- お役立ち記事
- Inspection methods to ensure safety standards for imported products Steps to be taken by the purchasing department
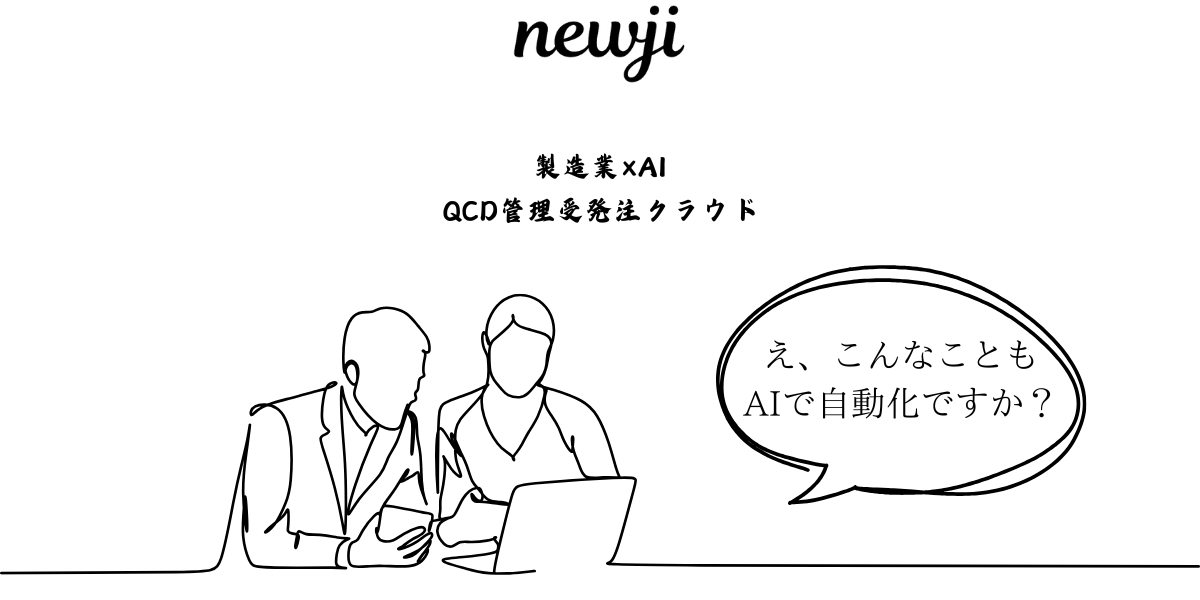
Inspection methods to ensure safety standards for imported products Steps to be taken by the purchasing department
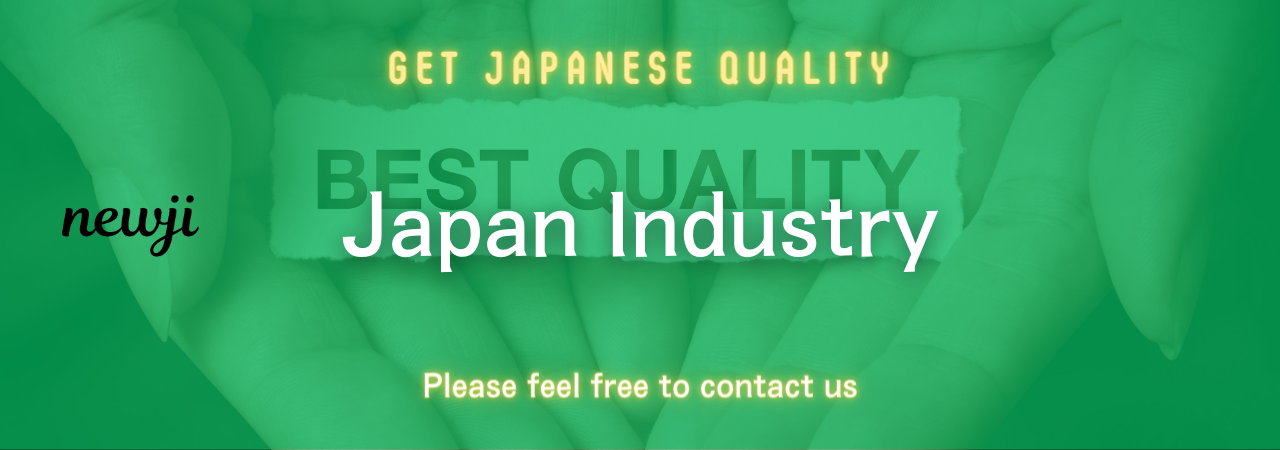
目次
Understanding the Importance of Safety Standards for Imported Products
The global marketplace is expanding rapidly, creating various opportunities for businesses to source products from different parts of the world.
However, with these opportunities come challenges, particularly ensuring that imported goods meet safety standards.
Ensuring products comply with safety regulations not only protects consumers but also preserves a company’s reputation and avoids legal issues.
