- お役立ち記事
- International certification acquisition support and quality control methods that purchasing personnel should know
International certification acquisition support and quality control methods that purchasing personnel should know
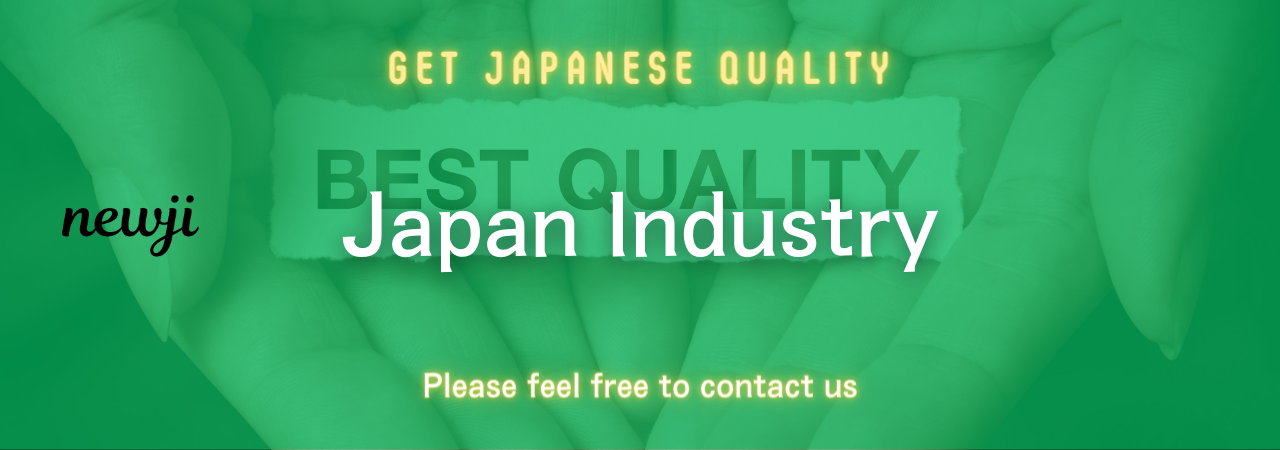
目次
Understanding International Certification
International certification plays a crucial role in global trade and manufacturing.
For purchasing personnel, understanding these certifications is essential to ensure that products meet international standards and quality requirements.
International certifications such as ISO, CE, and RoHS provide assurance of quality, safety, and environmental compliance.
Purchasing personnel should familiarize themselves with the different types of certifications relevant to their industry.
This knowledge will enable them to make informed decisions when selecting suppliers and products.
Certifications help mitigate risks, enhance brand reputation, and ensure compliance with regulatory standards in the target market.
The Importance of ISO Certification
ISO (International Organization for Standardization) certifications are among the most recognized standards across various industries.
They are designed to ensure safety, quality, and efficiency.
ISO certifications can range from quality management with ISO 9001 to environmental management with ISO 14001.
For purchasing teams, working with ISO-certified suppliers guarantees that products are manufactured in a controlled and consistent manner.
ISO certifications also demonstrate a supplier’s commitment to maintaining industry best practices.
Purchasing personnel should verify the ISO certifications of potential suppliers to ensure they meet these high standards.
Understanding CE Marking
CE marking is essential for products that are sold within the European Economic Area (EEA).
It signifies that a product complies with EU safety, health, and environmental protection requirements.
For purchasing teams, ensuring that products have CE marking is crucial when sourcing products destined for the European market.
CE marking covers a wide range of products, from electronics to medical devices.
Therefore, understanding the particular requirements for your product category is essential.
Purchasing teams should ensure that suppliers provide documentation that verifies the CE marking to avoid potential legal issues and ensure market access.
Introduction to RoHS Compliance
RoHS (Restriction of Hazardous Substances) compliance is crucial for electronic and electrical equipment.
This directive restricts the use of specific hazardous materials, ensuring products are environmentally friendly and safe.
For purchasing personnel, working with RoHS-compliant suppliers can prevent product recalls and protect consumer safety.
RoHS compliance is mandatory in the European Union and affects many product categories.
Purchasing teams should incorporate RoHS compliance checks into their supplier evaluation process to ensure that products are safe and eco-friendly.
