- お役立ち記事
- Intake Manifold Manufacturing Process and Airflow Improvement
月間76,176名の
製造業ご担当者様が閲覧しています*
*2025年3月31日現在のGoogle Analyticsのデータより
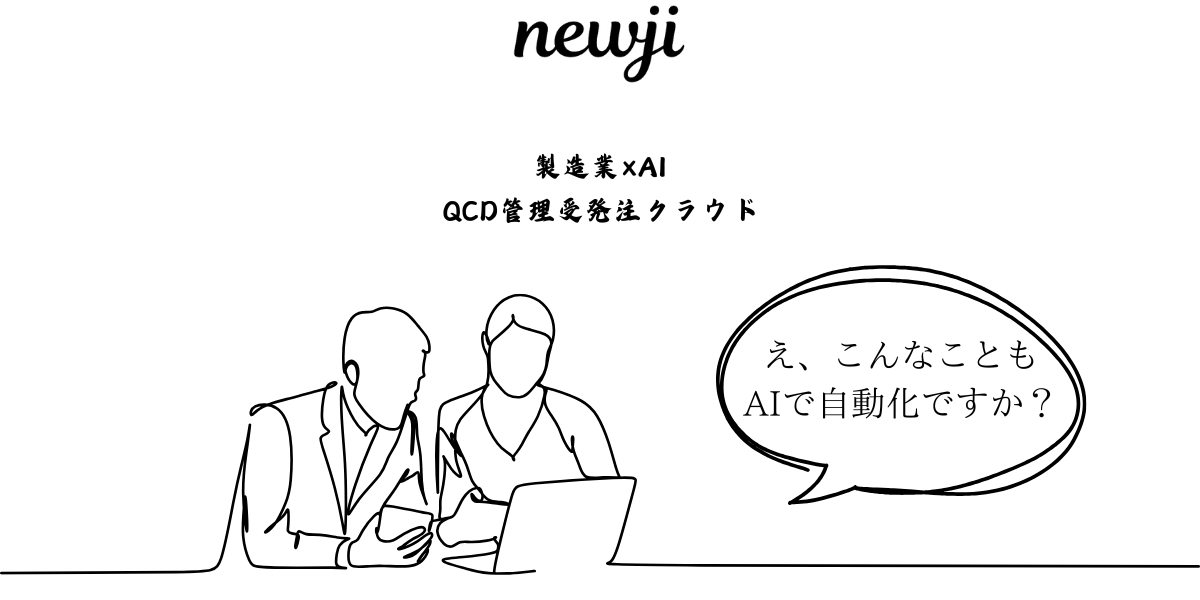
Intake Manifold Manufacturing Process and Airflow Improvement
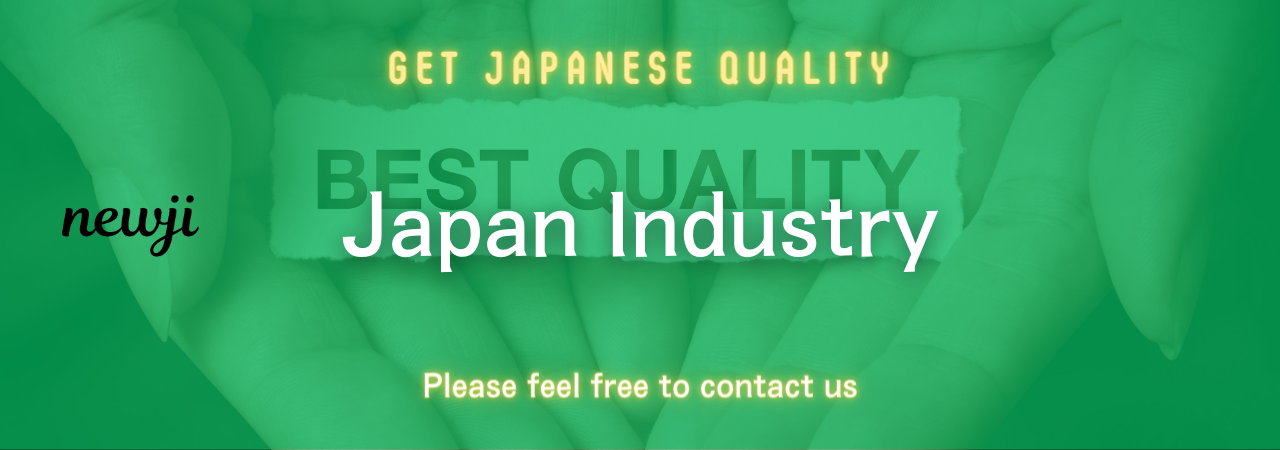
目次
Understanding the Basics of an Intake Manifold
An intake manifold is an essential component of an internal combustion engine.
Its primary function is to evenly distribute the air-fuel mixture to the engine’s cylinders.
This ensures that each cylinder receives the precise amount of mixture needed for optimal performance.
