- お役立ち記事
- Integrating and Streamlining Manufacturing Processes with CIM (Computer Integrated Manufacturing)
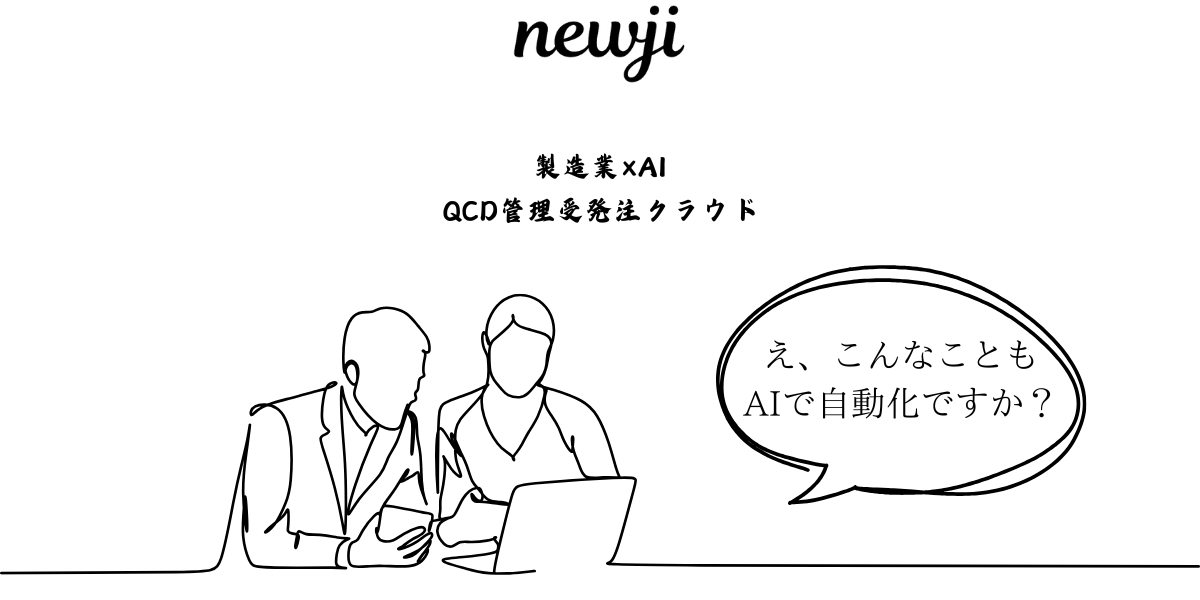
Integrating and Streamlining Manufacturing Processes with CIM (Computer Integrated Manufacturing)
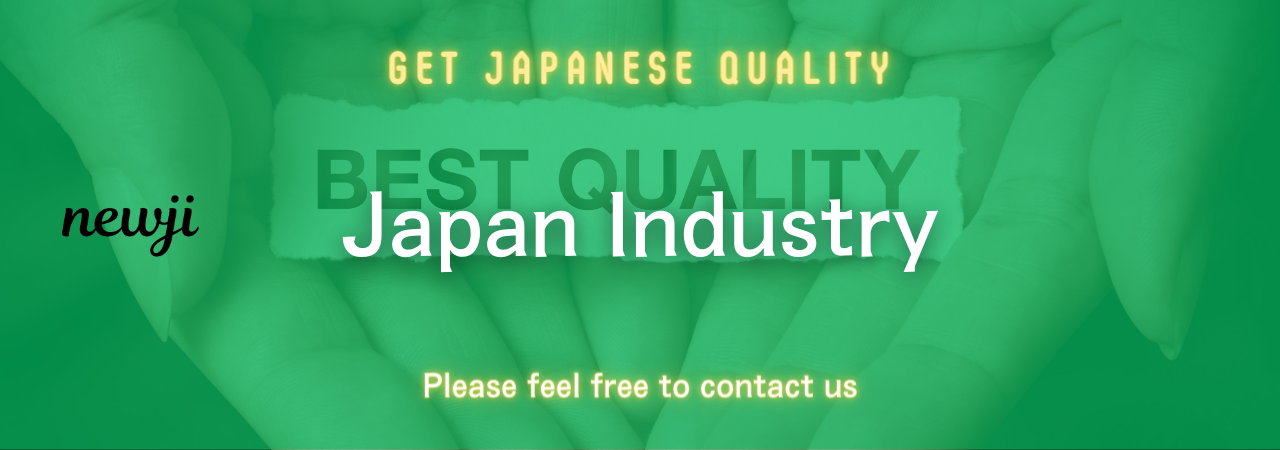
目次
Understanding Computer Integrated Manufacturing (CIM)
Computer Integrated Manufacturing (CIM) is a method of using computers to control the entire production process in manufacturing industries.
This concept aims to integrate various manufacturing processes, from the initial design to the final product, under one automated system.
By doing so, companies can achieve higher efficiency, reduce errors, and improve product quality.
In the world of modern manufacturing, technology plays a crucial role.
The integration of various automated systems and processes through CIM enables manufacturers to streamline their operations, leading to more productive and cost-effective manufacturing environments.
The Evolution of Manufacturing Processes
Manufacturing has come a long way from the days of manual labor and simple machineries, with significant advancements brought by industrial revolutions.
From mechanization to electricity, and more recently, the integration of information technology, each phase has contributed to improving manufacturing processes.
CIM represents the latest stage in this evolution, and it involves the use of computer systems to manage and control all aspects of manufacturing.
From product design, material handling, and production planning to quality control and even the end-user delivery, CIM encompasses every facet of a manufacturing operation.
The Role of Computers in CIM
Computers are at the heart of CIM, serving as the brains behind the entire operation.