Quality Control: A Key Element in Procurement
Quality control is vital in maintaining the integrity and reliability of products.
For purchasing personnel, implementing robust quality control methods can prevent defects, reduce costs, and increase customer satisfaction.
Developing a Supplier Evaluation Process
Developing a comprehensive supplier evaluation process is crucial in ensuring product quality.
Purchasing personnel should establish clear criteria for evaluating potential suppliers, such as ISO certification status, production capabilities, and past performance.
A thorough supplier evaluation can help identify potential risks and ensure that suppliers can consistently deliver high-quality products.
It should involve assessing the supplier’s quality management systems and their commitment to continuous improvement.
Implementing Incoming Inspection Procedures
Incoming inspection procedures are essential in verifying the quality of received goods.
Purchasing teams should establish robust inspection protocols to identify any defects or discrepancies upon product arrival.
These procedures may involve random sampling, visual inspections, or laboratory testing, depending on the product type and quality requirements.
Implementing incoming inspection procedures ensures that only products meeting the set standards enter the supply chain.
Utilizing Statistical Quality Control
Statistical quality control involves the use of statistical methods to monitor and control production processes.
Purchasing personnel can use tools like control charts and process capability analysis to identify variations and maintain quality.
Applying these techniques allows for early detection of quality issues and helps in taking corrective actions promptly.
By implementing statistical quality control measures, purchasing teams can ensure a consistent level of product quality.
Adopting Continuous Improvement Practices
Continuous improvement is key to maintaining and enhancing quality in procurement.
Purchasing personnel should foster a culture of continuous improvement within their teams and with their suppliers.
Encouraging Feedback and Collaboration
Encouraging feedback from end-users and collaborating closely with suppliers can lead to significant quality improvements.
Purchasing teams should actively seek feedback on product performance and work with suppliers to address any challenges.
Open communication channels and regular feedback loops can help in identifying areas for improvement and optimizing product quality.
Conducting Regular Audits
Regular audits of suppliers and internal processes can help in identifying non-conformities and areas for improvement.
Purchasing personnel should schedule periodic audits to assess compliance with quality standards and identify potential risks.
Audits provide valuable insights into supplier performance and ensure that quality control practices are being followed diligently.
Leveraging Technology for Quality Management
Technology can significantly enhance quality management efforts.
Purchasing teams should leverage technology tools such as data analytics, quality management software, and automated inspection systems.
These tools provide real-time data and insights, enabling purchasing personnel to make informed decisions and ensure consistent quality.
Embracing technology in quality management can lead to increased efficiency and a more robust procurement process.
In summary, acquiring international certification and implementing effective quality control methods are critical components for purchasing personnel.
By understanding certifications like ISO, CE, and RoHS, and adopting comprehensive quality management strategies, purchasing teams can ensure product compliance, maintain quality standards, and foster continuous improvement.
This not only enhances the reliability and safety of products but also builds trust with consumers and stakeholders.
資料ダウンロード
QCD調達購買管理クラウド「newji」は、調達購買部門で必要なQCD管理全てを備えた、現場特化型兼クラウド型の今世紀最高の購買管理システムとなります。
ユーザー登録
調達購買業務の効率化だけでなく、システムを導入することで、コスト削減や製品・資材のステータス可視化のほか、属人化していた購買情報の共有化による内部不正防止や統制にも役立ちます。
NEWJI DX
製造業に特化したデジタルトランスフォーメーション(DX)の実現を目指す請負開発型のコンサルティングサービスです。AI、iPaaS、および先端の技術を駆使して、製造プロセスの効率化、業務効率化、チームワーク強化、コスト削減、品質向上を実現します。このサービスは、製造業の課題を深く理解し、それに対する最適なデジタルソリューションを提供することで、企業が持続的な成長とイノベーションを達成できるようサポートします。
オンライン講座
製造業、主に購買・調達部門にお勤めの方々に向けた情報を配信しております。
新任の方やベテランの方、管理職を対象とした幅広いコンテンツをご用意しております。
お問い合わせ
コストダウンが利益に直結する術だと理解していても、なかなか前に進めることができない状況。そんな時は、newjiのコストダウン自動化機能で大きく利益貢献しよう!
(Β版非公開)