- お役立ち記事
- Integral molding joining technology of composite materials and metal and the latest composite material 3D printing technology
月間77,185名の
製造業ご担当者様が閲覧しています*
*2025年2月28日現在のGoogle Analyticsのデータより
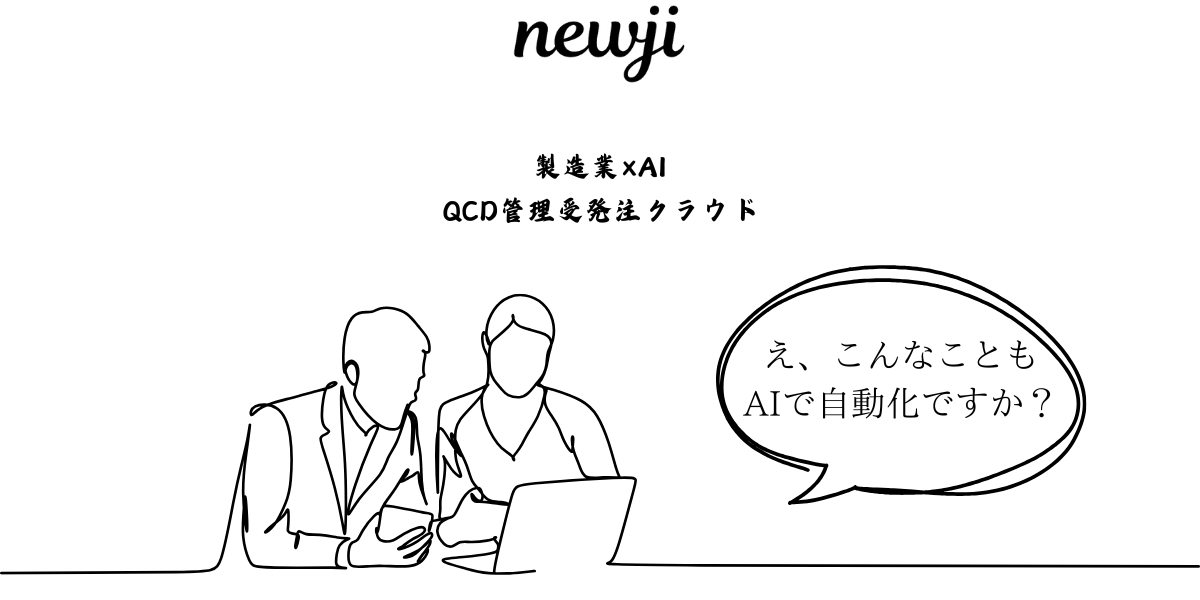
Integral molding joining technology of composite materials and metal and the latest composite material 3D printing technology
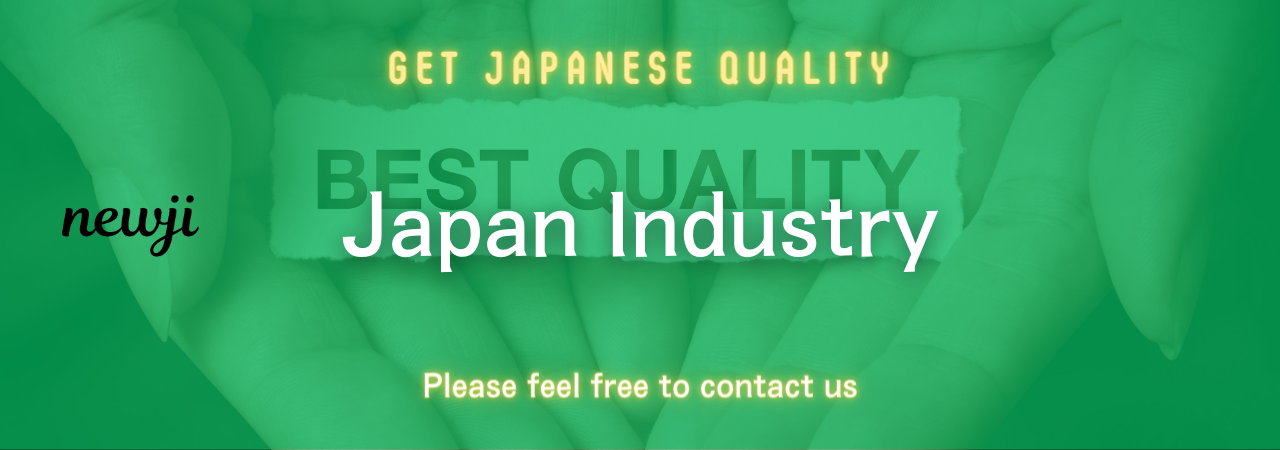
目次
Understanding Integral Molding Joining Technology
Integral molding joining technology is an innovative approach used to bond composite materials with metals.
This process is significant in industries such as aerospace, automotive, and construction.
The key benefit of this technology is that it harnesses the best qualities of both composite and metallic components, resulting in products that are both lightweight and strong.
Composite materials, which are made of two or more different constituent materials, offer advantages like high strength-to-weight ratio and resistance to corrosion.
Metals, on the other hand, provide robust structural integrity.
Combining these two through integral molding can lead to enhanced performance in the final products.