Improving airflow in an intake manifold is crucial for engine efficiency and power output.
The Importance of Airflow
Enhancing the airflow within an intake manifold can lead to significant improvements in engine performance.
When air moves smoothly, the engine can burn fuel more efficiently, resulting in better power, efficiency, and emissions.
Reducing turbulence and restrictions within the manifold aids in achieving this smooth airflow.
The Manufacturing Process of an Intake Manifold
Manufacturing an intake manifold involves several meticulous steps.
Each step contributes to the creation of a component that plays a vital role in engine performance.
Design and Material Selection
The manufacturing process begins with the design phase.
Engineers use advanced computer-aided design (CAD) software to draft designs that accommodate efficient airflow and fit the engine specifications.
Material selection is another critical consideration.
Common materials include aluminum, plastic composites, and cast iron.
Factors like weight, heat resistance, and cost influence the choice of material.
Prototype Development and Testing
Once the design phase is completed, a prototype is developed.
This prototype undergoes rigorous testing to ensure it meets the required performance standards.
During this phase, any necessary modifications are made to the design to enhance performance and address any potential issues.
Molding and Casting
After perfecting the prototype, the next step is to create molds for mass production.
The casting process involves pouring molten material into the mold to form the shape of the manifold.
For aluminum or iron manifolds, the process is known as sand casting, whereas plastic manifolds are often made through injection molding.
Finishing Process
Once the casting is complete, the manifold undergoes a finishing process to refine its shape and surface.
This involves machining operations where excess material is removed to achieve precise dimensions and a smooth finish that ensures optimal airflow.
Proper finishing is crucial as it minimizes airflow resistance inside the manifold.
Quality Control and Inspection
Before final assembly, intake manifolds are subject to strict quality control measures.
This includes inspecting the manifolds to ensure they meet all tolerances and specifications.
Any defects observed during this inspection are rectified to avoid performance issues when installed in an engine.
Improving Airflow in Intake Manifolds
Improving the airflow in intake manifolds often involves fine-tuning various aspects of the design and material.
Here are some strategies manufacturers and engineers employ:
Smooth Inner Surfaces
The inner walls of the intake manifold should be as smooth as possible.
Any roughness can create turbulence, which hinders smooth airflow.
This is why precision machining and polishing are crucial parts of the manufacturing process.
Consistent surface smoothness can significantly reduce air resistance and improve engine output.
Optimization of Manifold Geometry
The shape and design of the manifold can have a significant impact on airflow.
Engineers often conduct simulations to find the most efficient designs.
For instance, a shorter and more direct path from the throttle body to the intake valves can enhance airflow.
Moreover, the transition points within the manifold should be optimized to minimize disruptions to airflow.
Variable Intake Manifold Technology
Some modern engines use technology such as variable intake manifolds.
These systems allow the manifold to change the path and volume of airflow based on engine speed and load.
This adjustment optimizes performance at different speeds and demands.
Implementing such technology can help improve both fuel efficiency and power at varying engine conditions.
Regular Maintenance and Upgrades
Once an intake manifold is installed in an engine, regular maintenance is key to keeping it performing well.
Cleanliness is critical, as dirt and debris can negatively impact airflow.
Moreover, there are aftermarket upgrades available, such as high-performance intake manifolds designed specifically to enhance airflow further.
Conclusion
The intake manifold is a crucial component of a car’s engine, playing a significant role in performance and efficiency.
From the initial design phases to regular maintenance, each step in the manufacturing and usage process is vital for ensuring that air flows as smoothly and efficiently as possible.
By understanding and applying improvements in the manufacturing process and technology, manufacturers can continue to enhance the effectiveness of intake manifolds in engines worldwide.
資料ダウンロード
QCD管理受発注クラウド「newji」は、受発注部門で必要なQCD管理全てを備えた、現場特化型兼クラウド型の今世紀最高の受発注管理システムとなります。
ユーザー登録
受発注業務の効率化だけでなく、システムを導入することで、コスト削減や製品・資材のステータス可視化のほか、属人化していた受発注情報の共有化による内部不正防止や統制にも役立ちます。
NEWJI DX
製造業に特化したデジタルトランスフォーメーション(DX)の実現を目指す請負開発型のコンサルティングサービスです。AI、iPaaS、および先端の技術を駆使して、製造プロセスの効率化、業務効率化、チームワーク強化、コスト削減、品質向上を実現します。このサービスは、製造業の課題を深く理解し、それに対する最適なデジタルソリューションを提供することで、企業が持続的な成長とイノベーションを達成できるようサポートします。
製造業ニュース解説
製造業、主に購買・調達部門にお勤めの方々に向けた情報を配信しております。
新任の方やベテランの方、管理職を対象とした幅広いコンテンツをご用意しております。
お問い合わせ
コストダウンが利益に直結する術だと理解していても、なかなか前に進めることができない状況。そんな時は、newjiのコストダウン自動化機能で大きく利益貢献しよう!
(β版非公開)