- お役立ち記事
- Introduction and operation guide for cell production systems that manufacturing site managers should know
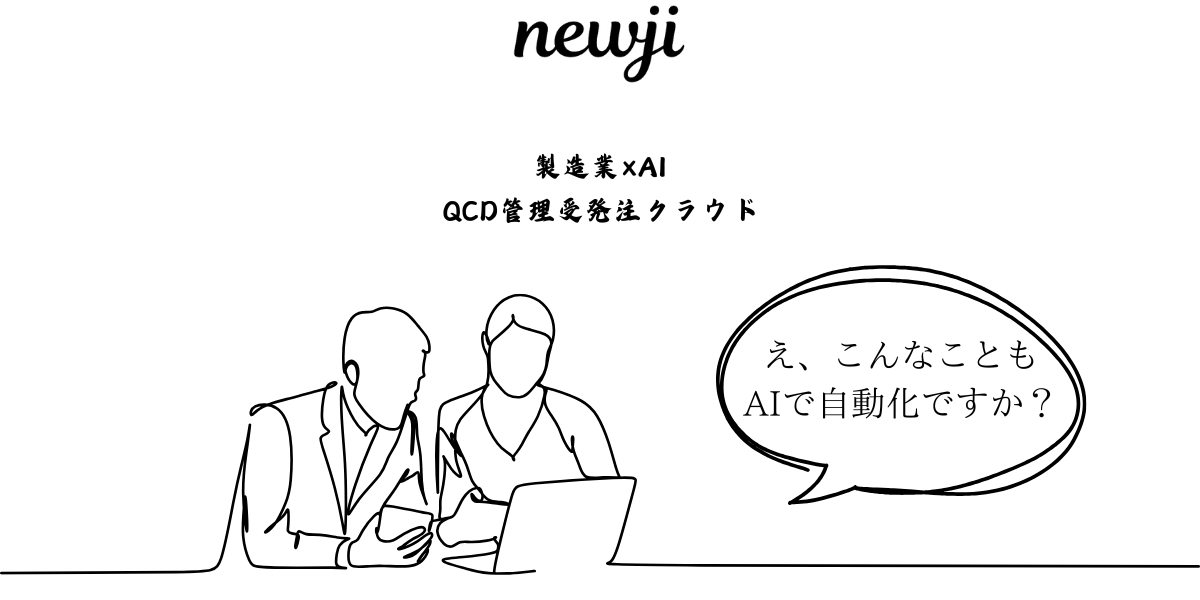
Introduction and operation guide for cell production systems that manufacturing site managers should know
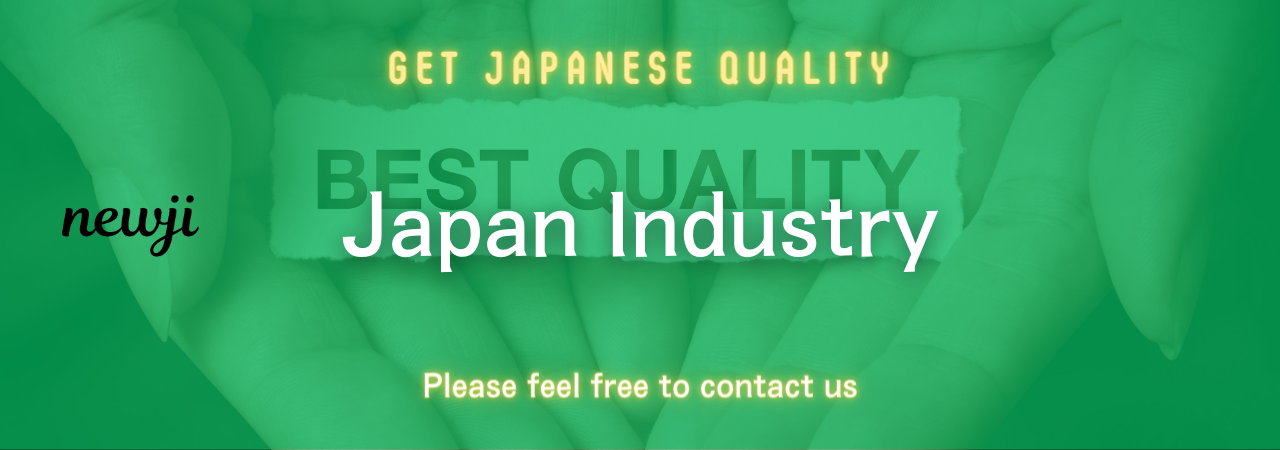
目次
Understanding Cell Production Systems
Cell production systems represent a shift in manufacturing that emphasizes efficiency and flexibility.
They involve a group of workstations, known as cells, arranged to produce a specific part or product.
Unlike traditional assembly lines where each worker specializes in a single task, cell production empowers workers to handle multiple responsibilities.
This setup not only reduces idle time but also enhances the production process by fostering a sense of ownership among the workers.
The Importance of Cell Production Systems
The main advantage of cell production is its ability to increase manufacturing efficiency.
By placing workstations in close proximity, communication among workers improves, and products move seamlessly from one process to the next.
