- お役立ち記事
- Introduction and Operation of Quality Management Systems (QMS)
月間76,176名の
製造業ご担当者様が閲覧しています*
*2025年3月31日現在のGoogle Analyticsのデータより
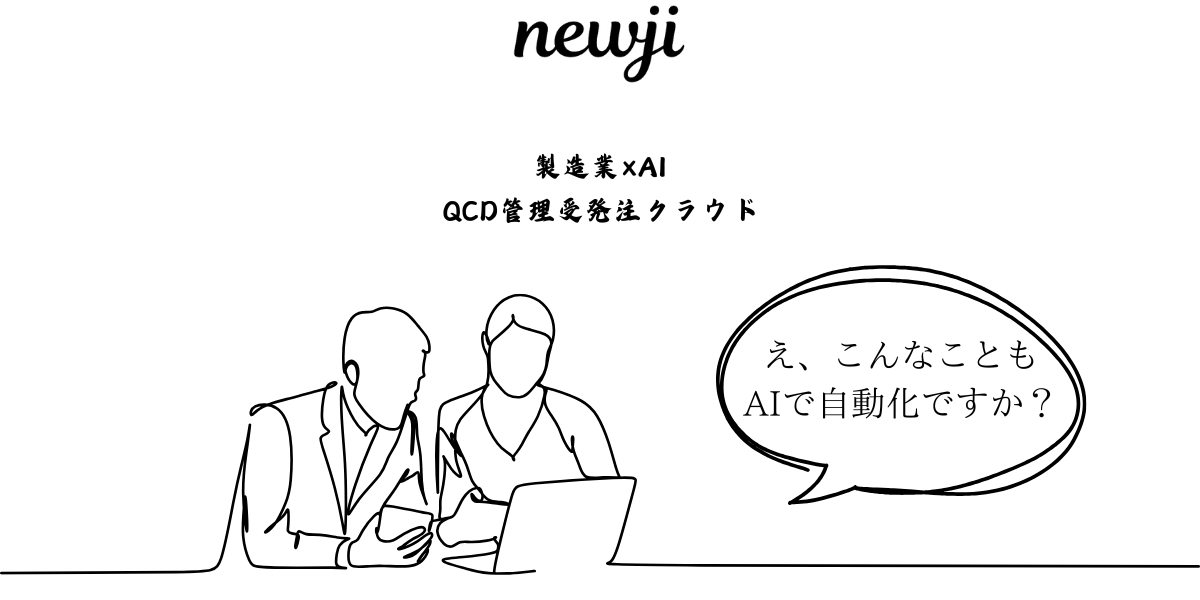
Introduction and Operation of Quality Management Systems (QMS)
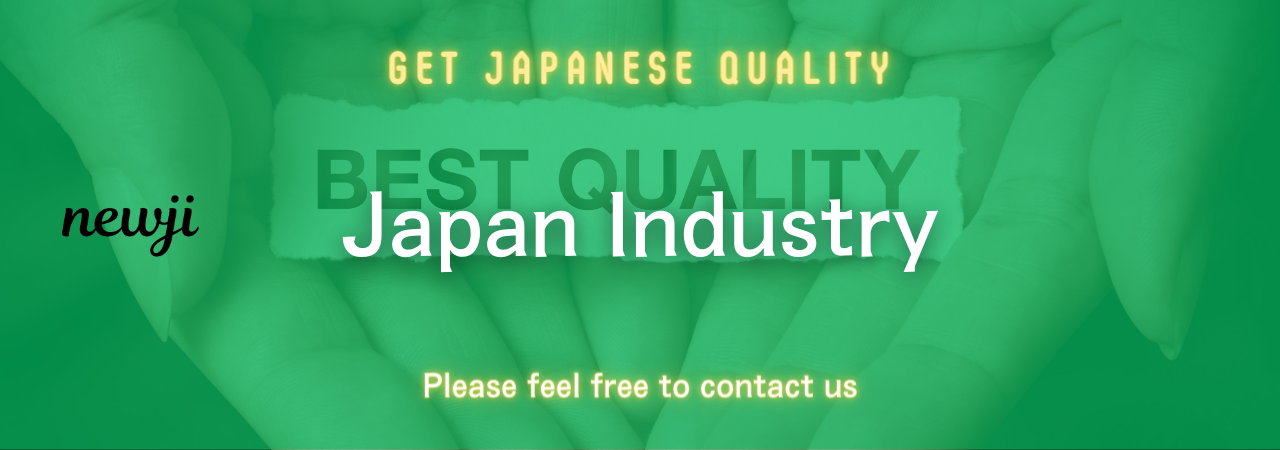
Quality Management Systems (QMS) play a crucial role in ensuring that organizations consistently meet customer expectations and regulatory requirements.
These systems encompass a set of policies, processes, and procedures designed to plan and control the quality of their products and services.
In this article, we will explore the fundamentals of Quality Management Systems, their benefits, and how to effectively implement and operate them within an organization.
目次
What is a Quality Management System (QMS)?
A Quality Management System (QMS) is a structured framework that documents processes, procedures, and responsibilities for achieving quality policies and objectives.
It helps organizations ensure that their products or services meet customer expectations and comply with regulations.
By adopting a QMS, companies aim to improve efficiency, reduce costs, and enhance customer satisfaction.
Components of a QMS
A typical Quality Management System comprises several key components:
1. **Quality Policy:** A formal statement from top management outlining the organization’s commitment to quality.
2. **Quality Objectives:** Specific, measurable goals related to quality that align with the quality policy.