The process involves simultaneous molding and bonding of parts, which eliminates the need for additional fasteners or adhesives.
This not only reduces the overall weight of the structure but also enhances its strength and durability.
In applications like avionics and high-performance automotive engines, this can be critical.
Advantages of Integral Molding Joining Technology
The integral molding process offers several advantages over traditional methods of joining composite materials and metals.
1. **Enhanced Bond Strength**: The direct bonding that occurs in integral molding creates a stronger joint compared to using bolts, screws, or adhesives.
The seamless integration leads to better mechanical properties and load distribution across the joint.
2. **Weight Reduction**: By eliminating the need for heavy fasteners and additional bonding materials, the overall weight of the structure is significantly reduced.
This is crucial for industries where weight reduction translates to increased efficiency and lower fuel consumption.
3. **Improved Durability**: Structures created using integral molding exhibit better resistance to fatigue, environmental stress, and aging.
This enhances the lifespan and performance of components, particularly in challenging environments.
4. **Design Flexibility**: Engineers have greater freedom in design as integral molding allows for complex geometries and varying material thicknesses.
This adaptability means components can be optimized for specific functions and performance requirements.
5. **Cost-Effectiveness**: Although the initial setup for integral molding can be expensive, it often results in lower production costs in the long run.
This is due to reduced material wastage, simplified assembly processes, and minimal need for secondary operations.
Latest in Composite Material 3D Printing Technology
While integral molding joining technology has revolutionized the way composite materials are combined with metals, the evolution of 3D printing technology has further advanced the capabilities within this realm.
Composite material 3D printing is gaining momentum as it allows for the creation of complex, high-performance structures with a high degree of precision.
What is Composite Material 3D Printing?
Composite material 3D printing refers to the process of using 3D printing technology to create parts made from composite materials.
These materials often include a mix of polymers and fibers, such as carbon fiber, to enhance strength and flexibility.
This technology enables the production of customized parts that maintain the desirable qualities of composite materials, while also benefiting from the versatility and precision of 3D printing.
Advantages of Composite Material 3D Printing
1. **Precision and Detail**: 3D printing allows for highly detailed and precise manufacturing.
This is advantageous for creating complex parts with intricate geometries that are otherwise difficult to achieve with traditional manufacturing methods.
2. **Rapid Prototyping**: Composite material 3D printing facilitates rapid prototyping, enabling manufacturers to quickly test and refine their designs.
This acceleration in the development phase leads to faster time-to-market.
3. **Material Efficiency**: The additive nature of 3D printing means that material waste is minimized.
Materials are only used where necessary, making the process more environmentally friendly and cost-efficient.
4. **Customization**: The technology allows for the personalization of parts to meet specific requirements or preferences, which is ideal for tailored applications in industries like medical devices or customer-centric products.
5. **Integration of Multifunctionality**: Due to the layer-by-layer approach of 3D printing, it is possible to incorporate different materials within the same part.
This integration can imbue parts with multifunctional properties, such as electrical conductivity or thermal resistance.
The Future of Integrating Composite Materials and 3D Printing
The symbiosis of integral molding joining technology and composite material 3D printing represents a significant leap forward in materials engineering.
By combining these technologies, industries can create products that are lighter, stronger, and tailored to specific needs.
In the automotive industry, for example, this could lead to producing lighter car parts without compromising safety.
In aerospace, it could mean more efficient components that reduce fuel consumption.
Furthermore, ongoing research and development in these technologies are likely to unlock even more potential.
For instance, the development of smart materials that can adapt to their environment, coupled with the precision of 3D printing, could lead to revolutionary products and structures.
However, challenges such as cost, scalability, and material diversity need to be addressed to fully harness the advantages offered by these technologies.
As equipment becomes more affordable and the range of available printing materials expands, we can expect to see broader adoption across various sectors.
In conclusion, the integration of integral molding joining technology with the latest in composite material 3D printing stands as a hallmark of modern engineering.
It not only revolutionizes the way composite materials and metals are used together but also sets the stage for future innovations in design and manufacturing.
資料ダウンロード
QCD管理受発注クラウド「newji」は、受発注部門で必要なQCD管理全てを備えた、現場特化型兼クラウド型の今世紀最高の受発注管理システムとなります。
ユーザー登録
受発注業務の効率化だけでなく、システムを導入することで、コスト削減や製品・資材のステータス可視化のほか、属人化していた受発注情報の共有化による内部不正防止や統制にも役立ちます。
NEWJI DX
製造業に特化したデジタルトランスフォーメーション(DX)の実現を目指す請負開発型のコンサルティングサービスです。AI、iPaaS、および先端の技術を駆使して、製造プロセスの効率化、業務効率化、チームワーク強化、コスト削減、品質向上を実現します。このサービスは、製造業の課題を深く理解し、それに対する最適なデジタルソリューションを提供することで、企業が持続的な成長とイノベーションを達成できるようサポートします。
製造業ニュース解説
製造業、主に購買・調達部門にお勤めの方々に向けた情報を配信しております。
新任の方やベテランの方、管理職を対象とした幅広いコンテンツをご用意しております。
お問い合わせ
コストダウンが利益に直結する術だと理解していても、なかなか前に進めることができない状況。そんな時は、newjiのコストダウン自動化機能で大きく利益貢献しよう!
(β版非公開)