- お役立ち記事
- Introducing Risk-Based Approaches in Quality Management for Manufacturing and Their Benefits
月間76,176名の
製造業ご担当者様が閲覧しています*
*2025年3月31日現在のGoogle Analyticsのデータより
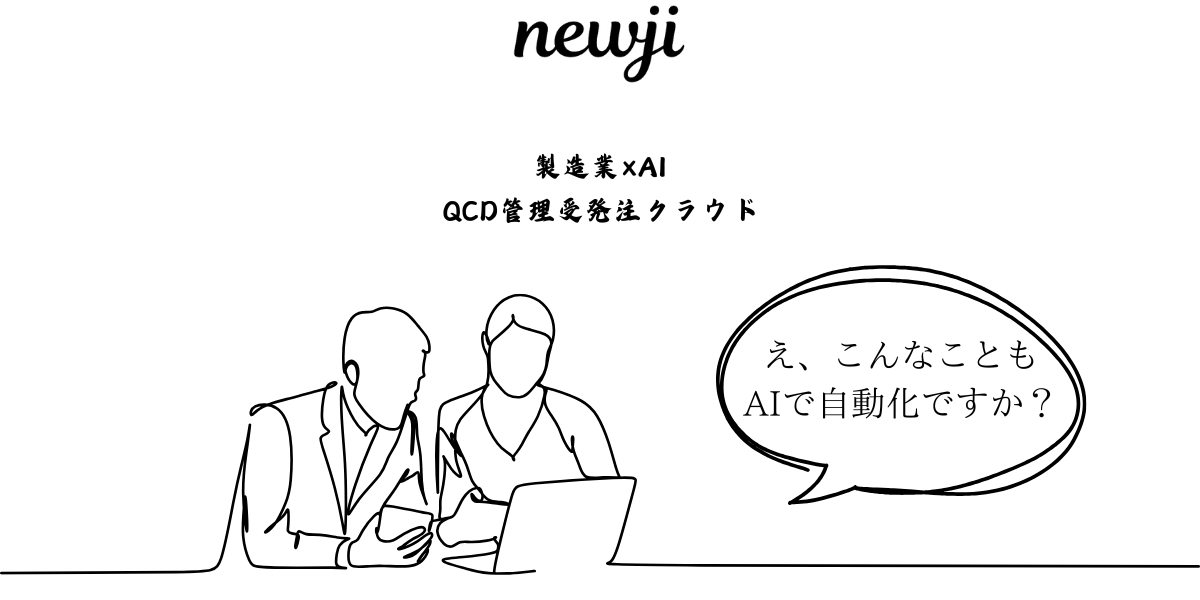
Introducing Risk-Based Approaches in Quality Management for Manufacturing and Their Benefits
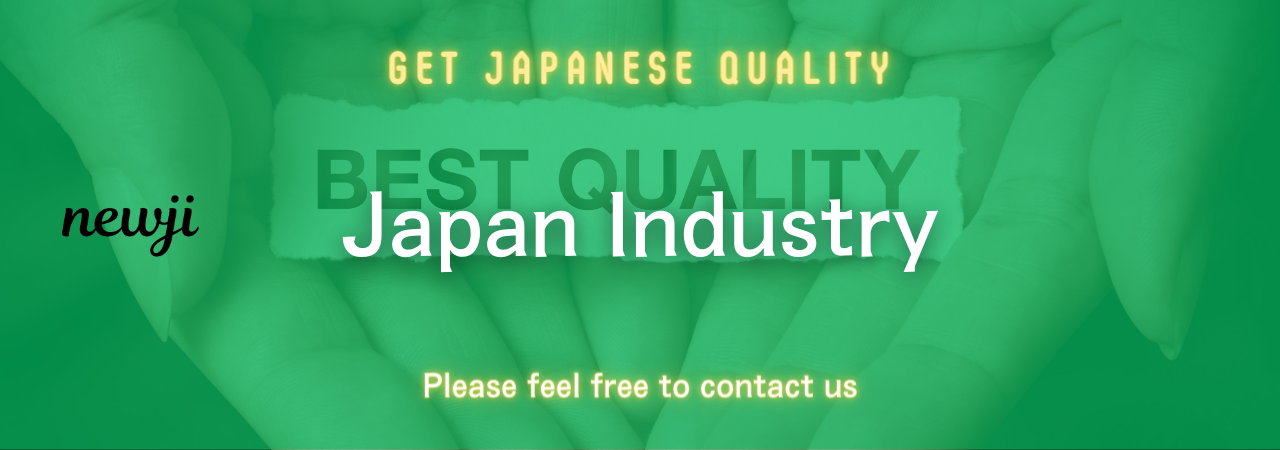
In the fast-evolving world of manufacturing, ensuring quality consistently can be daunting.
Traditional quality management approaches are evolving, making way for more efficient and effective methods.
One such method is the risk-based approach in quality management.
This method is not just about compliance, but a strategy that proactively addresses potential risks, ensures better product quality, and enhances overall operations.
Let’s delve deeper into what risk-based quality management entails and the numerous benefits it offers to manufacturing sectors.
目次
What is Risk-Based Quality Management?
Risk-based quality management involves identifying, assessing, and prioritizing risks that could potentially impact product quality.
Instead of reacting to quality issues after they occur, this approach focuses on anticipating and mitigating risks beforehand.
By doing so, manufacturers can ensure a higher level of quality assurance and minimize potential disruptions to their operations.
