacturing.
The push for sustainability is driving innovation in materials used for insert molding, contributing to more eco-friendly production methods.
Automation and Industry 4.0
Advancements in automation technology are also influencing the insert molding process.
Smart factories and Industry 4.0 concepts are being integrated into production lines, making the process more efficient and reducing the potential for human error.
Automated systems can precisely place inserts into molds and monitor the molding process, ensuring high-quality output.
In conclusion, insert molding is a powerful manufacturing technology that offers numerous advantages for OEM applications.
From improving product durability to reducing assembly costs, its benefits are clear.
With ongoing innovations and a focus on sustainability, the future of insert molding looks promising, providing tailored solutions for various industrial needs.
資料ダウンロード
QCD管理受発注クラウド「newji」は、受発注部門で必要なQCD管理全てを備えた、現場特化型兼クラウド型の今世紀最高の受発注管理システムとなります。
ユーザー登録
受発注業務の効率化だけでなく、システムを導入することで、コスト削減や製品・資材のステータス可視化のほか、属人化していた受発注情報の共有化による内部不正防止や統制にも役立ちます。
NEWJI DX
製造業に特化したデジタルトランスフォーメーション(DX)の実現を目指す請負開発型のコンサルティングサービスです。AI、iPaaS、および先端の技術を駆使して、製造プロセスの効率化、業務効率化、チームワーク強化、コスト削減、品質向上を実現します。このサービスは、製造業の課題を深く理解し、それに対する最適なデジタルソリューションを提供することで、企業が持続的な成長とイノベーションを達成できるようサポートします。
製造業ニュース解説
製造業、主に購買・調達部門にお勤めの方々に向けた情報を配信しております。
新任の方やベテランの方、管理職を対象とした幅広いコンテンツをご用意しております。
お問い合わせ
コストダウンが利益に直結する術だと理解していても、なかなか前に進めることができない状況。そんな時は、newjiのコストダウン自動化機能で大きく利益貢献しよう!
(β版非公開)