They gather data from various sensors, machines, and systems throughout the manufacturing process.
This data is then analyzed and used to make informed decisions, control machines, and optimize workflows.
The use of software tools like Computer-Aided Design (CAD) and Computer-Aided Manufacturing (CAM) allows for precise design and manufacturing instructions.
These systems ensure that every component is produced to exact specifications, reducing errors and waste.
Key Components of CIM
Several components make up a Computer Integrated Manufacturing system.
Here are some of the key elements:
1. Computer-Aided Design (CAD)
CAD software allows engineers and designers to create detailed 3D models of products.
These models serve as blueprints for the manufacturing process, ensuring accuracy and consistency.
2. Computer-Aided Manufacturing (CAM)
CAM systems convert CAD designs into instructions for automated machinery.
These instructions guide machines on how to create the product, ensuring precision and efficiency.
3. Programmable Logic Controllers (PLCs)
PLCs are specialized computers used to automate manufacturing processes.
They control machinery and ensure that each step of the production process is executed correctly.
4. Robotics
Robotic systems play a vital role in CIM.
They can perform tasks such as assembly, welding, and material handling with high efficiency and accuracy.
5. Enterprise Resource Planning (ERP)
ERP systems integrate all aspects of a business, including finance, supply chain, and manufacturing.
They ensure that all departments work together seamlessly, enhancing overall efficiency.
Benefits of Computer Integrated Manufacturing
Implementing CIM offers several advantages for manufacturing companies.
These benefits can significantly impact the overall performance and profitability of a business.
1. Improved Efficiency
By automating and integrating various processes, CIM reduces the time and effort required to produce a product.
Tasks that used to take hours can now be completed in minutes, leading to faster production cycles.
2. Enhanced Quality Control
CIM systems ensure that products are manufactured to strict specifications.
This consistent quality control reduces defects and enhances the reliability of the final product.
3. Cost Reduction
Automating manufacturing processes lowers labor costs and reduces material waste.
This results in significant cost savings for manufacturers.
4. Flexibility
CIM allows for easy adjustments to manufacturing processes.
Manufacturers can quickly reprogram machines to produce different products, enabling them to respond to market demands swiftly.
5. Data-Driven Decision Making
The data collected by CIM systems provides valuable insights into production processes.
Manufacturers can use this information to make informed decisions, optimize workflows, and identify areas for improvement.
Challenges in Implementing CIM
While CIM offers numerous benefits, its implementation can be challenging.
Manufacturers must address several issues to ensure a successful integration.
1. Initial Investment
The cost of setting up a CIM system can be substantial.
It requires investment in hardware, software, and training for employees.
However, the long-term benefits often outweigh the initial costs.
2. Complexity
Integrating multiple systems and processes requires careful planning and coordination.
Manufacturers must ensure that all components work seamlessly together.
3. Employee Training
Employees need to be trained to operate and maintain CIM systems.
This training is essential to ensure that the workforce can effectively use the technology.
4. Data Security
As CIM relies heavily on data, ensuring the security of this information is crucial.
Manufacturers must implement robust cybersecurity measures to protect against data breaches.
The Future of Computer Integrated Manufacturing
The future of manufacturing lies in further advancements in CIM technology.
As technology continues to evolve, so will the capabilities of CIM systems.
1. Internet of Things (IoT)
The IoT enables devices to communicate and share data seamlessly.
In the context of CIM, IoT can enhance the connectivity between machines, improving overall efficiency and control.
2. Artificial Intelligence (AI)
AI can analyze data and make decisions in real-time.
This capability allows CIM systems to optimize production processes, predict maintenance needs, and reduce downtime.
3. 3D Printing
3D printing technology can revolutionize manufacturing by allowing the creation of complex parts with minimal waste.
Integrating 3D printing into CIM systems can further enhance production capabilities.
4. Advanced Robotics
Robots are becoming increasingly sophisticated, capable of performing more complex tasks.
Advanced robotics can improve automation and efficiency in CIM systems.
In conclusion, Computer Integrated Manufacturing is a pivotal technology in modern manufacturing.
By integrating and streamlining various processes, CIM offers numerous benefits, including improved efficiency, enhanced quality control, and cost reduction.
While there are challenges to implementing CIM, the long-term advantages make it a worthwhile investment for manufacturers.
The future of CIM holds even greater promise, with advancements in IoT, AI, 3D printing, and robotics set to further revolutionize the industry.
資料ダウンロード
QCD調達購買管理クラウド「newji」は、調達購買部門で必要なQCD管理全てを備えた、現場特化型兼クラウド型の今世紀最高の購買管理システムとなります。
ユーザー登録
調達購買業務の効率化だけでなく、システムを導入することで、コスト削減や製品・資材のステータス可視化のほか、属人化していた購買情報の共有化による内部不正防止や統制にも役立ちます。
NEWJI DX
製造業に特化したデジタルトランスフォーメーション(DX)の実現を目指す請負開発型のコンサルティングサービスです。AI、iPaaS、および先端の技術を駆使して、製造プロセスの効率化、業務効率化、チームワーク強化、コスト削減、品質向上を実現します。このサービスは、製造業の課題を深く理解し、それに対する最適なデジタルソリューションを提供することで、企業が持続的な成長とイノベーションを達成できるようサポートします。
オンライン講座
製造業、主に購買・調達部門にお勤めの方々に向けた情報を配信しております。
新任の方やベテランの方、管理職を対象とした幅広いコンテンツをご用意しております。
お問い合わせ
コストダウンが利益に直結する術だと理解していても、なかなか前に進めることができない状況。そんな時は、newjiのコストダウン自動化機能で大きく利益貢献しよう!
(Β版非公開)