Steps Involved in a Risk-Based Approach
Implementing a risk-based approach involves several steps:
1. Risk Identification: This involves determining the potential risks that could impact product quality.
These can range from material defects to process inefficiencies.
2. Risk Assessment: Once risks are identified, they are assessed based on their severity and likelihood of occurrence.
3. Risk Prioritization: Not all risks carry the same weight. Prioritizing helps in focusing on the most critical risks first.
4. Risk Mitigation: This step involves developing strategies to minimize identified risks.
This can include process adjustments, equipment upgrades, or enhanced training for staff.
5. Continuous Monitoring: Risk management is not a one-time task.
Continuous monitoring and assessment ensure that new risks are identified and old ones are kept in check.
Benefits of Risk-Based Approaches in Quality Management
Adopting a risk-based approach in quality management offers numerous benefits.
Manufacturers that implement this strategy tend to reap the following rewards:
Proactive Quality Assurance
Traditional quality management often revolves around reacting to issues after they arise.
In contrast, a risk-based approach is proactive.
By identifying potential risks ahead of time, manufacturers can prevent issues before they occur.
This results in fewer defects and higher quality products reaching the market.
Improved Efficiency
By focusing on the most critical risks, resources can be allocated more effectively.
This ensures that time, money, and effort are directed where they are needed the most.
Consequently, production processes become more efficient, leading to reduced waste and lower costs.
Enhanced Compliance
In many industries, regulatory compliance is a significant concern.
A risk-based approach helps companies stay ahead of regulatory requirements by continuously monitoring and addressing potential risks.
This not only ensures compliance but can also prevent costly fines and sanctions.
Better Customer Satisfaction
Customers expect high-quality products.
By maintaining a consistently high level of quality, companies can enhance customer satisfaction and loyalty.
A proactive approach to quality management means that customers receive products that meet or exceed their expectations.
Continuous Improvement
One of the cornerstones of a risk-based approach is continuous improvement.
By regularly assessing and addressing risks, manufacturers can continually refine their processes.
This leads to ongoing enhancements in quality, efficiency, and overall operation.
Implementing a Risk-Based Quality Management System
Transitioning to a risk-based quality management system requires careful planning and execution.
Here are some critical steps for successful implementation:
Define Objectives
Before anything else, it’s vital to define clear objectives.
What does the company hope to achieve with a risk-based approach?
These objectives will guide the entire implementation process.
Engage Stakeholders
Quality management affects various departments within a manufacturing setup.
Engaging all relevant stakeholders ensures everyone understands the new approach and supports its implementation.
This includes management, production staff, and quality assurance teams.
Train Staff
Effective risk management relies on well-trained personnel.
Providing comprehensive training ensures that staff can identify and mitigate risks effectively.
Ongoing training keeps everyone up-to-date with the latest techniques and tools.
Utilize Technology
Advanced technologies like data analytics, artificial intelligence, and the Internet of Things (IoT) can enhance risk identification and management.
Leveraging these technologies enables more accurate risk predictions and more effective mitigation strategies.
Regular Reviews and Updates
The manufacturing landscape and associated risks are continuously evolving.
Regular reviews and updates to risk management strategies ensure that they remain effective over time.
This involves conducting periodic audits and making necessary adjustments based on findings.
The Future of Risk-Based Quality Management
As manufacturing processes become increasingly complex, the importance of risk-based quality management will continue to grow.
Technological advancements will play a significant role in this evolution, providing manufacturers with more sophisticated tools for risk management.
Predictive analytics, machine learning, and real-time monitoring are just a few technologies that will shape the future.
Moreover, as market competition intensifies, companies that excel in quality management will have a definite edge.
A proactive, risk-based approach not only ensures superior product quality but also drives efficiency, compliance, and customer satisfaction.
Companies that adopt this approach are better positioned for long-term success and sustainability in an ever-changing marketplace.
Implementing a risk-based quality management system may require investment and effort.
However, the long-term benefits far outweigh the initial challenges.
By embracing this approach, manufacturers can achieve higher quality standards, reduce operational costs, and gain a competitive advantage.
In conclusion, the risk-based approach in quality management for manufacturing is no longer optional but essential.
As complexities in manufacturing grow, so does the need for proactive and efficient quality management strategies.
By understanding and implementing this approach, manufacturers can ensure high-quality products, satisfied customers, and a prosperous future.
資料ダウンロード
QCD管理受発注クラウド「newji」は、受発注部門で必要なQCD管理全てを備えた、現場特化型兼クラウド型の今世紀最高の受発注管理システムとなります。
ユーザー登録
受発注業務の効率化だけでなく、システムを導入することで、コスト削減や製品・資材のステータス可視化のほか、属人化していた受発注情報の共有化による内部不正防止や統制にも役立ちます。
NEWJI DX
製造業に特化したデジタルトランスフォーメーション(DX)の実現を目指す請負開発型のコンサルティングサービスです。AI、iPaaS、および先端の技術を駆使して、製造プロセスの効率化、業務効率化、チームワーク強化、コスト削減、品質向上を実現します。このサービスは、製造業の課題を深く理解し、それに対する最適なデジタルソリューションを提供することで、企業が持続的な成長とイノベーションを達成できるようサポートします。
製造業ニュース解説
製造業、主に購買・調達部門にお勤めの方々に向けた情報を配信しております。
新任の方やベテランの方、管理職を対象とした幅広いコンテンツをご用意しております。
お問い合わせ
コストダウンが利益に直結する術だと理解していても、なかなか前に進めることができない状況。そんな時は、newjiのコストダウン自動化機能で大きく利益貢献しよう!
(β版非公開)