The purchasing department plays a vital role in this process.
It is responsible for implementing thorough inspection methods that guarantee the safety and quality of the products purchased.
The Role of the Purchasing Department in Product Safety
The purchasing department is the first line of defense in managing the quality of imported products.
This department needs to be well-versed in both national and international safety standards related to the products they wish to import.
Further, they should utilize the comprehensive inspection methods that are designed to meet these standards.
An efficient purchasing department will establish robust procedures to evaluate and select suppliers who maintain high manufacturing and safety criteria.
This includes assessing the suppliers’ compliance records and ensuring their certifications are in line with the required safety standards.
Steps to Engage in Effective Inspection Methods
To ensure that the products meet safety standards, the purchasing department should adopt a series of systematic steps in the inspection process.
Step 1: Supplier Evaluation and Selection
Before importing products, evaluate potential suppliers based on their ability to meet safety standards.
This can be achieved through site visits, reviewing manufacturing practices, and checking for industry certifications.
Choosing the right supplier is crucial as it sets the foundation for product safety and quality assurance.
Step 2: Demand for Compliance Certificates
Request recent compliance certificates from the supplier to verify adherence to safety standards.
These certifications should be from reputable agencies that confirm the product’s safety and quality.
Having these documents provides assurance that the initial stages of production align with required standards.
Step 3: Product Testing
Engage in independent product testing even after receiving compliance certificates.
Third-party testing laboratories can verify the safety and quality of products, ensuring they meet specific country requirements.
Such testing is important to detect any discrepancies which may have been overlooked in the supplier’s testing processes.
Step 4: Conduct On-Site Audits
Occasional on-site audits of the supplier’s facilities can provide insights into their manufacturing practices.
These audits should focus on the production processes, quality control measures, and the working environment.
On-site audits help verify that suppliers continue to adhere to safety standards over time.
Step 5: Implement Continuous Monitoring
The process of ensuring product safety doesn’t end once the product reaches its destination.
Establish continuous monitoring systems that evaluate the performance and safety of the products over time.
This includes tracking customer feedback and conducting periodic quality checks to identify any new safety concerns.
Challenges in Ensuring Safety Standards
While the steps above offer a robust framework, the purchasing department may face challenges in ensuring safety standards for imported products.
Communication Barriers
Language and cultural differences can pose significant hurdles in effectively communicating safety requirements to international suppliers.
Clear communication channels must be established, often requiring multilingual staff or professional translators to bridge these gaps.
Rapid Changes in Regulations
Safety standards and regulations change rapidly and differ between countries.
Keeping up-to-date with these changes is crucial for maintaining compliance.
This can be achieved by subscribing to regulatory updates, participating in industry seminars, and collaborating with legal experts.
Counterfeit Products
The risk of counterfeit products entering the supply chain can compromise safety standards.
Purchasing departments should develop vigilant measures to authenticate the legitimacy of products, such as partnering with trusted suppliers and conducting regular audits.
Cost Considerations
Implementing thorough inspection methods can be costly, and balancing cost with thoroughness is a common challenge.
Yet, the cost of non-compliance, including product recalls and potential lawsuits, far outweighs the investment in proper inspection methods.
Conclusion
Ensuring the safety of imported products is a critical responsibility of the purchasing department.
By implementing systematic inspection methods, from evaluating suppliers to conducting continuous monitoring, companies can guarantee that their products meet safety standards.
Though challenges exist, they can be managed with robust processes and effective communication.
In doing so, businesses not only protect their consumers but also bolster their reputation and foster trust in the international market.
資料ダウンロード
QCD調達購買管理クラウド「newji」は、調達購買部門で必要なQCD管理全てを備えた、現場特化型兼クラウド型の今世紀最高の購買管理システムとなります。
ユーザー登録
調達購買業務の効率化だけでなく、システムを導入することで、コスト削減や製品・資材のステータス可視化のほか、属人化していた購買情報の共有化による内部不正防止や統制にも役立ちます。
NEWJI DX
製造業に特化したデジタルトランスフォーメーション(DX)の実現を目指す請負開発型のコンサルティングサービスです。AI、iPaaS、および先端の技術を駆使して、製造プロセスの効率化、業務効率化、チームワーク強化、コスト削減、品質向上を実現します。このサービスは、製造業の課題を深く理解し、それに対する最適なデジタルソリューションを提供することで、企業が持続的な成長とイノベーションを達成できるようサポートします。
オンライン講座
製造業、主に購買・調達部門にお勤めの方々に向けた情報を配信しております。
新任の方やベテランの方、管理職を対象とした幅広いコンテンツをご用意しております。
お問い合わせ
コストダウンが利益に直結する術だと理解していても、なかなか前に進めることができない状況。そんな時は、newjiのコストダウン自動化機能で大きく利益貢献しよう!
(Β版非公開)