- お役立ち記事
- Inspection Criteria for Manufacturing
Inspection Criteria for Manufacturing
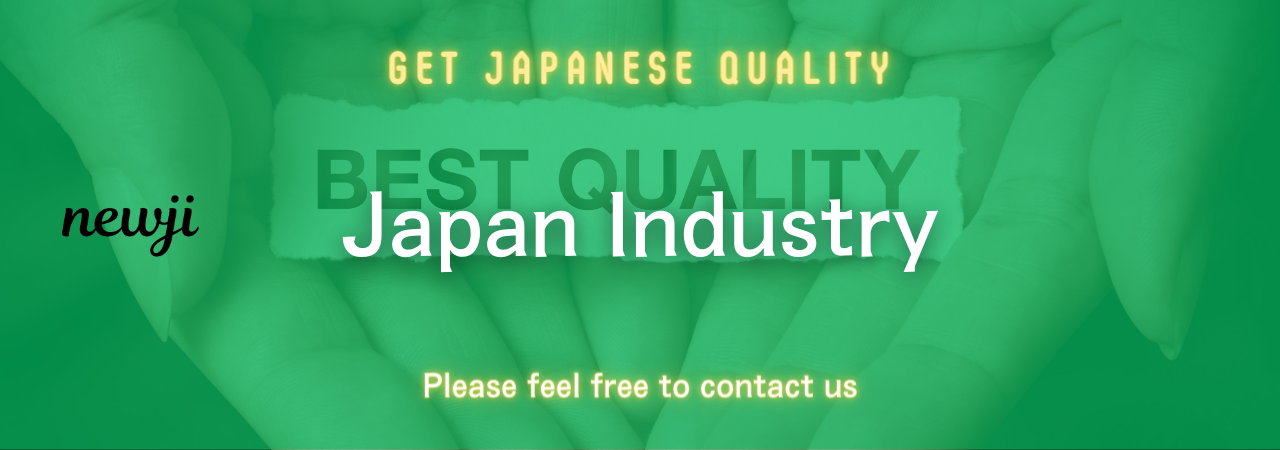
Understanding Inspection Criteria in Manufacturing
In the world of manufacturing, inspection criteria are the guidelines used to assess the quality and functionality of a product.
This crucial step ensures that products meet predefined standards before they reach consumers.
Understanding these criteria is essential for manufacturers aiming to produce high-quality products consistently.
The Importance of Inspection Criteria
Inspection criteria are vital for several reasons.
First and foremost, they help maintain product quality, reducing the risk of defects and recalls.
High-quality products lead to increased customer satisfaction and brand loyalty, ultimately driving sales and profitability.
Moreover, inspection criteria ensure compliance with industry standards and regulations.
Many industries have strict guidelines that manufacturers must follow to operate legally.
Failing to meet these standards can result in fines, legal issues, and damage to the company’s reputation.
Lastly, inspection criteria help optimize the production process.
By identifying errors early on, manufacturers can address them quickly and efficiently, reducing waste and production costs.
A well-defined inspection process also enhances consistency, ensuring each product adheres to the same quality standards.
Types of Inspection Criteria
There are several types of inspection criteria used in manufacturing.
Each type focuses on different aspects of the product and production process:
1. **Visual Inspection:** This involves examining products for visible defects such as scratches, dents, or discoloration.
Visual inspections are often the first step in quality control.
2. **Dimensional Inspection:** This type checks the physical dimensions of a product, ensuring it meets the specified measurements.
This is critical in industries where precision is vital, such as aerospace or automotive manufacturing.
3. **Functional Inspection:** This involves testing the product’s performance to ensure it operates as intended.
For example, an electronic device would undergo functional testing to verify its features work correctly.
4. **Material Inspection:** This checks the raw materials used in production to ensure they meet the quality requirements.
Material inspection is essential for maintaining product integrity and safety.
5. **Non-Destructive Testing:** This inspection method allows for testing materials and products without causing damage.
