- お役立ち記事
- Integrating Manufacturing Processes with CIM (Computer Integrated Manufacturing)
Integrating Manufacturing Processes with CIM (Computer Integrated Manufacturing)
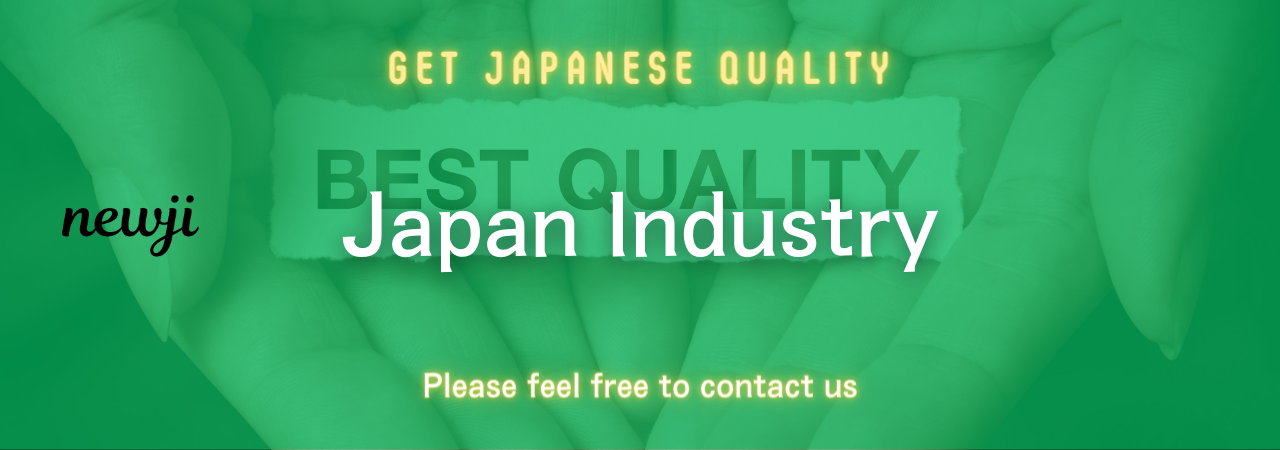
Manufacturing has greatly evolved over the past few decades.
Technological advancements have transformed how products are made, boosting efficiency, quality, and consistency.
One of the significant advancements in this domain is the integration of manufacturing processes with Computer Integrated Manufacturing (CIM).
目次
What is Computer Integrated Manufacturing (CIM)?
Computer Integrated Manufacturing (CIM) is a method of manufacturing that uses computers to control the entire production process.
This integration allows for a seamless flow of information from the design phase to production and even distribution.
CIM incorporates various technologies, including CAD (Computer-Aided Design), CAM (Computer-Aided Manufacturing), and PLM (Product Lifecycle Management).
The Role of CAD in CIM
Computer-Aided Design (CAD) is an essential component of CIM.
It helps engineers and designers create detailed 3D models of products on digital platforms.
These models are highly precise and help in identifying potential issues before actual manufacturing begins.
Design modifications can be done quickly, saving time and resources.
When CAD is integrated with CIM, it ensures that the design data is transferred accurately to the manufacturing machines.
The Contribution of CAM
Computer-Aided Manufacturing (CAM) takes the designs created in CAD and turns them into controlled instructions for machinery.
It means that the complex designs drawn up in CAD software can be manufactured precisely by various machines, such as CNC (Computer Numerical Control) machines.
CAM software ensures that designs are followed to the exact specifications, minimizing errors and enhancing quality control.
The link between CAD and CAM within CIM ensures that there is no loss of design data during the transition between designing and manufacturing.
Benefits of Integrating CIM in Manufacturing
The integration of CIM in manufacturing brings a host of benefits, enhancing both productivity and product quality.
Increased Efficiency
With CIM, manufacturing processes are quicker and more accurate.
Automated systems reduce the need for manual intervention, cutting down the time required for each step.
The entire workflow—from design to manufacturing to distribution—becomes streamlined.
Employees can focus on more strategic activities rather than mundane, repetitive tasks.