3. **Quality Manual:** A document that describes the QMS, including the scope, processes, and responsibilities.
4. **Procedures:** Detailed descriptions of how various processes within the organization should be carried out to ensure quality.
5. **Work Instructions:** Specific instructions for carrying out tasks, ensuring consistency and compliance with procedures.
6. **Records:** Documentation that provides evidence of compliance with the QMS and quality standards.
Why Implement a QMS?
The implementation of a QMS offers numerous benefits to organizations, including:
1. **Improved Efficiency:** A well-structured QMS streamlines processes, reducing waste and minimizing errors, ultimately leading to cost savings.
2. **Enhanced Customer Satisfaction:** By consistently delivering high-quality products or services, organizations can build trust and loyalty among their customers.
3. **Regulatory Compliance:** A QMS helps companies adhere to industry standards and regulations, reducing the risk of non-compliance and potential penalties.
4. **Employee Engagement:** Clear policies and procedures empower employees, fostering a culture of continuous improvement and accountability.
5. **Market Competitiveness:** A robust QMS can provide a competitive edge, differentiating an organization from its competitors.
Steps to Implement a Quality Management System
Implementing a Quality Management System requires a systematic approach.
The following steps will guide organizations through the process:
1. Commitment from Top Management
Successful implementation of a QMS begins with a commitment from top management.
Leaders must recognize the importance of quality and allocate the necessary resources to develop and maintain the system.
Their support is crucial for fostering a culture of quality throughout the organization.
2. Define the Scope
The next step is to define the scope of the QMS.
This involves identifying the areas of the organization that will be covered by the system and understanding the relevant regulatory requirements and industry standards.
3. Develop a Quality Policy and Objectives
Top management should establish a quality policy that reflects the organization’s commitment to quality.
Alongside this, they must set specific quality objectives that are aligned with the quality policy and measurable for evaluating performance.
4. Document Processes and Procedures
Organizations must document their processes and procedures to ensure consistency and compliance.
This includes creating a quality manual, detailed procedures, and work instructions.
Documentation provides a reference for employees and ensures that everyone understands their roles and responsibilities.
5. Train Employees
Employee training is an essential part of implementing a QMS.
All employees should be trained on the organization’s quality policy, objectives, and procedures.
Training ensures that employees are aware of their roles in maintaining quality and understand how to comply with the QMS.
6. Conduct Internal Audits
Regular internal audits are necessary to assess the effectiveness of the QMS.
Internal audits involve evaluating processes, procedures, and records to identify areas for improvement.
Findings from audits should be documented, and corrective actions should be taken to address any issues.
7. Continuous Improvement
A QMS is not a one-time implementation but an ongoing effort.
Organizations should continually review and improve their processes to enhance quality.
This involves analyzing performance data, seeking feedback from customers, and making necessary adjustments to the system.
Operating a Quality Management System
Once a QMS is implemented, it must be continuously monitored and maintained to ensure its effectiveness.
1. Monitor Performance
Organizations should establish key performance indicators (KPIs) to measure the effectiveness of their QMS.
Regular monitoring of performance against these indicators helps identify areas for improvement.
2. Conduct Regular Reviews
Regular reviews by top management are essential to ensure the QMS remains relevant and effective.
These reviews should consider changes in the organization’s environment, customer feedback, and the results of internal audits.
3. Engage Employees
Employee engagement is vital for the successful operation of a QMS.
Organizations should encourage employees to participate in the continuous improvement process by providing feedback and suggestions.
4. Address Non-Conformities
When non-conformities are identified, either through internal audits or customer complaints, organizations must take corrective actions to address the issues.
This involves identifying the root cause, implementing corrective measures, and preventing recurrence.
5. Maintain Documentation
Keeping documentation up-to-date is crucial for the effective operation of a QMS.
Organizations should regularly review and revise documents to reflect changes in processes, procedures, and regulations.
A well-implemented Quality Management System can significantly enhance an organization’s ability to deliver high-quality products and services.
By following a systematic approach to implementing and operating a QMS, organizations can achieve improved efficiency, customer satisfaction, and regulatory compliance.
Continuous monitoring, employee engagement, and a commitment to quality from top management are key factors in ensuring the long-term success of a QMS.
資料ダウンロード
QCD管理受発注クラウド「newji」は、受発注部門で必要なQCD管理全てを備えた、現場特化型兼クラウド型の今世紀最高の受発注管理システムとなります。
ユーザー登録
受発注業務の効率化だけでなく、システムを導入することで、コスト削減や製品・資材のステータス可視化のほか、属人化していた受発注情報の共有化による内部不正防止や統制にも役立ちます。
NEWJI DX
製造業に特化したデジタルトランスフォーメーション(DX)の実現を目指す請負開発型のコンサルティングサービスです。AI、iPaaS、および先端の技術を駆使して、製造プロセスの効率化、業務効率化、チームワーク強化、コスト削減、品質向上を実現します。このサービスは、製造業の課題を深く理解し、それに対する最適なデジタルソリューションを提供することで、企業が持続的な成長とイノベーションを達成できるようサポートします。
製造業ニュース解説
製造業、主に購買・調達部門にお勤めの方々に向けた情報を配信しております。
新任の方やベテランの方、管理職を対象とした幅広いコンテンツをご用意しております。
お問い合わせ
コストダウンが利益に直結する術だと理解していても、なかなか前に進めることができない状況。そんな時は、newjiのコストダウン自動化機能で大きく利益貢献しよう!
(β版非公開)