Techniques such as X-rays, ultrasonic testing, and magnetic particle testing fall under this category.
6. **Destructive Testing:** In some cases, products are tested to their breaking point to determine their strength and durability.
While destructive, this testing ensures products can withstand real-world use.
Implementing Inspection Criteria
Successfully implementing inspection criteria requires a systematic approach:
– **Define Quality Standards:** Clearly outline the quality standards that your products must meet.
These standards should align with industry regulations and customer expectations.
– **Develop Inspection Procedures:** Create detailed procedures for each type of inspection.
Include information on tools required, steps to follow, and criteria for passing or failing.
– **Train Inspectors:** Ensure that all inspectors are well-trained to carry out their tasks.
They should understand the importance of each inspection type and how to conduct them effectively.
– **Use Technology:** Leverage technology to enhance the inspection process.
Automated inspection tools, such as machine vision systems, can improve accuracy and efficiency.
– **Regular Audits:** Conduct regular audits of the inspection process to identify areas for improvement.
Audits help ensure compliance with standards and improve overall quality control.
Challenges in Maintaining Inspection Criteria
While inspection criteria are indispensable, maintaining them can present challenges:
– **Evolving Standards:** Industry standards and regulations can change, requiring manufacturers to update their inspection criteria regularly.
Staying informed and adaptable is crucial.
– **Human Error:** Despite training, inspectors may make mistakes.
Implementing double-check systems and encouraging a culture of vigilance can mitigate this risk.
– **Cost Implications:** Inspection processes can be costly, especially if they involve advanced technology or specialized personnel.
Balancing cost with quality assurance is a challenge many manufacturers face.
– **Time Constraints:** Inspections can be time-consuming, potentially bottlenecking the production process.
Streamlining procedures and using automation can help reduce delays.
Future Trends in Inspection Criteria
The future of inspection criteria in manufacturing is likely to be shaped by technology and innovation:
– **AI and Machine Learning:** These technologies can enhance inspection precision, predicting defects before they occur and optimizing processes.
– **Internet of Things (IoT):** IoT devices can provide real-time data on equipment and production conditions, facilitating immediate quality control responses.
– **Remote Inspections:** With advances in remote technology, inspections can be conducted remotely, reducing travel time and costs.
– **Sustainable Practices:** As sustainability becomes a priority, inspection criteria will likely incorporate environmental considerations, ensuring products are eco-friendly.
In conclusion, inspection criteria are a cornerstone of the manufacturing process.
By understanding and implementing these guidelines, manufacturers can ensure product quality, comply with regulations, and enhance efficiency.
Though challenges exist, technological advancements promise to streamline and improve inspection criteria, paving the way for a more efficient and effective manufacturing landscape.
資料ダウンロード
QCD調達購買管理クラウド「newji」は、調達購買部門で必要なQCD管理全てを備えた、現場特化型兼クラウド型の今世紀最高の購買管理システムとなります。
ユーザー登録
調達購買業務の効率化だけでなく、システムを導入することで、コスト削減や製品・資材のステータス可視化のほか、属人化していた購買情報の共有化による内部不正防止や統制にも役立ちます。
NEWJI DX
製造業に特化したデジタルトランスフォーメーション(DX)の実現を目指す請負開発型のコンサルティングサービスです。AI、iPaaS、および先端の技術を駆使して、製造プロセスの効率化、業務効率化、チームワーク強化、コスト削減、品質向上を実現します。このサービスは、製造業の課題を深く理解し、それに対する最適なデジタルソリューションを提供することで、企業が持続的な成長とイノベーションを達成できるようサポートします。
オンライン講座
製造業、主に購買・調達部門にお勤めの方々に向けた情報を配信しております。
新任の方やベテランの方、管理職を対象とした幅広いコンテンツをご用意しております。
お問い合わせ
コストダウンが利益に直結する術だと理解していても、なかなか前に進めることができない状況。そんな時は、newjiのコストダウン自動化機能で大きく利益貢献しよう!
(Β版非公開)