Improved Product Quality
CIM allows for precise control over manufacturing operations, significantly reducing errors.
The integration ensures that each product meets the specified standards.
Real-time monitoring and adjustments make it possible to maintain a consistent level of quality across all products.
Reduced Costs
Automation reduces the reliance on manual labor, significantly cutting labor costs.
Additionally, the high precision involved in CIM operations minimizes waste materials and defects.
Consequently, this leads to lower production costs and increases profitability.
Enhanced Flexibility
CIM systems are highly adaptable, allowing manufacturers to switch from making one product to another efficiently.
This flexibility is crucial in today’s market, where consumer preferences change rapidly.
CIM enables companies to remain competitive by responding quickly to market demands.
Challenges in Implementing CIM
While the benefits are numerous, integrating CIM into existing manufacturing processes is not without its challenges.
High Initial Investment
Setting up a CIM system can require a substantial initial investment.
The cost involves purchasing advanced machinery, software, and the necessary infrastructure.
However, the long-term benefits often justify this expense, especially for large-scale operations.
Need for Skilled Workforce
Operating CIM systems requires a workforce skilled in both manufacturing processes and computer technologies.
Training existing employees or hiring new ones with the required skill set can be challenging.
Ongoing training is also necessary to keep up with technological advancements.
System Integration
Integrating various components of CIM—such as CAD, CAM, and other software—can be complex.
Ensuring that all parts of the system communicate effectively with each other is crucial.
This requires meticulous planning and execution.
Future of CIM in Manufacturing
The future of CIM looks promising.
Technological advances continue to make computers and automation even more integral to manufacturing.
Internet of Things (IoT) Integration
The Internet of Things (IoT) can further enhance the capabilities of CIM by connecting all machines and processes through the internet.
IoT-compatible devices can share data in real-time, offering unprecedented levels of operational efficiency and real-time decision-making.
Artificial Intelligence (AI) and Machine Learning
AI and machine learning algorithms can analyze vast amounts of manufacturing data to provide actionable insights.
These technologies can predict equipment failures, optimize production schedules, and improve product quality.
When integrated with CIM, AI and machine learning can take manufacturing efficiency to the next level.
Continued Evolution of CAD and CAM
CAD and CAM technologies are continuously evolving, becoming more sophisticated and user-friendly.
Advances in these tools will make it even easier to design complex products and automate their production.
As these technologies improve, the efficiency and precision of CIM will also increase.
Integrating manufacturing processes with Computer Integrated Manufacturing (CIM) revolutionizes how products are designed, produced, and delivered.
Despite the initial challenges, the benefits of increased efficiency, improved quality, and reduced costs make it a worthy investment for many manufacturing firms.
As technology continues to advance, CIM will become even more critical in achieving operational excellence and staying competitive in the market.
資料ダウンロード
QCD調達購買管理クラウド「newji」は、調達購買部門で必要なQCD管理全てを備えた、現場特化型兼クラウド型の今世紀最高の購買管理システムとなります。
ユーザー登録
調達購買業務の効率化だけでなく、システムを導入することで、コスト削減や製品・資材のステータス可視化のほか、属人化していた購買情報の共有化による内部不正防止や統制にも役立ちます。
NEWJI DX
製造業に特化したデジタルトランスフォーメーション(DX)の実現を目指す請負開発型のコンサルティングサービスです。AI、iPaaS、および先端の技術を駆使して、製造プロセスの効率化、業務効率化、チームワーク強化、コスト削減、品質向上を実現します。このサービスは、製造業の課題を深く理解し、それに対する最適なデジタルソリューションを提供することで、企業が持続的な成長とイノベーションを達成できるようサポートします。
オンライン講座
製造業、主に購買・調達部門にお勤めの方々に向けた情報を配信しております。
新任の方やベテランの方、管理職を対象とした幅広いコンテンツをご用意しております。
お問い合わせ
コストダウンが利益に直結する術だと理解していても、なかなか前に進めることができない状況。そんな時は、newjiのコストダウン自動化機能で大きく利益貢献しよう!
(Β版非公開)