This streamlined workflow can lead to reduced production times and lower costs.
Moreover, cell production systems are inherently flexible.
They can be easily reconfigured to accommodate changing demands, making them ideal for manufacturers who need to produce a variety of products.
This adaptability is crucial in today’s fast-paced markets where consumer preferences often change rapidly.
Key Components of Cell Production Systems
Several key components make cell production systems successful.
Firstly, multi-skilled workers are essential.
Employees in a cell production setup need to be trained to perform various tasks, allowing them to switch roles as needed.
This versatile workforce ensures that there are fewer bottlenecks in the production process.
Secondly, the layout of the workstations is crucial.
Workstations should be arranged to minimize the distance that materials need to travel, reducing wastage of time and effort.
Clear visibility between stations allows for better coordination and immediate problem-solving.
Lastly, continuous improvement practices, such as Lean or Kaizen, are often integrated.
These methodologies encourage ongoing evaluation and refinement of the manufacturing process.
Challenges in Implementing Cell Production
Despite its advantages, implementing a cell production system poses certain challenges.
One of the primary concerns is the initial investment in training.
Since workers need to be multi-skilled, companies must dedicate resources to extensive training programs.
Another challenge is the design of the workspace.
Creating an efficient layout that minimizes waste while maximizing productivity requires careful planning and possibly redesigning existing facilities.
Additionally, there may be resistance to change from employees accustomed to traditional production methods.
Management must communicate the benefits effectively to gain employee buy-in.
Moreover, careful monitoring and adjustment are required to keep the system running efficiently as production demands change.
Steps to Implement Cell Production Systems
For a successful transition to cell production, site managers should follow a series of strategic steps.
Evaluate Current Processes
The first step is to evaluate existing production processes.
Conduct an audit to identify areas where efficiency improvements are needed.
This step involves analyzing bottlenecks, examining workflows, and understanding the skills of your workforce.
Using data collected, determine whether a cell production system would yield significant benefits.
Design the Cell Layout
Once you understand the current limitations, design a cell layout that addresses those challenges.
The layout should focus on reducing travel time and maintaining a smooth flow of materials.
Consider the product’s assembly sequence while ensuring that stations are in logical and efficient order.
The layout should also allow for flexibility to accommodate different products or changes in demand.
Train and Develop Employees
Training is crucial to the success of a cell production system.
Develop a comprehensive training program to upskill your workforce.
Ensure that employees are comfortable performing multiple tasks and understand the cell production system’s goals.
Encourage a culture of continuous improvement and problem-solving, as employees will be key to identifying areas for further development.
Implement and Monitor Operations
With the design and training in place, proceed to implement the cell production system.
Start with pilot testing in a small part of your manufacturing process to refine the approach before a full-scale implementation.
Once operational, monitor the system closely.
Use key performance indicators (KPIs) to assess efficiency, quality, and production times.
Regularly review these metrics and be prepared to make necessary adjustments.
Encourage Feedback and Continuous Improvement
Finally, foster an environment where feedback is welcomed and integrated.
Encourage employees to share observations and propose enhancements.
Utilize methodologies like Lean or Six Sigma to promote an ongoing culture of refinement.
Continuous improvement not only sustains the benefits of cell production but also helps in adapting to future changes in the manufacturing landscape.
Conclusion
Cell production systems offer a compelling alternative to traditional manufacturing approaches with their emphasis on efficiency and flexibility.
By understanding the principles behind cell production, focusing on key components, and overcoming challenges, manufacturing managers can significantly enhance their operations.
The journey to adopting cell production is demanding but ultimately rewarding, as it leads to a more responsive and effective manufacturing process.
By following a structured implementation plan, which includes evaluation, design, training, monitoring, and improvement, site managers can successfully introduce this advanced method into their operations.
資料ダウンロード
QCD調達購買管理クラウド「newji」は、調達購買部門で必要なQCD管理全てを備えた、現場特化型兼クラウド型の今世紀最高の購買管理システムとなります。
ユーザー登録
調達購買業務の効率化だけでなく、システムを導入することで、コスト削減や製品・資材のステータス可視化のほか、属人化していた購買情報の共有化による内部不正防止や統制にも役立ちます。
NEWJI DX
製造業に特化したデジタルトランスフォーメーション(DX)の実現を目指す請負開発型のコンサルティングサービスです。AI、iPaaS、および先端の技術を駆使して、製造プロセスの効率化、業務効率化、チームワーク強化、コスト削減、品質向上を実現します。このサービスは、製造業の課題を深く理解し、それに対する最適なデジタルソリューションを提供することで、企業が持続的な成長とイノベーションを達成できるようサポートします。
オンライン講座
製造業、主に購買・調達部門にお勤めの方々に向けた情報を配信しております。
新任の方やベテランの方、管理職を対象とした幅広いコンテンツをご用意しております。
お問い合わせ
コストダウンが利益に直結する術だと理解していても、なかなか前に進めることができない状況。そんな時は、newjiのコストダウン自動化機能で大きく利益貢献しよう!
(Β版非公開)